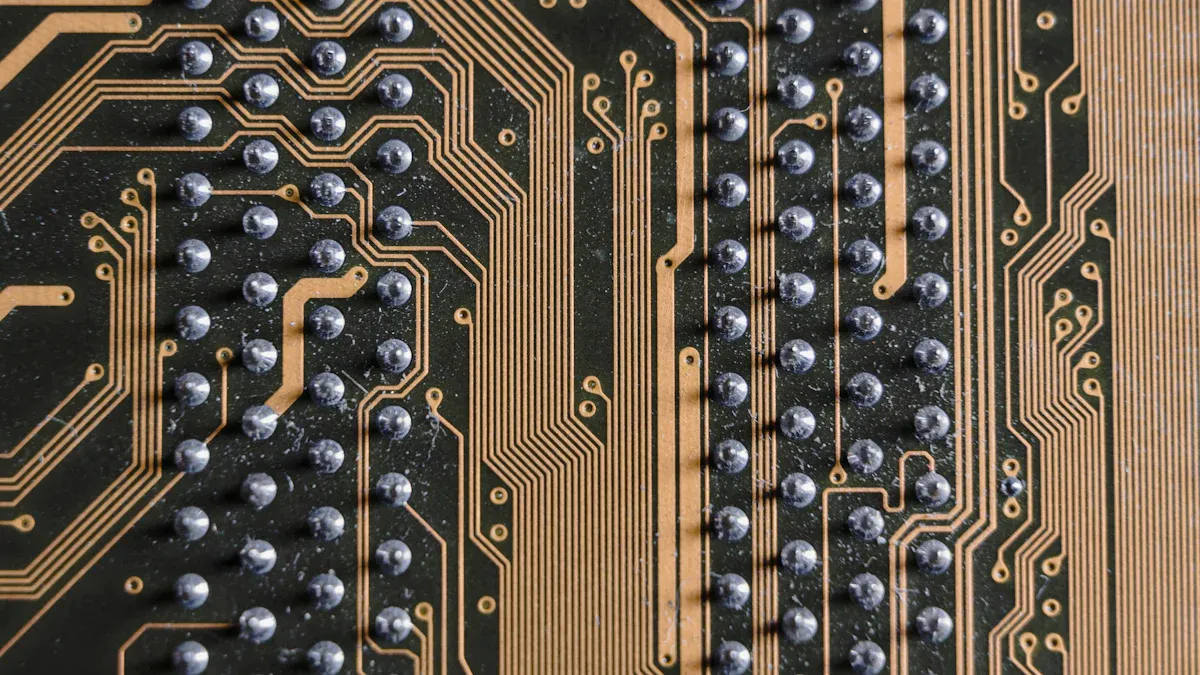
When it comes to PCB assembly, small errors can lead to significant problems. Identifying and resolving issues early in the process helps ensure your boards function effectively. Addressing problems promptly not only saves time but also enhances the reliability of your PCB assembly. So, why wait for issues to arise when you can tackle them early on?
Key Takeaways
Design for easy manufacturing (DFM) to avoid mistakes and make better PCBs. Work with your manufacturer early for a smooth assembly process.
Avoid placing parts wrong by matching your parts list (BOM) with the PCB design. Use machines to check for mistakes early.
Test every PCB carefully to find problems before shipping. Keep testing tools updated and write down results to help future projects.
Design for Manufacturability (DFM) Challenges
Why DFM Matters in PCB Assembly
Design for Manufacturability (DFM) is key to smooth PCB assembly. It means designing your PCB so it’s easy to make without mistakes. Focusing on DFM lowers the risk of errors and improves board quality. Think of it as building a strong base for success. Without DFM, even great designs can face production problems.
Common DFM Mistakes to Watch For
Some DFM mistakes happen often, but you can avoid them. Here are a few examples:
Part Number and Package Mismatch: This happens when the part number in your Bill of Materials (BOM) doesn’t match the PCB layout. It can waste boards or cost extra to fix.
