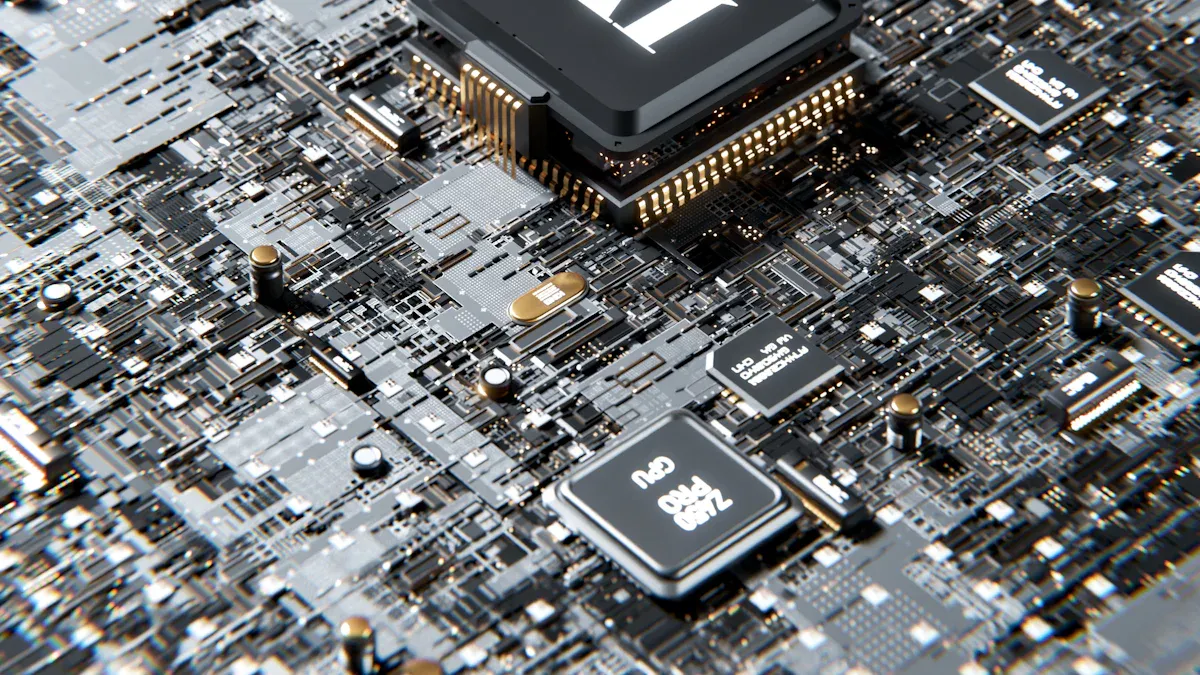
Industrial automation PCBA services play a crucial role in enhancing efficiency and precision in industrial automation. These services streamline production processes, save costs, and minimize errors through automated PCB assembly. Key advantages include:
Faster and consistent assembly operations.
Reduced reliance on manual labor, leading to cost savings.
Superior quality achieved through precise and repetitive tasks.
Strict adherence to production standards.
Industrial automation PCBA services enable the creation of compact and reliable designs, ensuring the seamless operation of systems like robotics and safety controls. This fosters innovation across various industries.
Key Takeaways
PCBA makes work faster by automating assembly, cutting mistakes.
It saves money by reducing handwork and keeping quality steady.
PCBA works with smart tech like AI and IIoT to watch systems and fix problems quickly.
Strong PCBs handle tough conditions, lasting longer in factories.
Green PCBA materials and methods help the planet and improve work efficiency.
Understanding PCBA in Industrial Automation
What is PCBA?
PCBA means Printed Circuit Board Assembly. It involves putting electronic parts on circuit boards. These boards are key to modern automation devices. They help machines do complex tasks accurately. PCBA is used in many fields like cars, medical tools, and airplanes.
To make sure PCBA works well, manufacturers follow IPC rules. These rules guide how to design, build, and test PCBA. By following them, companies make reliable boards that work for automation systems.
