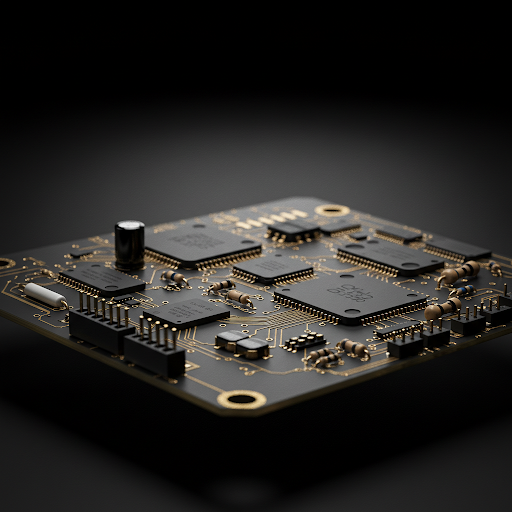
Manufacturing flex and rigid-flex PCBA manufacturing requires careful planning and focus. Every step, from selecting materials to assembly, must be precise. Choosing high-quality materials ensures they are strong and bendable. Intelligent designs enhance their performance. Quality checks are essential to prevent mistakes and ensure reliability. More industries are now adopting rigid-flex PCBA manufacturing, and their market is projected to grow by 10% annually until 2028. This growth highlights how they combine flexibility and rigidity, making them crucial for modern electronics. Understanding this process enhances products and paves the way for lasting success.
Key Takeaways
Use strong materials like polyimide for flex PCBs. This makes them tough and bendable, perfect for new gadgets.
Follow Design for Manufacturability (DFM) rules early on. This helps avoid mistakes and makes production smoother.
Do strict quality checks often. Testing and inspections find problems early, making PCBs work well and last longer.
Work with skilled manufacturers. Their knowledge helps prevent mistakes and improves the making process.
Use modern tools and machines. This gives better signals and smaller designs, keeping your products up-to-date.
Understanding Flex and Rigid-Flex PCBs

What Are Flex and Rigid-Flex PCBs?
Flex and rigid-flex PCBs are special circuit boards for modern gadgets. Flex PCBs use bendable materials, so they can twist without breaking. Rigid-flex PCBs mix stiff and flexible layers, making them strong and adaptable. These boards are grouped by their design and use:
Classification Type | Description |
---|---|
Performance Classes | Sets quality rules based on how they are used. |
Printed Board Types | Groups boards by complexity and number of layers. |
Installation Characteristics | Groups boards by how well they handle bending and tough conditions. |
There are five main types of these boards:
Type 1: One-sided flexible boards with one conductive layer.
Type 2: Two-sided flexible boards with two conductive layers.
Type 3: Flexible boards with three or more conductive layers.
Type 4: Rigid-flex boards with three or more conductive layers.
Type 5: Flexible or rigid-flex boards with two or more layers and no PTHs.
These groups help you pick the best board for your needs, ensuring it works well.
Applications and Benefits of Rigid-Flex PCBs
Rigid-flex PCBs are used in fields like aerospace, healthcare, and electronics. They are perfect for small, powerful devices because they mix flexibility and strength. For instance, smartphones and wearables use rigid-flex PCBs to save space and stay durable.
The rigid-flex PCB market is growing fast. In 2023, it was worth $1.2 billion and might reach $2.5 billion by 2032, growing 8.5% yearly. Multi-layer flex boards are leading this growth, as they are compact and high-density, reaching $7.4 billion in 2023.
This rise shows more people are using rigid-flex PCBs in advanced tech. These boards improve performance, lower weight, and boost reliability in designs.
Key Steps in Flex and Rigid-Flex PCBA Manufacturing
Material Selection and Preparation
Picking the right materials is key to making strong PCBs. Materials should be flexible, tough, and affordable. Polyimide substrates are popular for flex circuits. They resist water, dirt, and chemicals. These materials also handle high heat during soldering, making them great for hot environments.
