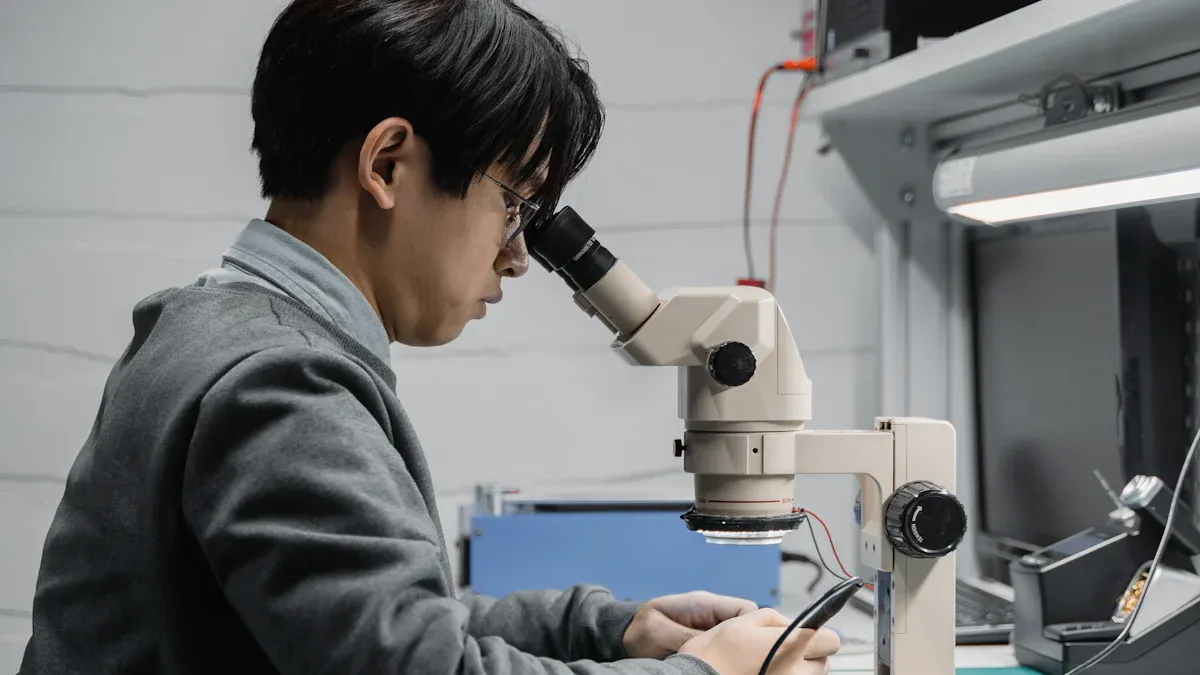
Conformal coating is crucial for keeping circuit boards safe, and our PCBA conformal coating services play a key role in this protection. These coatings shield circuit boards from elements like water, dust, and chemicals. Improved techniques enhance the longevity and performance of electronics. As the demand for more robust and efficient electronics increases, the need for these coatings is on the rise.
The global conformal coatings market was valued at $930.89 million in 2021 and is projected to grow by 5.9% annually until 2030.
By 2037, the market could expand from $1.13 billion in 2024 to $2.59 billion.
Innovative coating methods enhance their effectiveness, allowing for precise application and the use of superior materials. Utilizing our PCBA conformal coating services ensures that your electronics operate efficiently for an extended period.
Key Takeaways
Conformal coatings keep circuit boards safe from water, dust, and chemicals. This helps them last longer and work better.
Picking the right coating, like silicone for heat or urethane for bending, is important for good protection.
Using advanced tools, like robots, makes coating more accurate and faster. This gives better results.
Cleaning surfaces well and curing properly help coatings stick and work better.
Checking often and using quality checks keep coatings strong and prevent problems.
Overview of Conformal Coating Technologies
What is Conformal Coating?
Conformal coating is a protective layer for circuit boards. It keeps them safe from water, dust, chemicals, and temperature changes. Think of it as a shield for electronics. This shield helps devices last longer and work better. Rules like IPC A 610 and IPC-CC-830B set the quality standards. These rules make sure the coating works well for different uses.
Why is Conformal Coating Important?
Conformal coating helps circuit boards stay strong and reliable. It stops corrosion and prevents electrical problems. Some coatings can be very thick, up to 300µm, without breaking under heat. For example, car engine control units are tested with these coatings. They survive 1,000 heat cycles from -40°C to +140°C without cracking. This makes conformal coating very useful for tough jobs.
