
You see PCBA daily without knowing it, but what is PCBA? It powers things like phones, smart gadgets, and wearables. The PCB market might grow from $80.33 billion in 2024 to $96.57 billion by 2029, highlighting its importance. Since the 1960s, PCBA has evolved from simple calculator circuits to small IoT designs. This progress supports the increasing number of connected devices, which reached 16.7 billion in 2023. Learning what PCBA is and how it works reveals its significant role in technology today.
Key Takeaways
PCBA, or printed circuit board assembly, is key for modern gadgets like phones and smartwatches.
Using good materials and parts makes PCBA work better and last longer.
Checking for problems during production helps fix them early and saves money.
Using green materials and recycling can make PCBA less harmful to the planet.
Working with trusted PCBA makers gives better tools and steady quality, avoiding delays.
What is PCBA and Why is it Important?
Definition and Role of PCBA in Electronics
When people ask “what is PCBA,” it means printed circuit board assembly. This process involves attaching electronic parts to a plain PCB to make it work. PCBA is like the heart of modern gadgets. It links and powers parts like resistors, capacitors, and microchips. Without PCBA, devices such as phones, laptops, and smartwatches wouldn’t work.
PCBA’s importance shows in its rising market value. In 2023, the PCB and PCBA market was worth $68.4 billion. By 2032, it may grow to $105.8 billion, with a yearly growth rate of 4.9%. This rise comes from more demand for electronics and better car technology. Clearly, PCBA is shaping the future of tech.
Key Features of PCBA in Modern Devices
PCBA has many features that improve how devices work and last. These include special materials, inspection tools, and uses in different fields.
Material | Properties | Applications |
---|---|---|
Polyimide Substrates | Handles heat well, flexible | Used in military and space tech |
Rogers Materials | Low signal loss, great dielectric traits | Used in RF and microwave devices |
Metal Core PCBs | Better heat transfer | Used in LED lights, power gadgets |
Silver Conductive Inks | High conductivity, thin lines | Used in touchscreens, flexible screens |
Copper Conductive Inks | Affordable, resists rust | Used in RFID tags, antennas |
Carbon Conductive Inks | Strong and bendable | Used in printed sensors, electrodes |
Modern PCBA checks ensure devices work well. Tools like Automated Optical Inspection (AOI) and X-ray Inspection find problems fast. AI tools can check thousands of parts quicker than older methods. This makes PCBA vital for complex designs.
PCBA is useful in many industries. In healthcare, it powers MRI machines and prosthetics. In electronics, it helps make small gadgets like smartphones and wearables. These features make PCBA a key part of today’s technology.
Advantages of PCBA
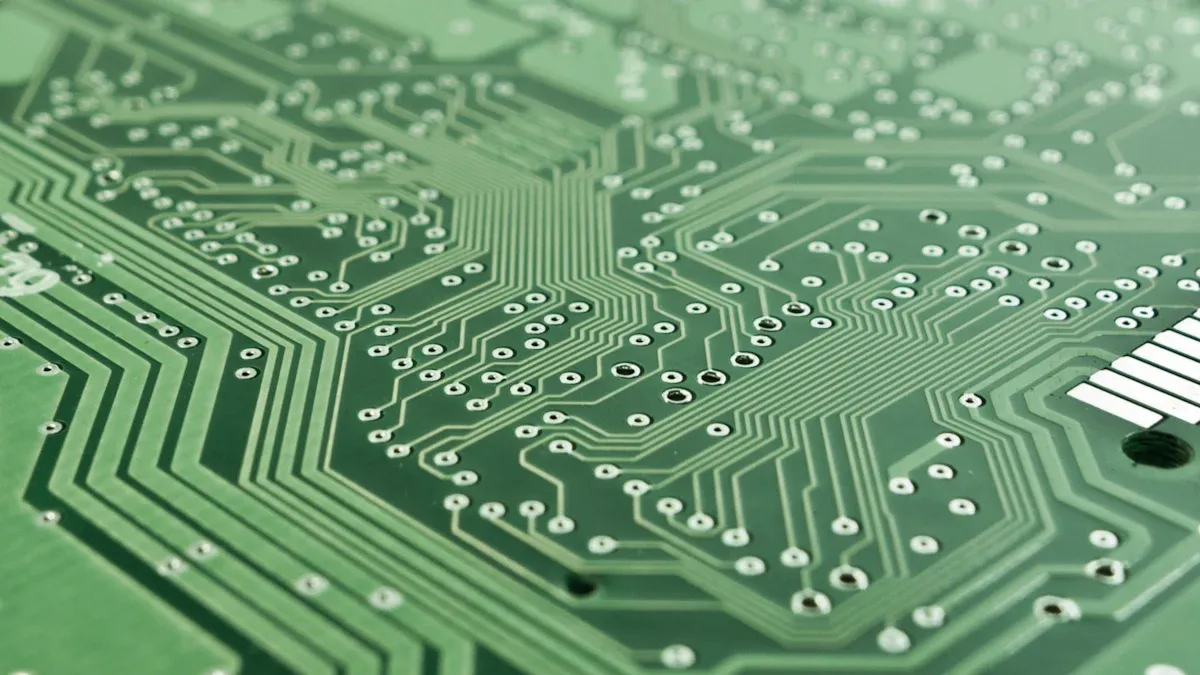
Compact and Space-Efficient Design
PCBA helps make devices smaller and more space-saving. Modern gadgets need to be tiny but still work well. PCBA combines many parts on one PCB, cutting down on wires. This allows for slim and lightweight designs.
