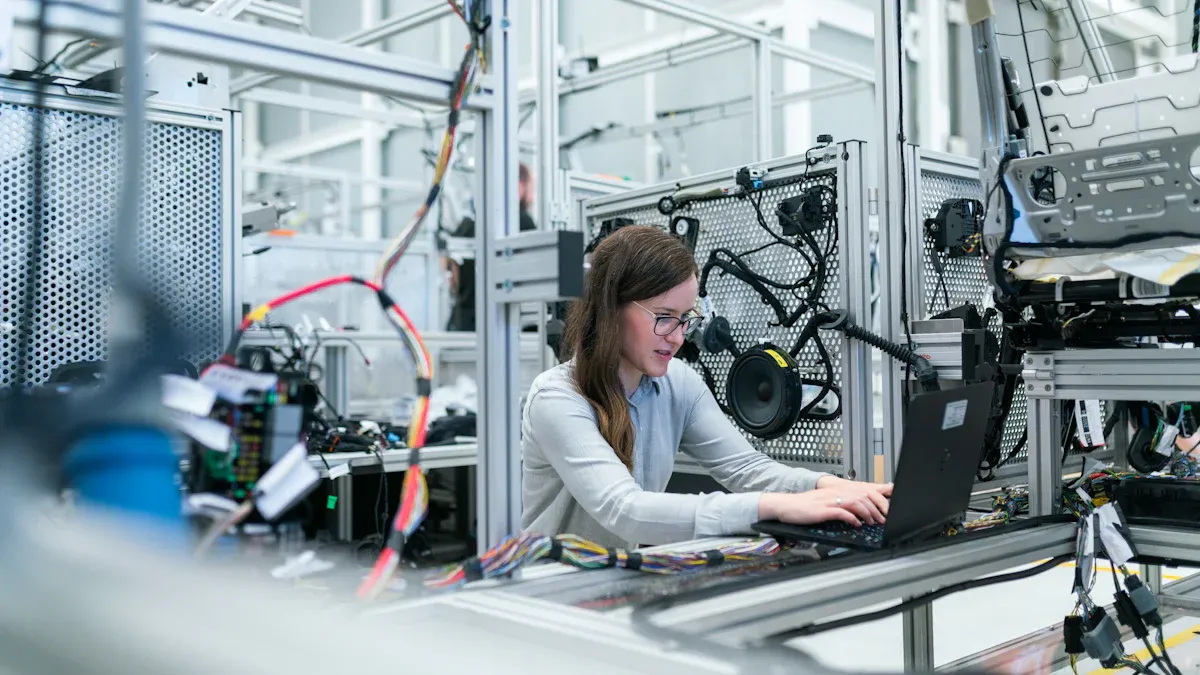
Choosing the right PCBA manufacturer is crucial. A reliable PCBA manufacturer provides excellent products on time and at a reasonable price. For example, modern tools like pick-and-place machines and AI checkers enhance efficiency and accuracy, helping to prevent errors. In contrast, subpar manufacturers can lead to delays, with each design change potentially adding weeks to the timeline. Selecting the right PCBA manufacturer saves time, money, and reduces stress. So, why settle for less when the best choice can ensure your project’s success?
Key Takeaways
Pick a PCBA maker with good quality checks. This helps make reliable products and lowers mistakes.
Find makers with important certifications like ISO 9001 and IPC. These show they care about quality and follow rules.
Request a full cost list to avoid surprise charges. Knowing all costs early helps you stick to your budget.
Check the maker’s experience and reputation. Read reviews and ask for examples to see if they fit your needs.
Keep clear communication with your maker. Share goals early and stay informed to prevent confusion.