Importance of PCBA in Industrial Automation
PCBA is important for devices like robots and controllers. It helps these devices work faster and more accurately. PCBA also reduces downtime and makes production smoother.
PCBA allows advanced tech like AI and IIoT to work in automation. These tools help monitor systems and fix problems early. PCBA is strong and flexible, making it perfect for modern automation.
How PCBA Supports Automation Processes
PCBA helps by automating tasks and improving accuracy. It keeps machines running longer and reduces waste. It also makes managing complex systems easier.
AI tools make PCBA even better by finding problems early. This lowers waste and improves results. PCBA also makes fixing machines easier with helpful feedback. These features make PCBA essential for automation systems.
Key Benefits of PCBA in Industrial Automation
Enhancing Reliability and Durability
Industrial systems must work well in tough conditions. PCBA helps these systems stay reliable by making electronics stronger. Manufacturers use special tests to ensure durability.
For example, they do tests like:
Checking if PCBs handle big temperature changes.
Testing resistance to moisture over long periods.
Ensuring stability during vibrations while working.
These tests make sure PCBs work even in hard environments. The table below shows more tests that improve reliability:
Testing Method | Purpose |
---|---|
High Accelerated Temperature and Humidity Stress Testing (HAST) | Checks if PCBs survive high heat and moisture for a long time. |
Temperature Cycling | Tests if PCBs can handle extreme temperature changes repeatedly. |
Salt Spray Testing | Ensures PCBs resist damage in salty or corrosive places. |
These methods help PCBs last longer and work better. Reliable PCBs mean less downtime and fewer repairs. This makes your systems more dependable and cost-effective.
Space Optimization and Miniaturization
Modern automation needs smaller, smarter designs. PCBA helps by creating compact devices that work better. Smaller designs fit more features into less space.
For example:
Tiny holes in PCBs improve electrical performance.
They also reduce problems in fast circuits.
This is important for industries like aerospace. Smaller satellites cost less to launch and can share rockets. In automation, compact PCBs make systems fit tight spaces while staying powerful.
Cost-Effectiveness in Manufacturing
PCBA helps lower manufacturing costs. Automated assembly reduces mistakes and needs less manual work. This saves money and keeps quality consistent.
Mass production of PCBs also cuts costs. Using standard designs and machines makes many reliable PCBs quickly. Strong PCBs last longer, so you spend less on repairs.
Investing in PCBA saves money and boosts efficiency. It’s a smart choice for businesses wanting better operations.
Scalability and Performance Improvements
Scalability and performance are key for automation systems. PCBs help these systems grow while staying efficient. Using advanced PCBA technology improves speed, saves time, and boosts quality.
Higher Throughput: Automated systems with PCBs work faster than manual ones. They increase production speed and keep outputs consistent.
Reduced Cycle Times: PCBs cut the time needed for each production step. This helps meet deadlines without lowering quality.
Improved Quality Control: Accurate part placement and defect checks improve product quality.
Tip: Scalable PCBA solutions let systems handle more work without big changes.
Feature | Benefit |
---|---|
Precision Placement | Fewer defects and better quality with accurate part placement. |
Consistent Quality | Keeps quality high with reliable defect detection. |
Scalability | Handles more production to meet growing needs. |
Flexibility | Works with different designs and parts for market changes. |
PCBs also reduce downtime. Strong PCBs mean fewer system breaks, improving efficiency. They adjust to new designs and parts, helping you keep up with changes.
Using PCBs lets your systems grow easily. Whether increasing production or adding new products, PCBs ensure steady performance and flexibility.
Applications of PCBA in Industrial Automation Systems
PCBA in Programmable Logic Controllers (PLCs)
Programmable logic controllers are key in industrial automation. They control machines and keep operations running smoothly. PCBs are essential for these controllers, helping them process data and work efficiently.
