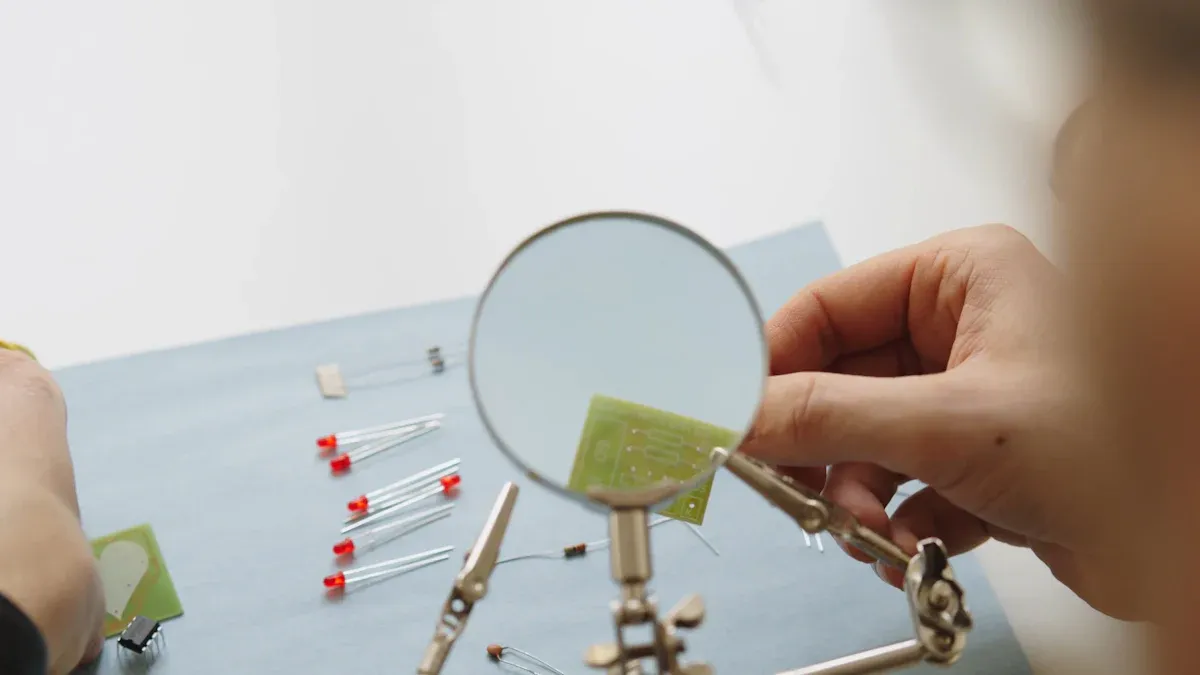
Mastering PCBA manufacturing methods improves the quality of circuit boards. You are important in making sure every step meets high standards. Good assembly needs accuracy and speed. For example, finding defects in PCBA manufacturing has 97.3% accuracy. It also works at speeds of 322.6 frames per second. These results show why advanced methods like soldering and packaging matter. Packaging keeps parts safe from moisture during production. Following PCBA manufacturing rules ensures boards are consistent and meet requirements. This protects the quality of every circuit board you make.
Key Takeaways
Learning PCBA methods helps make better circuit boards. Work carefully and quickly to keep high quality.
Use Surface Mount Technology (SMT) for faster builds and smaller gadgets. It makes things quicker, better, and eco-friendly.
Follow IPC rules to lower mistakes and make products last longer. Doing things the same way makes boards more dependable.
Use smart testing tools like Automated Optical Inspection (AOI) to find problems early and make better boards.
Use machines to work faster and waste less. It helps make more boards while keeping them high quality.