Key Factors When Choosing a PCBA Manufacturer
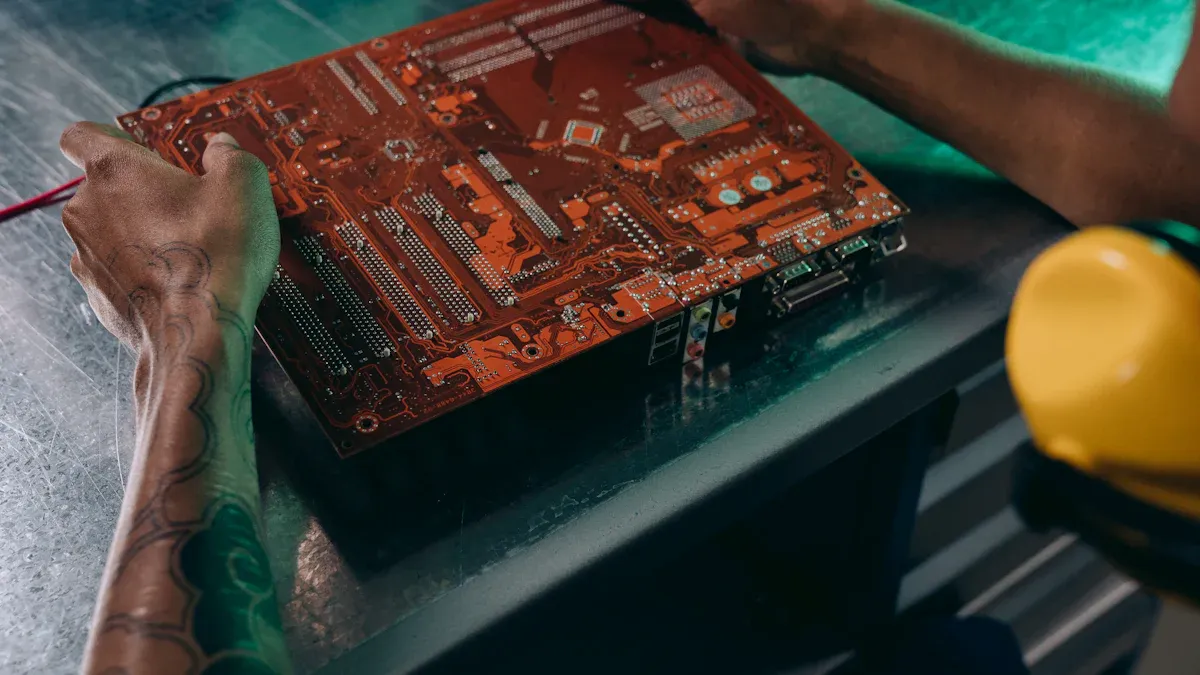
PCB Quality Control
Importance of consistent quality standards
Consistency in PCB quality is very important. You need a manufacturer that makes every batch meet high standards. This ensures your project runs smoothly without problems. Good PCBs are essential for reliable electronics, so don’t settle for poor quality. A great PCBA manufacturer uses strong processes to keep quality high during every step of production.
Role of testing and inspection processes
Testing and checking are must-haves in PCB production. Good manufacturers use tools like visual checks, X-rays, and automated inspections (AOI). They also test circuits and connections to make sure everything works. Statistical Process Control (SPC) helps catch problems early. Picking a manufacturer with strong testing means your boards will work as expected.
Certifications and Compliance
Key certifications to look for (e.g., ISO, IPC)
Certifications show a manufacturer cares about quality and reliability. Look for ISO 9001, which ensures good management practices. IPC certifications are also important for PCB standards. These prove the manufacturer follows best practices and delivers high-quality boards.
Ensuring compliance with industry standards
Following industry rules helps avoid costly mistakes. Certified manufacturers follow strict guidelines to meet all requirements. For example, ISO 9001 uses a cycle to improve processes and fix issues early. Choosing a compliant manufacturer supports your project’s long-term success.
Cost and Pricing Transparency
Balancing cost with quality
Finding good quality at a fair price takes effort. Cheap options may lead to bad PCBs that fail later. Instead, choose a manufacturer that offers reasonable prices without lowering quality. Spending more now can save money on repairs later.
Identifying hidden costs in quotes
Clear pricing is very important. Some manufacturers may add hidden fees after giving a low quote. Ask for a full cost breakdown upfront to avoid surprises. This includes materials, testing, and shipping. Honest manufacturers give clear prices to help you stay on budget.
Lead Times and Delivery
Understanding production capacity and timelines
It’s important to know how fast a manufacturer works. Their ability to meet deadlines depends on how much they can produce and how efficient they are. For example, simple PCBs take about 1-2 weeks, while more complex or larger orders may need 4-8 weeks or longer. Here’s a simple chart:
PCB Type | Usual Time Needed |
---|---|
Simple, small orders | 1-2 weeks |
Medium complexity, medium size | 2-4 weeks |
Complex or large orders | 4-8 weeks or more |
The type of service also affects delivery time. Standard services might take up to 4 weeks, but express services can deliver in just 1-3 days. However, faster services cost more and may not work for complicated designs.
