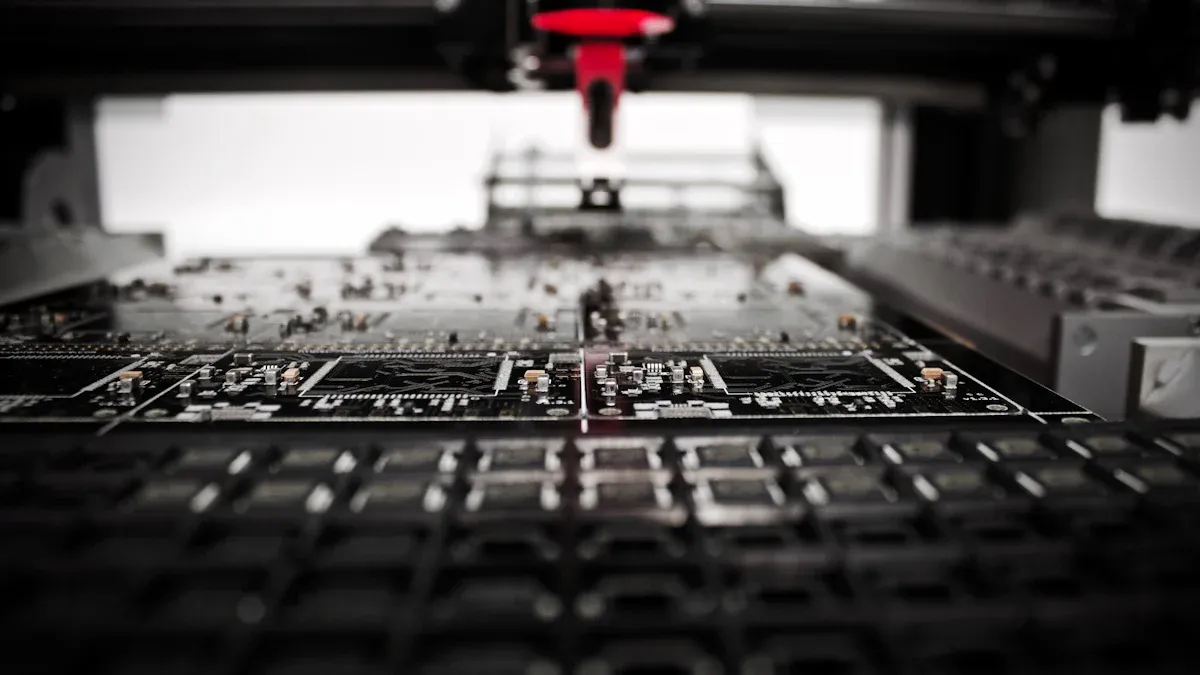
When making electronic devices, there are two main types of PCB fabrication: prototype PCBs and production PCBs. Each has a different job. Prototype PCBs allow you to test designs and find mistakes before producing many. They are cheaper and simpler to fabricate because they don’t include parts. Production PCBs are made for large-scale manufacturing. They contain parts and undergo strict quality checks. This makes them cost more but ensures they function well. Understanding these differences is essential for effective PCB fabrication and creating quality products.
Key Takeaways
Prototype PCBs help test designs and fix errors early on.
Production PCBs are made for large-scale use with high quality.
Prototypes let you get feedback and improve designs before production.
Think about your project’s needs, cost, and time when deciding.
Testing prototypes in real life ensures the final product works well.
What Is PCB Prototyping?