Key Techniques in PCBA Manufacturing
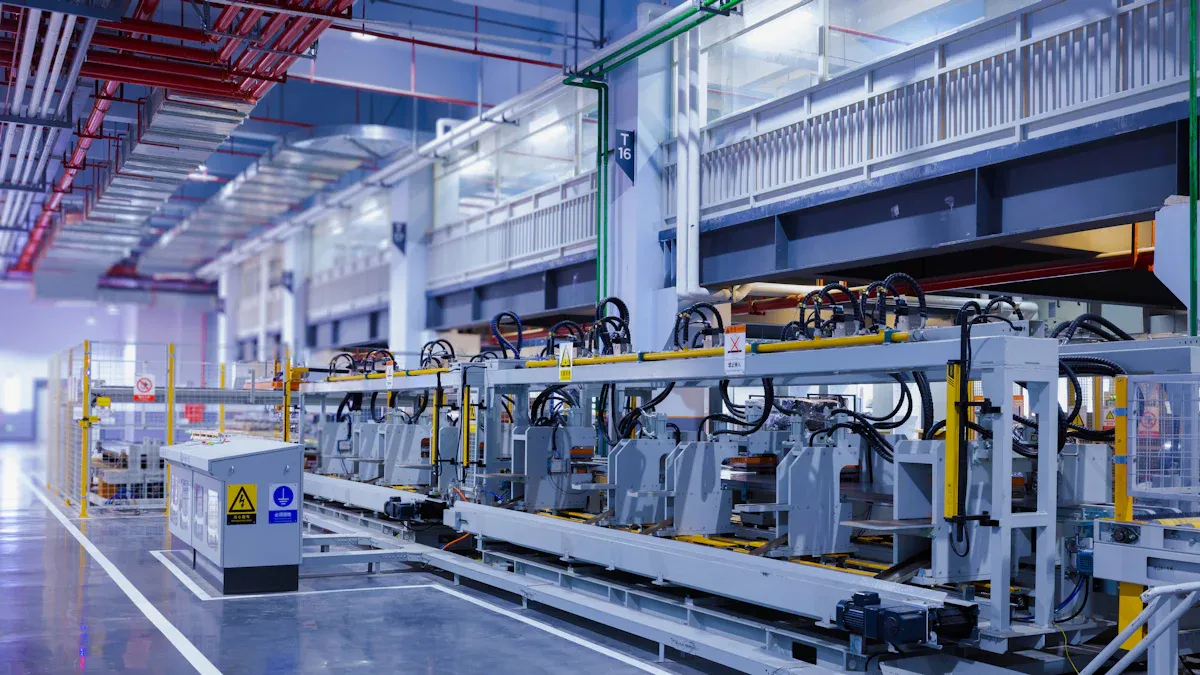
Surface Mount Technology (SMT)
Surface Mount Technology (SMT) is a popular way to assemble PCBs. It places parts directly on the board without drilling holes. This method is fast and helps make smaller devices. SMT is great for quick assembly, perfect for making many products.
For example, Panasonic’s NPM-G Series SMT machines, released in 2023, are advanced. They work fast, improve quality, and monitor in real-time. In 2022, GJD Manufacturing used Hanwha Techwin SM482 Plus machines. These machines made work faster and eco-friendly. These examples show how SMT boosts speed, quality, and sustainability.
Through-Hole Technology (THT)
Through-Hole Technology (THT) is another common PCB assembly method. Unlike SMT, THT puts part leads through holes and solders them underneath. This makes the connection strong, good for tough uses.
THT works well for parts like transformers and connectors. These parts handle big currents or physical stress. THT ensures PCBs stay strong in hard conditions. It is still a top choice for durable and reliable designs.
Mixed Technology Approaches
Mixed technology uses both SMT and THT in one process. It’s helpful when a design needs both types of parts. Though it’s more complex, it saves money and improves production.
Studies compare mixed technology with separate SMT and THT lines. Mixed technology cuts extra equipment but may cause soldering issues. Separate lines focus on better quality for each method. The best choice depends on your design and production needs.
Ball Grid Array (BGA) Assembly
Ball Grid Array (BGA) assembly helps make PCBAs work better. This method uses solder balls in a grid under the component. These balls connect to the PCB, making strong bonds.
BGA assembly has many benefits. It’s great for small devices like phones and tablets. Shorter connections make signals faster and clearer. The direct connection also spreads heat well, stopping overheating. This keeps devices working longer.
