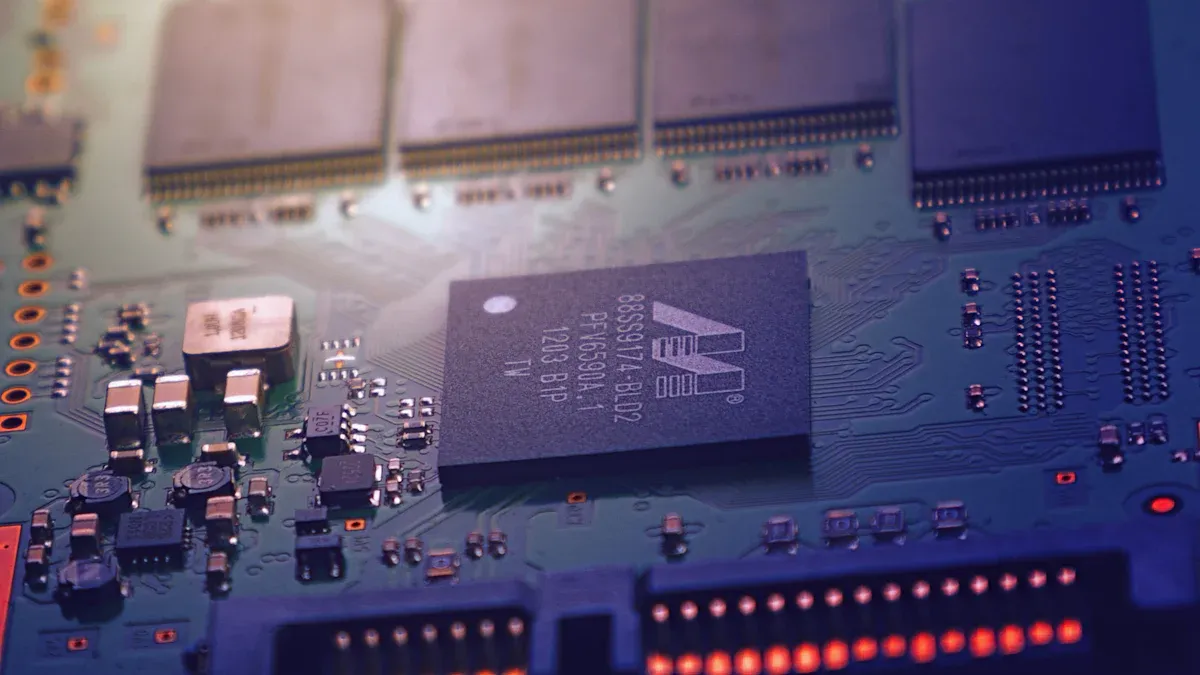
Low volume high mix PCBA manufacturing is very important today. It helps make different and special products quickly and accurately. This method uses new tools like 3D printing and CNC machines. These tools allow easy changes to designs and less waste. Lean ideas like Just in Time production also help reduce waste.
Making sure PCBA parts are real is very important for safety. Fake parts can cause problems, lower quality, and cost a lot to fix. Strong anti-counterfeiting steps are needed to keep your process safe. This ensures you make reliable and trustworthy products.
Key Takeaways
Making small amounts of many PCBA types helps meet customer needs. It ensures products are custom-made and high-quality.
Using strong anti-fake steps, like tracking and testing parts, stops fake pieces from entering your supply chain.
Fields like aerospace and healthcare gain a lot from this method. It helps make special parts that follow strict safety rules.
Smart tools like AOI and X-ray checks find problems early. This improves quality and makes small batches more reliable.
Following rules like IPC-A-610 keeps PCBA quality steady. This makes products safer and more dependable.
What is Low Volume High Mix PCBA Manufacturing?
Definition and characteristics of high-mix, low-volume manufacturing
High-mix, low-volume manufacturing makes many different products in small amounts. It works well for industries needing custom designs and frequent updates. Unlike mass production, this method focuses on being flexible and adaptable. Think of it like “made-to-order,” where each item fits specific customer needs.
Feature | Explanation |
---|---|
Wide Product Range | Creates many types of products in small quantities |
Custom Designs | Focuses on making products that can change quickly |
Production Style | Makes items based on what customers want |
For example, Scandinavian countries need small batches of marine and energy parts. Norway’s wind turbine makers often order custom flanges, sometimes only 100 units. This shows how this method helps industries with special needs.