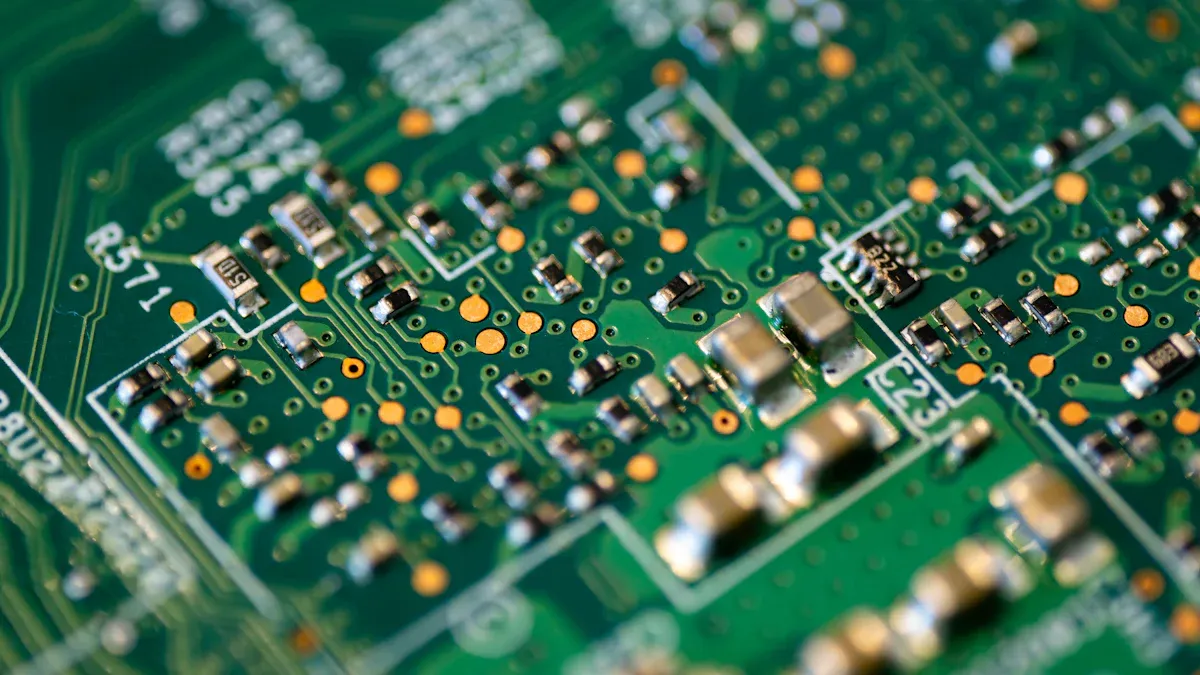
Definition of Prototype PCBs
Prototype PCBs are early versions of printed circuit boards made to test designs. These boards help check if your design works before mass production. Unlike production PCBs, they focus on testing layout and performance, not long-term use. They are made using simpler methods to save time and money during early development.
Description | |
---|---|
Single/Double-Sided | Simple boards with parts on one or both sides. |
Aluminum/Metal Core | Uses metal for better heat control in powerful devices. |
Multilayer | Layers stacked for more parts and better signals. |
Flexible | Made from bendable materials for small, unique shapes. |
Rigid-Flex | Mix of stiff and bendable parts for special designs. |
HDI | High wiring density for tiny, advanced electronics. |
Purpose of Prototype PCBs
Prototype PCBs are used to find and fix design problems early. By testing these boards, you can check if parts work together and meet performance needs. This process helps improve designs and avoid costly mistakes later. For example:
A fitness tracker startup used prototypes to test designs, fix issues, and get user feedback, speeding up their launch.
A factory equipment maker used prototypes to test new parts, fix signal problems, and improve performance for a better product.
Advantages of PCB Prototyping
Prototype PCBs have many benefits that make development easier. Some key advantages include:
Iterative Feedback: Regular reviews help improve the design step by step.
Risk Mitigation: Testing parts and conditions lowers the chance of problems.
Manufacturing Optimization: Fixing issues early makes production smoother.
Early User Testing: Feedback from users helps check if the design meets needs.
Testing prototype PCBs ensures your design works as planned. Repeating design and testing 2-3 times is ideal for a solid design. This saves time and reduces mistakes in the final product.
Disadvantages of PCB Prototyping
Even though pcb prototyping has many advantages, it also has some downsides. These issues can affect your schedule, costs, and design safety.
One big problem is the limited flexibility for design changes. If you use parts from manufacturers, changing your design becomes harder. This slows down testing, especially when trying different versions of your pcb prototypes.
