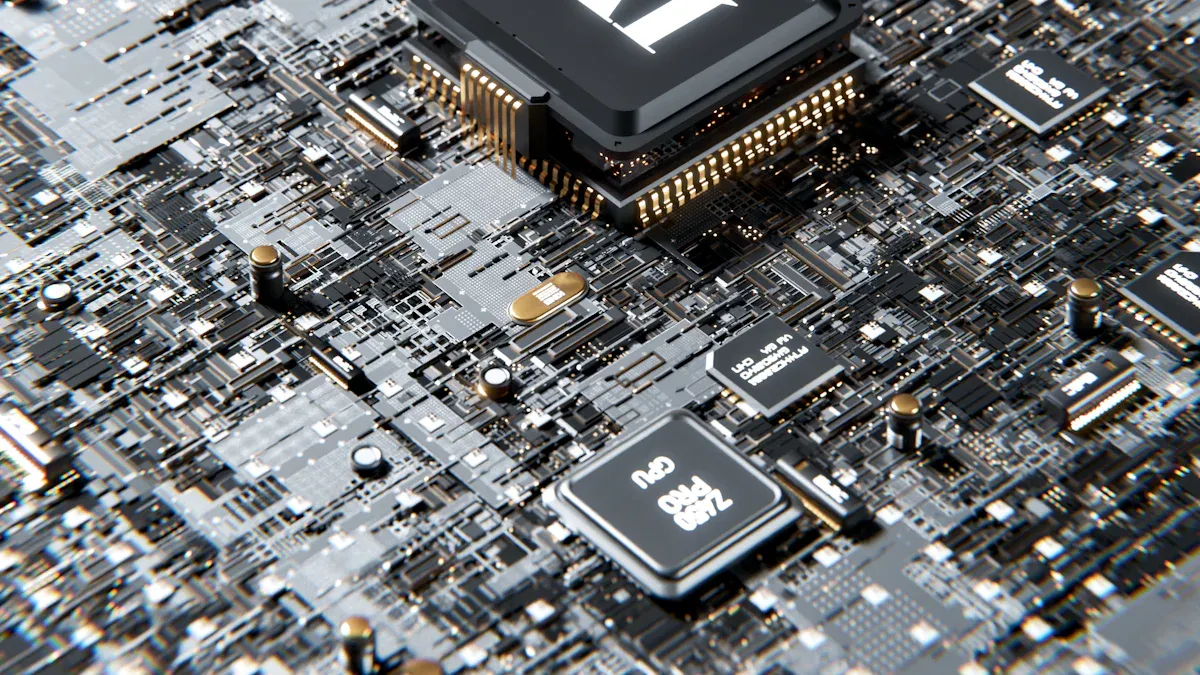
Printed Circuit Board Assembly (PCBA) plays a crucial role in modern electronics manufacturing by integrating electronic components onto a printed circuit board (PCB) to create functional electronic devices. Understanding PCBA meaning in modern electronics manufacturing highlights its importance in transforming basic circuit boards into advanced systems.
The PCBA industry has experienced significant growth due to advancements in technology and the rising demand for popular electronic devices. For instance:
The global PCB and PCBA market was valued at $68.4 billion in 2023 and is projected to reach $105.8 billion by 2032.
Asia-Pacific dominates PCB production, accounting for 47% of the market revenue in 2022.
This expansion underscores the increasing demand for smaller, more efficient, and reliable electronics in today’s technology-driven world.
Key Takeaways
PCBA stands for Printed Circuit Board Assembly. It helps electronic devices work by putting parts on a circuit board to make it functional.
The PCBA industry is growing fast because people want smaller and better electronics. This shows how important PCBAs are in today’s technology.
Quality checks, like inspections and tests, are done during PCBA. These checks make sure devices work well and catch issues early.
Picking the right PCBA supplier is very important. Choose suppliers with good skills, proper certifications, and a strong reputation for quality products.
