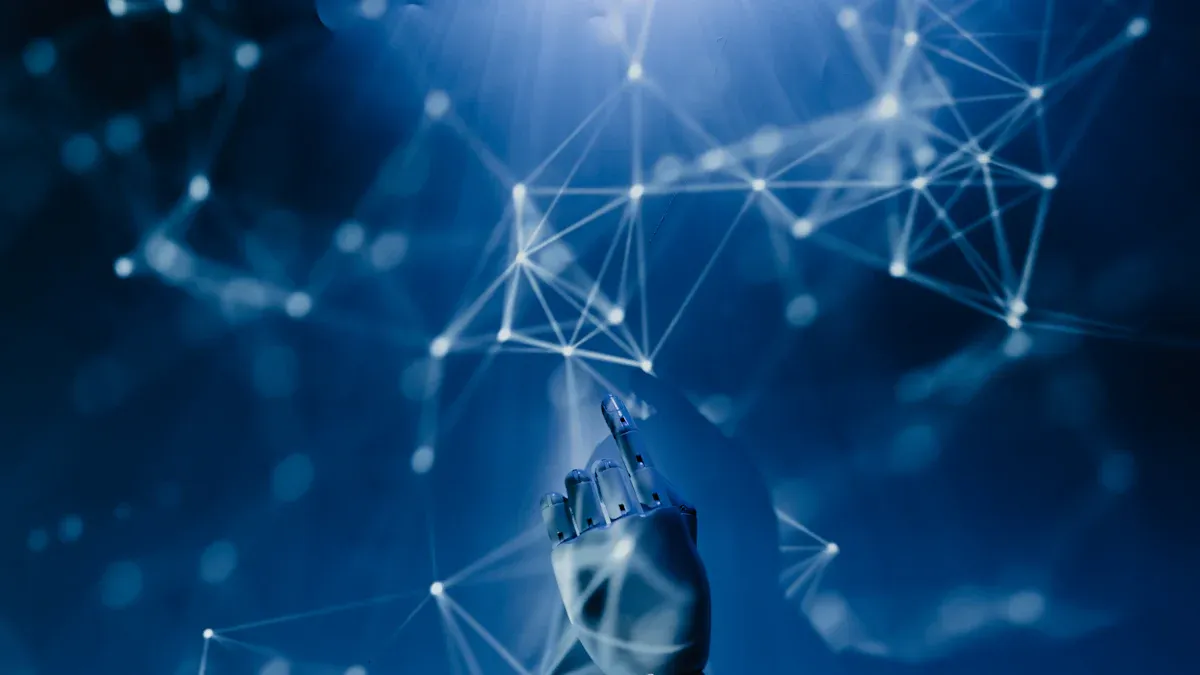
Artificial intelligence is reshaping how you approach printed circuit board assembly. By leveraging AI, you can achieve unparalleled efficiency in manufacturing processes. It reduces production flaws, optimizes workflows, and minimizes waste. For instance, AI-driven defect detection replaces traditional inspection methods, ensuring higher accuracy and fewer errors. Predictive maintenance models also help you avoid unexpected machine downtimes, enhancing operational reliability. While the initial investment in robotics and AI may seem high, its long-term benefits include reduced labor costs and improved profitability. The rise of Smart Factory PCB Assembly highlights how artificial intelligence in PCB assembly is making production smarter and faster.
Key Takeaways
AI makes PCB assembly faster by handling repetitive tasks. This speeds up production and lowers mistakes.
AI watches processes in real-time, giving quick feedback and fixes. This keeps quality steady and reduces waste.
AI predicts machine problems early, stopping breakdowns before they happen. This saves time and repair money.
AI finds defects better, so only good parts are used. This makes products more reliable.
Using AI in PCB design speeds up prototyping and improves layouts. This helps launch products quicker.