Here’s a simple look at BGA assembly’s key features:
Feature | What It Means |
---|---|
Speed | Faster signals due to shorter connections and fewer issues. |
Size | Smaller size fits well in tiny electronic devices. |
Heat Dissipation | Better heat control thanks to direct connections. |
When using BGA, careful testing is very important. X-ray checks help find hidden problems like gaps or misplaced solder balls. Good soldering methods are also needed for strong connections.
Learning BGA assembly helps you make better PCBAs. It boosts performance and makes devices last longer. This method is a great tool for modern electronics.
Role of PCB Assembly Standards in Manufacturing
Overview of IPC Standards
IPC standards are important for making high-quality circuit boards. They give clear steps for each part of the process. By using IPC rules, you can lower mistakes and make better products. For example, IPC-6012 checks rigid PCBs to meet top standards. IPC-A-610 helps with neat soldering and placing parts correctly.
Following IPC standards also makes products last longer. It prevents problems like solder bridging or tombstoning that cause failures. The table below shows why IPC standards are helpful:
Aspect | Description |
---|---|
Ensures Consistency | IPC rules make sure parts are placed the same way every time. |
Reduces Defects | |
Enhances Product Lifespan | Fewer mistakes mean stronger PCBs that last longer. |
Using these rules helps you make strong and reliable circuit boards.
Importance of ISO Certifications
ISO certifications, like ISO 9001, help keep quality high. This certification makes sure your work meets customer needs and rules. With ISO 9001, you can use tools like SPC to fix problems early.
Working with ISO-certified suppliers gives you better materials. This teamwork improves the whole process and makes better products. ISO certifications also build trust with customers and improve your reputation.
Compliance with RoHS and UL Standards
RoHS and UL standards keep products safe and eco-friendly. RoHS stops harmful materials from being used in electronics. For example, before RoHS, tin whiskers caused Swiss watches to fail. After RoHS, this problem disappeared.
UL standards check product safety to avoid risks. Following these rules makes products safer and more reliable. Meeting these standards protects customers and boosts your company’s image.
Guidelines for Inspection and Quality Control
Inspection and quality control are key to making great PCBs. By following the right steps, you can find problems early. This helps keep your products reliable and high-quality. Here are some simple practices to follow:
Visual Inspection: Look closely to spot surface problems like bad soldering or misplaced parts. This step makes sure all components are in the right place. Use magnifying tools to see small details better.
Functional Testing: Test the PCB to check if it works correctly in different situations. This step finds hidden problems that you might miss by just looking. It also ensures the PCB is safe and reliable.
The table below shows two main inspection methods and their uses:
Inspection Method | Purpose |
---|---|
Visual Inspection | Find surface issues and check if parts are placed and soldered properly. |
Functional Testing | Make sure the PCB works well and meets safety rules. |
To get good results, create a clear inspection plan. Teach your team to follow pcb assembly rules at every step. Check your process often to find ways to improve.
Using advanced tools like automated optical inspection (AOI) systems can help a lot. These tools quickly find defects and reduce mistakes made by people. By mixing manual checks with automated tools, you can make sure your PCBs meet high standards.
Adding these steps to your process will improve your PCB quality. Following pcb assembly rules lowers mistakes and earns customer trust.
Enhancing Product Quality Through Techniques and Standards
Making Products More Reliable
To make products more reliable, use better manufacturing methods. Follow pcb assembly rules to improve quality. Tools like Overall Equipment Effectiveness (OEE) and Overall Production Reliability (OPR) help measure success. OEE checks how close performance is to perfect. OPR looks at how dependable the whole system is. Fewer defects and happier customers also show better reliability.
Using quality checks like automated optical inspection (AOI) and functional testing helps a lot. These methods find problems early and prevent failures. By focusing on reliability, you gain customer trust and make products last longer.
Cutting Down Defects with Strong Rules
Following ipc rules helps lower defects in pcb assembly. These rules explain how to solder, place parts, and inspect boards. For example, IPC-A-610 ensures neat soldering and proper assembly. This reduces problems like solder bridging.