DNP Parts Listed Wrongly: If “Do Not Place” (DNP) parts are in your BOM or pick-and-place file, it can confuse the process.
Missing Part Numbers for Passives: Only listing sizes and values for passive parts without part numbers can cause trouble, especially with turnkey services.
Avoiding these errors makes assembly much easier.
Tips for Better DFM
Want to do DFM right? Work with your manufacturer early in the design stage. They can share tips to match their process. Use tools to check for manufacturability issues before production. Review your BOM and layout to ensure they match. Also, write clear instructions for everything. A little effort now can save big problems later.
Pro Tip: Talk to your assembly team often. They can help catch issues early and save money.
Component Placement Mistakes
Why Components Get Misplaced
Components can be misplaced due to pick-and-place machine errors. Unclear design files also cause problems. If your PCB layout doesn’t match the BOM, parts may go in the wrong spots. Outdated or incomplete documents can make things worse. Even small mistakes, like wrong orientation markers, can create big assembly issues.
How Misplaced Components Affect PCBs
Misplaced parts can harm your PCB’s performance and reliability. Here’s why:
Wrong or missing parts make the board wear out faster.
High-frequency PCBs, like those in 5G, need exact placement. Small mistakes can cause data loss or failed communication.
Poor tolerances may lead to cracks or damage, ruining functionality.
These issues don’t just hurt performance—they also raise repair and replacement costs.
Fixing Placement Mistakes
You can prevent placement mistakes by improving your process. Check your BOM and layout to ensure they match. Use automated optical inspection (AOI) to find errors early. Work with your assembly team to give clear instructions and correct orientation markers.
Here’s how fixing placement mistakes has helped industries:
Industry | Better Assembly Accuracy | Fewer Assembly Errors | Lower Maintenance Costs |
---|---|---|---|
Consumer Electronics | 10% | N/A | N/A |
Automotive | N/A | 15% | N/A |
Aerospace and Defense | N/A | N/A | 20% |
Following these steps helps your PCB assembly work better and stay reliable.
Soldering Defects in PCB Assembly
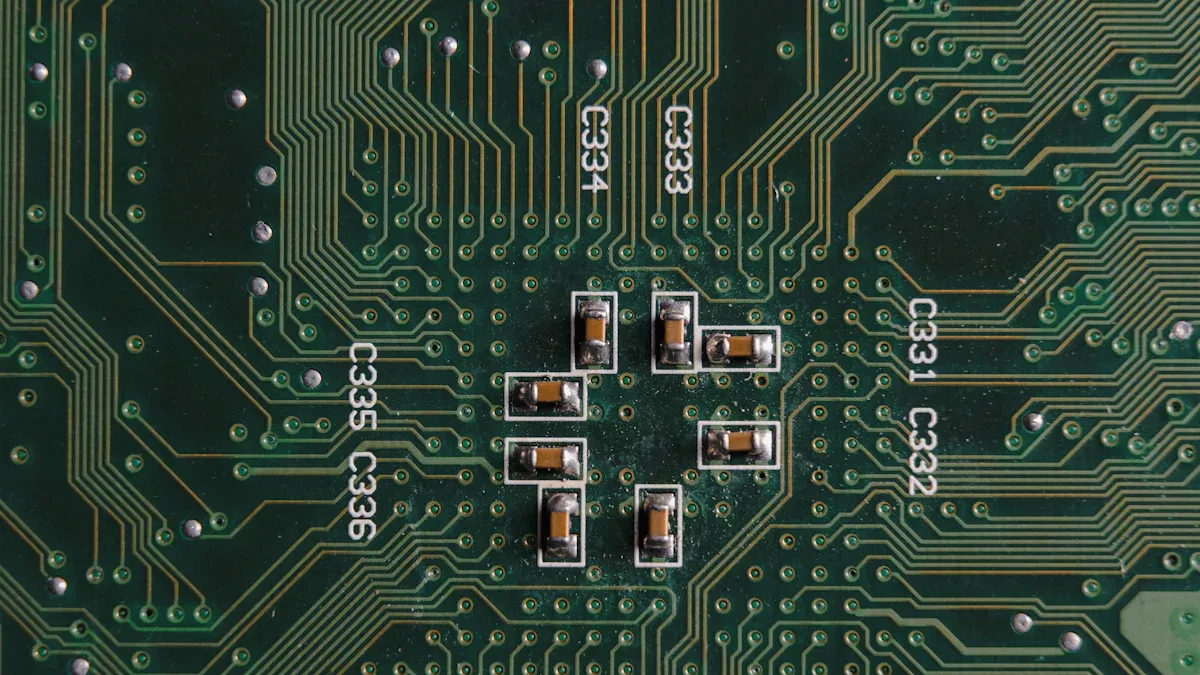
Common Types of Soldering Defects
Soldering problems can happen if you’re not careful. Some common ones are:
Cold Joints: These happen when solder doesn’t melt fully, making weak links.
