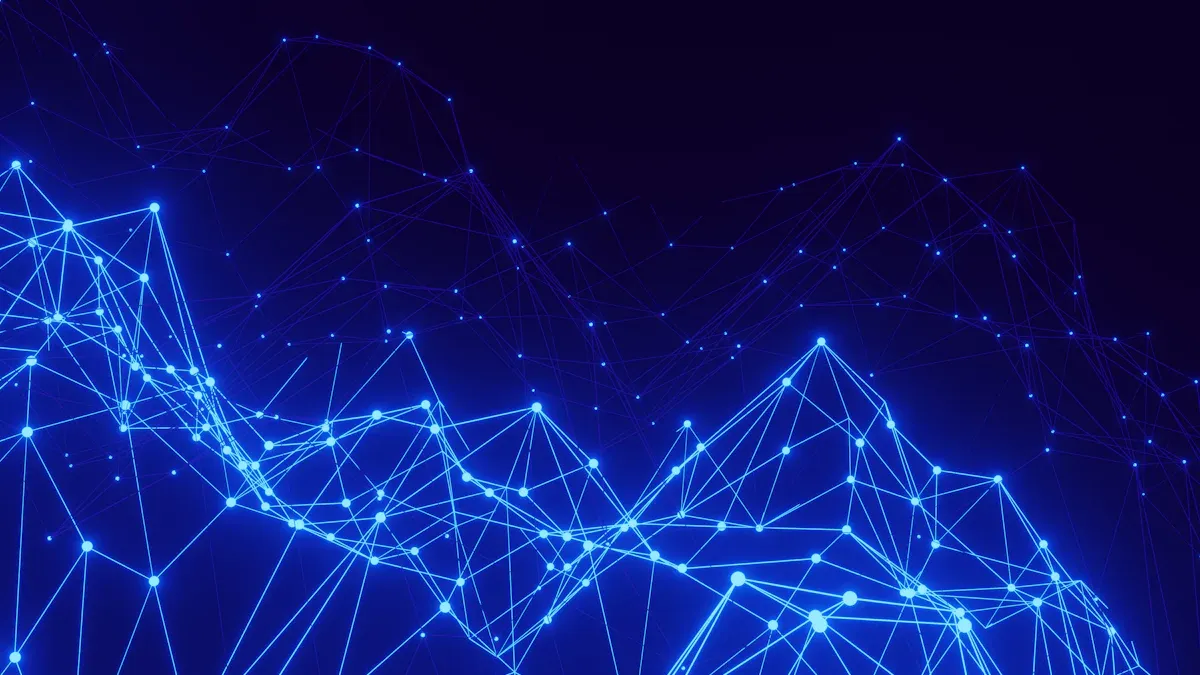
The transition to 5G is transforming the way devices communicate with one another. This shift requires innovative approaches to the creation and design of 5G-compatible PCBs. These specialized PCBs are crucial for achieving faster data transmission, reduced latency, and improved connectivity. They must effectively handle high-frequency signals while maintaining compact designs. Additionally, they need to be robust and dependable. The market for 5G-compatible PCBs is projected to expand from $8.2 billion in 2023 to $29.8 billion by 2033. Understanding how to fulfill these requirements will play a significant role in shaping the future of wireless technology.
Key Takeaways
PCBs for 5G help send data faster and connect better. Use materials that reduce signal loss and stay stable.
Managing heat is very important in 5G PCB design. Pick materials that handle heat well and add thermal vias or heat sinks for reliability.
To stop electromagnetic interference (EMI), keep traces short and spaced out. Use ground planes and shields to protect signals and improve performance.
Choosing the right base material helps signals stay strong. Materials like PTFE and LCP work well for high-frequency uses and keep signals clear.
Making low-power IoT devices needs smart planning. Control power flow, manage heat, and keep signals strong to make batteries last longer and work better.
