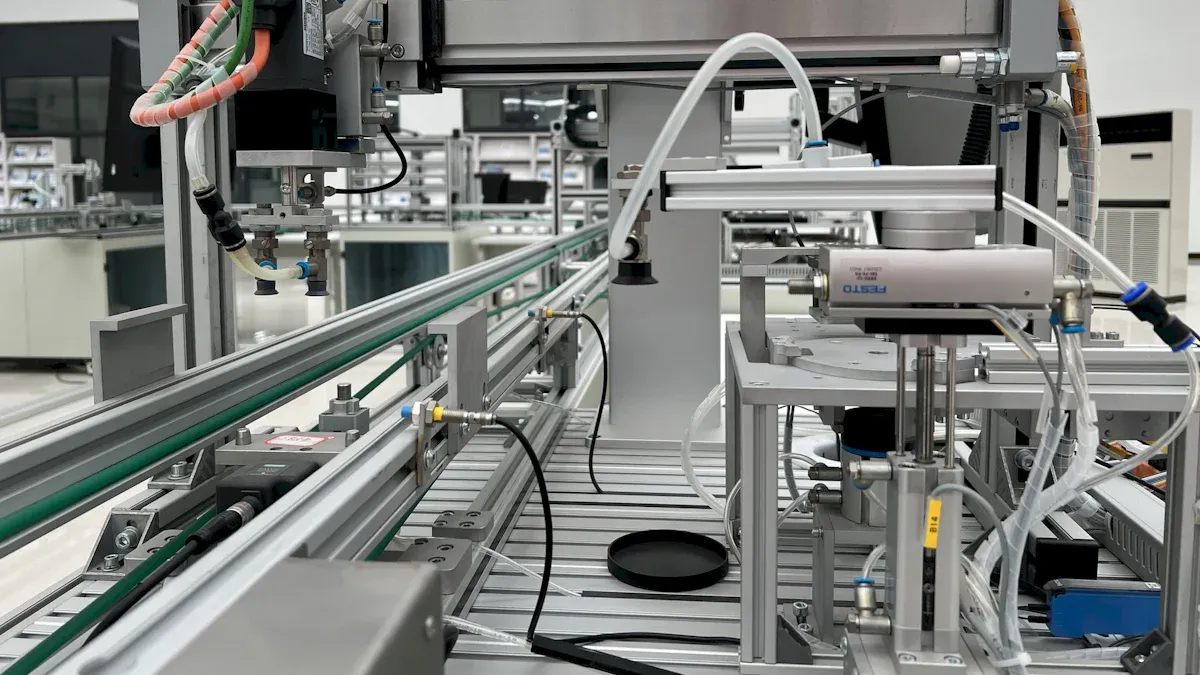
Printed Circuit Board Assembly (PCBA) forms the backbone of industrial automation PCBA. It powers systems that drive precision, speed, and reliability in modern industries. For instance, advanced PCBA technologies achieve defect detection with a 97.3% accuracy rate and process 322.6 frames per second, ensuring seamless operations. From controlling robotic arms in factory automation to streamlining food production, industrial automation PCBA enhances innovation across sectors. Its ability to ensure accurate communication, minimize downtime, and optimize space makes it indispensable in creating efficient and scalable solutions for automation systems worldwide.
Key Takeaways
PCBA is important for automation, helping machines work fast and accurately.
New PCBA tech can boost efficiency by 35% and lower costs a lot.
Special PCBA works well in tough places like space or oil fields.
Using PCBA helps create flexible systems for many industries.
Adding IoT and AI to PCBA improves monitoring and fixes problems early.
Definition and Importance of Industrial Automation PCBA
What is PCBA and how does it work?
PCBA, or Printed Circuit Board Assembly, is the process of assembling electronic components onto a printed circuit board to create a functional electronic system. It serves as the foundation for many devices, connecting components like microcontrollers, sensors, and resistors to ensure seamless communication and operation. In industrial automation, PCBA acts as the brain behind machines, enabling them to perform complex tasks with precision and speed.
The importance of PCBs lies in their ability to integrate multiple components into a compact and efficient design. For example, in industrial control systems, PCBA ensures that sensors and actuators work together to monitor and control processes. Without PCBA, achieving the level of automation required in modern industries would be impossible.
Why is PCBA essential for industrial automation systems?
PCBA plays a critical role in industrial automation systems by enhancing efficiency, reliability, and scalability. It allows machines to operate autonomously, reducing the need for manual intervention. According to industry reports, PCBs are essential for industrial automation and control systems because they connect and integrate various components, ensuring effective process management. This integration supports the smooth operation of systems like robotic arms, conveyor belts, and automated inspection tools.
Advancements in PCB technology also support emerging trends like Industry 4.0 and the Internet of Things (IoT). These innovations rely on PCBA to enable real-time data collection, analysis, and decision-making. For instance, empirical studies show that automation solutions powered by PCBA can improve operational efficiency by 35%, reduce inventory costs by 24%, and enhance compliance accuracy by 45%. These benefits highlight why PCBA is indispensable for industrial automation.