Definition of PCBA and its importance
What is PCBA?
Printed Circuit Board Assembly (PCBA) is the finished board after adding all parts to a Printed Circuit Board (PCB). A PCB is just a plain board, but a PCBA includes parts like resistors, capacitors, and microchips. These parts help the board send signals and do specific tasks.
Think of a PCBA as the brain of modern electronics. Without it, gadgets like phones, computers, and medical tools wouldn’t work. The meaning of PCBA shows how it turns simple boards into powerful systems that run complex devices.
Why is PCBA essential in electronics manufacturing?
PCBA is key in making electronics work well and last long. It improves how devices perform and makes them more reliable.
Better Durability: Special coatings protect PCBAs from water, dust, and damage. These methods help devices work even in tough conditions.
More Reliability: Cleaning PCBAs stops problems like corrosion and tiny metal growths. Clean PCBAs work better and fail less often than dirty ones.
Smaller Devices: PCBA lets makers fit many features into tiny gadgets. For example, fitness trackers like Fitbit have GPS, heart rate monitors, and Bluetooth in one small PCBA.
PCBA is important for more than just everyday gadgets. In healthcare, PCBAs power life-saving tools like defibrillators and scanners. This shows how PCBAs are needed to make reliable and portable devices for many industries.
The meaning of PCBA in modern electronics is more than just technical. It stands for progress, smart designs, and meeting the needs of today’s tech world.
PCBA vs. PCB: Key differences explained
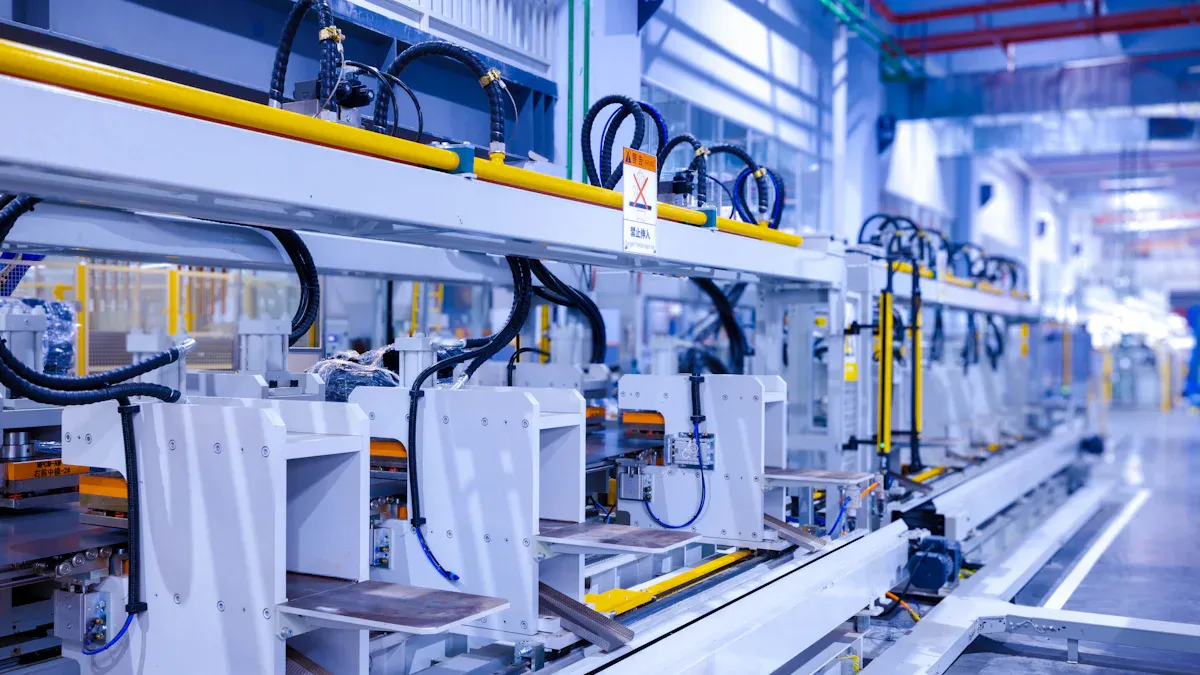
What is a PCB (Printed Circuit Board)?