Challenges in Designing 5G-Compatible PCBs
High-frequency signal weakening and its effect on design
Making 5G PCBs means solving problems with signal weakening. At high frequencies, signals lose strength because the PCB material absorbs energy. This is called dielectric absorption and makes signals less effective. The skin effect adds to the problem by increasing resistance on the PCB’s surface. This reduces the area for signals to travel, hurting performance, especially in millimeter-wave bands.
To fix this, use materials that lose less energy and wider traces. Noise, like RF interference and leakage currents, also weakens signals. Short and straight transmission lines help reduce these issues. Techniques like pre-emphasis and receiver equalization can keep signals strong over long distances. Solving these problems ensures your 5G PCB supports fast and reliable communication.
Handling heat in small, high-power systems
Managing heat is very important in 5G PCB design. Fast signals create heat that can damage parts or cause copper to peel off. Small designs make it harder to get rid of heat because there’s less space.
To handle heat well, pick materials that can take high temperatures. Substrates with good thermal conductivity help spread heat better. Adding thermal vias and heat sinks to your PCB design also helps. Good heat management keeps your 5G PCBs working under tough conditions.
Keeping signals strong in crowded 5G PCB layouts
Keeping signals clear in crowded 5G PCB designs is a big challenge. Features like MIMO make designs more complex, causing problems like crosstalk, parasitic capacitance, and electromagnetic interference (EMI). These issues weaken signals and hurt system performance.
To keep signals strong, control the impedance of RF traces carefully. For example, keeping impedance at 50 Ω stops signal reflections that lower quality. Choose the right transmission line type, like microstrip or CPWG, for your design. Keep traces short and straight to avoid losses and reduce interference. Multilayer boards with good trace spacing can also cut down EMI and crosstalk, helping your 5G PCB work reliably at high speeds.
Overcoming EMI challenges in wireless applications.
Electromagnetic interference (EMI) is a big problem for 5G PCBs. It can mess up signals, lower performance, and cause communication issues. Fixing these problems is key for reliable wireless systems.
Understanding EMI and Its Impact
EMI happens when unwanted signals disturb your PCB’s work. In 5G, where high-frequency signals are common, EMI is worse. Problems like crosstalk, signal bouncing, and trace coupling often occur. These issues weaken signals and make your 5G PCB less efficient.
A study on EMI in PCBs explains important points:
Section | Description |
---|---|
II | Info about wireless devices and how signals move. |
III | Details on EMI in random PCB traces. |
IV | Tips for estimating crosstalk. |
V | Explains inter-trace coupling factor (F). |
VI | Test PCB layout for study and analysis. |
VII | Data results and ways to reduce crosstalk. |
This research shows why understanding crosstalk and coupling is vital to fix EMI.
Strategies to Overcome EMI
To reduce EMI in 5G PCBs, try these steps:
Improve Trace Layouts: Keep traces short and straight. Avoid sharp turns to lower EMI.
Space Out Traces: Leave enough space between traces to cut down crosstalk. This is crucial for crowded 5G PCBs.
Add Ground Planes: Use ground planes to block outside interference. They also help keep impedance steady.
Use EMI Shields: Add shielding materials to stop outside signals from affecting your PCB.
Pick Low-EMI Parts: Choose parts that create less electromagnetic noise. This lowers the EMI from your PCB.
Testing and Validation
After making changes, test your PCB for EMI issues. Use tools like spectrum analyzers to find problem areas. Regular testing ensures your 5G PCB works well for wireless systems.
By solving EMI problems, your 5G PCBs will work better and stay reliable. This helps meet the needs of future wireless tech.