Another issue is intellectual property (IP) protection. Sharing your designs and part details with manufacturers can be risky. Your ideas might get copied or accidentally shared with others. This is why picking reliable manufacturers is very important.
Here’s a table showing these main disadvantages:
Disadvantage | Description |
---|---|
Limited Flexibility | Manufacturer-sourced parts make design changes harder. |
Intellectual Property Concerns | Sharing designs with manufacturers can risk IP safety. |
IP Protection Challenges | – Competitors might see your designs |
– Your ideas could be copied without permission | |
– Less control over private design details |
Lastly, pcb prototyping can cost more per unit than production PCBs. Since prototypes are made in small amounts, setup and materials cost more. This makes it less budget-friendly for projects with limited money.
Knowing these downsides helps you plan better. Fixing these problems early ensures an easier move from prototyping to production.
What Is Production PCB Fabrication?
Definition of Production PCBs
Production PCBs are the final printed circuit boards made for mass production. These boards follow strict rules to ensure they last a long time. Unlike prototype PCBs, they use better materials and precise methods for large-scale use. They are built to be strong, work well, and stay consistent.
Purpose of Production PCBs
The main purpose of production PCBs is to create reliable products. These boards are made to fit the needs of the final device, like a phone, car, or medical tool. They go through tough tests to make sure they work in real-life situations. Using top-quality materials and machines, manufacturers can make thousands or millions of identical boards.
Here’s how production PCB fabrication compares to prototype PCB fabrication:
Aspect | Prototype PCB Fabrication | Production PCB Fabrication |
---|---|---|
Materials | Simple copper types, cheaper laminates | High-quality materials, special substrates |
Manufacturing Processes | Quick and simple methods | Advanced machines for accuracy and stability |
Cost Structures | Higher cost per board, small batches | Lower cost per board with large orders |
Manufacturing Tools | Flexible tools for changes | Fixed tools for mass production |
Design Flexibility | Easy to change designs | Strict control over design changes |
Quality Priorities | Basic testing | Careful checks for reliability |
Common Use Cases for Production PCBs
Production PCBs are used in many industries. They are found in electronics, cars, communication systems, and medical tools. The demand for these boards is growing fast. The global PCB market is expected to grow from USD 72.99 billion in 2023 to about USD 97.88 billion by 2031. This shows how important production PCBs are in today’s technology.
Consumer Electronics: Phones, laptops, and gaming devices.
Automotive: Driver-assistance systems and electric cars.
Telecommunications: 5G networks and communication tools.
Medical Devices: Health monitors and diagnostic machines.
Production PCBs are key to making reliable and high-quality products in these fields.
Key Differences Between Prototype and Production PCBs