Benefits of flexibility and customization in PCBA production
This type of manufacturing has big advantages in flexibility and customization. It lets you quickly adjust to customer needs and market changes. This ensures your products match exact designs, even if they are complex.
Benefit | Explanation |
---|---|
Quick Adjustments | Makes production faster by changing to meet new demands. |
Custom Solutions | Creates products that fit specific customer needs perfectly. |
Fast Prototyping | Tests and changes designs quickly, speeding up product launches. |
Customization also helps test designs before finalizing them. This lowers the risk of making products that don’t work well. For example, some companies use 3D printing and machining to finish projects in just 12 days. This shows how flexible production saves time and improves results.
Importance for industries with diverse and specialized product needs
Industries like aerospace, medical devices, and renewable energy depend on this manufacturing style. They often need unique parts that can’t be mass-produced. Small-batch production ensures high quality and meets tight deadlines.
Advantage | Explanation |
---|---|
Fast Prototyping | Helps test new products quickly with small batches. |
Short Lead Times | Produces items fast to meet strict schedules. |
Custom Designs | Makes parts that fit special project needs and designs. |
Quality Focus | Pays close attention to quality because of smaller production sizes. |
Cost Savings | Cuts costs by avoiding large-scale production and reducing waste. |
A 2022 study found 68% of aerospace suppliers struggled to deliver parts under 10 weeks for small orders. High-mix low-volume manufacturing solves this problem with speed and flexibility. It’s key for creating advanced electronics as technology grows.
Applications of Low Volume High Mix PCBA Manufacturing
Use in aerospace and defense sectors
Low volume high mix PCBA manufacturing helps aerospace and defense industries. These fields need accurate and reliable parts. They often require small amounts of special components. For instance, an avionics company wanted to make more products without extra costs. Using this method, they saved a lot of money. They turned $10 million of fixed costs into flexible ones. They also cut inventory by over $5 million. This worked because they followed AS9100 rules and had a good product transfer process.
This method also helps build advanced systems like radar and communication tools. It ensures all parts meet strict safety and quality rules. You can trust this process to make great products and handle tough needs.
Role in medical devices and healthcare
Medical devices need to be precise and custom-made. Low volume high mix PCBA manufacturing is very useful here. It helps make small batches of important tools like pacemakers and health monitors. These devices often need special designs for specific medical uses.
This method also allows quick testing of new designs. You can improve products fast to meet healthcare rules. Its flexibility helps meet the changing needs of the medical world. This ensures patients get safe and reliable devices.
Applications in automotive and industrial electronics
In cars and factories, this method offers speed and flexibility. Tools like industrial CT scanning improve quality checks. You can use this process to make parts for electric cars and robots.
This approach gives useful data to make smarter choices. It also helps meet different customer needs and market changes. By focusing on small batches, you keep quality high and stay flexible. This makes it perfect for industries needing precision and innovation.
Examples of products using high-mix, low-volume manufacturing
High-mix, low-volume manufacturing helps make special products for many industries. It is important where accuracy and custom designs are needed.
Aerospace Components: Airplane makers need small amounts of custom parts like sensors and communication tools. These parts must follow strict safety rules. This method ensures the parts meet exact needs for important uses.
Medical Devices: Items like insulin pumps and heart monitors use this process. Each device is made to fit patient needs and follow health rules. This method makes small amounts of custom devices quickly.
Automotive Electronics: Electric car makers use this to create battery systems and sensors. These parts often need updates to match new technology. This process helps companies stay ahead in a fast-changing market.
Industrial Automation Tools: Factories use robots and tools made for specific jobs. For example, circuit boards for robotic arms are made in small batches. This ensures the tools work well and are reliable.
Tip: High-mix, low-volume manufacturing is great for industries needing new ideas and quick changes. It helps test designs, cut waste, and make high-quality products.
Using this method, you can create products that are unique and work well. It’s a big help for industries needing both precision and flexibility.