Flexible printed circuits (FPCs) are key to shrinking device size and weight. They can lower wiring costs by up to 70% while being more reliable. FPCs are also strong and resist electromagnetic interference, making them great for small devices like phones and wearables.
Advantage | Description |
---|---|
Size and Weight Reduction | FPCs make devices lighter and smaller, improving reliability. |
Mechanical Resistance | FPCs resist heat, wear, and electromagnetic interference (EMI). |
With PCBA, manufacturers can build smaller, tougher, and more efficient devices. This makes PCBA essential in industries like electronics, cars, and healthcare.
Enhanced Reliability and Durability
PCBA is very reliable, which is crucial for today’s gadgets. Makers test PCBAs to handle tough conditions like heat, humidity, and vibrations. These tests mimic real-life situations to ensure durability.
Temperature Cycle Test: Checks performance in extreme hot or cold.
Heat and Humidity Test: Tests strength in wet conditions.
Vibration Test: Ensures stability during movement.
Impact Test: Measures resistance to drops or hits.
Electrical Test: Confirms steady electrical performance.
These tests show how strong PCBAs are. For example, vibration tests check if parts stay secure, and temperature tests measure heat resistance. Testing improves reliability and lowers failure risks.
Quality Assurance: Ensures PCBAs work well in all conditions.
Cost Savings: Finds problems early, avoiding expensive fixes.
Safety: Prevents failures in important devices, keeping users safe.
By focusing on durability, PCBA helps create long-lasting devices that work in many environments.
Cost-Effectiveness in Mass Production
PCBA is cost-friendly, especially for large-scale production. Automated processes reduce labor costs and boost efficiency. For instance, automation can cut labor costs by 40% and save over $18,000 in rework expenses.
Cost-Saving Strategy | Impact on Costs |
---|---|
Material Selection | Saves 20-30% with cheaper materials. |
Production Automation | Cuts labor costs by 40%. |
Quality Control | Saves $18,000+ by reducing rework. |
Defect Rate Reduction | Lowers defects from 8% to 1.2%. |
ROI for Automation | Pays off in 14-18 months. |
Choosing the right materials also saves money. For example, FR-4 works for high-frequency needs, while CEM-1 is good for budget-friendly products. Quality checks reduce defects, making production smoother.
PCBA’s cost benefits make it ideal for industries needing affordable, reliable devices. By cutting costs and improving efficiency, PCBA helps create high-quality electronics at lower prices.
High Performance and Reduced Noise
Modern electronics need to work well and stay clear of noise. PCBA helps devices run smoothly and keeps signals clear. Using smart designs, PCBA boosts performance and cuts down interference.
A key way to check noise in PCBA is the Signal-to-Noise Ratio (SNR). SNR shows how strong a signal is compared to background noise. A higher SNR means clearer signals and better performance. For example:
High SNR gives better sound and picture quality.
It ensures steady data transfer in communication systems.
Less noise makes circuits more reliable for important uses.
To improve performance, makers focus on fast signal movement. Shorter signal paths on PCBs reduce loss and interference. Grounding and shielding also help stop electromagnetic problems. This keeps devices stable even in noisy environments.
By using these methods, devices become more reliable and work better. Whether for home gadgets or industrial tools, reducing noise and boosting performance are big PCBA benefits.
Scalability for Complex Designs
As gadgets get smarter, PCBA must handle more complex designs. PCBA is flexible and can grow with new needs. This is vital for industries like healthcare, cars, and telecoms, where small and advanced designs are key.
