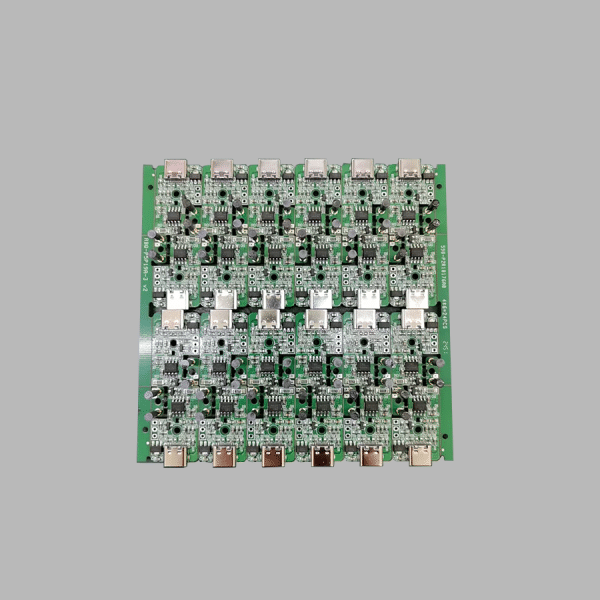
Soldering is very important in the lead-free PCBA manufacturing process for making circuit boards (PCBA). It connects parts both electrically and physically. There are two main soldering types: lead-based and lead-free. Knowing how they differ helps you choose wisely. Lead solder melts at a lower temperature (361°F) than lead-free solder (about 422°F). This difference affects how heat is handled during production. Lead-free solder often uses metals like tin, copper, and silver, which are safer for workers and the environment. These differences also affect how strong, long-lasting, and legal the boards are.
Key Takeaways
Lead-based solder melts at lower heat, making it simple to use. However, it can harm health because of lead exposure.
Lead-free solder is safer for people and nature. It uses metals like tin and copper but needs higher heat to work.
Picking the right solder depends on your product’s needs. Think about strength, heat resistance, and environmental rules.
Using lead-free solder can save money over time. It avoids fines and health problems, even though it costs more at first.
Keep up with industry changes and rules. This helps your manufacturing stay safe and eco-friendly.
Overview of Lead-Based and Lead-Free Solder
Characteristics of Lead-Based Solder
Lead-based solder has been used for many years in PCBA. It is made from a mix of tin and lead, often 63% tin and 37% lead. This type of solder melts at a low temperature of 361°F. This makes it easier to use during production. It spreads well, creating smooth and strong connections between parts. It is also tough and handles heat changes well, making it good for durable products.
But, lead-based solder can be harmful. Lead is poisonous and can hurt workers or pollute the environment if not managed safely. Because of these dangers, stricter rules now limit its use, pushing companies to find safer options.
Characteristics of Lead-Free Solder
Lead-free solder was created to solve the problems of lead-based solder. It uses metals like tin, silver, and copper instead of lead. This solder melts at a higher temperature, about 422°F. It is strong and reliable in many situations. Its performance can depend on things like joint shape and surface materials. For example, tests show that lead-free solder joints handle stress differently than lead-based ones.
Lead-free solder is safer for people and the planet. It lowers health risks for workers and reduces pollution. Many manufacturers now use it to follow global rules and protect the environment.
Transition to Lead-Free Manufacturing in the Industry
Switching to lead-free manufacturing has grown popular in recent years. Companies selling worldwide often choose lead-free methods to meet strict rules. Trade groups have helped spread awareness about these requirements. Small and medium businesses are also using lead-free solder, seeing its long-term benefits despite early challenges. This shift shows the industry’s focus on safety and protecting the environment.