Solder Bridges: Too much solder can connect parts by mistake, causing shorts.
Insufficient Solder: Not enough solder leads to bad electrical connections.
Excess Solder Blobs: Big blobs can block parts or cause overheating.
These problems can hurt how your PCB works, so fix them early.
Effects on PCB Performance
Soldering problems don’t just look bad—they can cause big issues. Cold joints may create loose connections, making the board unreliable. Solder bridges can short-circuit the board and damage parts. Too little solder weakens the flow of electricity. Big solder blobs might overheat or harm other parts. These problems can shorten your PCB’s life and cost more to fix.
Tip: Check solder joints closely. Smooth and shiny joints mean good soldering.
Preventive Measures for Soldering Issues
You can stop soldering problems by following simple steps:
Solder small parts first so bigger ones don’t get in the way.
Save delicate parts for last. Use low heat and heat sinks to protect them.
By doing these steps, you’ll lower soldering problems and make better PCBs.
Insufficient Testing and Quality Control
Why Testing Matters in PCB Assembly
Testing is very important to make sure PCBs work well. It finds mistakes early, saving money on fixes later. Manual or semi-automated testing makes production faster and more consistent. This reduces errors during assembly. Using electronic records during testing helps you see problems quickly. You can fix issues right away and improve the process.
Functional testing is also very important. It checks for problems before shipping the PCB. This testing doesn’t just find bad parts. It also helps you understand why the problem happened. Fixing these issues improves quality and helps with future projects.
Common Testing Errors
Skipping or rushing testing is a big mistake. Some people only use visual checks, which miss hidden problems. Others test too few boards, thinking one or two are enough. Old testing tools are another problem. They might not catch modern issues, leading to bad results.
Ignoring documentation is another error. Without clear records, it’s hard to know what went wrong. This can cause repeated mistakes and waste time.
Better Testing Methods
You can avoid mistakes by following simple steps. Test every board, not just a few. This helps catch all problems. Use both manual and automated testing for better results. Machines are fast and accurate, but people can spot things machines miss.
Keep your testing tools updated. New tools find today’s complex problems better. Also, write down everything during testing. Good records help you find patterns and avoid future issues. These steps will make your PCB assembly more reliable and higher quality.
Thermal Management Problems
Why Heat Control Matters
Heat can quietly damage your PCB assembly. If heat isn’t managed well, parts can overheat and fail. This might even cause the whole board to stop working. Good heat control keeps your PCB running safely, even in hot conditions. Engineers use special tools to design boards that handle heat better. This helps keep temperatures steady and makes electronics last longer.
Thermal profiling is very important. It helps create strong solder joints and avoids problems. Things like oven heat, conveyor speed, and solder paste affect how heat is handled. By improving these, you can stop heat problems and make assembly better.
Signs of Bad Heat Management
How can you tell if your PCB has heat issues? Watch for these signs:
Problem | What Happens |
---|---|
Too much heat | Parts fail, circuits weaken, and layers may peel apart. |
Thermal shock test | Finds stress, cracks, or broken parts caused by heat changes. |
Burn-in testing | Checks performance for 40-160 hours at high heat (up to 125 °C). |
These signs show serious trouble. Ignoring them can lead to expensive fixes or replacements.