Efficiency and Process Optimization in Smart Factory PCB Assembly
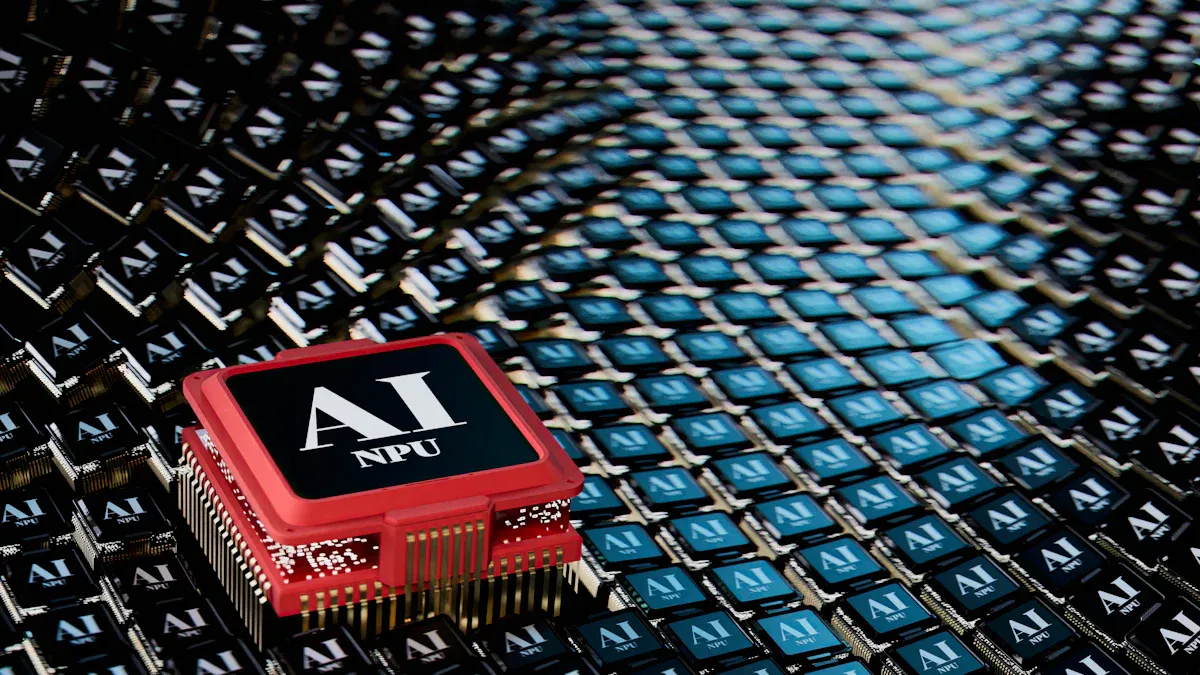
Streamlining workflows with AI-driven automation
AI is transforming how you manage workflows in smart factory PCB assembly. By automating repetitive tasks, you can achieve faster production cycles and reduce errors. AI-driven routing algorithms optimize the placement of components, ensuring precision and saving time. For example, Company A streamlined its production process with advanced automation, leading to faster time-to-market and lower manufacturing costs. Similarly, Company B enhanced quality control with AI-powered inspection systems, improving customer satisfaction through higher-quality PCBAs.
The benefits of workflow automation extend beyond speed. AI enables you to identify bottlenecks and adjust processes in real time. This adaptability ensures that your production line operates at peak efficiency, even when faced with unexpected challenges.
Case Study | Results |
---|---|
Automotive Electronics Reliability Enhancement | 70% improvement in design compliance, 55% faster issue identification |
High-Speed Communication Board Optimization | 45% reduction in design cycle time, 30% better signal integrity |
Consumer Electronics Miniaturization | 60% faster component placement, 35% reduction in board area |
Real-time monitoring for process optimization
Real-time monitoring plays a crucial role in smart manufacturing. It provides detailed data on machine performance, parameters, and activities. This allows you to quickly identify and correct process issues, ensuring consistent quality. For instance, real-time monitoring systems offer immediate feedback to the manufacturing execution system (MES), enabling you to make data-driven decisions.
By integrating machine learning and AI technologies, you can automate learning and decision-making processes. This further enhances process optimization, helping you maintain efficiency and reduce waste. Monitoring also ensures that your equipment operates within optimal parameters, extending its lifespan and minimizing downtime.
Reducing production time and improving throughput
AI helps you reduce production time and boost throughput by optimizing every stage of the PCB assembly process. Intelligent design optimization allows you to analyze vast datasets, reducing design time and improving manufacturability. Predictive maintenance systems forecast equipment failures, cutting unplanned downtime by up to 70%.
Automated quality control systems detect defects with high accuracy, improving yields and reducing scrap rates. Additionally, AI enables supply chain synchronization, predicting raw material demand and optimizing inventory management. These advancements ensure that your production line operates smoothly, delivering high-quality products faster and more efficiently.
Quality Improvement through Artificial Intelligence in PCB Assembly
AI-powered defect detection and quality control
AI has revolutionized defect detection in printed circuit board assembly. Traditional inspection methods often miss subtle flaws, but AI-based optical inspection systems excel at identifying even the smallest defects. These systems use high-resolution imaging and machine learning to analyze components during assembly. They verify the presence and type of each part, ensuring the correct components are used. This level of precision helps you cut down on errors and maintain consistent quality.