Materials and Technologies for 5G PCB Design
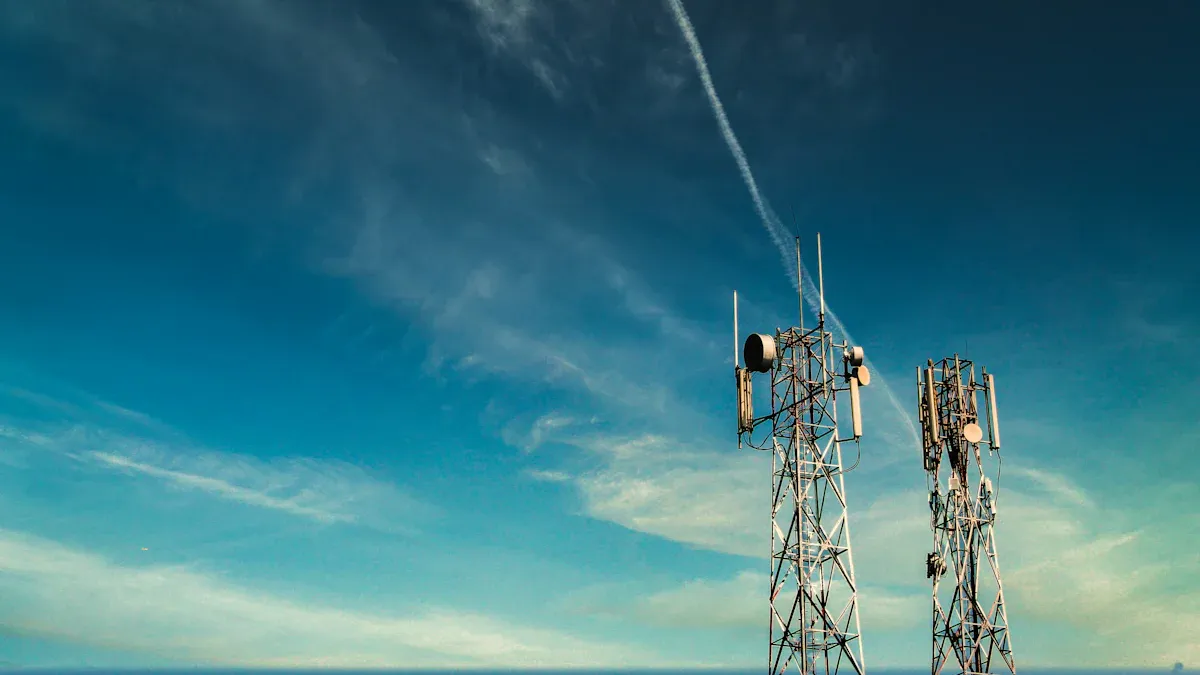
Picking the right substrate for strong signals
Choosing the right material is key for 5G PCBs. High-frequency signals need materials that lose less energy and stay stable. Look for substrates with low dielectric constant (Dk) and dissipation factor (Df). These features help signals stay strong and reduce weakening.
Here are some common materials for 5G PCBs:
HTE: Handles high heat and works well with fast signals.
RTF: Good for mid-range signals but not for very high ones.
PTFE: Affordable and used in car radar systems.
Liquid Crystal Polymers (LCP): Great for flexible designs like phone antennas.
Low Temperature Co-Fired Ceramic (LTCC): Works for small, high-frequency filters.
TiO₂ and Al₂O₃: Strong and reliable for space and telecom uses.
Picking the right material helps your PCB handle fast signals better.
Layer stackup tips for better 5G PCB performance
The way layers are stacked affects how well a PCB works. A good stackup lowers signal loss and blocks interference. Use full ground planes to keep signals clear and avoid splitting them. Extending the ground plane to the edges helps with power stability.
Here are some helpful tips:
Don’t split the ground plane into parts.
Use multiple layers with enough space to avoid signal mixing.
Add impedance-controlled traces for faster signals.
Figure | Description |
---|---|
8 | Shows the layers in a PCB design. |
9 | Top layer has patches; bottom has the network. |
10 | Side view of an antenna system for 5G. |
11 | Prototype of a 32-element antenna. |
12 | Setup for testing the board’s performance. |
13a,b | Graphs showing signal strength at each port. |
A smart layer stackup helps your PCB work well with fast and high-frequency signals.
Advanced methods for making reliable 5G PCBs
Making 5G PCBs needs careful and accurate processes. Using high-quality copper and aligning layers properly improves signal flow. Focus on plating vias and checking quality to ensure good results.
Here are some important steps:
PCB Making: Use precise cutting and layer alignment tools.