Defect rates and First Pass Yield (FPY) are key to tracking quality. Defect rates show how many products have issues. FPY measures how many items are made right the first time. The table below explains these terms:
Indicator | What It Means | How to Calculate |
---|---|---|
Defect Rates | Shows the percentage of faulty products. | (Number of Defective Units / Total Units Produced) x 100 |
First Pass Yield (FPY) | Shows the percentage of items made correctly the first time. | (Number of Units Completed Correctly on First Try / Total Number of Units Produced) x 100 |
Process Capability Index (Cpk) | Checks if a process meets limits. | Cpk = min((x̄ – LSL) / (3σ), (USL – x̄) / (3σ)) |
Using these rules lowers costs from bad quality, like fixing or replacing items. Training and tools like statistical process control also help reduce defects.
Keeping Manufacturing Consistent
Consistency in pcb manufacturing is key to making great products. Manufacturing Process Validation (MPV) checks if products meet quality and safety rules. This is very important for things like medical devices.
Quality checks like AOI, X-ray inspection, and in-circuit testing (ICT) help keep processes consistent. AOI finds soldering mistakes. X-ray checks hidden parts in complex designs. ICT tests electrical performance, and functional testing makes sure the pcb works as it should.
For instance, PCBasic uses these checks to ensure every pcb meets high standards. Consistent processes make reliable products, which improves your reputation and keeps customers happy.
Practical Tips for Effective PCBA Manufacturing
Using Design for Manufacturing (DFM) Principles
Using Design for Manufacturing (DFM) makes PCBA designs easier to produce. Involving engineers early helps cut costs and improve testing. Working together with design and manufacturing teams avoids delays and problems.
Here are some tips to improve DFM:
Check parts for availability, reliability, and environmental safety.
Arrange parts to manage heat and keep signals clear.
Use 3D tools to ensure parts fit and avoid clashes.
Follow Design for Assembly (DFA) to make assembly simpler.
These steps reduce mistakes and prepare designs for automated assembly. Tools like automated optical inspection (AOI) also improve quality by catching errors quickly.
Picking High-Quality Materials and Components
Choosing good materials and parts is key for reliable PCBA performance. Bad parts can cause failures, waste, and higher costs. Always buy from trusted suppliers and check specifications.
Important Factors | Why It Matters |
---|---|
Solder Mask Quality | Stops issues like bridging and provides proper insulation. |
Copper Plating Thickness | Improves how well the PCB conducts electricity and lasts longer. |
Component Reliability | Lowers failure risks and increases the number of good products made. |
Inspect and test materials before assembly to find problems early. This ensures your PCBs meet high-quality standards.
Using Advanced Testing and Inspection Methods
Advanced testing and inspection keep PCBA quality high. Tools like AOI and X-ray checks find problems fast. For example, AOI spots soldering mistakes, and X-rays find hidden issues in complex parts like BGAs.
Here are key testing methods:
Use in-line AOI to catch problems during production.
Do X-ray checks for parts with hidden connections.
Run burn-in tests for products needing high reliability.
Check your processes and suppliers regularly.
Modern tools, like the Koh Young KY8030-3, offer quick and accurate 3D checks. Adding these methods improves quality and builds customer trust.
Leveraging Automation for Efficiency
Automation helps make PCBA manufacturing faster and better. It takes care of repetitive tasks, reducing mistakes and saving time. Automated machines handle jobs like soldering, placing parts, and checking for errors with great accuracy. This keeps the quality the same for every batch.
A big advantage of automation is using resources wisely. Machines waste less material and use less energy, making production eco-friendly. For example, studies show automation can lower energy use by 40% and cut PCB waste by 60%. The table below shows these benefits:
Efficiency Metric | Improvement Percentage |
---|---|
Energy Use Reduction | 40% |
PCB Waste Reduction | 60% |
Automation also speeds up production a lot. Machines like pick-and-place systems can put together thousands of parts in an hour. This is much faster than doing it by hand and helps meet deadlines without losing quality.
It also improves testing and inspection. Tools like Automated Optical Inspection (AOI) and X-ray machines find problems quickly. These tools catch mistakes that people might miss, ensuring only top-quality products are made.
Tip: Start small when using automation. Begin with tasks that take the most time or have the most errors. Slowly add automation to other areas as you learn more.
Using automation makes production faster, cheaper, and better. It’s a smart way to stay ahead in the fast-moving electronics world.