The role of PCBA in enabling factory automation
Factory automation relies heavily on PCBA to streamline production processes and improve productivity. By integrating advanced technologies like AI and robotics, PCBA enables machines to perform tasks with minimal human intervention. For example, automated pick-and-place machines use PCBA to precisely position components on a production line, reducing errors and increasing speed.
Case studies further illustrate the impact of PCBA on factory automation. One company faced challenges with labor-intensive processes and long lead times. By implementing advanced automation solutions with PCBA, they reduced assembly time, improved accuracy, and enhanced productivity. Another company used AI-powered inspection systems to address quality control issues, resulting in fewer defects and higher customer satisfaction.
The following table summarizes real-world examples of how PCBA drives factory automation:
Company | Challenge | Solution | Results |
---|---|---|---|
Company A | Labor-intensive processes, long lead times | Advanced automation solutions, robotic assembly, automated pick-and-place | Reduced assembly time, improved accuracy, enhanced productivity |
Company B | Quality control issues, defects | AI-powered inspection systems | Reduced defects, improved reliability, enhanced customer satisfaction |
Company C | Environmental sustainability | Eco-friendly materials, energy-efficient techniques | Reduced environmental footprint, increased market share, positive reputation |
These examples demonstrate how PCBA enables factories to achieve higher efficiency, better quality, and greater sustainability. By leveraging the power of PCBA, you can transform your production processes and stay competitive in the rapidly evolving industrial landscape.
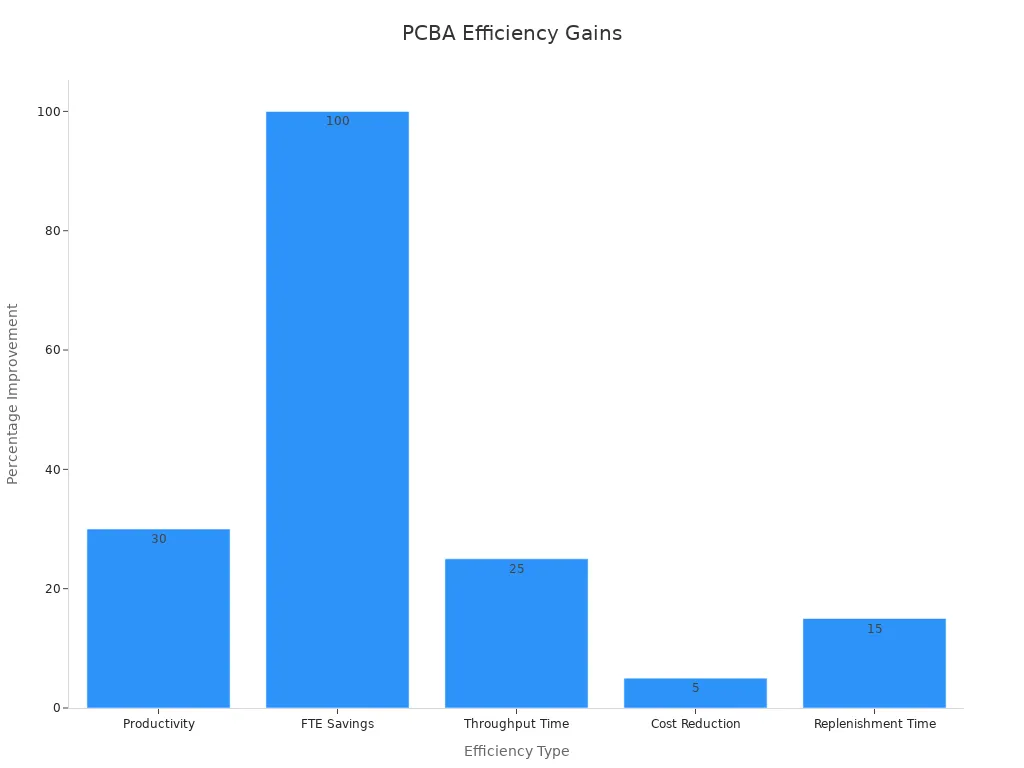
Types of PCBA Used in Industrial Automation
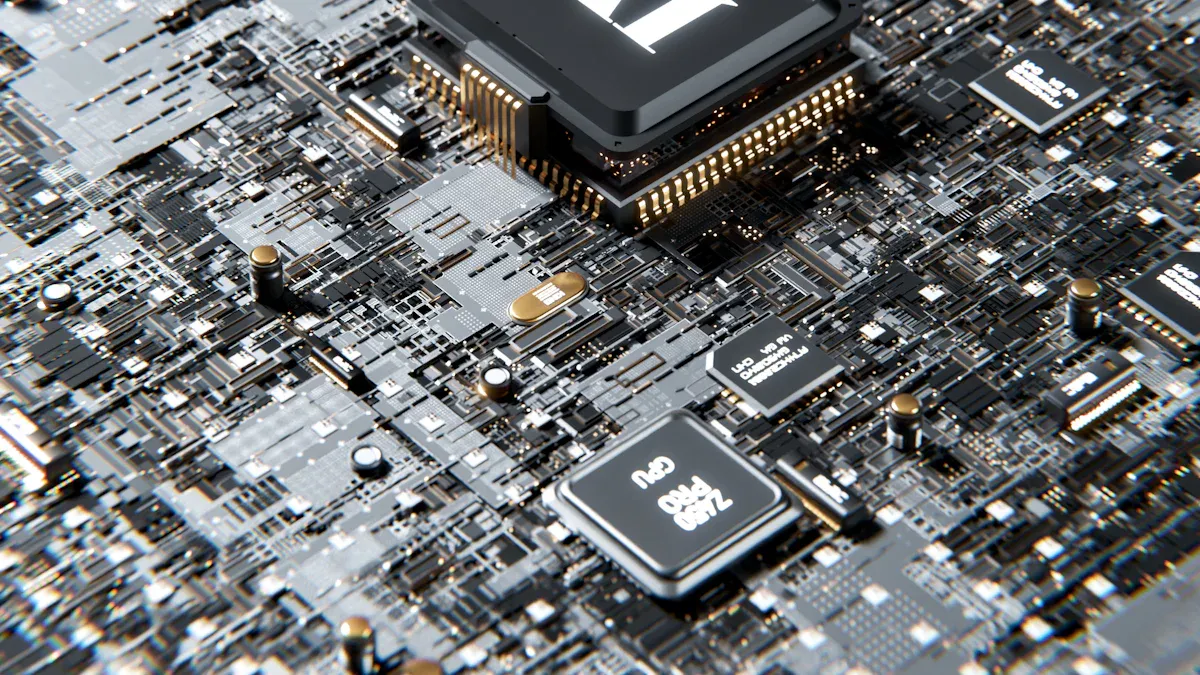
Single-sided PCBA and its applications
Single-sided PCBA is the simplest type of circuit board. It features a single layer of conductive material, typically copper, with components mounted on one side. This design makes it cost-effective and easy to manufacture. You’ll often find single-sided PCBA in applications where complexity is minimal, such as LED lighting systems, household appliances, and basic industrial controls.
The material used in single-sided PCBA, like FR-4 (a glass-reinforced epoxy laminate), provides excellent strength and water resistance. This makes it suitable for environments where durability is essential but advanced functionality isn’t required. Its straightforward design ensures reliability in systems that don’t demand high-speed or high-power performance.
Double-sided PCBA for complex systems