Glue is important for keeping layers stuck together. Strong adhesives stop layers from peeling or cracking. Polyimide films protect the board’s wires from damage and weather, making them last longer.
For tough jobs like in space or medicine, choose materials that survive harsh conditions. New material discoveries help flex PCBs work better and support advanced designs. Good preparation ensures a smooth manufacturing process.
Tip: Match your materials to your project needs for better results.
Design Considerations for Flexibility and Durability
Good PCB design balances bending with strength. Designers must think about stress, weather, and how electricity flows. Flex PCBs can crack under pressure, so handle them gently. Separating parts helps avoid damage in moving or shaking environments.
Keeping signals clear is very important, especially for fast circuits. Nearby parts can mess up signals, so layouts should reduce interference. Heat control is also crucial. Flex PCBs must survive hot processes like soldering without breaking.
Smart designs make boards last longer. For example, raising the time between failures from 1200 to 2000 hours shows how better designs improve reliability. Careful planning ensures rigid-flex PCBs work well in tough situations.
Design Consideration | Impact on Strength and Flexibility |
---|---|
Risk of mechanical damage | Flex PCBs can crack under stress, so they need careful handling. |
Separating parts | Helps prevent damage in places with movement or shaking. |
Electrical interference | Nearby parts can disrupt signals, so layouts should reduce this problem. |
Keeping signals clear | Important for fast circuits to avoid losing or messing up signals. |
Managing heat | Necessary to keep flex PCBs working during hot processes like soldering. |
Layer Stacking and Lamination
Stacking and laminating layers are key steps in making PCBs. Good layer design keeps signals clear and controls electricity flow. Pick materials that make boards stable and easy to build. For example, switching prepreg directions and using extra copper layers can stop bending during lamination.
PCB thickness and copper sticking strength are important for testing lamination success. Stress relief stops layers from shifting, and watching the glass transition point (Tg) avoids peeling risks. Lamination also affects how electricity moves, helping with signal flow and stopping leaks.
Using advanced lamination methods makes rigid-flex PCBs stronger and more reliable. These methods improve both the board’s physical and electrical features, making them fit for complex designs.
Evidence Type | Description |
---|---|
Layer Design | Good layer design keeps signals clear and controls electricity flow. |
Material Choice | Picking the right materials improves board strength and ease of building. |
Lamination Methods | Techniques like switching prepreg directions and using extra copper layers stop bending and improve stability. |
Drilling, Plating, and Etching
Drilling, plating, and etching are key steps in making PCBs. These steps shape the board and make it work electrically. Each step needs careful attention for good results.
Drilling makes holes for connecting layers. Laser drilling creates tiny, accurate holes for modern designs. Cleaning the holes after drilling removes dirt and gets them ready for plating.
Plating adds a metal layer to the holes for connections. Electroplating puts copper inside holes and on the board’s surface. This makes strong and reliable connections. Watching plating thickness avoids problems like uneven copper.
Etching takes away extra copper, leaving circuit patterns. Chemical etching is the usual method. Controlling etching prevents mistakes like removing too much or too little copper.
Statistical methods help keep these steps accurate. They track important details to ensure the board meets quality standards.
Statistical Method | Description |
---|---|
Statistical Process Control | Tracks process details to find and fix problems early. |
Control Charts | Shows data visually to keep processes stable. |
Using these methods reduces mistakes and improves efficiency.
Assembly and Quality Testing
Assembly and testing turn the PCB into a working device. Components are added to the board carefully to avoid errors.
Surface mount technology (SMT) places parts directly on the board. This saves space and makes the board stronger. Soldering secures the parts in place. Good soldering stops weak joints or bridges.
Testing checks if the board works as planned. Both manual and machine tests are used. Common tests include:
Looking for cracks, peeling, or dirt on the board.
Using machines to spot bad solder or misplaced parts.
X-rays to find hidden solder problems.
Checking circuits for breaks or shorts.
Testing signals for high-speed designs.
Bending the board to test strength.
Checking glue strength between layers.
