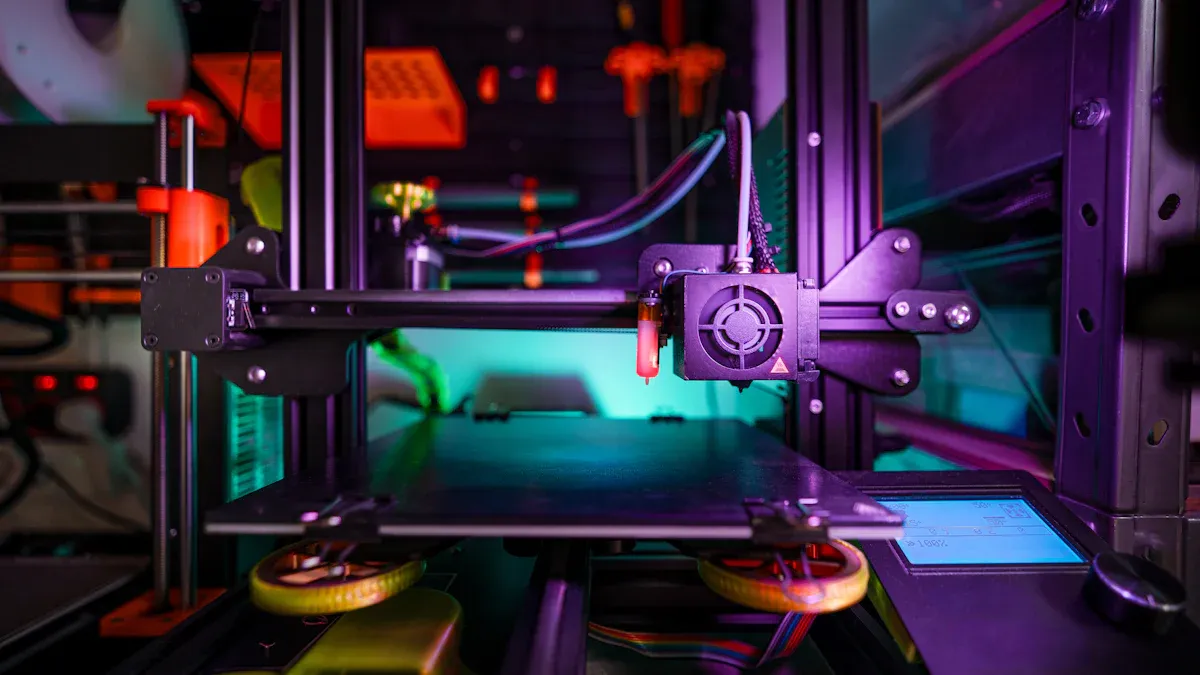
Smart factory controller PCB assembly is revolutionizing the way PCB assembly is performed. These systems utilize machines to produce electronics more quickly and efficiently. With advanced technologies such as IoT and AI, they operate with precision and minimize waste. Smart factory controller PCB assembly enhances the quality of PCBs and increases order capacity. Additionally, they streamline workflows and reduce errors, saving valuable time. Leveraging these tools provides a competitive edge in the fast-paced electronics industry.
Key Takeaways
Smart factory controllers help PCB assembly by using IoT and AI. They cut waste and make products better.
Automation makes PCB assembly faster and reduces mistakes. This creates better products at lower costs.
Real-time data helps factories check performance and act quickly. It stops defects and boosts efficiency.
Smart factory technology costs a lot at first. But it saves money later and gives businesses an edge.
Smart factory systems are flexible and scalable. They adjust quickly to meet changing customer needs.