Double-sided PCBA takes functionality a step further by adding conductive layers on both sides of the board. This allows components to be mounted on both surfaces, increasing the board’s capacity to handle more complex circuits. You’ll see double-sided PCBA in systems like power supplies, industrial sensors, and communication devices.
Materials like PTFE (Teflon) are often used in double-sided PCBA for their flexibility and lightweight properties. These boards are ideal for applications requiring higher performance without sacrificing durability. Additionally, double-sided PCBA supports Surface Mount Technology (SMT), enabling compact designs and efficient assembly processes.
Multi-layer PCBA for advanced industrial needs
Multi-layer PCBA is the go-to choice for advanced automation systems. These boards stack multiple layers of conductive material, separated by insulating layers, to create a compact yet powerful design. They are commonly used in robotics, aerospace systems, and high-speed data processing equipment.
The advantages of multi-layer PCBA include reduced size, improved signal integrity, and enhanced durability. For example, the vertical stacking of layers minimizes the board’s footprint while maintaining high routing density. A single connection point simplifies integration into complex systems, and the separation of power and ground planes reduces electromagnetic interference (EMI).
Advantage | Description |
---|---|
Reduced PCB Size | Utilizes vertical space, significantly reducing the overall footprint of the board. |
Lightweight | Thinner boards retain complex circuitry, making them lighter than single/double-layer boards. |
High Quality and Density | Increases routing density and quality of connections between components. |
Better Durability and Flexibility | Protects components between layers, enhancing durability and application flexibility. |
Improved Signal Integrity | Reduces crosstalk and noise by separating power and ground planes, enhancing performance. |
Multi-layer PCBA is essential for industries that demand high performance and reliability. Its ability to handle complex circuits in a compact form makes it a cornerstone of modern industrial automation.
Specialized PCBA for high-temperature and rugged environments.
Industrial environments often expose electronic systems to extreme conditions, including high temperatures, rapid temperature changes, and mechanical stress. Specialized PCBA ensures reliable performance in these challenging settings by using advanced materials and rigorous testing methods.
Materials Designed for Extreme Conditions
Specialized PCBA uses materials like polyimide and ceramic substrates to handle thermal loads effectively. Polyimide offers excellent heat resistance, while ceramic substrates provide durability and stability under high temperatures. These materials prevent warping and degradation, ensuring long-term functionality. You’ll find these PCBs in industries like aerospace, oil and gas, and heavy machinery, where systems must operate in harsh environments.