Fixing Heat Problems
You can solve heat issues with smart designs. Try these methods:
Heat Control Method | What It Does | Why It Helps |
---|---|---|
Lowers resistance and heat build-up. | Keeps parts cooler and more reliable. | |
Grouping parts by heat levels | Stops hotspots and spreads heat evenly. | Protects the board from overheating. |
Built-in heat pipes | Moves heat using liquid evaporation. | Improves cooling in small designs. |
Liquid cooling systems | Uses coolant to absorb heat. | Handles heavy heat loads for tough tasks. |
Heat simulation tools | Shows where heat builds up. | Helps design better boards. |
Using these ideas, you can keep your PCB cool and working well, even in tough situations.
Low-Quality Components
Risks of Substandard Components
Using bad components in PCB assembly can cause many problems. These parts often don’t meet design needs, making circuits unstable. For example, wrong parameters or poor PCB design can cause signal issues. Leftover dirt from bad cleaning or cheap cleaners can hurt your board’s performance. Broken parts, damaged by static electricity or physical stress, also increase failure risks.
Here’s a simple table of symptoms, causes, and fixes:
Symptoms | Causes | Solutions |
---|---|---|
Unstable circuit functionality | Wrong component parameters | Use parts that match design needs |
Poor PCB design, like signal mismatches | Fix PCB design for better signal flow | |
Residual contaminants | Bad cleaning process | Clean thoroughly to remove all dirt |
Cheap cleaning products | Use good-quality cleaners to avoid residue | |
Damaged components | Static electricity (ESD) damage | Use anti-static tools like wrist straps |
Too much voltage or current | Add protection against high voltage and current | |
Physical stress breaking parts | Handle parts carefully during assembly |
How to Source High-Quality Components
Finding good parts doesn’t have to be hard. Work with trusted suppliers who have a good reputation. Check if they have certifications to prove their parts are high quality. Always double-check part details to match your PCB design. If you can, test samples before buying a lot. This helps you find problems early.
Tip: Stay in touch with your suppliers. Good communication helps avoid delays and ensures you get the best parts.
Ensuring Component Reliability
Even great parts need proper care to work well. Store them in clean, dry places to avoid damage. Use anti-static tools, like wrist straps, to protect sensitive parts during assembly. Check and test parts often to catch problems early. These steps will make your PCB assembly last longer and work better.
PCB Warping and Bowing
Why PCBs Warp During Assembly
PCBs can bend or twist if they don’t stay flat. Uneven heating during soldering is a common cause. If one side heats faster, the board may warp. Using materials that expand differently when heated can also cause bending. For example, copper and the board base might expand at different rates. Storing PCBs in humid places or stacking them wrong can lead to warping too.
Problems Caused by Warping
A bent PCB can create big issues. Parts might not sit correctly, causing bad connections. Misaligned parts can hurt how the board works, especially in fast systems. In bad cases, warping can break solder joints or crack the board. These problems make the PCB less reliable and cost more to fix.
How to Stop Warping
You can stop warping with simple steps. Use materials that expand the same way when heated. Keep PCBs in dry, flat places to avoid moisture damage. During soldering, control heat carefully to warm the board evenly. Adding supports during assembly can also keep the board flat. These tips will help your PCBs work better and last longer.
Documentation Errors
Why Accurate Documentation Matters
Good documentation is key to successful PCB assembly. It tells everyone what to do and how to do it. Clear instructions reduce confusion and speed up the process. They also prevent costly mistakes, like using wrong parts or placing them incorrectly. Think of it like a guide—without it, things can go wrong fast.
Tip: Always review your documentation carefully before sending it out.
Common Documentation Problems
Some documentation mistakes happen more often than you’d expect:
Unclear instructions: If details are vague, people might misunderstand them.
Old files: Using outdated designs or BOMs can cause mismatched parts.
Missing information: Forgetting part numbers or notes can delay the process.