Emerging Trends in PCBA Manufacturing
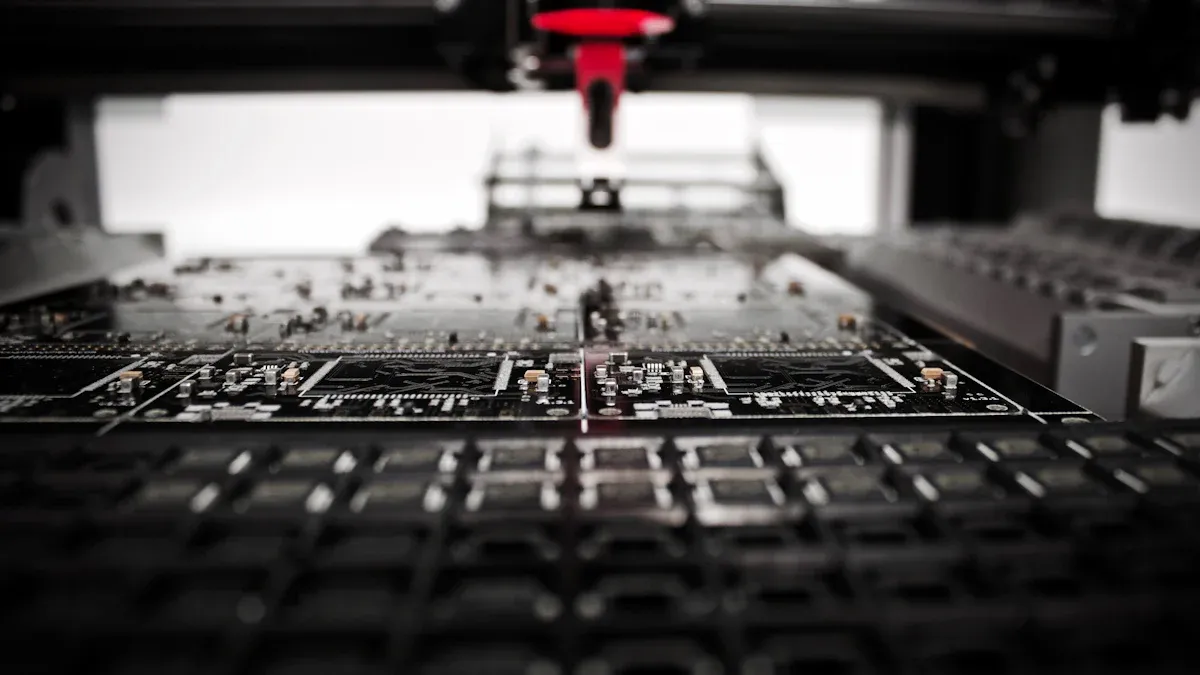
Advancements in Automation and Robotics
Automation and robotics are changing how pcb assembly is done. Robots work nonstop without getting tired, making production faster. They also place parts accurately, reducing mistakes from manual work. Automated tools like optical and X-ray systems find problems early, improving quality checks.
Automation offers more than just speed and accuracy. It saves money over time by cutting labor costs and wasting fewer materials. For example, robots can lower energy use by 40% and reduce pcb waste by 60%. These improvements make automation essential for modern pcb manufacturing.
Metric | What It Means |
---|---|
Increased Throughput | Robots handle more work faster than humans can. |
Enhanced Precision | Automation places parts correctly every time. |
Improved Quality Control | Automated tools catch problems early in production. |
Cost Efficiency | Saves money by using less labor and materials. |
Integration of AI and Machine Learning in Quality Control
AI and ML are improving quality checks in pcb assembly. ML programs find defects automatically, reducing the need for people to check. These programs spot even tiny flaws, ensuring high-quality boards.
AI also handles large amounts of data quickly, perfect for big production runs. Offline data analysis helps improve processes by finding new defect patterns. Adding AI boosts efficiency, cuts costs, and keeps you following ipc standards.