Testing for Reliability
Testing plays a crucial role in ensuring the durability of specialized PCBA. Manufacturers conduct thermal cycling tests to simulate repeated exposure to temperature fluctuations. Burn-in testing evaluates the PCB’s performance under sustained high temperatures. These methods identify potential weaknesses, allowing engineers to refine designs for maximum reliability.
📌 Did you know? Standards like IPC-TM-650 2.6.7 and MIL-STD-202G define testing methods for thermal shock resistance. These tests ensure PCBs can withstand rapid temperature changes without compromising performance.
Advancements in High-Temperature Technology
Recent innovations in integrated circuits and supporting components have enhanced the reliability of PCBA in extreme conditions. These advancements allow systems to function efficiently in environments that were previously considered unsuitable for electronics. For example, thermal shock tests now evaluate a PCB’s ability to endure sudden temperature shifts, making them ideal for rugged applications.
Specialized PCBA empowers you to deploy automation systems in environments where durability and heat resistance are critical. By choosing the right materials and testing methods, you can ensure your systems perform reliably, even under the harshest conditions.
Key Benefits of Applications for PCBs in Industrial Automation
Enhancing operational efficiency and productivity
PCBA plays a pivotal role in boosting the efficiency of automation systems. By integrating advanced technologies like IoT and AI, PCBA enables real-time monitoring and intelligent decision-making. This ensures that your production process runs smoothly and minimizes disruptions. For instance:
IoT applications in manufacturing could generate an economic impact of USD1.25 to USD3.65 trillion annually by 2025.
Real-time monitoring through IoT can reduce energy costs by over 40%, directly improving cost efficiency.
Automation systems powered by PCBA also reduce unplanned downtimes, which can cost manufacturers upwards of USD250,000 per hour. Predictive maintenance, enabled by PCBA, ensures that potential issues are identified and resolved before they escalate. This not only saves costs but also enhances productivity.
Additionally, PCBA supports automation by enabling intelligent detection and fault prediction. AI-powered systems reduce errors and optimize production planning. This leads to better capacity utilization and improved operational efficiency. By leveraging PCBA, you can achieve faster production cycles and higher output quality, giving your business a competitive edge in industrial automation.
Improving reliability and durability in harsh conditions
Industrial environments often expose electronic systems to extreme conditions, such as high temperatures, vibrations, and mechanical stress. PCBA ensures reliability and durability in these challenging settings by using robust materials and advanced manufacturing techniques.
For example, specialized PCBA uses materials like polyimide and ceramic substrates, which can withstand high thermal loads and mechanical stress. These materials prevent warping and degradation, ensuring long-term functionality. Rigorous testing methods, such as thermal cycling and burn-in tests, further enhance the reliability of PCBA in harsh environments.
Automation systems equipped with durable PCBA can operate seamlessly in industries like aerospace, oil and gas, and heavy machinery. This reliability minimizes downtime and maintenance costs, allowing you to focus on optimizing your production process. By choosing the right PCBA for your automation needs, you can ensure consistent performance even under the most demanding conditions.
Reducing costs in large-scale production
PCBA significantly reduces costs in large-scale production by streamlining the automation process. Advanced PCBA technologies optimize the assembly process, reducing labor costs and minimizing errors. For instance, a cost estimation tool developed by researchers from the National University of Singapore and Flextronics simulated the PCB assembly process. This tool captured dynamics like machine breakdowns and quality defects, leading to significant improvements in cost estimation and process efficiency.
AI integration in the physical design phase of PCBA further accelerates the process and reduces costs. Early insights into potential design issues enhance reliability and prevent costly rework. Real-time data analysis, enabled by PCBA, optimizes production planning and improves capacity utilization. This directly impacts operational efficiency and reduces overall production costs.
Moreover, automation and digitization have reduced manufacturing deviations by over 65%, improving quality and lowering costs associated with defects. By investing in PCBA, you can achieve cost-effective production while maintaining high standards of quality and reliability.
💡 Tip: Effective management of raw material costs is crucial for profitability. Strategic sourcing and inventory management can further enhance the cost benefits of PCBA in automation systems.
Enabling scalability and adaptability for diverse industries.
PCBA plays a vital role in helping industries scale their operations and adapt to changing demands. Its versatility allows you to customize automation systems for specific needs, ensuring seamless integration across diverse sectors. Whether you’re in manufacturing, healthcare, or energy, PCBA provides the foundation for creating flexible and scalable solutions.
How PCBA Supports Scalability
Scalability is essential for industries aiming to grow without compromising efficiency. PCBA enables you to expand your automation systems by integrating additional components or upgrading existing ones. For example:
Modular Designs: PCBA supports modular system designs, allowing you to add or replace components as your needs evolve. This reduces downtime and ensures a smooth transition during upgrades.