Modern PCBA methods support designs that allow for growth. For example:
Design Technology | Benefits |
---|---|
High-Density Interconnect | Sharper signals, stronger boards, lighter materials, better heat control. |
Flexible PCBs | Fits many layers, saves space, allows bendable designs. |
Modular Design Methods | Adds more parts in small spaces, making designs easier to scale. |
High-Density Interconnect (HDI) lets more parts fit in less space. This makes boards smaller and speeds up signals. Flexible PCBs allow creative designs, perfect for wearables and tiny gadgets.
Scalability also lowers costs. Modular designs make building and testing faster and cheaper. This saves money without losing quality.
Adding scalable designs to PCBA keeps devices ready for future needs. Whether simple or complex, scalability helps meet today’s tech demands.
Disadvantages of PCBA
Manufacturing Complexity and Costs
Making a PCBA is a detailed process. It can be tricky and costly. As gadgets get smaller and smarter, manufacturers need advanced designs. These designs require careful work, which makes production harder. For example:
Tiny, dense designs need special tools and skilled workers.
5G and IoT devices need stronger and more stable PCBs.
Custom designs make the process even more challenging.
The cost of making PCBAs depends on many things. Materials like copper and solder can be expensive. Steps like drilling and soldering need special machines, which add to costs. Skilled workers also increase expenses. Complex designs can lead to more mistakes, raising costs further.
To handle these issues, companies use better methods and machines. Automation can lower labor costs, but buying new equipment is pricey. Balancing these costs is key to keeping PCBs strong and affordable.
Environmental Impact of Materials and Processes
Making PCBs uses a lot of resources and harms the environment. The process needs a lot of water. For example, making 100 small PCBs uses about 1500 liters of water. This high water use adds to environmental problems.
Chemicals used in PCB production also cause harm. Etching chemicals can pollute water and damage the ozone layer. Old PCBs add to e-waste, which can leak harmful materials into nature.
To reduce harm, companies are trying eco-friendly methods. Using lead-free solder and water-based solutions helps cut pollution. Recycling and managing waste are also important. These steps help make PCB production better for the planet.
Risk of Component Failure and Repair Limitations
PCBA parts can fail for many reasons. Stress, heat, and weather can weaken a PCB. Electrical problems and aging also cause failures. For example, shaking or dropping a device can break parts. Extreme heat or cold can damage the board.
Manufacturers study how and why parts fail. This helps them design better PCBs. But fixing broken PCBAs is hard. Modern boards are small and complex. Replacing one part can damage the whole board.
Examples show why good design is important. Bad patterns on a PCB can cause soldering problems. This makes the board less reliable. By focusing on strong designs and quality checks, companies can make PCBAs that last longer and work better.
Dependence on Specialized Equipment and Expertise
Making PCBA needs special tools and skilled workers. Advanced machines like pick-and-place systems and soldering stations are key. These tools help make sure the boards are precise and reliable. Without them, it’s hard to meet the high standards of modern electronics.
The process also needs a strong support system. This includes special materials, design software, and skilled technicians. For example:
Special machines keep the circuit board safe during assembly.
Trained workers run the machines and fix problems.
Design software helps create better layouts for performance.
Using these tools and skills increases production costs. Companies must train workers and maintain expensive machines. Automation can save money on labor, but it costs a lot upfront. Smaller companies may find it hard to afford these resources.
To solve this, working with expert PCBA makers can help. These partnerships give access to the right tools and knowledge. This reduces risks and ensures your products stay high-quality and reliable.
Supply Chain Vulnerabilities
PCBA production depends on a steady supply of materials. Items like copper, solder, and substrates are needed to make boards. If these materials are delayed or unavailable, production stops, and costs go up.
Problems in the supply chain often come from outside events. Natural disasters, political issues, or pandemics can disrupt supplies. For example, during COVID-19, factory closures caused delays in PCB production. These events show how global supply chains can fail.
Another issue is relying on specific suppliers for key parts. If one supplier fails, finding a replacement can take time. This can hurt product quality and damage trust. Also, changing prices for materials like copper can affect budgets.
To handle these problems, companies can use several strategies. They can work with more suppliers and keep extra materials in stock. Building local factories can also reduce dependence on global networks. Planning ahead helps avoid risks and keeps production running smoothly.
Practical Tips for Improving PCBA Usage
Picking the Best Materials and Parts
Choosing good materials and parts makes PCBs work better. Think about strength, conductivity, and price. Polyimide handles heat well, so it’s great for hot environments. Rogers materials lose less signal, making them ideal for RF devices. Flexible PCBs use bendable materials, which fit small gadgets like wearables.
Always pick quality parts that match your design. Cheap parts can break and cost more to fix later. Working with suppliers helps you get better materials. Using eco-friendly options, like lead-free solder, is better for the planet and still works well. Smart choices make PCBs strong and eco-friendly.