Types of Conformal Coating Materials
There are different materials used for conformal coatings. Each has special features. Here’s a table showing the common types:
Type | Features |
---|---|
Acrylic | Protects from water, easy to use, cheap, but weak to heat and solvents. |
Epoxy | Strong against chemicals and scratches, but can crack in heat. |
Urethane | Resists water and solvents, flexible, good for changing temperatures. |
Silicone | Works well in high heat, flexible, resists water, but costs more. |
Parylene | Covers evenly, great for water and chemical protection, best for important uses, expensive. |
Acrylic is cheap and easy to use, while silicone works in hot places. Parylene costs more but gives the best protection. Picking the right material helps your circuit boards last longer and work better.
Advanced Techniques in Conformal Coating
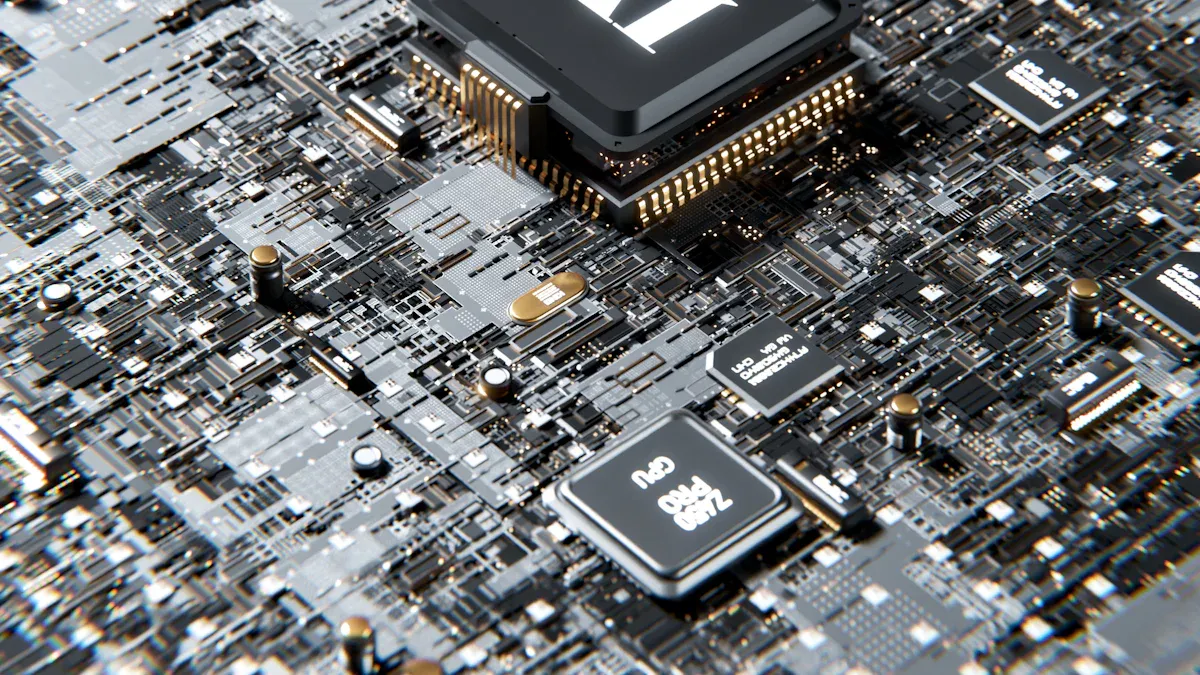
Precision Application Methods
Applying conformal coating carefully gives better protection to PCBA. Using proper methods improves the coating’s evenness and quality. For example, dip coating is a common way to apply it. This method needs clean surfaces, clean solutions, correct soaking time, and steady withdrawal speed. These steps help create a smooth and even layer for strong protection.
Special machines, like Baron Blakeslee Coating Systems, make application more precise. These machines are great for medical devices needing exact coatings. The Lab-Koat Series Coater mixes the solution well and saves fluid. Using these tools gives consistent results and helps electronics last longer.
Robotic and Automated Coating Systems
Robots have changed how conformal coating is done. They work with great accuracy and speed. Robots copy human movements but do it more precisely. They coat complex shapes evenly, which is important for advanced electronics.
In factories, automated systems save time and improve safety. They coat more items faster and keep workers safe from harmful chemicals. These systems are small, easy to program, and reduce waste. Robots also use less energy, making them eco-friendly. Adding robots improves both speed and quality in coating processes.
Emerging Materials in Advanced Coating Solutions
New materials are making conformal coatings better. Thin-film coatings with low surface energy work very well. They lower surface tension to below 25 dynes/cm². This makes them resist dirt and buildup. For example, they create smooth, water-repelling surfaces on metal tubes.
A Texas refinery showed how these coatings help. Coated tubes had 9% better flow rates than uncoated ones. Even after cleaning, coated tubes kept a 50% higher water flow. These new materials make electronics stronger and more efficient. Using them can help you stay ahead in the market.