PCBAs improve how PLCs perform. They process data faster and control systems accurately. For example, in a factory, a PLC with a strong PCBA can manage conveyor belts, adjust speeds, and find problems quickly. This reduces downtime and increases productivity.
Custom PCBs for PLCs also allow growth. As automation needs increase, these PCBs handle harder tasks without losing performance. This makes them very useful in modern automation systems.
Role of PCBA in Robotics and Motion Control
Robotics and motion control systems rely on PCBAs. These systems need precise movements and quick decisions, which PCBAs provide.
In robots, PCBAs power sensors, motors, and control units. They use sensor data to guide robotic arms or vehicles. For instance, on an assembly line, robots with advanced PCBAs can pick and place parts with great accuracy. This speeds up work and reduces mistakes.
Motion control systems also use PCBAs. They control motor speed, position, and force. A good PCBA keeps these systems running smoothly, even in tough conditions. Whether it’s a robotic arm or a conveyor belt, PCBAs improve reliability and performance.
Note: PCBs are crucial for robotics. They help machines do hard tasks with little human help, driving progress in automation.
PCBA in Safety and Monitoring Systems
Safety and monitoring systems are vital in automation. PCBAs make these systems better by giving real-time data and working reliably.
You’ll find PCBAs in sensors that check operations and spot problems. For example:
Smart cities use PCBAs in sensors to measure air quality.
Industrial sensors with PCBAs check machines for wear and damage.
These sensors work in tough places like high heat and vibrations.
PCBAs are also used in safety devices like stop buttons and fire alarms. In smart factories, PCBAs in monitors warn about dangers, so you can act fast.
But challenges exist. Heat and moisture can harm PCBAs. Manufacturers fix this by using strong materials and testing carefully. This ensures PCBAs work well in harsh conditions.
Tip: High-quality PCBA services improve safety and efficiency. Strong PCBAs lower risks and make systems more stable.
Integration with Industrial IoT and Smart Factories
Industrial IoT (IIoT) and smart factories change how industries work. These technologies link machines, sensors, and systems for smooth data sharing. PCBs are key to making this connection possible. They act as the base for devices used in IIoT and smart factories.
In smart factories, PCBs connect sensors, controllers, and communication tools. These parts team up to watch and improve production. For example, sensors with advanced PCBs check machines in real time. This helps find problems and fix them quickly.
PCBs also allow wireless communication in IIoT systems. They help devices share data using Wi-Fi, Bluetooth, or Zigbee. This keeps all factory parts connected. For instance, a PCB device can alert you when a machine needs fixing. This cuts downtime and boosts efficiency.
Another benefit of PCBs in IIoT is handling big data. Modern PCBs process and send data fast, keeping operations smooth. In smart factories, this means you can check production stats and decide faster.
Tip: Use strong PCBs for your IIoT devices. Good PCBs work reliably and lower system failure risks.
PCBs also save energy in smart factories. They manage power use across devices, cutting costs and helping the environment.
As IIoT and smart factories grow, PCBs stay important. They support advanced tech like AI and machine learning. These tools need PCBs to handle complex tasks and give useful insights.
Adding PCBs to your IIoT systems improves efficiency and productivity. Whether automating jobs or making better choices, PCBs make it happen.
Design and Assembly Tips for Industrial Automation PCBA Services
Keeping PCBs Cool for Better Performance
Managing heat is key to keeping PCBs working well. If parts get too hot, they can break. Using smart cooling methods helps PCBs stay cool under tough conditions.
For instance, tiny thermoelectric coolers and diamond layers remove heat fast. Forced cooling systems, like TEC modules, make heat sinks work 200% better. CoolSiC™ semiconductors cut heat loss by 64% in high temperatures. These tools help PCBs handle heavy tasks without overheating.