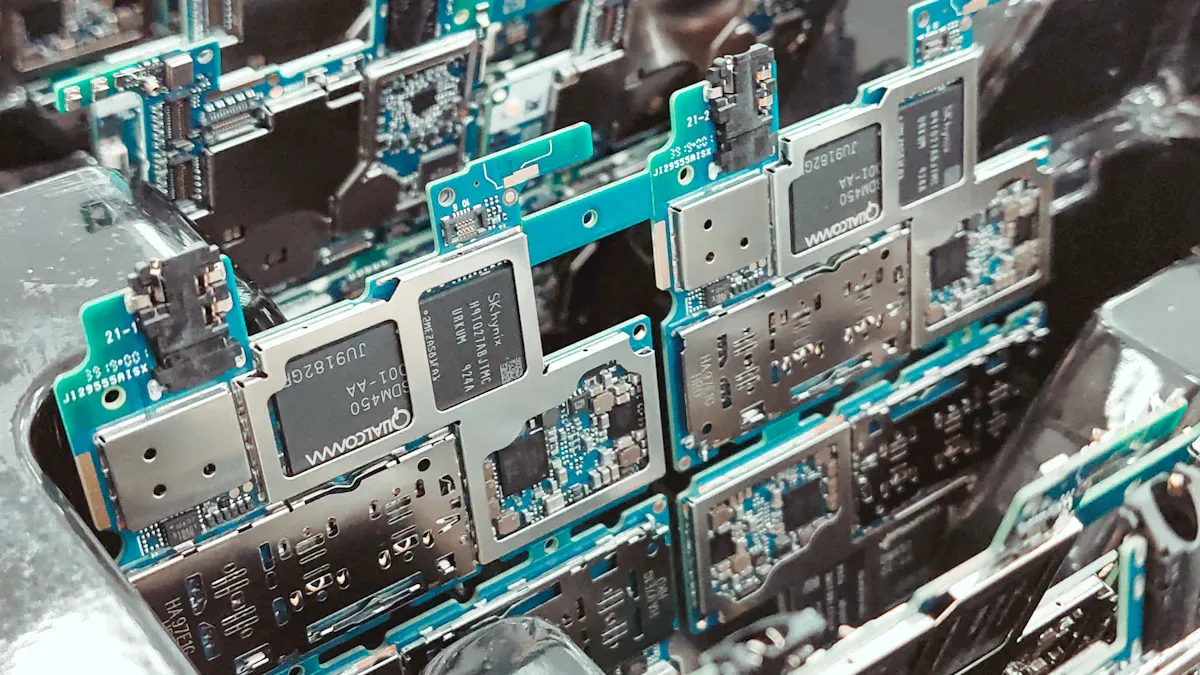
Manufacturing Processes
Making prototype PCBs and production PCBs is very different. For prototypes, speed and flexibility are most important. Simple methods like hand assembly or small machines are used. This helps test designs fast and make quick changes. Prototype PCBs usually have fewer layers and simpler designs, so they are faster to make.
Production PCBs need advanced methods. They use precise machines and strict quality checks. These steps ensure the boards meet high standards and are consistent. Special tools and equipment are used for mass production. This reduces mistakes and makes the process more efficient.
Cost Considerations
Prototype PCBs cost more per board than production PCBs. This is because prototypes are made in small amounts, spreading setup costs over fewer boards. To save money, focus on key features and track spending. For example:
Cost Tip | Explanation |
---|---|
List materials, labor, and services needed for prototypes. | |
Improve Gradually | Start simple and add features step by step to save money. |
Talk to Suppliers | Work with suppliers to get better prices and discounts. |
Production PCBs are cheaper per board when made in large numbers. Using the same designs and materials lowers costs even more during mass production.
Materials and Components
The materials for prototype and production PCBs are not the same. Prototypes often use common materials like FR-4, which are affordable and work well. This helps test designs without spending too much. For production PCBs, materials depend on what the device needs. High-end materials like PTFE or Polyimide are used for special cases, like high heat or fast signals.
Material | Features | Cost Level |
---|---|---|
FR-4 | Good mix of cost and performance | Medium cost |
PTFE | Great for fast signals | Higher cost |
Polyimide | Handles high heat well | Higher cost |
CEM-1/3 | Good for saving money | Lower cost |
Choosing the right materials ensures the boards work well and stay within budget.
Testing and Quality Assurance
Testing and quality checks are important for both prototype and production PCBs. For prototype PCBs, testing ensures the design works as planned. Simple methods like looking for errors or basic electrical tests are used. This helps find and fix problems before making many boards.
Production PCBs need stricter testing. Advanced tools like AOI, X-ray, and ICT are used. These tests make sure every board meets high standards. In production, even small mistakes can ruin thousands of boards.
The testing location also matters. Prototype PCBs are tested in labs with controlled settings. Production PCBs are tested in real-world-like conditions. This ensures they work well in their actual use.
Lead Times and Scalability
The time to make and scale PCBs is different for prototypes and production. Prototypes are made quickly to test designs. Small batches are produced fast, but delays can happen if special parts are needed.
Production PCBs take more time to plan. Large-scale production needs materials, setup, and supplier coordination. Using common materials and trusted suppliers avoids delays and keeps production steady.