These errors slow things down and increase the chance of mistakes. Fixing them later wastes both time and money.
How to Make Better Documentation
Avoid these problems by following these easy steps:
Stay organized: Use the same format for all your files.
Be detailed: Add all important info, like part numbers and instructions.
Keep it updated: Share the newest version with everyone involved.
Ask for feedback: Let your assembly team check your files for clarity.
Better documentation makes PCB assembly faster and less stressful.
Electrostatic Discharge (ESD) Risks
How ESD Affects PCB Components
Electrostatic discharge (ESD) might look harmless, but it’s not. Static electricity can build up and suddenly release. This can harm sensitive parts like semiconductors. It’s not just a small issue—it’s expensive. The electronics industry loses up to $9 billion yearly due to ESD. Around 27% to 33% of semiconductor failures are caused by ESD problems.
The good news is that fixing ESD issues works. One company reduced ESD damage rates from 0.12% to 0.003% by using protective steps. Another U.S. company cut ESD mistakes caused by people by 83%. These examples show that solving ESD risks saves money and reduces stress.
What Causes ESD Damage
What leads to ESD damage? It starts with static electricity. Simple actions like walking on a carpet or touching parts without grounding can create static. When this static hits your PCB, it can destroy delicate parts. Low humidity makes static build up faster. Bad storage or packaging can also increase ESD risks.
How to Stop ESD Problems
You can stop ESD problems with easy steps. Use anti-static tools like wrist straps, mats, and bags. These tools keep you and your parts grounded. Control your workspace by keeping humidity between 40% and 60%. Teach your team about ESD safety. When everyone handles parts correctly, fewer problems happen.
Pro Tip: Use ESD-safe packaging for storing and shipping parts. It’s a small cost that prevents big losses.
Supply Chain Delays
How Delays Affect PCB Assembly
Supply chain delays can slow down your PCB assembly. If parts don’t arrive on time, production might stop. This can cause missed deadlines and upset customers. Imagine waiting weeks for a part, only to find it’s unavailable. Delays don’t just waste time—they also cost more money. You might need to pay for faster shipping or use pricier suppliers.
Why Delays Happen
What causes supply chain delays? One reason is a lack of raw materials. When demand rises, suppliers may struggle to keep up. Poor communication with your supplier can also create problems. If they don’t tell you about stock or shipping issues, you won’t know what’s happening. Relying on just one supplier is risky too. If they have problems, your project gets delayed.
How to Avoid Supply Chain Problems
You can reduce delays with smart planning. Work with several suppliers so you have backups. Order parts early to avoid running out. Stay in touch with suppliers to catch problems early. Keep a small stock of important parts as a safety net. It costs more upfront but prevents bigger delays later.
Pro Tip: Use software to track orders and inventory in real time. It helps you stay organized and avoid surprises.
Fixing these 10 common PCB assembly problems isn’t just about solving issues—it’s about creating better boards from the beginning. Taking smart steps, like managing heat well or choosing good parts, helps you succeed in the long run.
Here’s how being proactive helps:
Problem | Long-Term Benefit |
---|---|
Stops parts from wearing out and makes electronics last longer. | |
Design Techniques | Lowers heat stress, keeping solder joints strong and dependable. |
Material Selection | Prevents overheating, boosting efficiency and keeping performance steady. |
By fixing these problems early, you’ll save time, cut costs, and make sure your PCBs work great. Don’t wait—start using these tips now and improve your assembly process!
FAQ
How can I stop PCB assembly mistakes?
Begin with a good design. Check your BOM, layout, and instructions carefully. Work with your manufacturer early to find and fix problems. 🛠️
How do I keep components safe from static electricity?
Use anti-static items like wrist straps and mats. Keep parts in special ESD-safe bags. Teach your team how to handle parts safely to avoid damage. ⚡
Why does heat control matter in PCB assembly?
Too much heat can harm parts and make your PCB fail sooner. Good heat control keeps your PCB working well and avoids expensive fixes. 🔥