Key Differences in the Manufacturing Process
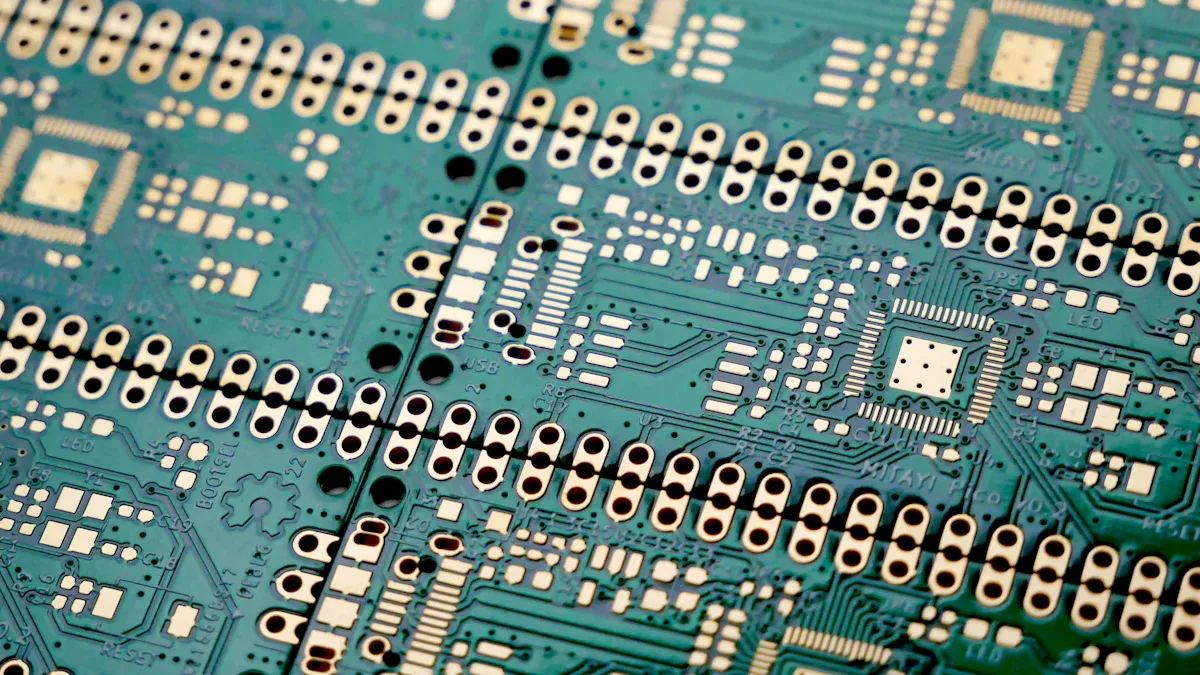
Composition and Alloy Materials
Solder makeup is very important in soldering. Lead-based solder is a mix of tin and lead. A common ratio is 63% tin and 37% lead (Sn63Pb37). This mix melts easily and conducts electricity well. Other types, like Sn62 (62% tin, 36% lead), are used for special needs.
Lead-free solder has no lead at all. It uses safer metals like tin-copper (SnCu) or tin-silver-copper (SAC). These are better for workers and the planet. But they need changes in how they are used because they act differently.
Here’s a table comparing solder types:
Alloy Composition | Lead Percentage | Tin Percentage | Conductivity (IACS Score) |
---|---|---|---|
15/85 Lead-Tin Alloy | 15% | 85% | 8.5% |
20/80 Lead-Tin Alloy | 20% | 80% | 8.7% |
Sn62 (62% Tin, 36% Lead) | 36% | 62% | 11.9% |
Sn63 (63% Tin, 35% Lead) | 35% | 63% | 11.5% |
80/20 Gold-Tin Alloy | 20% | 80% | 14.51% |
88% Gold, 12% Germanium | 12% | 88% | 14.67% |
82% Gold, 18% Indium | 18% | 82% | 14.9% |
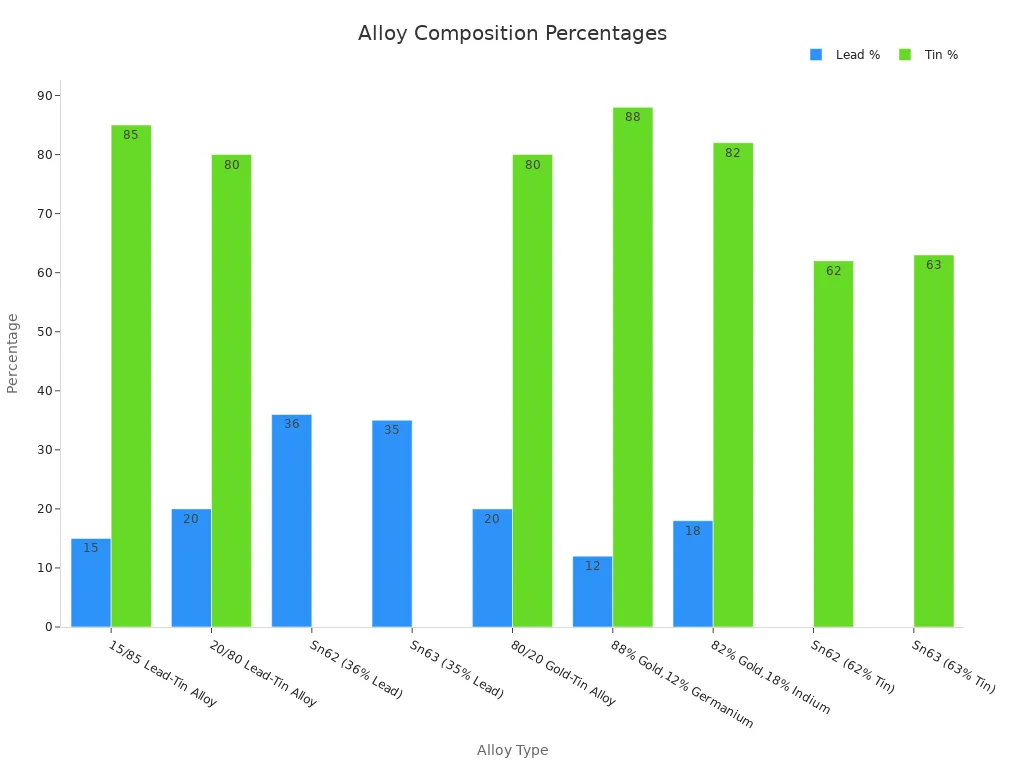
When picking solder, think about your PCBA needs. Lead-free solder needs careful handling because of its special traits.
Melting Point and Thermal Requirements
The melting point affects how solder works. Lead-based solder, like Sn63Pb37, melts at 183°C. This low temperature makes it easy to use. It also lowers heat stress on parts. Tin-lead solder melts between 179°C and 188°C, giving flexibility.
Lead-free solder melts at higher temperatures, often over 217°C. This means hotter tools are needed, which can stress parts more. For example:
Lead solder (Sn63Pb37): Melts at 183°C.
Lead-free solder: Melts above 215°C.