Adding Quality Checks
Quality checks make sure PCBs work as they should. Testing finds problems early and improves reliability. AOI systems spot missing parts or bad soldering. X-ray tests find hidden issues like shorts. Functional tests check if the PCB works in real-life situations.
Steps for quality control include:
Checking materials when they arrive.
Inspecting the first batch to ensure processes are correct.
Watching production to catch issues early.
Testing boards to see if they handle stress well.
Using AI tools can lower defects and improve reliability. These steps help make PCBs that last and meet high standards.
Designing for Easy Production
Designing for easy production saves time and money. Work with manufacturers early to make assembly simpler. Their advice can prevent mistakes and delays.
HDI technology makes smaller boards with faster signals. Modular designs allow scaling while keeping quality. Flexible PCBs let you create unique layouts for modern gadgets. Good planning speeds up production and ensures high-quality PCBs.
By following these tips, you can design PCBs that are affordable and ready for large-scale production.
Addressing Environmental Concerns Through Sustainable Practices
Making PCBA more eco-friendly is now very important. There are ways to lower the environmental harm of making circuit boards. Recycling is one key solution. Studies show recycling chips can cut the environmental impact of gadgets like remotes by over 50%. Small changes in how we make things can have a big effect.
Using greener materials also helps the planet. Lead-free solder and water-based solutions create less pollution. Picking materials that are easier to recycle, like certain board types, reduces waste. These choices make the production of circuit boards cleaner and better for the environment.
Energy-saving methods in factories also help. Many factories now use renewable energy and efficient machines to lower emissions. For example, automated systems reduce waste and save energy during production. These steps make circuit boards with less harm to nature.
Managing waste is just as important. Properly disposing of chemicals and recycling old boards keeps harmful materials out of the environment. Working with recycling programs ensures old boards are handled safely. These actions protect the earth and support global eco-friendly goals.
Partnering with Reliable PCBA Manufacturers
Picking the right PCBA maker is key to good circuit boards. Reliable makers bring skill, advanced tools, and steady quality. They help avoid problems and ensure your products meet high standards.
Experienced makers use modern machines for tricky designs. Their factories often have automated tools for precise assembly and testing. This makes your circuit boards strong and efficient. By teaming up with them, you get top technology without buying costly equipment.
Good manufacturers focus on quality checks. They inspect every step, from picking materials to final tests. This lowers the chance of mistakes and ensures your boards work well in real life.
Trusted makers also have strong supply chains. They get good materials and keep production steady, even during global issues. This avoids delays and keeps your projects on time. Working with a reliable maker gives you confidence and helps you deliver great products to your customers.
PCBA is important for modern electronics. It helps make small, reliable, and affordable devices. But making PCBAs can be hard and may harm the environment.
Advantages | Problems |
---|---|
Very dependable | Costs a lot to make |
Saves space | Hard to produce |
Works well with fast signals | |
Handles heat | |
Keeps signals clear over long distances | |
Good for tough places like space or hospitals |
In the future, PCBA will keep improving and changing electronics.
Robots will make PCBA faster and more accurate.
5G will need new PCB designs and better materials.
Eco-friendly methods will focus on saving the planet.
Smaller designs will fit more parts into tiny gadgets.
Smart PCBs will help IoT devices with sensors and controls.
By using its strengths and fixing its problems, PCBA can stay useful for making great electronics.
FAQ
What is the difference between PCB and PCBA?
A PCB is just a plain board with no parts. A PCBA has all the parts attached, so it works. Think of a PCB as a frame and a PCBA as the finished product.
Why is PCBA important in modern electronics?
PCBA helps make devices small, strong, and useful. It links and powers parts like chips and resistors. This makes gadgets like phones, laptops, and medical tools work. Without PCBA, these devices wouldn’t exist.
Can PCBA be recycled?
Yes, PCBA can be recycled. Special methods recover materials like copper and gold. Harmful parts are safely removed. Recycling lowers e-waste and helps the environment.
How do you ensure PCBA quality?
Makers use tests like AOI and X-ray to find problems. They also test how PCBA works in real-life situations. Checking at every step ensures the PCBA works well.
What industries benefit most from PCBA?
PCBA is key in healthcare, cars, telecom, and electronics. It powers things like MRI machines, electric cars, phones, and smart gadgets. These industries rely on PCBA to function.
See Also
Innovative Technologies Shaping PCBA Production For Today’s Electronics
Exploring Sub PCBA Uses In Electronics And Other Fields
Discover The Role Of AI In Advancing PCBA Technology
Outsourcing Medical Device PCBA: Benefits And Drawbacks To Consider
Comparing Turnkey And Consignment PCBA Manufacturing Approaches In 2025