Compact and Efficient Layouts: Multi-layer PCBA minimizes space requirements, making it easier to scale systems without increasing their physical footprint.
High-Speed Processing: Advanced PCBA technologies handle increased data loads, ensuring your systems perform efficiently even as operations grow.
💡 Tip: When planning for scalability, choose PCBA designs that prioritize modularity and compatibility with future technologies.
Adapting to Industry-Specific Needs
Every industry has unique requirements, and PCBA offers the adaptability needed to meet them. Its customizable nature allows you to tailor automation systems for specific applications. Here’s how PCBA adapts to different industries:
Manufacturing: PCBA powers robotic arms, conveyor belts, and quality control systems, ensuring high precision and efficiency.
Healthcare: In medical devices, PCBA enables accurate monitoring and diagnostics, supporting patient care and safety.
Energy: Renewable energy systems rely on PCBA for efficient power conversion and grid management.
Industry | Application Example | PCBA Contribution |
---|---|---|
Manufacturing | Robotic assembly lines | Enhances precision and reduces errors |
Healthcare | Wearable health monitors | Enables real-time data collection and analysis |
Energy | Solar inverters | Improves energy conversion efficiency |
Future-Proofing with PCBA
PCBA not only supports current needs but also prepares you for future challenges. Its compatibility with emerging technologies like IoT and AI ensures your systems remain relevant. For instance, IoT-enabled PCBA allows real-time monitoring and predictive maintenance, helping you stay ahead in a competitive market.
📌 Did you know? PCBA advancements now include eco-friendly materials, aligning with sustainability goals while maintaining high performance.
By leveraging PCBA, you can create automation systems that grow with your business and adapt to industry trends. This flexibility ensures long-term success and keeps you competitive in an ever-changing industrial landscape.
The PCBA Assembly Process for Industrial Applications
Design and prototyping tailored for industrial needs
Designing a PCB for industrial automation requires careful planning and attention to detail. You must consider factors like the operating environment, power requirements, and the complexity of the system. For example, high-temperature environments demand heat-resistant materials, while compact systems benefit from multi-layer designs. These pcb design considerations ensure that the final product meets the specific needs of your application.
Prototyping plays a crucial role in refining the design. Engineers create a prototype to test the functionality and identify potential issues. This step allows you to make adjustments before moving to mass production. By addressing problems early, you save time and resources while ensuring the pcb assembly process runs smoothly.
Component placement and soldering techniques
The pcb assembly process begins with preparing the bare PCB. Cleaning and inspecting the board ensures it is free from contaminants. Next, solder paste is applied to designated areas with precision. This step is critical for creating strong connections between components and the board.
After applying the solder paste, components are placed meticulously on the PCB. Automated pick-and-place machines handle this task with incredible accuracy. Once the components are in place, the board undergoes reflow soldering. During this process, the PCB is exposed to controlled heat, which melts the solder paste and secures the components.
Proper soldering techniques are essential for ensuring the reliability of the final product. Poor solder joints can lead to failures, especially in demanding industrial environments. By following these steps, you can create a robust and reliable PCB.
Inspection and testing for quality assurance
Inspection and testing are vital parts of the pcb assembly process. After soldering, the PCB undergoes rigorous testing to verify its functionality and reliability. Automated optical inspection (AOI) systems check for defects like misaligned components or poor solder joints. Functional testing ensures the PCB performs as intended under real-world conditions.
Cleaning the PCB is the final step. This process removes residual flux and contaminants, ensuring the board is ready for integration into industrial systems. By prioritizing quality assurance, you can deliver a product that meets the highest standards of performance and durability.
Final assembly and integration into automation systems.
The final assembly stage transforms a completed PCBA into a fully functional component of an industrial automation system. This step ensures that the PCBA integrates seamlessly with other system elements, enabling smooth operations.
Key Steps in Final Assembly
Housing and Enclosure Installation
You must place the PCBA into a protective housing or enclosure. This protects the board from environmental factors like dust, moisture, and mechanical stress. For example, in high-temperature environments, heat-resistant enclosures ensure long-term reliability.Wiring and Connectivity
Proper wiring connects the PCBA to sensors, actuators, and other system components. You should ensure that connectors and cables are securely attached to avoid signal loss or interruptions. Using color-coded wires simplifies troubleshooting and maintenance.System Calibration
After assembly, calibrate the system to ensure it meets performance specifications. This involves fine-tuning the PCBA to align with the automation system’s requirements. For instance, adjusting sensor sensitivity ensures accurate data collection.Integration Testing
Before deployment, test the assembled system in a controlled environment. This step verifies that all components work together as intended. Functional tests simulate real-world conditions to identify potential issues.
💡 Tip: Always document the assembly and integration process. This helps streamline future maintenance and upgrades.
Benefits of Proper Integration
Proper integration ensures that your automation system operates efficiently. It minimizes downtime, reduces errors, and extends the lifespan of your equipment. By following these steps, you can create a robust system that meets the demands of modern industrial automation.