Industry Applications of PCBA Conformal Coating Services
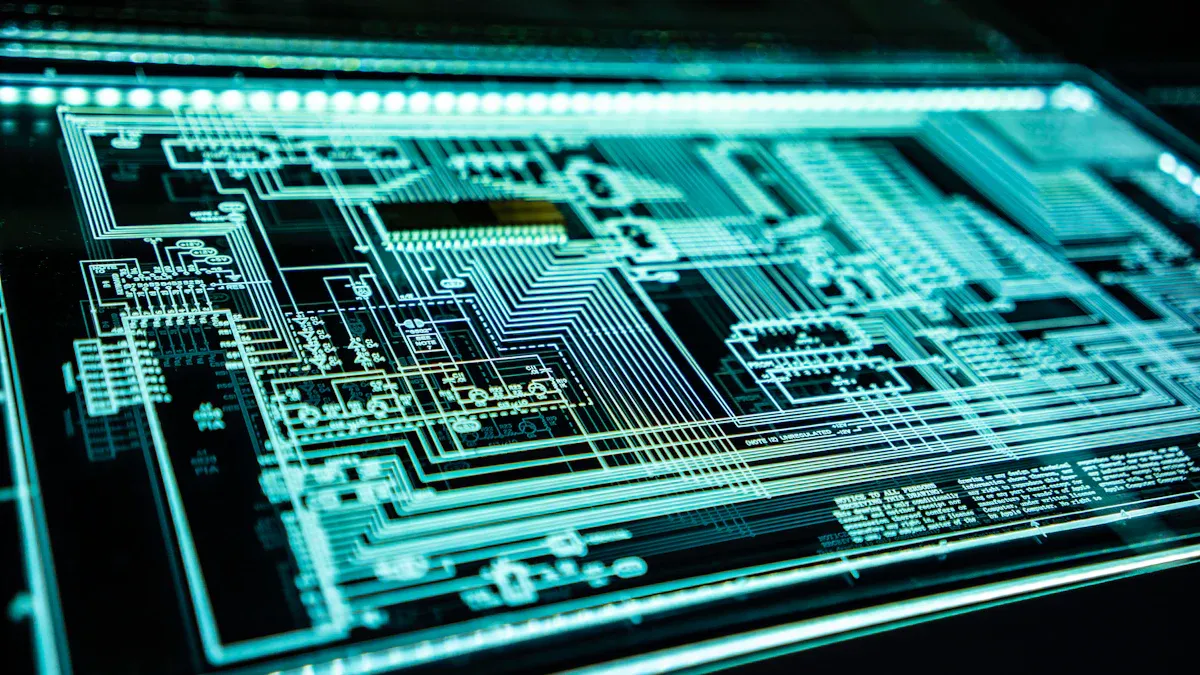
Medical Devices: Keeping Electronics Safe and Reliable
Conformal coating is important for making medical devices work well. These devices often face moisture, dust, and dirt that can cause problems. Adding conformal coatings helps protect electronics in tools like pacemakers and ventilators. These coatings stop corrosion and provide insulation, keeping devices working longer.
Strict rules ensure coatings meet safety standards. For example, IPC-A-610 checks for protection from dirt, and UL 746E tests resistance to water. Below is a table of key standards for medical device coatings:
Standard Type | Description |
---|---|
IPC Standards | IPC-A-610 sets rules for electronic assembly quality. |
UL Standards | UL 746E tests water and humidity resistance in materials. |
ASTM Standards | ASTM D7866 checks how coatings resist water. |
Military Standards | MIL-PRF-55342 ensures waterproofing for military use. |
IEC Standards | IEC 61086 focuses on moisture protection for circuit boards. |
Following these rules makes medical devices safer and more reliable. This helps protect patients and ensures devices work when needed.
EV Charging Stations: Protecting Electronics Outdoors
EV charging stations face tough weather like heat, rain, and chemicals. Conformal coatings protect the electronics inside these stations. They stop corrosion and make sure the systems last longer.
Tests show how well coatings work in EV stations. For example, Parylene coatings block water and salt damage. The table below shows test results:
Test Type | Requirement | Result |
---|---|---|
Operations Test | Work for 24 hours at 23°C | Worked perfectly for 24 hours |
Coating Property | No gaps or thin spots | Coating thickness 225±3 μm achieved |
Electrical Test | Voltage >1.5 kV | Insulation resistance >10 GΩ |
Corrosion Test | Salt spray (35°C, 96 hours) | No rust on chip parts |
Protection Against Water | Compare coatings | Parylene: Best water protection |
Salt/Chemical Protection | Compare coatings | Parylene: High salt/chemical resistance |
Durability | Compare coatings | Parylene: Very durable |
Using conformal coatings in EV stations improves their strength and performance. This helps them work well in bad weather, supporting eco-friendly transportation.