Study/Source | Findings | Cooling Methods |
---|---|---|
JEDEC Committee on Wide Bandgap Power Electronics | Standards for SiC and GaN technologies | Focus on quality and reliability |
Cal Tech and Jet Propulsion Laboratory | Thermoelectric microcoolers for spot cooling | Diamond or aluminum layers |
National Renewable Energy Lab | Cooling SiC devices | Low thermal resistance TIM and microchannels |
European Commission’s SMARTPOWER project | Forced cooling solutions with TEC modules | Improved heat sink performance by 200% |
ATS Cold Plates | 30% better than other cold plates | Special internal fin design |
Using these ideas makes PCBs last longer and work better.
Stopping Electrical Noise in PCBs
Electrical noise, or EMI, can harm PCBs and devices. To stop this, plan for EMI and EMC during design.
High-frequency currents often cause noise problems. Placing parts carefully can lower noise. PSPICE models help find noise sources early. Sudden events, like relay bounces, also create noise. Radiation models can predict and block these issues.
Helpful steps include:
Checking high-frequency currents with special tools.
Watching small voltage changes, as even 300 mV can harm parts.
Following SEMI E176 rules to control ground plane currents.
These steps keep PCBs working well in noisy places.
Picking Strong Materials for PCBs
Choosing strong materials makes PCBs last longer in tough jobs. Materials like polyimide and Rogers laminates handle heat and electricity well. These are great for aerospace and communication systems.
Material | Features | Uses |
---|---|---|
Polyimide Substrates | Handles heat, stays flexible | Military and aerospace |
Rogers Materials | Low signal loss, strong dielectric | RF and microwave communication |
Metal Core PCBs | Moves heat away fast | LED lighting and power electronics |
Accelerated Life Testing (ALT) finds weak spots in PCBs. This testing helps pick materials that survive heat and shaking. ALT results can also improve designs to make PCBs stronger.
Using tough materials and testing ensures PCBs work well in hard conditions.
Testing and Quality Assurance
Testing ensures PCBs work well in automation systems. Strict checks during and after assembly confirm quality. These steps make sure PCBs meet standards and work in real conditions.
First, use parts from trusted suppliers. Good suppliers give proof that parts meet quality rules. During assembly, checks happen at many stages. Both manual and machine methods find problems early.
Advanced tests improve quality checks further. AOI uses cameras to spot misplaced parts or solder issues. TDR testing finds electrical breaks by measuring impedance. Flying probe tests check PCBs cheaply without special tools.
In-circuit testing (ICT) is also important. It finds open or short circuits and checks chip performance. Functional tests mimic real use to confirm PCBs meet industry needs. These tests prove PCBs can handle automation tasks.
Keeping accurate records is key. This data helps find problems and keeps quality steady. By following these steps, you reduce mistakes, cut downtime, and make systems more reliable.
Tip: Regular testing keeps PCBs working longer and saves money over time.
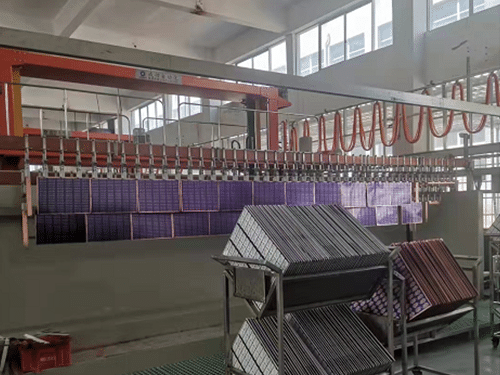
Future Trends in PCBA for Industrial Automation
Miniaturization and Advanced Packaging
Smaller and smarter devices are changing PCBA technology. Miniaturization helps fit more features into tiny spaces. This is important for modern automation systems. Advanced packaging, like embedded die and system-in-package (SiP), boosts performance while shrinking size. These methods are vital for industries like cars and electronics, where lightweight parts are needed.
The advanced packaging market is growing fast. In 2021, it was worth $30 billion. By 2031, it may reach $55 billion, growing at 8% yearly. By 2034, it could hit $111.4 billion with an 11.5% yearly growth. This growth is due to MEMS and bigger silicon wafers, which cut costs. These improvements make PCBs smarter and cheaper, helping create better automation systems.