A PCB is the base of most electronics. It is a flat board made from materials like fiberglass. Thin copper lines on the board connect different parts. These lines let electricity flow between components. But a PCB alone cannot do anything. It needs parts added to work.
PCBs are carefully made to meet strict rules. For example:
25-micron hole plating makes the board stronger and prevents breaks.
Solder masks protect the board from rust and damage.
These features make PCBs reliable and long-lasting. They are a strong starting point for building electronic devices.
Feature | Benefits | Risks |
---|---|---|
25-micron nominal hole plating | Makes boards stronger and prevents breaks. | Can cause holes or connection problems. |
Defined solder masks (IPC-SM-840 class T) | Stops rust and keeps circuits safe. | Bad ink can harm the board. |
How is PCBA different from PCB?
PCBA and PCB are not the same. A PCB is just a plain board. A PCBA, or printed circuit board assembly, has all the parts added. These parts include resistors, chips, and capacitors. They make the board work and do tasks.
Making a PCBA takes more steps than making a PCB. Parts must be bought, placed, and soldered onto the board. This process costs more and is harder to do. But it also makes the board more reliable. Careful testing finds problems early, so the final product works better and lasts longer.
Why is PCBA important for devices?
PCBA turns a simple board into a working device. Adding parts lets the board do specific jobs. For example, in a phone, the PCBA helps it connect to the internet and show pictures on the screen.
Quality checks are very important in PCBA production. Using good parts lowers the chance of failure. This makes devices more reliable and builds trust with users. Without PCBA, we wouldn’t have modern gadgets like fitness trackers, laptops, or medical tools.
Aspect | Explanation |
---|---|
Quality Assurance | Good parts make devices work better and last longer. |
Reliability | PCBAs handle stress and keep working well. |
Consumer Trust | High-quality boards make people trust the product more. |
The PCBA process in electronics manufacturing
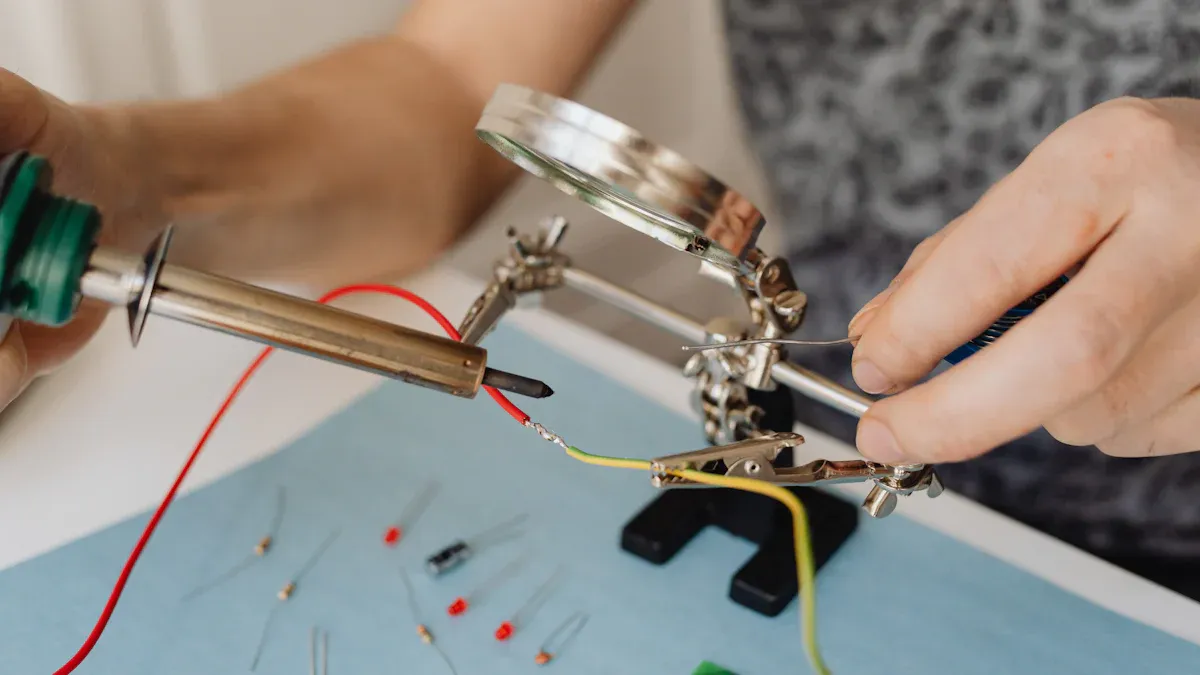
Solder paste application
The first step in making a PCBA is applying solder paste. This paste is a mix of powdered solder and flux. It acts like glue, holding parts on the PCB before soldering. Think of it as the sticky layer that keeps everything in place.
Manufacturers use stencils to apply the paste exactly where needed. These stencils make sure the paste only goes on the pads for components. It’s very important to do this step correctly. If the paste is uneven or messy, it can cause weak connections or short circuits.
Here’s a simple guide to solder paste quality:
Parameter/Defect | Description |
