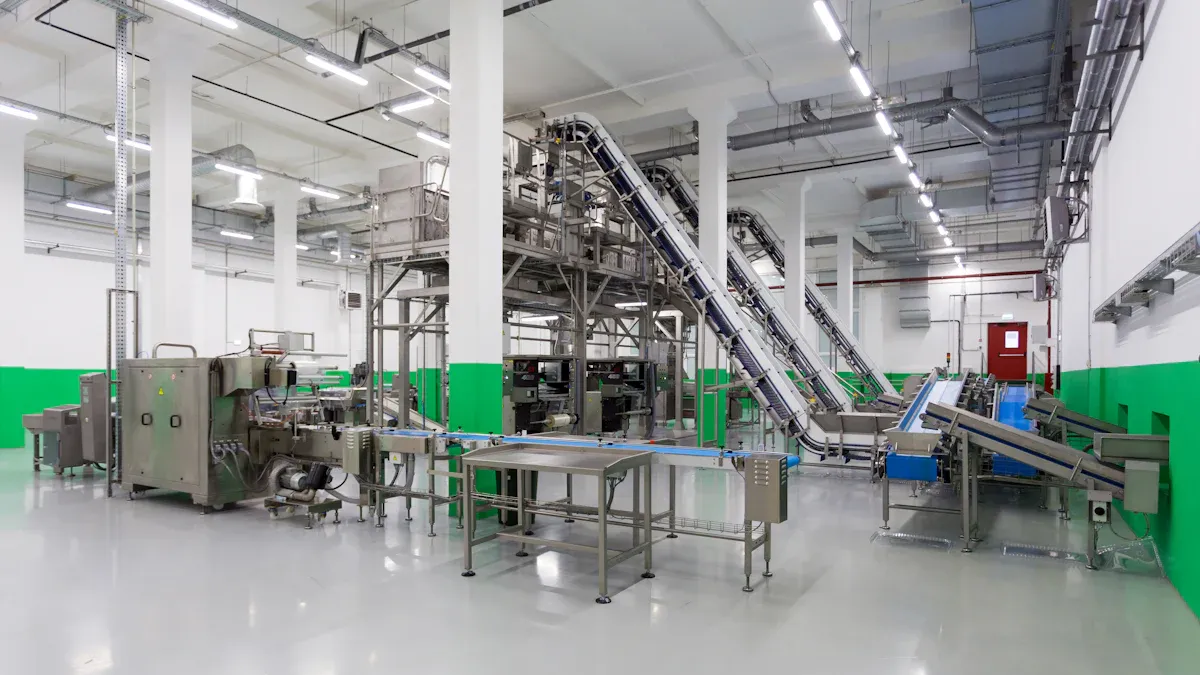
Imagine knowing exactly when ocean rip currents will happen. This could save many lives. Similarly, the concept of a PCB rip current forecast can revolutionize Sustainable PCB Manufacturing. Just as rip current forecasts rely on models to analyze data and predict outcomes, these tools can be applied in PCB production to minimize waste and optimize resource usage. Embracing such methods not only benefits the planet but also enhances efficiency. Smart data utilization has the potential to transform how we approach Sustainable PCB Manufacturing.
Key Takeaways
Predictive tools help find issues early, reducing PCB waste.
Using safer materials and clean energy makes PCB production greener.
Recycling old PCBs saves resources and lowers production expenses.
Smart tools track energy use, improving efficiency and cutting pollution.
Green manufacturing helps the planet and saves companies money.
Rip Current Forecasts and Predictive Modeling
What Are Rip Current Forecasts?
Rip current forecasts tell when and where rip currents may happen. They use data from weather, ocean currents, and waves. Scientists study this data to find risky spots and warn swimmers.
Rip currents are dangerous because they pull people away from the shore. These fast-moving water channels often surprise beachgoers. Predicting them helps save lives and avoid accidents.
Tip: Rip current forecasts act like a safety guide for beaches. They use science to keep people safe and informed.
Experts use tools like radar and satellite images to collect data. This data goes into models that predict where rip currents might form.
Principles of Predictive Modeling in Rip Current Forecasts
Predictive modeling is key to rip current forecasts. It uses math to study patterns and guess future events. Models depend on past data, live updates, and simulations for accuracy.
Here’s how predictive modeling works:
Data Collection: Experts gather details about waves, wind, and tides.
Pattern Recognition: Computers find trends and links in the data.
Simulation: Models test scenarios to predict what might happen.
Predictive modeling isn’t just about numbers. It shows how different factors connect. For instance, changing wind direction can raise rip current risks.
🌊 Fun Fact: Some models even predict rip currents months ahead by studying seasons.
Using these methods makes forecasts more trustworthy. They help you stay safer at the beach.
Challenges and Opportunities in Sustainable PCB Manufacturing
Environmental Challenges in PCB Manufacturing
Making printed circuit boards can harm the environment. The process creates dangerous waste, like polychlorinated biphenyls. These chemicals can hurt nature and people if not handled well.
Factories often pollute water by releasing harmful metals and chemicals. This dirty water can poison rivers and underground water sources. Air pollution happens too, from gases released during production.
PCB production uses a lot of energy, which adds to carbon emissions. If old PCBs aren’t managed properly, toxic materials can leak into the ground. Recycling and safe disposal are very important to fix this issue.