Service Type | Time Needed | Cost Level | Limits |
---|---|---|---|
Standard Service | 1-4 weeks | Normal | Slower, not good for tight deadlines |
Quick-Turn Service | 3-10 business days | Higher than Normal | May not handle complex designs, costs more |
Express Service | 1-3 business days | Highest | Simple designs only, smallest orders, very costly |
By checking these details, you can pick a manufacturer that fits your schedule and budget.
Why meeting deadlines matters
Finishing on time is very important for your project. Delays can mess up your plans, cost more money, and hurt your reputation. A good manufacturer will focus on delivering on time by working efficiently and planning well. Always ask about their history with deadlines and how they deal with problems. This helps keep your project on track and stress-free.
Experience and Industry Reputation
Why experience is important
Experience is key in PCBA manufacturing. A skilled manufacturer knows how to handle tricky designs and follow strict rules. They make sure your PCB works well for its purpose. Choose a manufacturer with a strong background in your field to avoid mistakes.
Checking reviews and feedback
A manufacturer’s reputation shows how reliable they are. Before choosing, read reviews and ask for references. Look for things like First Pass Yield (FPY), defect rates, and customer satisfaction. High FPY and low defects mean they care about quality. Here’s a quick guide:
Indicator | What It Means |
---|---|
First Pass Yield (FPY) | Percent of products passing all checks the first time. |
Defect Rate | Percent of faulty units made during production. |
Throughput | Number of units made in a set time. |
Customer Returns or Complaints | Number of items sent back or complaints about quality. |
By reviewing these points, you can decide if the manufacturer is a good match for your project.
Questions to Ask When Picking a PCB Manufacturer
Quality and Testing Processes
What steps ensure good quality?
When choosing a PCB maker, ask about their quality checks. A trustworthy manufacturer uses strong systems to make sure PCBs are top-notch. For example, they might use tools like AOI or X-ray tests. These catch problems early and save money on fixes later. Also, see if they follow rules like IPC-A-610 or RoHS. These show they stick to strict quality standards.
You can also ask for specific numbers. For instance, find out how often they deliver on time or meet tight deadlines. These details show how reliable and efficient they are.
What happens with faulty products?
Even the best companies make mistakes. That’s why it’s important to know how they handle bad products. Do they have a clear return or replacement policy? Will they fix problems for free? A good manufacturer owns up to errors and solves them fast. Asking this now can save you trouble later.
Certifications and Experience
What certifications do you have?
Certifications show a company is trustworthy and professional. Always ask what certifications they hold. Look for ISO 9001 for quality management and IPC for PCB standards. These prove they meet industry rules and make reliable products.
How long have you been in this business?
Experience is key in PCB making. A company with years of work knows how to handle tricky projects. They also have a history of making great PCBs. Ask about their past work and the types of projects they’ve done. This helps you see if they can meet your needs.
Production and Customization
Can you make special designs?
Not all companies can handle custom PCBs. If your design is unique or complex, you need a skilled manufacturer. Ask if they’ve done similar work before and how they solve problems. This ensures they can meet your expectations.
How do you handle prototypes and scaling?
Prototyping is an important step in PCB making. A good company has a smooth process for testing designs before full production. Ask how fast they can make prototypes and scale up production. This helps you plan your project better.
Costs and Timelines
Are there extra fees not in the quote?
When comparing prices from a PCBA manufacturer, don’t just look at the total. Have you thought about hidden costs? Some companies might skip listing fees for testing, shipping, or setup. These extra charges can surprise you later and mess up your budget.
To prevent this, ask for a full cost breakdown. Check for things like material prices, assembly fees, and inspection costs. If something isn’t clear, ask questions. Honest manufacturers will explain all charges upfront. This helps you know exactly what you’re paying for and plan your budget better.
What is your usual lead time for projects like mine?
Knowing production times is key to staying on schedule. Each PCB project is different, so timelines can change. For instance, a simple PCB might take one or two weeks. A more detailed design could need several weeks.
When speaking with a manufacturer, ask about their average timelines for similar projects. Also, find out how they handle rush orders or delays. A dependable company will give you a clear schedule and stick to it. They’ll also update you if problems come up, so you’re not left wondering.
Remember, faster isn’t always better. Quick services may not work for complex designs. Balancing speed and quality ensures your PCB meets your needs without added stress.
Tip: Always get lead times in writing. This avoids confusion and keeps everyone responsible.
Common Mistakes When Picking the Right PCB Supplier
Skipping Certifications
Problems with uncertified manufacturers
Working with a manufacturer without certifications can cause big issues. They might not have the skills or systems to make good boards. This can lead to broken boards, late deliveries, or even failed projects.