Challenges in Low Volume High Mix PCBA Manufacturing
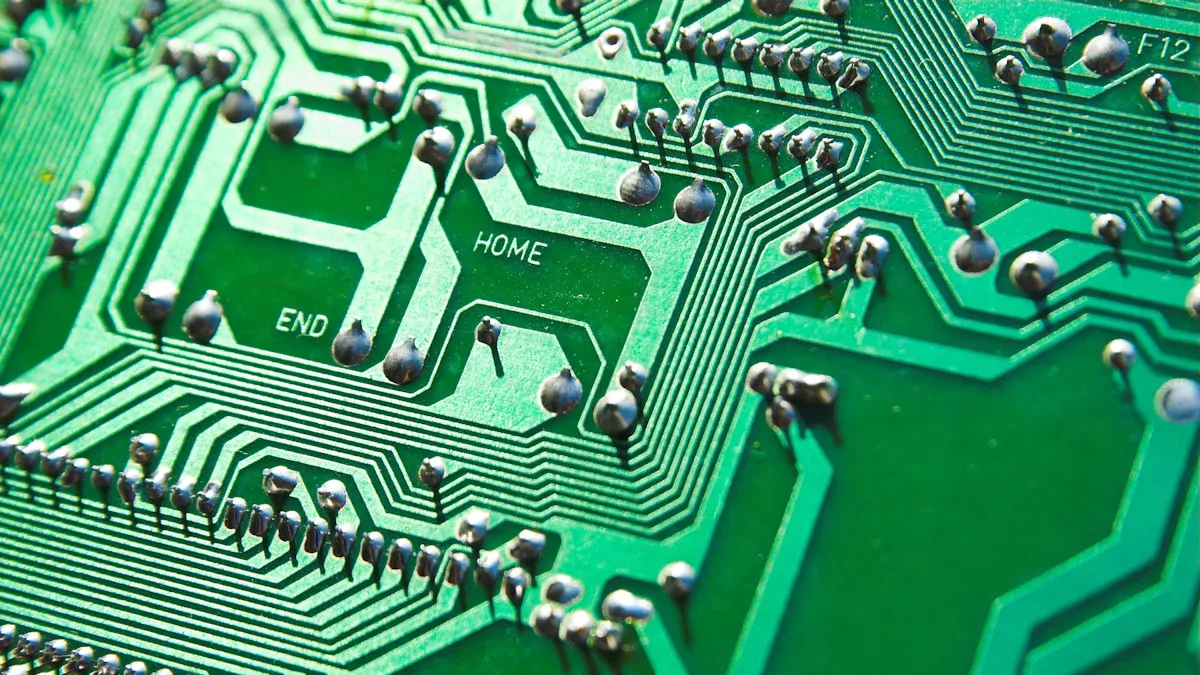
Supply chain problems and finding components
HMLV manufacturing has tricky supply chain issues. Managing many materials for small batches costs more for storage. For example, keeping lots of parts can cause more waste than big-batch production. Making different PCB assemblies also makes scheduling harder and slows projects. Even simple tasks can take longer.
Another problem is material costs. You might need to buy more parts than needed. This extra stock can become useless over time. Production lines for HMLV need constant changes, which lowers how much you can make.
Problem Type | Explanation |
---|---|
Storage Costs | Many materials need more space and create more waste. |
Scheduling Issues | Different PCB assemblies make planning and timing harder. |
Extra Material Costs | Buying in bulk creates waste if parts aren’t used. |
Lower Efficiency | Changing production lines often slows down the process. |
Dangers of fake components
Fake parts are a big problem in HMLV manufacturing. These bad parts can make your products fail, especially in important uses. In 2022, ERAI found 768 fake or bad parts, 35% more than in 2021. Fake parts hurt product quality and cost more because of fixes and recalls.
The money lost to fake goods is huge. The U.S. Chamber of Commerce says fake items cost $500 billion yearly. For small-batch production, even one fake part can ruin the process. It can delay orders and harm your company’s reputation.
Quality control in small-batch production
Keeping quality high in small batches is tough. You need advanced tests like AOI, X-ray checks, and ICT. These tests make sure every PCB meets strict rules. Small batches mean fewer chances to fix mistakes, so quality checks are very important.
Following IPC rules, like IPC-A-610, helps keep products consistent. These rules ensure your PCBs meet industry standards. By focusing on quality at every step, you can handle small-batch challenges and make reliable products.