---|---|
Paste consistency | Paste should be smooth for good flow and sticking. |
Volume | Enough paste prevents weak joints but not too much. |
Area | Paste must cover all pads properly. |
Height | Paste height matters for strong connections. |
Insufficient Solder | Too little solder can cause parts to fail later. |
Solder Bridges | Too much solder can connect pads by mistake. |
Irregular Shapes | Uneven paste can lead to bad connections. |
Impact on Functionality | Bad paste can cause failures like short circuits or weak joints. |
Good solder paste application is key to avoiding problems later. This step sets the stage for a strong and reliable circuit board.
Component placement
After the solder paste is applied, parts are placed on the PCB. These parts include resistors, chips, and capacitors. They must be placed exactly right, or the device might not work.
Most factories use machines to place parts. These machines are fast and very accurate. They use software to know where each part should go. Automation makes this step quicker and reduces mistakes. For example, CNC machines drill holes precisely, and AI tools catch errors humans might miss.
Here are tips for better component placement:
Evidence Description | Key Insight |
---|---|
Software improves manual placement and drilling accuracy. | Automation saves time and boosts efficiency in PCB making. |
Design choices can affect quality and output. | Careful design helps avoid problems during production. |
High-speed CNC machines make drilling more precise. | Automated drilling improves accuracy and speeds up work. |
AI finds mistakes that tired workers might miss. | Using AI improves quality checks and speeds up production. |
By following these tips, you can make sure parts are placed correctly. This step is crucial for building devices that work well and last long.
Reflow soldering
Reflow soldering is when the solder paste melts and hardens. This step connects the parts to the PCB permanently. The board goes through a reflow oven, which heats it to the right temperature. The heat melts the paste, bonding the parts to the board.
Temperature control is very important here. If it’s too low, the solder won’t melt properly, causing weak joints. If it’s too high, it can damage the parts or the board. Factories check things like push force to make sure the solder joints are strong.
Here’s data on reflow soldering success rates:
Batch No. | Avg. Push Force (N) | Min. Push Force (N) | Pass Rate |
---|---|---|---|
B2101 | 32.5 | 28.7 | 100% |
B2102 | 34.2 | 30.1 | 100% |
B2112 | 33.8 | 29.5 | 100% |
Reflow soldering is a key step in making reliable electronics. It ensures parts are securely attached to the board. By keeping quality high during this step, you can create durable and high-performing devices.