AI and Machine Learning Integration
AI and machine learning are changing how PCBs work in automation. These tools help PCBs process data quickly and make instant decisions. For example, AI can adjust factory settings to save time and reduce waste. Predictive maintenance uses data to find problems early, avoiding breakdowns.
High-speed PCBs are now needed for fast data transfer. With 5G and IoT, these boards ensure smooth device communication. AI also improves quality checks by spotting defects during production. Adding AI to PCBs makes systems faster, more reliable, and better for complex tasks.
Flexible and Wearable PCBs
Flexible and wearable PCBs bring new ideas to automation. These boards can bend and stretch, fitting into small or odd shapes. For example, stretchable boards are made for jobs needing extra flexibility. Thin, flexible PCBs are already used in wearables and screens, showing their value.
These boards work well where rigid PCBs fail. Flexible PCBs are tough and adaptable, making them great for hard conditions. As tech improves, these boards will help build better and more versatile systems.
Tip: Use flexible PCBs for lightweight and adaptable designs. They combine strength and flexibility, making them a smart choice for automation projects.
Sustainable and Eco-Friendly Materials
Sustainability is now important in PCBA manufacturing. Using eco-friendly materials helps protect the environment and build better automation systems. These materials cut waste and make products easier to recycle.
Eco-friendly processes have many advantages:
They lower harmful waste and keep production cleaner.
Green materials improve recycling and remove dangerous substances.
Lifecycle checks ensure sustainability from start to finish.
For instance, lead-free solder and halogen-free laminates reduce toxic emissions. These materials follow rules like RoHS, meeting global environmental standards. Biodegradable substrates also break down naturally, cutting landfill waste.
Recycling is key for sustainable PCBs. Recovering metals like copper and gold reduces mining and saves resources. Some PCBs are now designed for easy disassembly, making recycling simpler at the end of their use.
Energy-saving production methods boost sustainability further. Additive manufacturing uses fewer materials and creates less waste. These methods match the need for greener automation systems.
Tip: Choose materials that balance good performance with low environmental impact. This supports sustainability and shows your brand cares about the planet.
By going green, you help the environment while keeping your systems efficient and reliable. Eco-friendly PCBs are not just popular—they are the future of smart manufacturing.
PCBA is crucial for industrial automation. It helps systems work well and last long. Its small size and strength make it key for linking parts like sensors and controllers. Without PCBs, factories would struggle to stay productive.
Many industries need better PCBs:
Cars use special PCBs for electric and self-driving vehicles.
Medical tools need strong PCBs for precise testing.
Factories use PCBs to improve automation and controls.
As tech improves, PCBA will lead the way, creating smarter systems.
FAQ
What is the difference between PCB and PCBA?
A PCB is just a plain circuit board. It has no parts on it. A PCBA is a PCB with all its parts attached. Think of a PCB as the base and a PCBA as the finished product.
How does PCBA improve industrial automation?
PCBA helps machines work faster and more accurately. It powers robots, sensors, and controllers. With PCBA, systems become reliable, small, and cost-saving. This boosts performance and cuts downtime.
Can PCBA handle harsh industrial environments?
Yes, PCBA works well in tough places. Strong materials and careful testing make it reliable. It resists moisture, heat, and shaking, so it’s great for hard jobs.
Why is miniaturization important in PCBA?
Smaller PCBA designs save space and add more features. This is key for modern systems. Compact designs improve performance, lower costs, and fit into tight spaces.
Is PCBA eco-friendly?
Yes, PCBA can be eco-friendly. Using green materials and methods helps the planet. Lead-free solder and recyclable parts reduce waste. Choosing eco-friendly PCBA supports a cleaner future.
Tip: Pick PCBA services that focus on quality and being eco-friendly. This helps your systems and the environment.
See Also
Discover AI’s Role in Advancing PCBA for Electronics
Speeding Up PCBA Production While Maintaining High Standards
Expert Techniques for Achieving Superior PCBA Manufacturing