Sometimes, mistakes in PCB production cause extra waste. Finding and fixing these mistakes can lower environmental damage. Solving these problems helps make PCB manufacturing better for the planet.
Green Manufacturing Principles for PCB Production
Green manufacturing aims to save resources and cut down waste. To make PCB production eco-friendly, follow some key ideas.
First, switch to safer materials. Using alternatives to polychlorinated biphenyls reduces harm to the environment. Second, use energy-saving tools. Renewable energy can help lower pollution from factories.
Recycling is very helpful in green manufacturing. Recovering useful parts from old PCBs reduces the need for new materials. Cleaning wastewater before releasing it stops water pollution.
Smart tools can predict problems in PCB production. These tools use data to find issues early and improve processes. Fixing problems quickly prevents waste and saves resources.
Using green methods protects nature and makes production more efficient. Green manufacturing helps industries grow while caring for the planet.
Connecting Rip Current Forecasts to Sustainable PCB Manufacturing
Using Predictive Models in PCB Manufacturing
Predictive models can change how printed circuit boards are made. These models study data to find patterns and guess results. Using them helps reduce waste, save resources, and work more efficiently.
In PCB production, predictive modeling spots problems before they happen. For example, it makes failure analysis better with data tools. These tools find PCB defects early, saving time and materials.
Here’s how predictive modeling works in PCB production:
Data Collection: Collect details about materials, processes, and the environment.
Pattern Recognition: Software finds trends like repeated defects or wasted resources.
Simulation: Test ideas to predict results and improve production steps.
Predictive models also help with environmental problems. They show ways to use fewer harmful substances like polychlorinated biphenyls. They also track energy use and suggest switching to renewable energy.
Tip: Predictive modeling isn’t just for fixing mistakes. It helps design smarter processes that make PCB production eco-friendly.
Examples of Predictive Modeling in Green Manufacturing
Predictive modeling is already helping green manufacturing grow. Many industries use it to focus on sustainability.
One example is recycling. Predictive tools study old PCBs to find useful parts. This reduces waste and saves materials.
Another example is energy tracking. Factories use predictive models to check energy use. They find ways to switch to cleaner and more efficient energy sources.
Predictive modeling also helps find defects in PCBs. By studying past production data, factories learn what went wrong. This helps improve processes and avoid future mistakes.
🌱 Fun Fact: Some factories use predictive models to predict how their work affects the environment. This helps them choose better materials and methods.
These examples show how predictive modeling supports green manufacturing. Using these tools makes PCB production better for the planet and more efficient.
Benefits of Using Predictive Modeling in PCB Manufacturing
How It Helps the Environment
Predictive modeling makes PCB production kinder to the planet. It studies data to find ways to cut waste and pollution. For instance, it tracks polychlorinated biphenyls and suggests safer options. This stops harmful chemicals from entering nature.
These tools also check how much energy is used. They show where energy is wasted and suggest fixes. Switching to renewable energy lowers pollution and helps the Earth.
Water safety improves too. Predictive models study wastewater and suggest cleaning methods. This keeps rivers and groundwater free from harmful chemicals.
Using predictive modeling means cleaner manufacturing. It also ensures your work follows eco-friendly rules.
🌱 Tip: Predictive tools protect nature and impress eco-friendly customers.
Saving Money with Predictive Tools
Predictive modeling isn’t just good for nature; it saves money too. It finds problems early, so less material is wasted. This means fewer bad PCBs and lower costs.
It also helps use resources wisely. These tools find where materials are overused. Fixing this saves money and boosts efficiency.
Energy tracking is another plus. Predictive models show how to use less energy. Switching to renewable energy cuts bills and helps the planet.
Recycling gets easier too. Predictive tools find useful parts in old PCBs. Reusing these parts saves money and reduces waste.
💡 Note: Predictive modeling costs money at first but saves more later.
By using predictive modeling, you help the planet and save money. It’s a win-win!
Predictive modeling, like rip current forecasts, changes how PCBs are made. Using data, it cuts waste, saves resources, and solves environmental problems. These tools make production better and kinder to the planet.
With predictive modeling, PCB production becomes smarter and eco-friendly. It follows green rules and encourages new ideas. By using these methods, you help the Earth and lead in sustainable manufacturing.
🌱 Takeaway: Simple steps in PCB production can greatly help the environment.
FAQ
What does green manufacturing mean in PCB production?
Green manufacturing means making PCBs while cutting waste and pollution. It uses safe materials, saves energy, and recycles to help nature.
How can predictive modeling help PCB production?
Predictive modeling studies data to find problems before they happen. It cuts waste, saves resources, and makes production faster and better.
Can old PCBs be recycled using predictive tools?
Yes, predictive tools find parts in old PCBs to reuse. This lowers waste and saves materials, making recycling easier.
Is renewable energy good for PCB factories?
Using renewable energy reduces pollution and saves money on power. It also helps factories follow eco-friendly rules.
Are predictive models costly to start?
Predictive models cost money at first but save later. They cut waste, improve work, and lower energy bills over time.
See Also
Achieving Superior Quality Through PCBA Manufacturing Mastery
Comparing Lead-Free and Lead-Based Processes in PCBA
Ensuring Quality Control Throughout the Entire PCBA Process
Emerging Smart Manufacturing Trends Shaping PCBA in 2025
Essential Technologies Transforming PCBA Manufacturing for Consumers