Inspection and testing
Inspection and testing are very important in the PCBA process. These steps check if the boards work well and meet standards. They also help find problems early, so devices don’t fail later. Think of this as a checkpoint to ensure quality before moving forward.
Common Testing Protocols
Manufacturers use different tests to check how PCBAs perform. Each test has a specific job to make sure the board is strong and works properly. Here’s a simple list of common testing methods:
Testing Protocol | Description | Advantages/Limitations |
---|---|---|
Automated Optical Inspection (AOI) | Finds visible problems without touching the board. | Quick and precise; misses hidden issues. |
Automated X-Ray Inspection (AXI) | Checks inside solder joints for hidden defects. | Great for complex boards; shows detailed images. |
Functional Testing (FCT) | Tests how the board works in real-life situations. | Ensures full functionality; takes time and special tools. |
Environmental and Reliability Testing | Tests how the board handles tough conditions. | Finds weak spots; important for harsh environments. |
In-Circuit Testing (ICT) | Looks for shorts, opens, and checks part placement. | Fast automated testing; needs custom tools. |
Flying Probe Testing | Flexible testing for small batches or prototypes. | No custom tools needed; good for quick checks. |
Extra Quality Checks
To keep quality high, manufacturers can do these things:
Use Statistical Process Control (SPC) to track and improve quality.
Study defects and fix problems quickly.
Always look for ways to make processes better.
Steps for Inspection
Visual Check: Look at parts and solder joints to spot issues.
Size Check: Measure the board to match design rules.
Stress Testing: Test in tough conditions to find weak points.
By using these methods, manufacturers can make sure every PCBA is ready for today’s advanced electronics.
Cleaning and finishing
Cleaning and finishing are the last steps in making circuit boards. These steps remove dirt and prepare the PCBA for long-term use. If cleaning is skipped, leftover materials like dust or flux can cause problems like short circuits.
Why Cleaning Matters
Clean boards work better and last longer. Dirt or residue can cause failures, like broken connections or peeling layers. Cleaning also helps protective coatings stick well. These coatings protect the board from water and rust. Using eco-friendly cleaning methods also helps keep quality high.
Final Touches
After cleaning, a protective layer is added to the board. This coating keeps the PCBA safe from things like moisture and temperature changes. It makes the board stronger and ready for use in many devices, from phones to factory machines.
By focusing on cleaning and finishing, manufacturers can make boards that last longer and work better. These steps are key to creating top-quality products in today’s competitive tech world.
Advantages of PCBA in modern electronics manufacturing
Better efficiency and reliability
PCBA makes electronics more efficient and reliable. It uses advanced tools and careful methods. Many parts are combined on one board, saving time and money.
Placing parts accurately improves how products work.
Strong soldering keeps parts connected and prevents failures.
Finding problems early with FMEA helps things run smoothly.
Using FMEA during PCBA production makes products last longer. It also lowers costs and improves quality. This leads to stronger designs and better market success.
Helping miniaturization and complex designs
PCBA is important for making smaller and smarter devices. New PCB technologies, like HDI and mSAP, allow compact and powerful designs.
HDI PCBs make devices smaller and work better.
Flexible PCBs, made from special materials, allow foldable designs.
Advanced machines create tiny, detailed PCBs for modern gadgets.
These improvements make PCBA perfect for small devices like wearables and IoT tools. Space-saving and performance are key for these products.
Cost savings for large-scale production
PCBA is cost-effective for making many devices at once. Producing in large amounts lowers the cost per unit.
Factor | Explanation |
---|---|
Labor Costs | Skilled workers in places like Southeast Asia lower costs and work quickly. |
Total Cost of Ownership | Knowing all costs helps manage suppliers better. |
Economic Scale | Bigger orders reduce costs by sharing setup expenses. |
Turnkey PCB assembly simplifies production and saves time. Planning for different order sizes can save even more money. This makes PCBA a smart choice for large-scale manufacturing.