Assembly: Use lead-free solder and protective coatings.
Testing: Check how the PCB works under stress and in real conditions.
Environment: Protect against heat and moisture for longer life.
Advanced Tools: Use signal tests and reliability checks to improve designs.
These steps make sure your 5G PCBs are strong and meet today’s wireless needs.
Practical Guidelines for 5G PCB Design and Manufacturing
Controlling impedance for fast signals
Keeping impedance steady is key for strong signals in 5G PCBs. Fast signals, especially in gigahertz ranges, need precise impedance control. If mismatched, signals can bounce back, weaken, or cause timing problems. This lowers the performance of your 5G PCBs. To fix this, design layouts carefully and pick materials that keep impedance stable.
You can adjust trace width, spacing, and layer stackup to help. For example, keeping traces even and spaced properly avoids impedance changes. Using materials with steady dielectric properties also reduces signal issues. The table below shows factors that affect impedance and their impact:
Tolerance Factor | Potential Issue | Effect on Impedance | Impact on High-Speed Systems |
---|---|---|---|
Trace Width & Spacing | Signal bounce, loss, or mismatch | Impedance changes, weaker signals | Errors in data, poor signal quality |
Layer Stackup & Material | Dielectric changes, uneven traces | Impedance shifts, timing problems | Problems in RF and high-speed designs |
Differential Pair Spacing | Timing errors, jitter | Uneven impedance between paired signals | Issues in USB, Ethernet, and HDMI communication |
By using these methods, your 5G PCB will handle fast signals better and stay reliable.
Blocking EMI for wireless parts
Electromagnetic interference (EMI) is a big problem for 5G PCBs. Wireless parts like Bluetooth and Wi-Fi are easily affected by EMI. This can mess up signals and hurt performance. To stop EMI, you need good shielding to protect parts and reduce noise.
Ground planes are great for blocking interference and keeping impedance steady. Adding shielding materials around important areas also helps. Research shows PCB-level shielding works better than case shielding for stopping high-frequency noise. Benefits of EMI shielding include:
Protecting parts and keeping signals clear.
Reducing problems like crosstalk and power noise.
Helping wireless systems work without interruptions.
Using these ideas in your PCB design will help solve EMI problems and make your 5G boards stronger.
Adding antennas to 5G PCBs
Antennas are very important in 5G PCB designs. Where and how you place them affects how well your system works. To make antennas work well, you need to balance design and function while keeping the PCB small.
Place antennas inside the device to shield them from outside damage. Run RF signals on outer layers over a solid ground plane to keep impedance steady. Put surface-mount antennas close to wireless parts to shorten traces and reduce noise. Test different antenna spots during design to find the best one.
Here are some tips for adding antennas:
Plan layouts to lower electromagnetic interference.
Keep antennas apart for better isolation.
Use a large ground plane under antennas for better performance.
Match impedance to 50Ω after designing.
Follow FCC part 15c rules for telecom boards.
These steps will improve your 5G PCB’s antenna performance and ensure smooth wireless connections.
Design tips for low-power, energy-saving IoT devices
Making PCBs for IoT devices means focusing on saving energy. These devices often use small power sources like batteries or energy harvesters. To work well, you need to balance power use, heat control, and signal quality.
1. Improve Power Flow
Good power flow is key for IoT devices with low power. Use traces with low resistance and voltage regulators that save energy. Keep power and ground planes close to lower impedance and deliver energy better. Pick parts that use less power when working or resting.
Tip: Turn off unused PCB sections to save energy when not needed.
2. Control Heat
Heat control helps IoT devices stay reliable. Even small systems can get hot, especially in tight spaces. Use materials that spread heat well. Add thermal vias and heat sinks to remove heat faster. Good heat control keeps parts safe and makes devices last longer.
Heat Control Methods | Advantages |
---|---|
Thermal vias | Moves heat away from hot spots |
High-heat materials | Stops overheating in small areas |
Heat sinks | Protects parts from damage |
3. Keep Signals Strong
Strong signals are important for IoT devices, especially with 5G. High-speed signals can weaken from interference or mismatched impedance. Use traces with controlled impedance and keep them short. Shield signal paths and separate noisy parts to avoid interference.