Hotter temperatures in lead-free soldering can cause problems. Parts might get damaged, or defects could happen. Careful heat control is needed for good results.
Wettability and Oxidation Behavior
Wettability shows how well solder sticks to surfaces. Lead-based solder spreads well and makes smooth joints. This makes it easy to create strong connections.
Lead-free solder doesn’t spread as well. It can make uneven joints, which might not last long. It also oxidizes more because of its high melting point. Oxidation blocks bonding and can cause defects.
To fix this, use fluxes made for lead-free solder. These fluxes stop oxidation and help solder stick better. This improves lead-free PCBA manufacturing results.
Mechanical and Physical Properties
When comparing lead-based and lead-free solder, their physical traits are important. These traits affect how solder works under pressure and its durability. They also decide which solder fits certain uses.
Key Property Comparisons
For years, lead-based solder was the top choice because it’s reliable. But now, lead-free solder is popular as a safer option. Here’s a table showing their key differences:
Parameters | Leaded Solder | Lead-Free Solder | Units |
---|---|---|---|
Melting Point | 183 | 218 | °C |
Density | 8.5 | 7.44 | g/cm³ |
Resistivity | 15 | 11 | MΩ-cm |
Electrical Conductivity | 11.5 | 15.6 | IACS |
Thermal Conductivity | 50 | 73 | W/m·1k·1s |
TCE (Thermal Expansion) | 23.9 | 21.4 | micrometers / M / ºC |
Fatigue Life | 3 | 1 | |
Surface Tension | 481 | 548 | mN/m |
Shear Strength | 23 | 27 | MPa |
What These Properties Mean for You
Melting Point: Lead-free solder melts at higher temperatures. This uses more energy and stresses parts. Make sure your tools can handle the heat.