Picking a manufacturer without the right skills can cause delays and bad-quality boards. These are major risks when working with uncertified suppliers.
Traceability is also very important. Certified manufacturers keep detailed records to find and fix problems early.
Traceability data helps spot defects before products leave the factory. Delays in PCB production often increase defects, showing the dangers of uncertified manufacturers.
Checking certifications
Always check a manufacturer’s certifications before agreeing to work with them. Look for certifications like ISO 9001 for quality and IPC for PCB standards. Don’t just trust their word—ask for proof or check their website. If you can, visit their factory to see how they work. This ensures you’re choosing a trustworthy partner for your project.
Only Looking at Price
Why the cheapest isn’t always best
Choosing the lowest price can cause problems later. Cheap manufacturers may skip steps, making bad boards. These boards can break, costing you more money to fix or replace. Spending more on a good manufacturer now can save you trouble later.
Costs of bad-quality PCBs
Bad PCBs can hurt your business and cost you money. Imagine selling a product that breaks because of a bad board. You’d lose money on returns and refunds, and customers might stop trusting you. Picking a manufacturer with strong quality checks keeps your product working well and protects your business.
Ignoring Communication
Why clear communication matters
Good communication is key to a smooth project. A manufacturer who listens to you and gives updates helps avoid problems. Clear communication keeps everyone on the same page.
Signs of bad customer service
Be careful of manufacturers who take too long to reply or give unclear answers. Bad customer service can cause delays and stress. If they don’t care about your concerns early on, they won’t later either. Choose a manufacturer who is honest and helpful to keep your project running smoothly.
Not Researching the Manufacturer
Skipping reviews and references
Not checking reviews is a big mistake. Reviews show how other customers feel about the manufacturer. They tell you if the company keeps promises, fixes problems, and makes good products. Without this, you’re taking a risky chance.
Start by reading reviews on Google or industry websites. Look for common complaints like delays or bad quality. Also, see if people praise their service and reliability. Don’t just rely on reviews—ask the company for references. A good manufacturer will share contacts of past clients who can confirm their work.
Tip: Notice how they reply to bad reviews. A polite and helpful response shows they care about fixing problems and value their customers.
Dangers of skipping a factory visit or audit
Not visiting the factory can cause problems later. You might find out too late that they don’t have the right tools or systems. A visit lets you check their machines, quality checks, and how organized they are.
If you can’t visit in person, ask for a virtual tour or photos of their factory. During the audit, make sure they follow rules and have certifications like ISO 9001. This step helps you pick the best manufacturer for your project.
Why it matters: Visiting the factory proves they can do what they promise. It also builds trust and gives you peace of mind.
Doing proper research saves you from mistakes and helps you find a reliable manufacturer for your needs.
Tips for Finding the Best PCBA Manufacturer
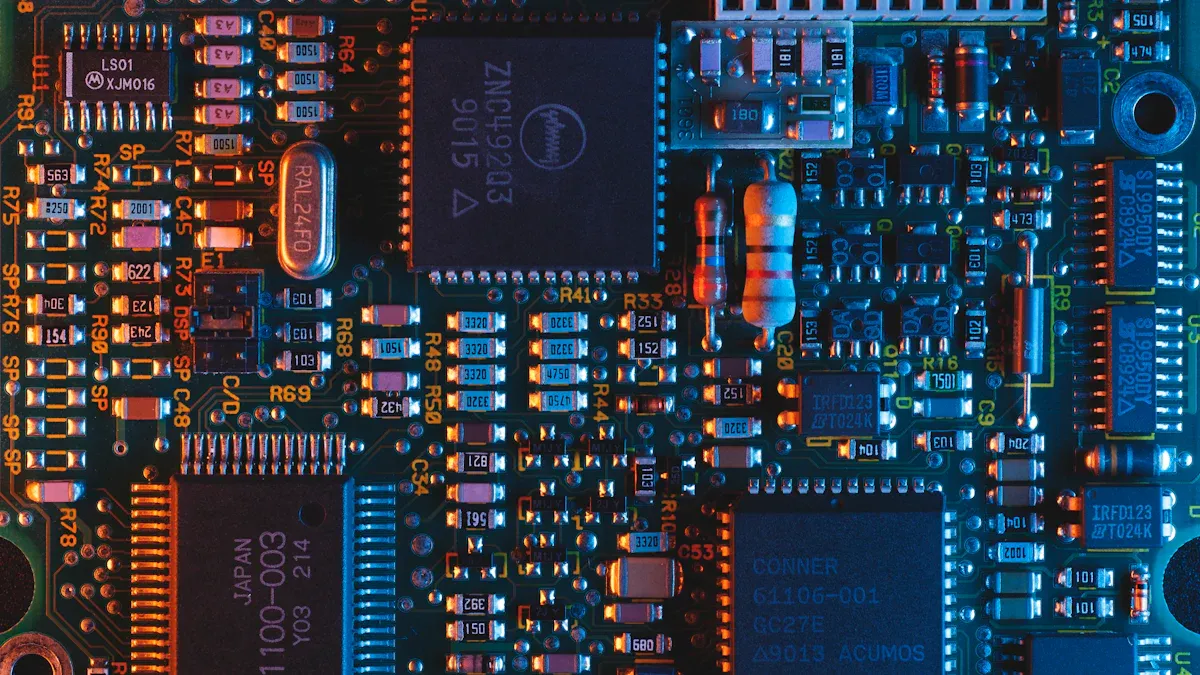
Balancing Cost and Quality
How to evaluate trade-offs effectively
Balancing cost and quality can be challenging. Spending too little may cause problems, but overspending isn’t ideal either. First, decide what matters most for your project. Do you need strong boards or fast delivery? Once you know, compare manufacturers based on these needs. Pick one that offers good quality at a fair price.