📌 Note: Investing in high-quality enclosures and connectors can significantly enhance the durability of your automation systems.
Testing and Quality Assurance in PCBA
Importance of rigorous testing in industrial automation
Rigorous testing ensures the reliability and safety of PCBA in industrial automation. You rely on these systems to perform critical tasks, so any failure can lead to costly downtime or safety risks. Testing identifies potential issues early, allowing you to address them before deployment. This process ensures that your automation systems operate efficiently and meet performance expectations.
Testing also helps maintain consistency in production. By monitoring key parameters, you can detect variations that might affect quality. For example, Statistical Process Control (SPC) tracks process data to ensure every PCBA meets the same high standards. Continuous improvement initiatives, such as staff training and technology upgrades, further enhance the reliability of your systems.
📌 Note: Defect analysis and corrective actions are essential for identifying root causes and preventing recurring issues in PCBA.
Common testing methods like functional and in-circuit testing
You can use various testing methods to ensure the quality of PCBA. Each method serves a specific purpose, from detecting defects to verifying functionality. Here’s a breakdown of common testing techniques:
Testing Method | Description |
---|---|
In-Circuit Testing (ICT) | Checks for shorts, opens, resistance, capacitance, and inductance using a bed-of-nails fixture. |
Flying Probe Testing | Offers flexible testing for prototypes or low-volume productions without custom fixtures. |
Functional Testing | Simulates real-world conditions to verify all PCBA functions meet design specifications. |
Visual Inspection | Examines component placement and solder joint quality. |
Environmental Stress Screening | Simulates real-world conditions to identify potential weaknesses in PCBAs. |
Functional testing is particularly important for industrial automation. It ensures that your PCBA performs as intended under actual operating conditions. In-circuit testing, on the other hand, focuses on identifying manufacturing defects like soldering errors or misaligned components. By combining these methods, you can achieve comprehensive quality assurance.
Ensuring compliance with industry standards and certifications
Compliance with industry standards guarantees that your PCBA meets the highest quality and safety requirements. Adhering to these standards not only ensures reliability but also builds trust with your customers. Key standards for PCBA testing include:
IPC-SM 785 and IPC 9701: Guidelines for testing reliability in circuit board manufacturing.
MIL-STD 202 and MIL-PRF 3102: Environmental stress tests for printed circuit boards.
JEDEC standards: A collection of testing methods for electronic circuit boards.
IEC 60068: Environmental test methods, including vibrations, heat, and humidity tests.
These standards cover various aspects of PCBA testing, from environmental stress screening to thermal cycling. For example, MIL-STD 202 evaluates how well your PCBA withstands mechanical and environmental stresses. By following these guidelines, you can ensure that your automation systems perform reliably, even in harsh conditions.
💡 Tip: Use pcb design software to incorporate compliance requirements into your designs from the start. This approach simplifies the testing process and reduces the risk of non-compliance.
Future Trends in PCBA Technology for Industrial Automation
Advancements in materials and manufacturing processes
You can expect significant advancements in PCBA materials and manufacturing processes to shape the future of industrial automation. Manufacturers are now exploring materials like polyimide and ceramic substrates for their superior heat resistance and durability. These materials ensure that PCBA performs reliably in harsh industrial environments. Additionally, flexible PCBs are gaining popularity due to their ability to fit into compact and irregular spaces, making them ideal for modern automation systems.
On the manufacturing side, automation is revolutionizing production. AI-powered robotics and machine learning algorithms are optimizing assembly lines, reducing errors, and increasing efficiency. For example, automated optical inspection systems can now detect defects with incredible precision, ensuring high-quality output. These advancements not only improve the reliability of PCBA but also reduce production costs, making automation more accessible to various industries.
Integration with IoT, AI, and smart technologies
The integration of IoT, AI, and smart technologies is transforming PCBA and its role in automation. IoT-enabled PCBA allows real-time data collection and monitoring, which enhances operational efficiency. For instance, predictive maintenance systems use IoT to identify potential issues before they cause downtime, saving you time and resources.
AI is another game-changer. It uses big data analytics to optimize production schedules and improve supply chain management. This ensures that your automation systems operate at peak efficiency. Smart technologies, such as sensors and actuators, are also becoming more sophisticated. They enable seamless communication between devices, creating a fully connected and intelligent automation ecosystem.
Trend/Technology | Description |
---|---|
IoT Integration | Enhances connectivity and operational efficiency through real-time data. |
AI-Driven Decision Making | Optimizes production schedules and supply chain management. |
Sustainable Practices | Focuses on eco-friendly materials and processes to reduce environmental impact. |
Miniaturization and increased functionality of PCBA
Miniaturization is a key trend in PCBA technology. As devices become smaller, you need PCBA that can deliver high performance in a compact form. Multi-layer PCBs are leading this trend by stacking multiple conductive layers, allowing for complex circuits in a smaller footprint. This is especially important in automation, where space-saving designs are crucial.