Density: Lead-free solder is lighter than lead-based solder. You’ll need more of it to fill the same space.
Electrical and Thermal Conductivity: Lead-free solder conducts heat and electricity better. It’s great for products needing good heat flow and electrical performance.
Fatigue Life: Lead-based solder lasts longer under repeated stress. It’s better for products facing constant movement or pressure.
Shear Strength: Lead-free solder is stronger against breaking. It’s ideal for products needing tough connections.
Tip: Pick solder based on your product’s needs. For example, if your product gets very hot, lead-free solder may work better due to its heat-handling ability.
Challenges with Lead-Free Solder
Lead-free solder has higher surface tension, making smooth joints harder. You might need to adjust your process or use special fluxes. Its shorter fatigue life means it’s less suited for products facing vibrations or temperature changes.
By knowing these traits, you can choose the right solder for your goals.
Performance Comparison in Lead-Free vs Lead-Based PCBA Manufacturing Process
Reliability and Strength of Solder Joints
How strong and reliable solder joints are is very important. These joints affect how well a PCBA works. Lead-based solder has been popular because it makes strong, lasting joints. Its low melting point helps it spread easily. This creates smooth and even connections. It’s great for things like medical devices and airplanes that need high reliability.
Lead-free solder has gotten better over time. Alloys like SAC305 (tin-silver-copper) are often used. They are strong but can break more easily under stress. Tests show SAC305 joints don’t last as long as lead-based ones when stressed. Studies using Weibull distribution also show lead-based solder performs better in hot conditions.
Tip: If your product faces tough conditions, think about the solder’s strength. Lead-based solder might work better, but lead-free solder is improving with new alloys.
Longevity and Durability
How long solder joints last depends on how well they handle stress. Lead-based solder is known to stay strong over time. It resists damage from temperature changes and vibrations. This makes it good for products that face these challenges often.
Lead-free solder is safer for the environment but has durability issues. Its higher melting point can add stress during soldering. This might shorten the joint’s life. However, newer lead-free alloys, like SAC-Q, are better at lasting longer. These improvements make them useful for more products.
When picking solder, think about where your product will be used. Lead-free solder works well in gadgets but may not last as long as lead-based solder in cars or airplanes.
Common Defects in Lead-Free Soldering vs Lead-Based Soldering
Problems during soldering can hurt a PCBA’s quality. Lead-based solder is easier to use and has fewer defects. It spreads well, reducing problems like voids or weak joints. It also resists oxidation, which helps avoid defects.
Lead-free soldering has its own challenges. Its higher melting point can harm parts and cause oxidation. This can lead to uneven joints or brittle breaks. Common issues include tin whiskers and voids. But better fluxes and improved processes have lowered these problems in lead-free soldering.
Here’s a table comparing issues and defect rates:
Solder Type | Reliability Issues | Defect Rates Comparison |
---|---|---|
Lead-Free Solder | Struggles in tough environments | Reliable in most cases, but less certain for critical uses |
Lead-Based Solder | Fewer tin whisker problems | More reliable, especially for space or medical devices |
To make lead-free soldering better, use strict controls and advanced tools. This helps manage heat and lowers defect chances.
Note: Lead-free soldering needs more care but follows environmental rules. It’s also safer for workers and nature.