Ask for samples or prototypes before deciding. This helps you check the quality yourself. Also, see if they use good materials and follow strict steps. These checks help you make better choices.
Prioritizing long-term value over short-term savings
Choosing the cheapest option may seem smart, but it can backfire. Poor-quality boards might break, costing you more later. Fixing or replacing them can hurt your budget and reputation.
Instead, think about long-term value. Pay a bit more for a manufacturer who makes reliable boards. Good pcb quality keeps your products working well and protects your business.
Building a Strong Partnership
Importance of trust and collaboration
Working well with your manufacturer is very important. Trusting them means you know they’ll do a good job. Teamwork also helps solve problems faster. A good manufacturer listens to your needs and finds solutions that fit.
How to establish a good working relationship
Be clear about what you want from the start. Share your goals, deadlines, and special needs. Talk regularly to check progress and fix issues early. Treat the manufacturer like a partner, not just a supplier. This builds respect and leads to better results.
Ensuring Clear Communication
Setting expectations upfront
Good communication starts with clear instructions. Tell the manufacturer exactly what you need, like design details and delivery dates. Ask them to confirm they understand. This avoids confusion and keeps everyone aligned.
Maintaining regular updates throughout the project
Stay connected during the project. Regular updates help you see progress and fix problems early. Ask for weekly reports or set up calls to review work. A manufacturer who communicates well will keep you informed and reduce worries.
Picking the right PCB maker is very important. A good one gives quality boards, delivers on time, and communicates well. To avoid problems, choose manufacturers with certifications, testing, and teamwork.
Methods like SPC and automation help reduce mistakes and improve work. Here’s a simple table showing how they do it:
Improvement Method | What It Does |
---|---|
Statistical Process Control (SPC) | Tracks production data to fix issues early and lower defects. |
Automation and Testing | Uses machines to avoid human mistakes and work faster. |
Supplier Quality Checks | Makes sure materials are good by working closely with suppliers. |
Worker Training | Teaches workers new skills to make better products. |
Spend time learning about manufacturers and asking smart questions. A great PCBA maker will meet your needs and help your project succeed.
FAQ
1. How can I tell if a PCBA manufacturer is trustworthy?
Check for certifications like ISO 9001 and IPC. Read reviews and ask for references. A good manufacturer has a solid reputation, clear communication, and delivers quality products on time.
2. What’s the difference between standard and quick-turn services?
Standard services take more time but cost less money. Quick-turn services are faster, often just a few days, but cost more. Pick based on how urgent or complex your project is.
3. Can I get a prototype before full production?
Yes, most manufacturers provide prototypes. Prototypes help test your design before making more. Ask about their process and how fast they can deliver it.
4. What should I include when contacting a manufacturer?
Send your design files, project details, and deadlines. Mention your budget and any special needs. This helps them give you an accurate quote and timeline.
5. How do I avoid hidden costs in quotes?
Request a full cost breakdown. Check for fees like materials, testing, shipping, or setup. Honest manufacturers explain all charges clearly upfront.
Tip: Always share your expectations clearly. This keeps you and the manufacturer on the same page during the project.