Automated inspection processes powered by AI also enhance counterfeit component detection. By analyzing patterns and materials, AI can identify counterfeit parts before they enter the production line. This ensures that only authentic components are used, safeguarding the reliability of your products. With AI, you can achieve higher accuracy in defect detection, reducing the risk of faulty PCBs reaching your customers.
Minimizing human error in inspection processes
Human inspection, while valuable, is prone to errors due to fatigue or oversight. AI for PCBA inspection eliminates these challenges by automating the process. AI-based systems work tirelessly, scanning every detail of the printed circuit board with unmatched precision. They identify potential issues, such as defect component detection, before they escalate into larger problems.
By relying on AI, you can reduce dependency on manual labor for inspection tasks. This not only minimizes human error but also speeds up the inspection process. AI-driven systems provide consistent results, ensuring that every PCB meets the required standards. This consistency builds trust in your manufacturing process and improves overall product quality.
Enhancing precision in component placement
AI plays a crucial role in enhancing precision during component placement. It fills in missing information about PCB layouts, improving the understanding of circuit functionalities. Machine learning and thermal imaging work together to identify potential defects with high precision, ensuring that components are placed accurately.
AI also supports automated inspection by verifying component placement during assembly. High-resolution imaging systems analyze the board in real time, ensuring that each part is correctly positioned. This reduces the likelihood of errors and improves the overall accuracy of the assembly process. With AI, you can achieve a higher level of precision, resulting in reliable and high-performing printed circuit boards.
Cost Reduction with Predictive Maintenance and Optimization
Identifying equipment issues before failures
AI in manufacturing helps you identify equipment issues before they escalate into costly failures. By analyzing machine data in real time, AI systems detect early signs of wear or malfunction. For example, smart sensors monitor equipment performance and pinpoint error-prone areas. This proactive approach ensures that potential problems are addressed before they disrupt production.
Evidence Description | Impact on Effectiveness |
---|---|
AI-assisted predictive maintenance reduces downtimes in the assembly line. | This helps avoid impending losses by identifying issues before they lead to failures. |
Smart sensors capture data from machines to identify error-prone areas. | This proactive approach enhances the reliability of the production process. |
AI-based optical inspection improves speed and accuracy in defect identification. | This supports proactive maintenance strategies by ensuring defects are caught early. |
By leveraging AI, you can maintain consistent production quality while avoiding unexpected breakdowns. This not only saves time but also reduces repair costs significantly.
Reducing downtime and repair costs
AI-driven predictive maintenance minimizes downtime by optimizing maintenance schedules. Instead of waiting for equipment to fail, you can rely on AI to forecast when maintenance is needed. This approach reduces unplanned downtime by up to 50%, ensuring your production line operates smoothly.
Predictive maintenance reduces unexpected breakdowns, leading to lower repair or replacement costs.
Effective scheduling of maintenance optimizes the use of maintenance personnel, contributing to overall cost savings.
Monitoring equipment performance allows for early detection of issues, minimizing downtime and maintaining production quality.
By reducing repair costs and improving operational efficiency, AI in manufacturing helps you achieve significant cost savings.
Extending equipment lifespan and minimizing waste
AI extends the lifespan of your equipment by identifying early signs of wear and enabling timely maintenance. This proactive strategy prevents equipment failures and reduces the need for frequent replacements. For instance, a global electronics manufacturer used digital twins to enhance its PCB assembly line. This resulted in a 20% reduction in cycle time and a 15% decrease in material waste.
Predictive maintenance also minimizes waste by improving process control. AI identifies overuse of materials or frequent rework, allowing you to make targeted improvements. This not only lowers production costs but also supports sustainable manufacturing practices.
Predictive maintenance can reduce system downtime by 30-50%.
It can extend the lifespan of machinery by 20-40%.
By integrating AI into your operations, you can achieve long-term cost savings while maintaining high-quality production standards.
Innovation in PCB Design and Manufacturing
AI-assisted design optimization for complex layouts
AI has revolutionized the way you approach complex PCB layouts. By automating component placement, AI ensures optimal positioning to reduce electromagnetic interference and improve signal integrity. It also enhances routing and trace optimization, minimizing signal crosstalk and ensuring proper impedance matching. These advancements lead to better performance and reliability in your designs.
AI tools validate designs against predefined rules, reducing errors and costly redesigns. For example, machine learning algorithms simulate electrical and thermal performance, identifying potential issues before prototyping. This proactive approach saves time and resources while improving the overall quality of your PCB layouts.