Environmental and Health Impacts of Lead-Free Soldering
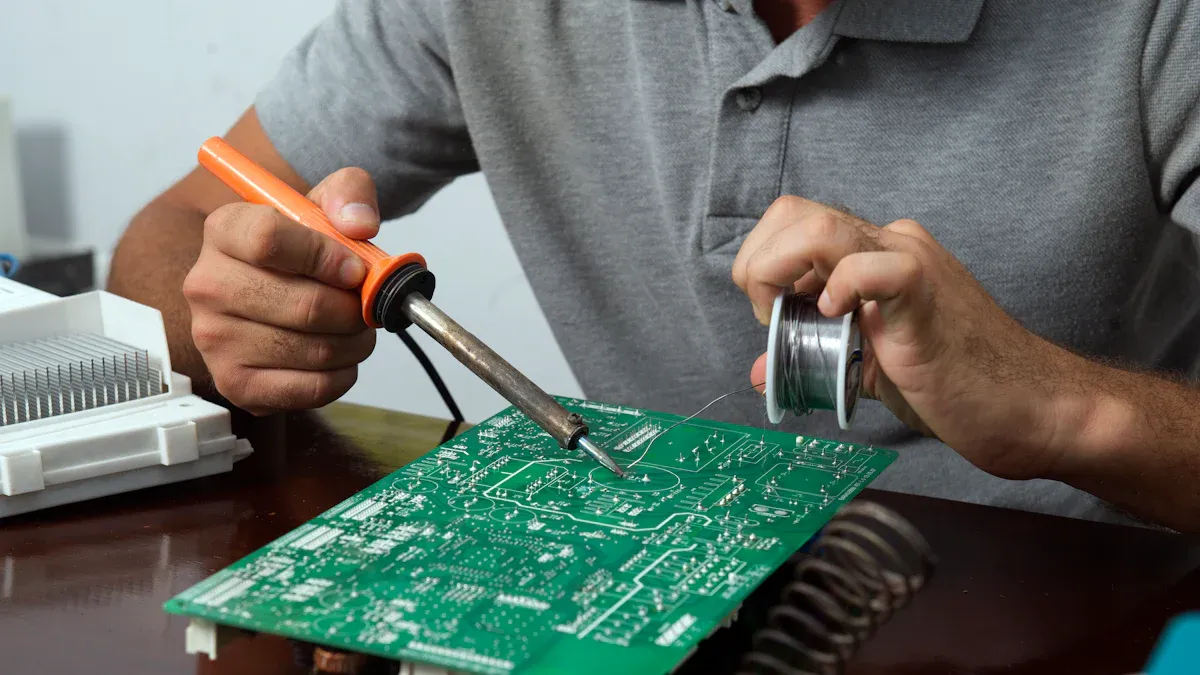
Dangers of Lead-Based Solder to Health and Nature
Lead-based solder can harm people and the environment. If thrown away carelessly, lead can seep into soil and water. This pollution hurts plants, animals, and humans. Workers making products with lead face health problems. It can damage their nerves and kidneys.
Studies show big differences between lead-based and lead-free soldering. Lead-free soldering uses more energy but is less toxic when thrown away. This makes it a better choice for protecting nature over time.
How Lead-Free Solder Keeps Workers Safe
Using lead-free solder makes workplaces safer. It removes the danger of lead exposure, which harms health. Workers avoid breathing harmful fumes or touching dangerous materials. This change also helps future generations by cutting down on toxic waste.
Lead-free soldering supports global efforts to protect workers. Safer metals like tin, silver, and copper are used. This creates a healthier and more responsible way to make products.
Following Environmental Rules with Lead-Free Solder
Switching to lead-free soldering helps follow strict environmental rules. Groups like the EPA set limits on lead in products. For example, the Safe Drinking Water Act requires products to meet lead-free standards. These rules aim to stop lead from polluting water and harming health.
By following these rules, you avoid fines and show you care about the planet. This also improves your company’s image and ensures your products meet global standards.
Regulatory Compliance and Standards for Lead-Free Manufacturing
Role of RoHS and Similar Regulations
Rules like RoHS help make safer electronics. They limit harmful materials like lead, mercury, and cadmium. For example, RoHS allows only 0.1% lead in products. This keeps items safer for people and nature.