Increased functionality is another area of focus. Modern PCBA integrates advanced features like wireless connectivity and high-speed data processing. These capabilities enable automation systems to handle more complex tasks with greater precision. For example, robotic arms equipped with advanced PCBA can perform intricate assembly tasks with minimal human intervention. This not only improves productivity but also ensures consistent quality.
📌 Tip: When selecting PCBA for your automation systems, prioritize designs that offer both compactness and advanced functionality. This ensures your systems remain efficient and future-proof.
Adoption of sustainable and eco-friendly practices.
Sustainability has become a critical focus in industrial automation. As industries grow, you must consider the environmental impact of your processes. By adopting eco-friendly practices, you can reduce waste, conserve resources, and align with global sustainability goals.
Eco-Friendly Materials in PCBA
Modern PCBA manufacturing uses materials that minimize environmental harm. For instance, lead-free solder and halogen-free laminates have replaced traditional, harmful substances. These materials ensure that your automation systems meet environmental standards while maintaining performance.
🌱 Tip: Look for PCBA suppliers certified under standards like RoHS (Restriction of Hazardous Substances) to ensure compliance with eco-friendly practices.
Energy-Efficient Manufacturing
Energy efficiency plays a vital role in sustainable automation. Advanced PCBA production techniques, such as automated assembly lines, reduce energy consumption. These methods not only lower your carbon footprint but also cut operational costs. For example, using energy-efficient reflow ovens during soldering can save significant power without compromising quality.
Recycling and Waste Management
Recycling is another way to make your automation systems more sustainable. Many PCBA components, such as copper and gold, can be recovered and reused. Implementing a recycling program for outdated boards helps you reduce electronic waste. Additionally, proper disposal of non-recyclable materials prevents environmental contamination.
Long-Term Benefits
Adopting sustainable practices benefits both the environment and your business. Eco-friendly automation systems appeal to environmentally conscious customers, enhancing your brand reputation. Moreover, compliance with green regulations avoids penalties and opens doors to new markets.
📌 Did you know? Sustainable automation practices can reduce production costs by up to 20% while improving energy efficiency by 30%.
By integrating sustainability into your automation processes, you contribute to a healthier planet while staying competitive in the industry.
Real-World Applications for PCBs in Industrial Automation
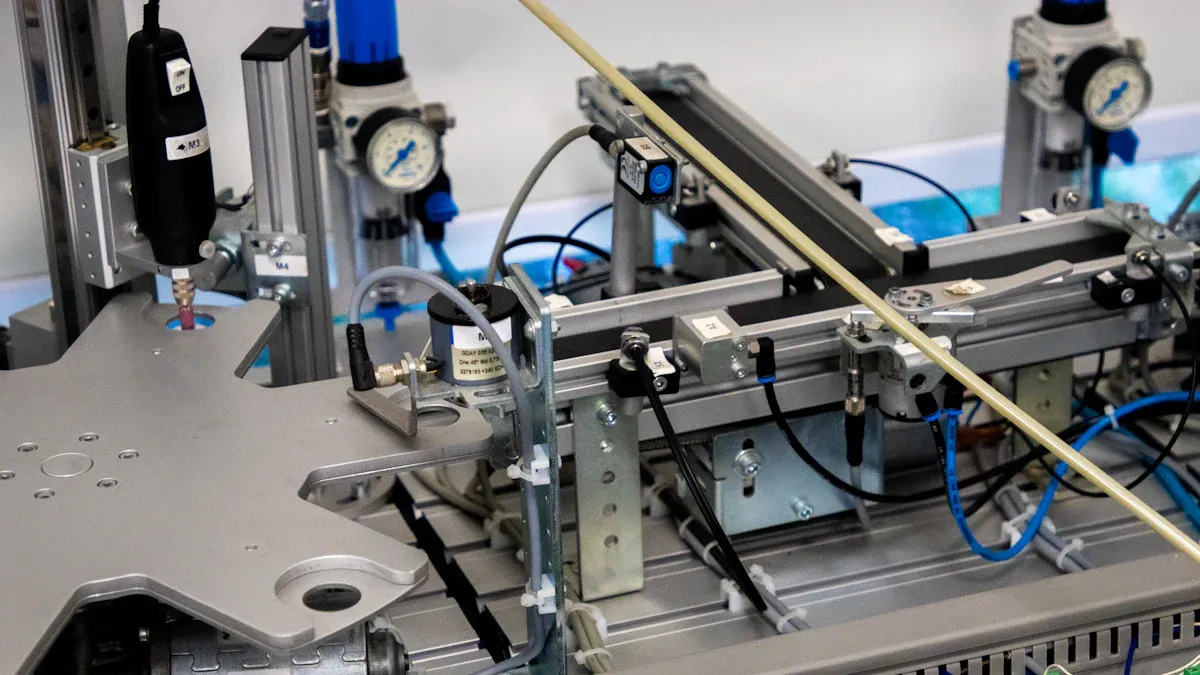
Use of PCBA in robotics and automated machinery
PCBA plays a vital role in robotics and automated systems. It acts as the control center, enabling precise movements and efficient operations. In robotics, PCBA ensures seamless communication between sensors, actuators, and processors. This allows robots to perform tasks like assembly, welding, and material handling with high accuracy. For example, robotic arms in manufacturing plants rely on PCBA to execute repetitive tasks quickly and consistently.