Practical considerations for choosing a PCBA supplier
Key factors to evaluate suppliers
Picking the right PCBA supplier is important for your project’s success. Here are key things to check when choosing a supplier:
Technical Capabilities: Check if they can handle tricky PCB designs. Suppliers skilled in multilayer or flexible PCBs can meet different needs.
Quality Assurance: Make sure they follow rules like ISO 9001 and IPC-A-610. These certifications mean they make good products and use reliable methods.
Production Capacity: Ensure they can produce enough and deliver on time.
Cost Transparency: Pick suppliers with clear prices and no hidden costs.
Reputation: Read reviews and case studies to see if they are trustworthy.
Sustainability Practices: Choose suppliers who care about the environment and follow green rules.
Key Factor | What to Look For |
---|---|
Supply Chain Management | Good sourcing of materials and proper inventory control. |
Customer Service | Quick responses and helpful support after sales. |
Geographical Location | Close to your market and skilled in regional needs. |
Importance of certifications and quality assurance
Certifications and quality checks are very important when picking a PCBA supplier. Certifications like ISO9001 and UL show they care about safety and quality. For car-related electronics, ISO16949 ensures they meet special industry rules.
Suppliers should also do regular tests and checks to keep quality high. These include automated optical inspection (AOI) and functional testing to catch problems early. Annual reviews of their systems make them even more reliable.
Certification Standard | What It Means |
---|---|
ISO9001 | Proves strong quality management systems |
UL | Confirms product safety |
SGS | Offers testing and inspection services |
Tip: Always check a supplier’s certifications and testing methods to avoid future issues.
Assessing supplier expertise and capabilities
A supplier’s skills affect how good your PCBA will be. Check their technical knowledge, production ability, and safety standards. Suppliers with skilled engineers can improve designs to save money and make them easier to build.
Look at things like audit results and eco-friendly practices to judge their reliability. Also, see if they can handle big orders and meet tight deadlines. Companies like Jabil Inc. and TTM Technologies are known for their strong skills and services.
Metric | What It Shows |
---|---|
Manufacturing Capacity | Can they make large amounts of PCBA? |
Technical Expertise | Do they know PCB design and assembly well? |
Environmental Compliance | Do they follow eco-friendly rules? |
By focusing on these points, you can find a supplier who fits your technical and business needs.
Knowing what PCBA means shows its importance in making devices work. PCBA changes simple boards into systems that power gadgets like phones and medical tools. Learning how PCBA is made helps you see how each step improves quality and strength.
When picking a PCBA supplier, check their skills, certifications, and ability to produce enough. Good suppliers make high-quality boards, helping your products do well in the market. Spend time reviewing their abilities to choose wisely.
FAQ
What is the difference between SMT and THT in PCBA?
SMT puts parts directly on the board’s surface. THT places parts into drilled holes. SMT is quicker and helps make smaller devices. THT gives stronger connections for tough uses.
How do you ensure PCBA quality during manufacturing?
Factories use machines like AOI and AXI to check boards. Functional tests see if boards work in real life. Certifications like ISO9001 prove good quality. Regular checks and fixing problems make processes better.
Can PCBA be used for flexible electronics?
Yes, PCBA works for flexible electronics. Flexible boards use bendable materials like polyimide. These boards allow foldable designs for wearables and smart devices. PCBA steps adjust for these special materials.
What is turnkey PCB assembly?
Turnkey PCB assembly handles everything from start to finish. It includes buying parts, making boards, and testing them. This method saves time and lowers costs for big orders.
Why is cleaning important in PCBA?
Cleaning removes dirt like flux and dust. Dirt can cause broken connections or rust. Clean boards last longer and let protective layers stick well.
See Also
Essential Technologies Shaping PCBA Production in Today’s Electronics
Benefits and Obstacles of Implementing PCBA in Today’s Devices
Understanding PCB and PCBA: Key Distinctions Explained