Note: Place antennas carefully to avoid signal loss or nearby noise.
4. Lower Standby Power Use
IoT devices often stay in standby mode for long times. Use microcontrollers and sensors that need very little power. Add sleep modes and wake-up features to save energy. These steps are vital for battery-powered devices where every bit of power matters.
5. Plan for Future Networks
IoT devices will depend more on 5G networks. Design PCBs to handle high-speed signals and work with 5G modules. This ensures your devices stay useful as wireless tech improves.
By following these tips, you can make PCBs that fit low-power IoT needs. These designs improve performance, extend battery life, and help the environment.
Future Trends in PCB Design for 5G and Beyond
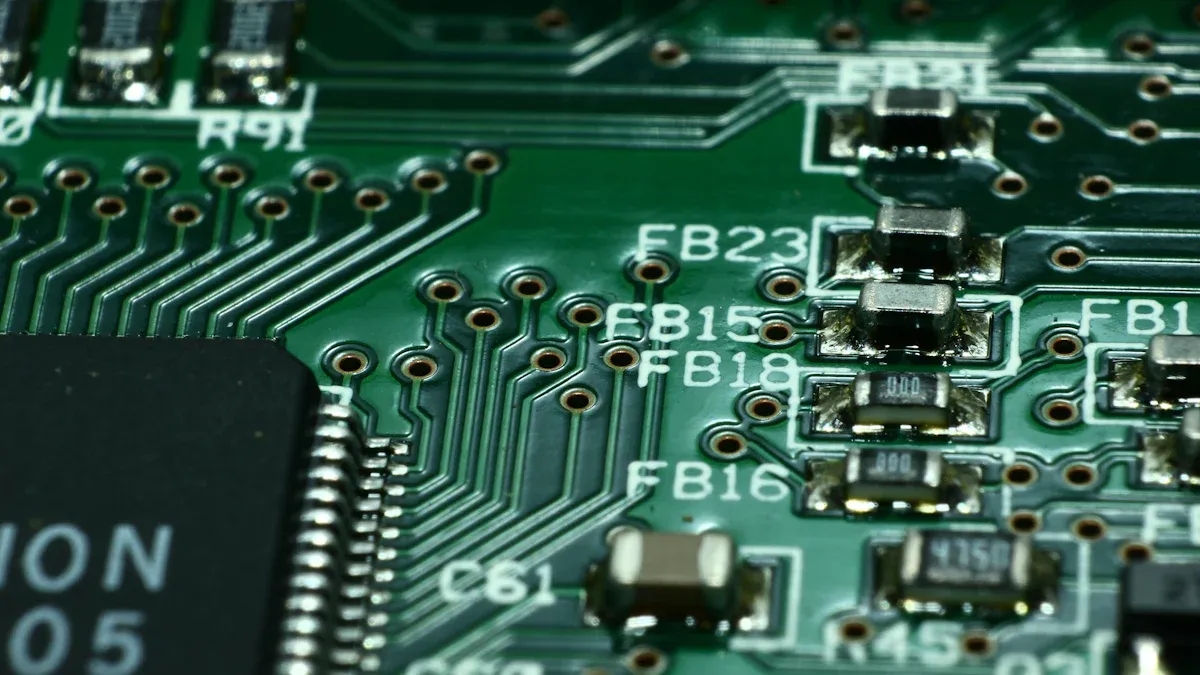
New materials for mmWave and 6G systems
5G and 6G need better materials for higher frequencies. These materials must have low dielectric constant (Dk) and low dielectric loss (Df) to keep signals strong. Studies show advanced PTFE and epoxy thermosets are great for high-frequency use. Flexible materials are also being made to match thermal expansion in mmWave systems.
Substrates like HDI, LTCC, and glass are becoming popular. Each has special benefits, like better signal quality and less interference. LTCC works well for small designs, while HDI helps fit more parts on tiny boards. These new materials will improve PCB designs for faster networks.