Each test ensures the board works well. For example, signal tests keep fast designs reliable. Bend tests check if the board can handle movement.
By combining careful assembly with strong testing, you make boards that last. This process meets industry rules and customer needs.
Best Practices for Flex PCB Manufacturing
Collaborating with Experienced Manufacturers
Working with skilled manufacturers helps make flex PCBs better. These experts know the process well and can avoid mistakes. They help pick materials, improve designs, and make production smoother.
Starting early with manufacturers is very helpful. They can spot problems in your design before they cause trouble. For example, they might suggest changes to stop peeling or bending during production. This saves time and money by reducing fixes later.
Tip: Talk to your manufacturer early in your project. Their advice can make the process easier and give better results.
Ensuring Design for Manufacturability (DFM)
Design for Manufacturability (DFM) makes flex PCBs easier to build. It reduces mistakes, improves success rates, and makes products more reliable.
DFM checks your design at different steps, like picking parts and planning layouts. This helps find problems early and makes production smoother.
DFM analysis should happen at many stages, like part selection and layout planning. It helps catch issues early and improves production success.
Benefits of DFM include:
Early teamwork with manufacturers to fix problems quickly.
Better production processes for faster and easier manufacturing.
Solving issues early for a smooth move from design to production.
By focusing on DFM, your flex PCB design will work well and be easy to make. This leads to a stronger and more affordable product.
Leveraging Advanced Equipment and Technology
Using modern tools and technology makes flex PCB production better. These tools help create high-quality boards for today’s advanced devices.
For example, High-Density Interconnect (HDI) flexible PCBs are very useful. They improve signal quality and reduce interference. These features are important for devices like phones and medical tools. Many industries use HDI flex PCBs because they are reliable and versatile.
Advantages of advanced technology include:
Better signal quality for fast and powerful devices.
Less interference, making devices more dependable.
Smaller, lighter designs that still work well.
By using the latest tools and methods, you can stay competitive and deliver great products to your customers.
Implementing Rigorous Quality Control
Quality control is key to making great flex PCBs. Testing and inspections help find problems early. This improves reliability and avoids expensive mistakes. A strong quality program makes PCBs work better and builds customer trust.
Key Testing Methods for Quality Assurance
Advanced testing ensures every PCB meets high standards. These tests check for issues and improve product quality. Below is a table of important testing methods:
Testing Method | Purpose |
---|---|
Automated Optical Inspection (AOI) | Finds problems like bad solder or broken joints. |
Electrical Testing | Checks for faults, signal issues, and leftover materials. |
Mechanical Testing | Tests the PCB’s strength and durability. |
Reliability Assessments | Measures how well the PCB works in tough conditions. |
Each test focuses on a specific area to ensure the PCB works well in real-life situations.
Certifications and Standards
Following industry rules is important for quality control. Certifications like ISO 9001 and IPC show your work meets global standards. These prove your PCBs are reliable and well-made.
Tip: Regular checks and audits help you stay compliant and improve processes.
Benefits of Rigorous Quality Control
Strong quality control has many benefits. Finding problems early saves money and avoids recalls. For example, checking designs and processes makes fixing issues easier and cheaper.
This approach reduces failures and makes customers happier. It also boosts your reputation as a trusted manufacturer. This gives you an advantage in the market.
By focusing on quality control, you can make strong, reliable PCBs for modern devices.
Overcoming Challenges in Rigid-Flex PCB Manufacturing
Managing Material Stress and Flexibility
Handling material stress is key to making strong, flexible PCBs. Choose materials that can bend often and handle tough conditions. Advanced options like graphene are great because they are flexible and conduct electricity well. Coatings spread out stress, lowering the chance of cracks or breaks.
New methods help manage stress better. For example, laser direct imaging (LDI) makes patterns more accurate. Roll-to-roll (RTR) lamination speeds up work by layering multiple sheets at once. Smart designs, like wavy paths for circuits, let them stretch without breaking.