Harsh Environments: Protecting Electronics in Tough Conditions
Electronics in cars, planes, and gadgets often face extreme conditions. Conformal coatings protect them from water, dust, chemicals, and heat. These coatings stop corrosion and short circuits, making devices more reliable.
Different coatings work best in certain conditions. Silicone coatings handle heat and chemicals, so they’re great for cars and planes. Urethane coatings are flexible and resist water, making them good for changing temperatures. These coatings help devices last longer, even in tough places.
Benefits of conformal coatings in harsh conditions:
Block water and dust
Stop corrosion
Improve insulation
Make devices last longer
Choosing the right coating and method keeps electronics safe in extreme environments. This boosts performance and lowers repair costs.
Addressing Challenges in Conformal Coating Technologies
Common Application Issues and Their Solutions
Conformal coating can face problems that affect its protection. Issues like bubbles, uneven layers, or mistakes in applying can happen. These problems reduce the coating’s ability to protect. Small parts or tiny PCBs make applying the coating harder. Cracks, ripples, or peeling may occur from bad methods or weather.
To fix these problems, follow a good application plan. If too much coating or low thickness causes flow issues, clean the board well and use solvent coatings. Cracks and ripples can be stopped by using the right thickness and drying longer. Uneven layers or residue can cause dewetting, so clean the surface first. For bubbles or holes, use thinner coatings and apply in light layers. These tips help create smooth and strong coatings.
Best Practices for Surface Preparation and Curing
Cleaning the surface is key for good coatings. Dirt, grease, or wax can cause problems. Use cleaning methods like solvents, water-based cleaners, or plasma cleaning to remove them. This helps the coating stick better.
Curing is also very important. The curing type—heat, moisture, UV light, or air drying—depends on the coating and thickness. UV curing works fast, while heat curing is better for thick coatings. Check for problems during curing with UV lights or special inspection tools. These steps make coatings last longer and work better.
Quality Assurance in Advanced Coating Processes
Keeping quality high is very important in coating. Buy materials from trusted suppliers and check them when they arrive. Watch temperature and humidity because they affect the coating. Use HVAC systems to keep conditions steady.
Take care of tools like spray guns and mixers. Fix and check them often. Train workers to spot problems with tools and do regular checks. Test things like thickness and viscosity to avoid mistakes. These steps ensure the coating is strong and reliable.
By solving problems and using good methods, you can make coatings that last and meet industry needs.
Using advanced conformal coating techniques makes electronics work better and last longer. These methods apply coatings carefully, protect devices from damage, and help them stay reliable. Below is a table showing the good and bad sides of these techniques:
Advantages | Challenges |
---|---|
Accurate and even coating | Costs a lot to maintain |
Simple to use | Uses more energy and is noisy |
Can be adjusted easily | Hard to learn software |
Might fail sometimes |
Examples show how these coatings help over time:
Tests prove silicone coatings work well in wet places. They stop leaks and stay strong.
Heat tests show polyurethane coatings make devices more reliable. They lower failure rates compared to no coating.
Using advanced coatings keeps electronics safe in tough conditions. Try these methods to make your devices stronger and last longer.
FAQ
What is the best conformal coating material for high-temperature environments?
Silicone works best in very hot conditions. It stays strong and flexible even in extreme heat. This makes it perfect for use in cars and airplanes.
Tip: Always check how much heat the coating can handle before using it on your PCBA.
How do you ensure proper adhesion of conformal coatings?
Clean the surface well before applying the coating. Use cleaners like solvents, water-based solutions, or plasma cleaning to remove dirt and grease. A clean surface helps the coating stick better and protect more.
Note: If the surface isn’t cleaned properly, the coating may peel or look uneven.
Can conformal coatings be repaired or removed?
Yes, you can fix or take off conformal coatings. Use tools like solvents, sanding, or special removal equipment based on the coating type. Acrylic coatings are the easiest to remove, but Parylene needs advanced methods.
Reminder: Always follow safety rules when using solvents or removal tools.
How do robotic systems improve conformal coating processes?
Robots make coating more accurate and consistent. They apply coatings evenly, even on tricky shapes, and reduce mistakes. This leads to better coatings and faster work.
Emoji Insight: 🤖 Robots also keep workers safe by reducing contact with harmful chemicals.
What are the common inspection methods for conformal coatings?
Check coatings using UV lights, thickness tools, and visual inspections. These methods help find problems like bubbles, uneven spots, or areas without coating.
Inspection Method | Purpose |
---|---|
UV Light | Finds where coating is applied |
Thickness Tools | Checks if coating is even |
Visual Checks | Spots surface problems |
Pro Tip: Regular checks help prevent failures and improve quality.
See Also
Excelling in PCBA Production Methods for Superior Quality
Ensuring Quality in PCBA Production: Comprehensive Process Oversight
Advanced Soldering Methods for Contemporary PCB Assembly