Automated machinery also benefits from PCBA. It powers systems that monitor and adjust processes in real time. For instance, conveyor belts equipped with PCBA can detect product defects and remove faulty items without human intervention. This improves efficiency and reduces waste. By integrating PCBA into your automated systems, you can achieve higher productivity and better quality control.
Case studies showcasing PCBA-driven innovations
Real-world examples highlight the transformative impact of PCBA in industrial automation. Companies across industries have leveraged PCBA to enhance their operations. Here are two notable case studies:
Industry | Company | Case Study Description | Key Features | Results |
---|---|---|---|---|
Automotive | BMW | Implementation of CIRE at Spartanburg plant for door assembly. | Lightweight cobots assist in door seal installation, AI vision systems, IoT sensors for monitoring. | 50% reduction in worker fatigue, 20% increase in production speed, 85% decrease in defects. |
Electronics | Hitachi | CIRE in Omika Works for PCB assembly and control systems manufacturing. | Collaborative robots, AI for scheduling, AR interfaces for assembly guidance. | 30% increase in OEE, 40% reduction in lead times, 25% improvement in customization. |
These examples demonstrate how PCBA enhances efficiency, reduces errors, and supports innovation in automated systems. By adopting similar strategies, you can optimize your operations and stay competitive.
Industries benefiting from PCBA, such as automotive, manufacturing, and energy sectors
PCBA has revolutionized industries like automotive, manufacturing, and energy. In the automotive sector, PCBA powers advanced driver-assistance systems (ADAS), electric vehicle (EV) components, and automated assembly lines. These applications improve safety, efficiency, and sustainability. For example, PCBA enables precise control of EV batteries, ensuring optimal performance and longevity.
In manufacturing, PCBA supports automated systems that streamline production. It powers robotic arms, quality control systems, and IoT-enabled devices. These technologies enhance productivity and reduce costs. The energy sector also benefits from PCBA. It drives renewable energy solutions like solar inverters and wind turbine controllers. These systems rely on PCBA for efficient energy conversion and grid management.
By leveraging PCBA, these industries achieve higher efficiency, better reliability, and greater innovation. You can explore similar applications to transform your operations and meet the demands of modern industrial automation.
Printed Circuit Board Assembly (PCBA) is the cornerstone of industrial automation. It empowers you to achieve greater efficiency, reliability, and innovation in factory systems. By enabling seamless communication between components, PCBA ensures smooth operations and minimizes downtime.
🌟 Future Outlook: As PCBA integrates with IoT, AI, and sustainable practices, it will redefine automation technologies. You can expect smarter, more adaptable systems that meet evolving industrial demands.
By leveraging PCBA, you can stay ahead in the competitive landscape and unlock new possibilities for growth and innovation.
FAQ
What is the difference between PCB and PCBA?
A PCB is a bare circuit board without components. PCBA refers to a PCB with all components assembled and ready for use. You can think of PCB as the foundation and PCBA as the complete, functional product.
How does PCBA improve industrial automation?
PCBA enhances automation by enabling machines to perform tasks with precision and speed. It integrates sensors, processors, and actuators, ensuring seamless communication. This reduces errors, increases efficiency, and supports real-time decision-making in automated systems.
Can PCBA withstand harsh industrial environments?
Yes, specialized PCBA uses durable materials like polyimide and ceramic substrates. These materials resist high temperatures, vibrations, and mechanical stress. Rigorous testing ensures reliability, even in extreme conditions like factories, oil rigs, or aerospace applications.
Why is multi-layer PCBA important for advanced systems?
Multi-layer PCBA allows compact designs with high routing density. It supports complex circuits, improves signal integrity, and reduces electromagnetic interference. This makes it essential for advanced systems like robotics, aerospace equipment, and high-speed data processors.
How do you ensure PCBA quality during production?
Manufacturers use testing methods like in-circuit testing (ICT) and functional testing. These tests identify defects and verify performance. Standards like IPC and MIL-STD guide quality assurance, ensuring your PCBA meets industry requirements.
💡 Tip: Always choose PCBA suppliers with certifications like ISO 9001 for guaranteed quality.
See Also
Enhancing Industrial Automation Efficiency Through PCBA Technology
Essential Technologies Shaping PCBA Production in Today’s Electronics
Exploring Sub PCBA Uses in Electronics and Other Fields
Benefits and Obstacles of PCBA in Contemporary Electronics
Understanding Automotive PCBA Assembly’s Importance for 2025