Innovative Trend | Description |
---|---|
Automated Component Placement | AI suggests optimal placement to reduce electromagnetic interference and improve signal integrity. |
Design Optimization | AI enhances layout efficiency, ensuring better use of board space while maintaining performance. |
Thermal Management | Algorithms predict overheating issues and optimize heat dissipation paths. |
Routing Automation | AI evaluates multiple paths for efficient signal transmission layouts. |
Accelerating prototyping and production cycles
AI accelerates prototyping by enabling rapid design iterations. Machine learning generates and evaluates multiple prototypes quickly, reducing the time needed for testing and refinement. For instance, AMD uses AI-driven tools to create high-performance PCBs faster than traditional methods.
Failure prediction is another key benefit. AI identifies potential issues in prototypes, minimizing the number of iterations required. This reduces production time and ensures that your designs are ready for manufacturing sooner. By streamlining these processes, AI helps you bring products to market faster and more efficiently.
Evidence Type | Description |
---|---|
Rapid Design Iterations | Machine learning enables the generation and evaluation of multiple prototypes quickly. |
Failure Prediction | AI can foresee potential issues in prototypes, minimizing the number of iterations needed. |
Example | AMD employs AI-driven prototyping tools to speed up the creation of high-performance PCBs. |
Enabling innovative manufacturing techniques
AI enables you to adopt cutting-edge manufacturing techniques that improve efficiency and quality. For example, Jabil uses deep learning-based machine vision systems for real-time quality control. This technology detects even the smallest defects, reducing costs associated with rework and scrap.
Predictive equipment maintenance is another innovation powered by AI. By analyzing machine data, AI minimizes unplanned downtime and increases production efficiency. Additionally, AI optimizes pick-and-place machine configurations, reducing cycle times and improving assembly accuracy. These advancements, combined with ai-assisted soldering machines, ensure that your manufacturing processes remain competitive and reliable.
Company: Jabil
Technique: Deep Learning-based machine vision systems for real-time quality control.
Outcome: Detection of minimal defects, reducing costs associated with rework and scrap.
Technique: Optimization of pick-and-place machine configurations.
Outcome: Reduced cycle times and improved assembly accuracy.
By integrating AI into your manufacturing processes, you can achieve higher efficiency, better quality, and lower costs.
Enhanced Fault Diagnosis and Rework Assistance
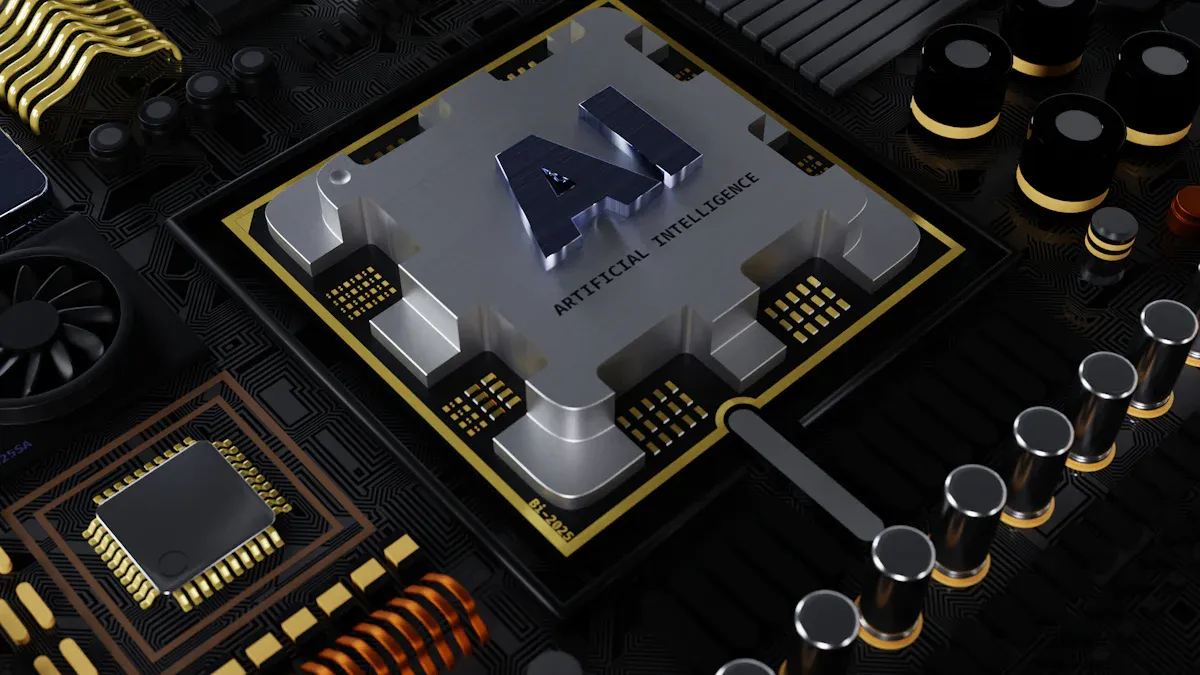
AI tools for pinpointing faults in defective PCBs
AI tools have transformed fault diagnosis in PCB assembly. These tools use advanced technologies like 3D convolutional neural networks (3D CNN) and automated optical inspection (AOI) systems to detect defects with remarkable accuracy. For example, 3D CNN simulates changes in glue drops on substrates, achieving high precision in identifying faults. AOI systems, on the other hand, excel at detecting various defects, improving accuracy by 3.2% overall and 5.6% for spur-defect classes.