Here’s a table showing limits for substances under RoHS:
Substance | Maximum Allowed Amount (%) |
---|---|
Lead | 0.1 |
Mercury | 0.1 |
Cadmium | 0.01 |
Hexavalent chromium | 0.1 |
Polybrominated biphenyls (PBB) | 0.1 |
Polybrominated diphenyl ethers (PBDE) | 0.1 |
Bis(2-Ethylhexyl) phthalate (DEHP) | 0.1 |
Benzyl butyl phthalate (BBP) | 0.1 |
Dibutyl phthalate (DBP) | 0.1 |
Diisobutyl phthalate (DIBP) | 0.1 |
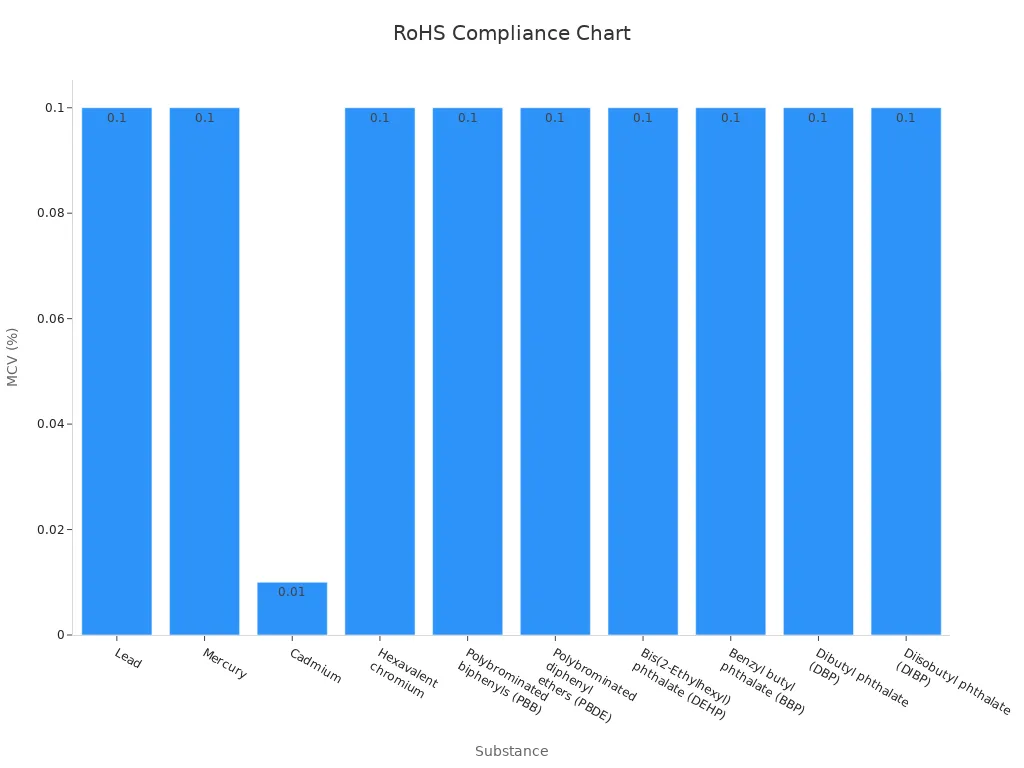
By following these limits, products stay safe and eco-friendly.
Industry Standards for Lead-Free PCBA Manufacturing Process
Standards guide quality in lead-free PCBA production. Rules like IPC-A-610 and IPC-J-STD-001 focus on soldering and inspections. These updates ensure reliable and consistent products.
ISO certifications also support quality checks. Following RoHS and REACH rules keeps lead below 0.1%. This protects the planet and reduces health risks.
Tip: Using these standards improves product safety and builds trust.
Challenges in Meeting Compliance Requirements
Switching to lead-free manufacturing can be hard. Problems include lack of training, poor process changes, and limited resources. These issues may hurt compliance and product quality.
Not enough training for workers |
Weak management of process changes |
Few resources for monitoring and analysis |
To fix these problems, train workers, improve processes, and invest in monitoring tools. This helps meet rules and ensures smooth transitions to lead-free manufacturing.
Practical Considerations for Choosing Between Lead-Based and Lead-Free Solder
Cost Differences and Economic Implications
Cost is important when picking between lead-based and lead-free solder. Lead-free solder costs more because metals like tin, silver, and copper are pricey. Studies show its base metals cost 263% more than lead-based solder. But, you need 14.1% less lead-free solder by weight, which helps reduce costs.
Switching to lead-free manufacturing may need new tools. Higher temperatures mean buying heat-resistant equipment like reflow ovens. These upfront costs are high but save money later. They lower risks with environmental rules and improve worker safety.
Tip: Check your budget and production needs. Decide if long-term savings from lead-free solder are worth the initial expense.
Suitability for Specific Applications
Choosing solder depends on what your PCBA needs. Lead-free solder works well for electronics because it’s eco-friendly and meets global rules. But lead-based solder is better for reliable uses like medical devices or airplanes.