Ensuring Authenticity and Reliability of PCBA Components
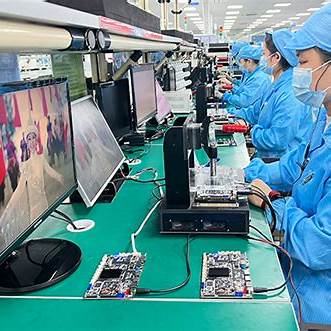
Anti-counterfeiting measures for PCBA components
Fake parts can harm your PCB assembly. They may cause failures, safety issues, and cost money. To stop this, use strong anti-counterfeiting steps. First, track each part to its source. This helps confirm it is real. Buying parts from trusted sellers also lowers the chance of getting fake ones.
Testing is key to finding fake parts. Check and test all parts when they arrive. You can also use outside testing services for extra safety. These tests might not catch every fake, but they add more protection.
Anti-Counterfeiting Measure | Description |
---|---|
Component Traceability | Tracks parts back to their source to confirm they are real. |
Testing Procedures | Checks parts carefully to ensure they are genuine. |
Sourcing from Authorized Distributors | Buys parts from trusted sellers to avoid fake components. |
Tip: Blockchain can help track parts better. It keeps a secure record of every transaction, making it harder for fakes to slip in.
Quality assurance practices in PCBA manufacturing
Keeping high quality in small-batch PCBA production needs good checks. Follow rules like IPC-A-610 to meet industry standards. These rules make sure your PCBs work well and last long.
Use different ways to inspect your PCBs. Look at them closely to find surface problems. Use machines like AOI to spot misplaced parts. Electrical tests, like ICT, check if the PCBs work properly. SPC methods help you watch and control the process for steady quality.
Key Practices for Quality Assurance:
Check PCBs visually and with AOI machines.
Test PCBs electrically to ensure they work.
Use SPC to keep production steady and reliable.
A report from IPC showed over 50 companies use SPC and First-Pass Yields to keep quality high. By using these methods, your PCBs will be reliable and meet top standards.
Role of advanced technologies in combating counterfeiting
New tools help fight fake PCBA parts. Visual checks can find wrong markings or finishes. X-ray checks look inside parts to see if they match real ones.
Functional tests are also helpful. Replace a suspicious part on a working PCB to see if it works. These tools not only find fake parts but also make your production more reliable.
Source Type | Counterfeit Rate | Error Range in Traceability |
---|---|---|
Franchised Source | 0.4% | 0.5% to 8% |
Brokers’ Industry | 4-5% | N/A |
Steps to Combat Counterfeiting:
Inspect all parts when they arrive.
Compare parts visually with real ones.
Use x-rays to check inside parts.
Using these tools lowers the risk of fake parts. This keeps your products trustworthy and safe, even for important uses.
Low volume high mix PCBA manufacturing is very important for industries. It helps make custom, high-quality products that meet changing needs. This method is crucial for fields like aerospace, healthcare, and cars, where safety and quality are a must.
Reminder: Fake parts can harm your product’s safety and work. Using anti-counterfeiting steps and strong quality checks keeps your PCBs up to industry standards.
To improve authenticity and reliability, you should:
Buy parts only from trusted sellers.
Use advanced tests like AOI and X-ray checks.
Track every part with traceability systems.
By following these steps, you can make reliable products and gain customer trust.
FAQ
How can you make sure PCBA parts are real?
Buy parts only from trusted sellers and use tracking systems. Tests like AOI, X-ray, and ICT check if parts are real. Blockchain can also safely track parts to stop fakes.
How do new technologies improve PCBA quality checks?
Tools like AOI and X-ray find problems early. ICT checks if PCBs work correctly. SPC keeps production steady. These tools make products better and reduce mistakes in small batches.
Why is IPC-A-610 important for making PCBs?
IPC-A-610 gives rules for making good PCBs. Following these rules ensures your products are reliable and meet global standards. It also helps keep quality the same in every batch.
How does tracking parts stop fake components?
Tracking shows where each part comes from. It creates a clear record, making it harder for fake parts to get into your supply chain. This keeps your products safe and trustworthy.
Which industries use low volume high mix PCBA manufacturing?
Industries like aerospace, healthcare, cars, and factories use this method. It helps make custom designs, test ideas quickly, and create high-quality products for special needs.
See Also
Achieving Superior Quality Through Effective PCBA Manufacturing Methods
Guidelines for Assembling PCBA and Avoiding Frequent Mistakes
Locating the Ideal PCBA Manufacturer to Suit Your Requirements