Method | Description | Improvement |
---|---|---|
3D CNN | Simulates changes in glue drops on substrates | Achieved high accuracy in defect detection |
AOI Systems | Detects various defects using optical inspection | Improved accuracy by 3.2% overall, 5.6% for spur-defect class |
By leveraging these tools, you can quickly identify and address issues, ensuring that defective PCBs are repaired before they impact production quality.
Automating rework processes for faster repairs
AI-driven automation simplifies rework processes, making repairs faster and more efficient. Instead of relying on manual troubleshooting, AI systems analyze data to pinpoint the root cause of defects. This allows you to focus on targeted repairs, reducing the time spent on trial-and-error methods.
For instance, AI-powered systems provide real-time feedback and guidance during rework. This ensures that workers perform tasks correctly the first time, minimizing errors. By automating repetitive tasks, you can streamline the rework process and maintain consistent quality across all repairs.
Improving yield and reducing material waste
AI enhances yield by identifying inefficiencies and suggesting improvements in the assembly process. Tools like the Assembly Copilot and Kaizen Copilot play a significant role in this area.
The Assembly Copilot improves first pass yield (FPY) by offering real-time feedback and guidance.
It collects and analyzes data to identify inefficiencies, enabling targeted process improvements.
The Kaizen Copilot automates time studies, allowing for quicker adjustments to enhance FPY.
Failure Mode and Effects Analysis (FMEA) identifies potential failures and their causes, aiding in root cause analysis for low FPY.
By improving yield, you can reduce material waste and lower production costs. These advancements not only enhance efficiency but also support sustainable manufacturing practices.
AI is revolutionizing PCB assembly by delivering unmatched benefits in efficiency, quality, and innovation. It reduces costs by automating design processes and minimizing rework. AI also enhances adaptability, suggesting innovative designs and optimizing performance. Predictive analysis helps you address potential issues early, ensuring better outcomes.
By integrating AI, you can future-proof your operations and stay competitive in a fast-changing industry.
Benefit/Advantage | Description |
---|---|
Cost Reduction | Automating design processes reduces labor costs and rework. |
Design Innovation and Adaptability | AI suggests innovative designs and adapts quickly to changes. |
Predictive Analysis | AI predicts issues, enabling proactive optimizations for better performance. |
Enhanced Human Capabilities | AI boosts productivity and improves product quality. |
FAQ
What is PCBA, and why is it important?
PCBA stands for Printed Circuit Board Assembly. It involves mounting electronic components onto a PCB to create functional circuits. PCBA is crucial because it forms the backbone of modern electronic devices, ensuring they operate efficiently and reliably.
How does AI improve PCBA processes?
AI enhances PCBA by automating tasks like defect detection, component placement, and quality control. It reduces errors, speeds up production, and optimizes workflows. AI also enables predictive maintenance, ensuring equipment operates efficiently and minimizing downtime.
Can AI reduce costs in PCBA manufacturing?
Yes, AI reduces costs by improving efficiency and minimizing waste. Predictive maintenance prevents expensive equipment failures. Automated processes lower labor costs and reduce material waste. These savings make PCBA manufacturing more cost-effective and sustainable.
What role does AI play in PCBA quality control?
AI ensures high-quality PCBA by identifying defects with precision. Automated optical inspection systems detect flaws that human inspectors might miss. AI also minimizes human error, ensuring consistent quality across all assembled boards.
Is AI suitable for small-scale PCBA manufacturers?
AI benefits manufacturers of all sizes. Small-scale PCBA operations can use AI tools for design optimization, defect detection, and process automation. These tools improve efficiency and product quality, helping smaller manufacturers compete in the market.
See Also
Discover AI’s Role in Improving PCBA for Electronics
Exploring AI Innovations in RSJPCBA Design and Production
The Impact of PCBA on Efficiency in Automation Systems
Understanding Automotive PCBA Assembly’s Importance for 2025
The Significance of AS9100 Certified PCB Assembly in Aerospace