Tip: Test your designs with thermal cycling and flex tests. These tests mimic real-life use to find weak spots early.
Evidence Type | Description |
---|---|
Advanced Materials | Graphene adds flexibility and conductivity for thinner boards. |
Stress Mitigation | Coatings and materials spread stress evenly to avoid damage. |
Design Strategies | Wavy paths stop circuits from breaking when bent or stretched. |
Avoiding Delamination and Warping
Delamination and warping are common problems in PCB making. Uneven heat or mismatched material expansion often causes these issues. To stop warping, balance copper layers and stack them evenly. Dummy planes can also reduce stress on uneven copper areas.
Delamination happens more with too much heat or moisture. Control resin flow and keep temperatures steady during production. Store boards in dry places and bake them before heating to avoid these risks.
Key Prevention Tips:
Balance copper layers to prevent warping.
Stack layers evenly to avoid bending.
Manage resin and heat carefully during production.
Note: Regular checks during production can catch these problems early and fix them.
Ensuring Signal Integrity in Complex Designs
Good signal flow is vital for high-tech PCBs. Bad signal handling can cause data loss or interference. Controlled impedance design helps signals move smoothly without bouncing back. Grounding and shielding protect parts from electromagnetic interference (EMI).
Electromagnetic compatibility (EMC) tests ensure your designs follow rules. Tools like spectrum analyzers check for emissions and immunity, helping you make reliable products.
Technique/Standard | Description |
---|---|
Controlled Impedance Design | Keeps signals smooth for better performance. |
Shielding | Blocks outside electromagnetic fields from affecting parts. |
EMC Testing Standards | Makes sure designs meet rules for emissions and immunity. |
By solving these problems, you can build strong, reliable rigid-flex PCBs that meet industry needs.
A clear process is key for making flex and rigid-flex PCBs. It helps them stay strong, reliable, and work well. Using smart methods, like working with experts and using new tools, lowers risks and boosts efficiency. Careful testing and quality checks make sure the boards are dependable.
Key Lessons from Industry Research | Why It Matters |
---|---|
Following quality rules | Makes rigid-flex PCBs strong and long-lasting. |
Fine-line and microporous tech | Helps create compact and advanced designs. |
Testing during early stages | Lowers chances of failure and improves reliability. |
Skilled manufacturers | Reduces risks and ensures high-quality production. |
Organized manufacturing steps | Solves layout and strength issues for better performance. |
By focusing on teamwork and new ideas, you can make flexible PCBs that meet today’s needs and stay top quality.
FAQ
What makes flex PCBs different from rigid-flex PCBs?
Flex PCBs can bend completely, while rigid-flex PCBs mix stiff and bendable parts. This mix makes rigid-flex PCBs strong and flexible, perfect for tough designs and hard conditions.
How do you pick the best materials for flex PCBs?
Choose materials that are bendable, strong, and resist damage. Polyimide substrates are common because they handle heat and last long. Always pick materials that fit your project for the best results.
Tip: Ask your manufacturer for advice on the best materials for your design.
Why is checking quality important in PCB making?
Quality checks make sure PCBs work well and last long. They find problems early, saving money and time. Tests like electrical and strength checks ensure boards work properly in real-life use.
Can flex PCBs support fast signals?
Yes, flex PCBs can handle fast signals if designed well. Keeping impedance steady and using shielding reduces signal problems. These methods help them work well in advanced tech like phones and medical tools.
How do you stop rigid-flex PCBs from peeling?
Stop peeling by balancing copper layers and controlling resin flow. Keep heat steady during production. Store boards dry and bake them before heating to avoid moisture issues.
Note: Check boards often during production to catch problems early.
See Also
Achieving Excellence in PCBA Manufacturing Techniques and Quality
Comparing Turnkey and Consignment PCBA Manufacturing Approaches
Choosing the Ideal PCBA Manufacturer to Meet Your Requirements
Speeding Up PCBA Production While Maintaining Top Quality
Essential Best Practices for Low-Volume PCBA Production Explained