Think about PCB design, factory setup, and heat levels when choosing. Standards like IPC J-STD-001 help guide soldering processes. They ensure good solder joints and match your needs. For plated through-hole (PTH) connections, full solder fill is key for strong and lasting bonds.
Solder paste is also important. It connects parts and stops oxidation. This helps make high-quality lead-free PCBA products.
Availability of Materials and Equipment
Material and tool availability can affect your choice. Lead-based solder is easy to find and works with most setups. Lead-free solder needs special alloys like SAC and tools for high heat. Smaller factories may struggle with these needs.
Switching to lead-free solder might mean finding new suppliers and buying advanced tools. This can seem hard, but demand for lead-free solder has grown. Many suppliers now offer solutions for different industries.
Note: Work with trusted suppliers and train your team. This makes switching to lead-free solder easier and more effective.
Future Trends in Lead-Free Manufacturing
The future of lead-free manufacturing is changing quickly. New ideas and eco-friendly goals are driving these changes. Industries are improving soldering methods to meet new needs. These updates aim to make products better and factories more efficient.
One big trend is using more lead-free solder in different industries. By 2025, the market for lead-free solder preforms is expected to reach $383 million. It is growing at 6.3% each year from 2019 to 2025. This shows a rising need for greener solutions, especially in electronics, medical tools, and cars. Tiny gadgets like wearable health devices and smart car sensors are leading this change.
Manufacturing methods are also improving. High-tech machines now handle precise soldering and assembly. These tools help make smaller, more detailed electronic parts. For instance, automated systems apply solder evenly. This lowers mistakes and makes products more reliable.
Saving energy is another focus. Companies are finding ways to use less power during lead-free PCBA production. Better reflow ovens and flux materials are reducing harm to the environment. Research is also creating new alloys that work well at lower temperatures.
Tip: Keep up with these trends to stay ahead. Using advanced tools and eco-friendly methods helps meet rules and customer needs.
As demand for lead-free solder rises, the industry will keep improving. This will lead to safer and smarter ways to manufacture products.
Knowing the differences between lead-based and lead-free PCBA processes helps you choose wisely. Lead-based solder melts at lower temperatures and lasts longer under stress. Lead-free solder handles heat better and is safer for the planet.
Item | Lead-Based (Sn37Pb) | Lead-Free (SAC387) | Lead-Free (Sn0.7Cu) |
---|---|---|---|
Melting Point (°C) | 183 | 217 | 227 |
Thermal Conductivity (W/m·1k·1s) | 50 | 73 | / |
Fatigue Life | 3 | 1 | 2 |
Think about rules and environmental effects when deciding. For important uses, focus on how the solder performs. Check costs, tools, and long-term benefits to pick the best option for your needs.
Tip: Follow industry updates to meet future needs and eco-friendly goals.
FAQ
1. What makes lead-based and lead-free solder different?
Lead-based solder melts at lower heat and makes strong joints. Lead-free solder uses safer metals like tin and copper but needs higher heat. Pick based on your product’s needs and environmental rules.
2. Why is lead-free soldering better for nature?
Lead-free solder removes harmful lead, keeping soil and water clean. It also keeps workers safe from dangerous exposure. Using it supports safer practices and follows rules like RoHS.
3. Is lead-free solder more expensive than lead-based solder?
Yes, lead-free solder costs more because of pricey metals like silver. But it saves money later by avoiding fines and health problems. Check your budget and goals before choosing.
4. Can lead-free solder work in tough conditions?
New alloys like SAC305 make lead-free solder stronger. But it’s not as durable as lead-based solder for extreme uses. For things like airplanes or medical tools, lead-based solder might be better.
5. What tools are needed for lead-free soldering?
You’ll need heat-resistant tools like advanced reflow ovens. Special fluxes can also help stop oxidation. These tools make lead-free soldering easier and more effective.
See Also
Achieving Excellence in PCBA Manufacturing Techniques and Practices
Comparing Turnkey and Consignment PCBA Manufacturing Approaches
Understanding the Key Differences Between Prototype and Production PCBs
Ensuring Quality Control Throughout the Entire PCBA Manufacturing Process
Facilitating a Smooth Transition from Prototype to Production in PCBA