Scaling is another big difference. Prototype PCBs are not made for large amounts. They are for small batches only. Production PCBs are designed for scaling. Factories use flexible tools and processes to meet market needs. For example:
Factor | Problem | Solution | Outcome |
---|---|---|---|
Managing Lead Times | Delays from rare materials | Use common materials | Smooth production, no delays |
Planning for Scaling | Uncertain future demand | Use flexible tools and suppliers | Quick response to market changes |
Knowing these differences helps you plan better and move smoothly from testing to full production.
When to Use Prototype PCBs vs. Production PCBs
Early Development and Testing Phases
Prototype PCBs are very useful in early product development. They help test designs, find problems, and improve features before mass production. This stage is about trying ideas and making quick changes. Prototype PCB assembly is faster, so you can test many designs quickly.
For example, if you’re making a fitness tracker, prototypes let you check how it works with sensors and get user feedback. Fixing these issues early saves money and avoids big mistakes later.
Tip: Test prototype PCBs in real-world conditions. This helps ensure your product works as planned before moving to production.
Transitioning to Mass Production
After testing and finalizing your design, move to production PCBs. This step focuses on making strong, high-quality boards for large-scale use. However, scaling up can be tough. Studies show only 11% of companies succeed in moving from testing to full production, while 88% face big challenges.
Evidence | Description |
---|---|
Out of 33 AI prototypes, only 4 reach production. | |
11% success rate | Just 11% of companies gain value beyond pilot projects. |
3x higher revenue impact | Companies that scale AI see up to 20% revenue growth. |
To make this shift easier, focus on designs that are easy to manufacture and reliable. Work with manufacturers who use advanced tools like automated testing and strict quality checks.
Factors to Consider When Choosing Between the Two
Choosing between prototype and production PCBs depends on your project needs. Think about these factors:
Manufacturing Capabilities: Check if the manufacturer can handle your design, like SMT or THT assembly.
Turnaround Time: Prototypes are made faster, which helps with tight deadlines.
Technical Expertise: Pick a manufacturer skilled in complex designs to avoid mistakes.
Quality Control Processes: Ensure the manufacturer has strong testing to make reliable boards.
Factor | Description |
---|---|
Manufacturing Capabilities | Services like SMT and THT are important for different designs. |
Turnaround Time | Prototypes are quicker to produce, helpful for fast projects. |
Technical Expertise | Skilled manufacturers reduce errors in tricky PCB designs. |
Quality Control Processes | Strong testing ensures the boards work well and last long. |
By thinking about these points, you can choose the right PCB type for your project and timeline.
Prototype PCBs let you test and improve your designs. They make sure everything works before moving forward. Production PCBs are made for strength and reliability in large amounts. Knowing these differences helps you plan better and avoid expensive mistakes.
Key Takeaway:
Use prototype PCBs for testing early ideas. Switch to production PCBs when your design is complete and ready for mass production.
Tip: Think about your project’s stage, budget, and needs. Picking the right PCB type helps you build faster and launch successfully.
FAQ
What is the main difference between prototype and production PCBs?
Prototype PCBs are used to test and improve designs. Production PCBs are made for large-scale use in final products. Prototypes allow quick changes, while production boards are built for strength and reliability.
Can you reuse prototype PCBs for production?
No, prototype PCBs cannot be reused for production. They are made with simpler materials and methods, which may not meet the high standards needed for mass production.
How long does it take to manufacture prototype PCBs?
Making prototype PCBs takes a few days to a week. The time depends on how complex the design is and if materials are available.
Are prototype PCBs more expensive than production PCBs?
Yes, prototype PCBs cost more per piece because they are made in small amounts. Production PCBs are cheaper per piece when made in large numbers.
Why is testing important for prototype PCBs?
Testing checks if your design works correctly. It helps find and fix problems early, saving time and money before production. Skipping testing can lead to costly mistakes in the final product.
Tip: Test prototype PCBs in real-world settings to get accurate results.
See Also
Achieving Superior Quality Through PCBA Manufacturing Mastery
Comparing Turnkey And Consignment PCBA Manufacturing Approaches
Guide to Assembling PCBA While Avoiding Frequent Mistakes
Locating The Ideal PCBA Manufacturer To Suit Your Requirements