AI and machine learning in PCB design
Artificial intelligence (AI) is changing how PCBs are made. AI can study big data, find patterns, and make processes better. Companies like Siemens and Jabil use AI to spot defects early and predict maintenance needs. This saves money and time.
Machine learning helps predict demand by studying past data and trends. It cuts errors by up to 65%, making sure you get the right parts on time. Adding AI to your workflow makes PCB production faster and more reliable.
Adding sensors and wireless modules to PCBs
Sensors and wireless modules bring new ideas to devices like IoT systems and self-driving cars. Placing sensors carefully and using reference planes keeps signals clear and avoids interference.
New sensors and board materials let you design better PCBs for modern tech. For example, putting sensors inside PCBs improves performance and reduces signal problems. This is important for devices needing accuracy, like medical tools and smart city systems.
Sustainability and eco-friendly practices in PCB production.
Making PCBs in a sustainable way is now very important. Using eco-friendly methods helps the planet and makes production better. These steps match global goals and keep your designs useful for a long time.
Switching to lead-free solders is a big improvement. It cuts down on toxic waste and keeps workers and nature safe. Using halogen-free laminates also helps by reducing harmful gases during production and disposal. These materials follow strict rules and still work well.
Saving energy is another key step. Better production methods use less power and cost less to run. For example, laser drilling and precision etching need less energy than older methods. This saves resources and lowers pollution.
Recycling and managing waste are just as important. New recycling systems can recover valuable metals like copper and gold from old PCBs. This reduces trash and saves natural resources. Designing PCBs to be taken apart easily makes recycling simpler and parts reusable.
Here’s a simple table of these practices and their benefits:
Eco-Friendly Practices in PCB Production | Benefits |
---|---|
Use lead-free solders | Cuts toxic waste and protects health |
Choose halogen-free laminates | Lowers harmful gases during production |
Use energy-saving methods | Reduces power use and costs |
Improve recycling and waste systems | Saves resources and reduces trash |
Design for easy recycling | Makes recycling simpler and cuts waste |
By following these ideas, you help create a cleaner world. These actions not only protect the environment but also make your designs stand out in the growing 5G market.
Making PCBs for 5G comes with special problems. These include signal loss, heat control, and interference. Using metal core boards, thermal vias, and EMI shields can help. New materials like PTFE and liquid crystal polymers improve performance. Advanced tools like 3D EM simulations also make PCBs work better.
To stay ahead, use smart strategies. Invest in AI and 5G to save money and train workers. About 34% of companies plan to use 5G soon. The industry is moving toward smarter and greener methods. By focusing on new ideas, you can get ready for better connectivity and lead the way forward.
FAQ
What materials are best for 5G PCBs?
Use materials with low Dk and Df values. PTFE, LCP, and LTCC are great options. These materials help signals stay strong and work well at high speeds.
How can EMI be reduced in 5G PCBs?
Keep traces short and straight to lower EMI. Add ground planes and shielding to block interference. Space traces apart to stop crosstalk. Test designs with tools like spectrum analyzers to check for EMI problems.
What should you know about placing antennas in 5G PCBs?
Put antennas close to wireless parts to reduce noise. Use a solid ground plane under antennas for better signal control. Test different spots during design to find the best placement.
How do you manage heat in small 5G PCBs?
Pick materials that handle heat well. Add thermal vias and heat sinks to remove heat. Use high-temperature materials to keep parts safe and reliable.
Can 5G PCBs work for energy-saving IoT devices?
Yes, they can! Use low-power parts and improve power flow. Add sleep modes and manage heat to save energy while keeping good performance.
See Also
Essential Technologies Transforming PCBA Production For Today’s Electronics
Leading Smart Manufacturing Innovations For PCBA By 2025
Diverse PCBA Uses In Consumer Electronics And Other Fields
Key Trends Influencing Industrial IoT PCB Assembly By 2025
The Importance Of IoT Device PCBA Production In Today’s Market