Evidence Type | What It Means |
---|---|
Automated Defect Detection | ML finds defects faster and more efficiently. |
Improved Accuracy | ML spots very small flaws that are easy to miss. |
Cost Reduction | Automation makes defect detection cheaper. |
Data Processing Speed | ML handles large data sets quickly. |
Continuous Optimization | Offline analysis helps improve production processes. |
Adoption of Sustainable Manufacturing Practices
Sustainability is becoming more important in pcb production. Companies are using greener methods to lower their environmental impact. Recycling materials and using low-temperature processes help reduce waste. For example, biodegradable materials are being tested to replace traditional pcb materials.
Making pcbs uses a lot of resources. Producing 100 small pcbs can take 1500 liters of water. The semiconductor industry uses over 500 billion liters of water each year. By adopting eco-friendly practices, you can save water, cut chemical waste, and reduce metal waste, meeting ipc standards for green production.
Evidence Type | What It Means |
---|---|
Water Usage | The semiconductor industry uses huge amounts of water. |
Chemical Waste | Chemicals from production create a lot of waste. |
Metal Waste | Metal scraps, like copper, come from trimming and etching. |
Tip: Start small with sustainable changes. Focus on areas like water and chemical use first.
New Ideas in PCB Assembly Methods
New ideas in making PCBs are changing how they’re built. These updates make work faster, cheaper, and more reliable. Learning about these changes helps you make better boards and follow IPC rules.
Important Changes in PCB Assembly
Recent studies show big changes in PCB assembly. These include smarter machines, better materials, and advanced design tools. The table below explains these updates:
Change | What It Does |
---|---|
Smarter Machines | AI and IoT make production faster and cheaper. AI tools find defects early. |
Better Materials | New materials like PTFE and carbon nanotubes improve performance. |
Advanced Design Tools | Software helps with heat control and signal problems. |
Faster Networks | New PCB designs meet the needs of 5G and future networks. |
These updates show how technology is improving PCB assembly. For example, AI tools catch mistakes early, helping you follow IPC rules.
New Ways to Make PCBs
3D printing and additive manufacturing are changing how PCBs are made. These methods save materials and allow quick testing of new ideas. Flexible PCBs and special materials are also becoming popular for their strength and performance.
Wearable devices and IoT gadgets need small, powerful PCBs. Using materials like PTFE helps meet these needs. Automated tools like AOI and X-ray checks ensure your boards meet IPC quality rules.
Using New Methods in Real Life
Smart devices and IoT need special PCBs for sensors and connections. Modern design tools help manage heat and signals better. This keeps your boards working well and meeting IPC standards.
New methods like 3D printing and flexible materials make stronger PCBs. These techniques also cut waste, helping the environment and supporting green manufacturing.
Learning PCBA manufacturing methods and following assembly rules is important. These steps help make strong and high-quality products. By using strict rules like IPC and ISO, you keep work consistent. This is needed for things like electronics, airplanes, and defense tools. Advanced tools like AOI and X-ray checks make products even better.
Using these methods lowers mistakes and earns customer trust. Knowing about new ideas like AI and eco-friendly ways keeps you ahead. Stick to these tips to do great in PCBA work and make amazing products.
FAQ
What helps make high-quality PCBA manufacturing?
Follow rules like IPC and ISO for better results. Use tools like AOI and X-ray to check for problems. These steps keep your process consistent and lower mistakes.
How can defects in PCBA manufacturing be reduced?
Stick to guidelines like IPC-A-610 for soldering and assembly. Use machines to test and inspect your work. Train your team to spot and fix problems early.
Why is automation useful in PCBA manufacturing?
Automation makes work faster and more accurate. Machines do repeated tasks quickly and with fewer mistakes. This saves time, cuts costs, and keeps quality steady.
What materials are best for PCBA manufacturing?
Pick strong and reliable materials. Use solder masks to stop bridging and thick copper plating for durability. Always buy parts from trusted suppliers.
How do eco-friendly methods help PCBA manufacturing?
Green practices cut waste and save water and energy. They follow environmental rules, improve your company’s image, and save money over time.
See Also
Guide to Assembling PCBA While Avoiding Frequent Mistakes
RSJPCBA’s Commitment to Quality in PCB and PCBA Production
Discover AI’s Role in Improving PCBA for Today’s Electronics
Comparing SMT and Through-Hole: Which PCB Assembly Wins?
Understanding Why FR-4 Dominates the PCB Manufacturing Industry