Core Technologies Powering Smart Factory Controller PCB Assembly
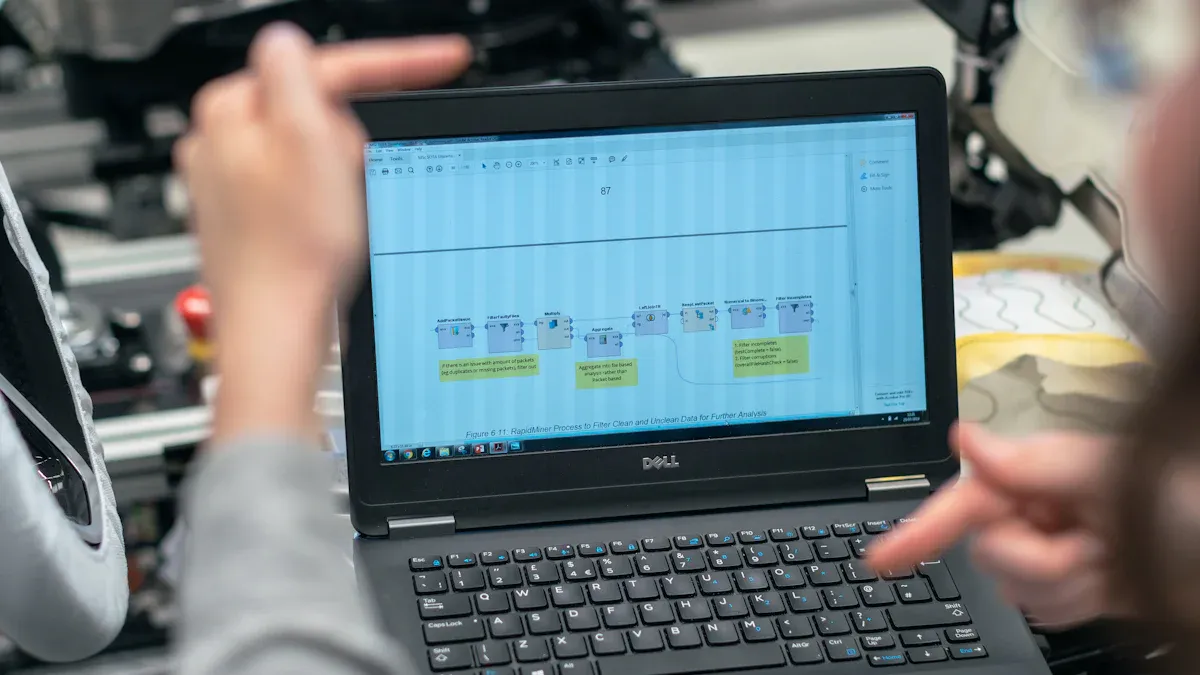
Internet of Things (IoT) for Connectivity and Automation
The Internet of Things (IoT) is key in smart factories. It links machines, sensors, and systems for smooth communication. This connection helps monitor and control assembly steps from anywhere. For example, IoT tools check assembly line performance live. They ensure every part is placed correctly.
IoT helps factories by cutting downtime and boosting efficiency. Bosch’s plant in Germany cut downtime by 25% using IoT. It also improved equipment effectiveness by 1.5%. Siemens’ factory in Germany saw a 20% productivity rise with IoT and AR-guided assembly. These examples show how IoT improves automation and advanced production in PCB factories.
Artificial Intelligence (AI) for Defect Detection and Process Optimization
Artificial intelligence (AI) changes how PCBs are checked for defects. Old methods miss flaws or take too long to find them. AI uses smart learning to spot problems quickly and accurately. It checks PCBs faster and better, lowering the chance of bad products.
A study called “AI-Driven Quality Control in PCB Manufacturing” shows AI improves defect detection. It also speeds up inspections and boosts production rates. Adding AI to your factory helps workflows run smoothly. It ensures high-quality results and smarter automation. AI makes processes more precise and efficient.
Robotics in Automation for PCB Assembly
Robots are vital in smart PCB assembly. They do tasks like placing parts and soldering quickly and precisely. This lowers mistakes and keeps quality steady. Robots also speed up production, making more PCBs in less time.
Studies show robots cut production time a lot. Moving parts at 50% speed makes assembly faster with fewer shakes. At 30% speed, robots place parts more accurately. These improvements show how robots make factories more efficient. Using robots helps meet the demand for better PCBs while scaling operations.
Real-Time Data Analytics for Better Monitoring and Decisions
Real-time data analytics helps improve how PCBs are made. It looks at data as it happens, allowing quicker decisions. This helps spot problems, fix them fast, and keep things running smoothly.
One big benefit is stopping defects early. Watching data all the time lets you catch issues before they grow. For example, if a machine acts strangely, analytics can warn you to fix it. This saves materials and makes better PCBs. Real-time tracking also shows patterns that improve production. Learning these patterns helps factories work faster and smarter.
Another advantage is tracking important numbers, called KPIs. KPIs show how well your factory is doing. You can measure speed, mistakes, and how resources are used. These numbers help you improve processes and boost efficiency.
Here are some facts about real-time analytics in factories:
Fact | What It Means |
---|---|
Unplanned downtime costs $50 billion yearly (Deloitte, 2021) | Shows how fixing problems quickly saves money. |
Predictive maintenance cuts downtime by 30-50% (McKinsey, 2022) | Proves analytics make machines last longer and work better. |
75% of quality issues can be stopped early (Quality Magazine, 2022) | Shows how analytics improve product quality. |
IIoT could add $1.2 to $3.7 trillion globally by 2025 (McKinsey, 2021) | Highlights the big economic impact of using analytics. |
Companies using analytics see big improvements. They work 17% more efficiently than others. They also make better products with 21% fewer mistakes. These results show why real-time analytics is important for PCB assembly.
Using real-time analytics can change how factories work. It helps make smarter choices and keeps everything running well.
Benefits of Automation in PCB Assembly with Smart Factory Controllers
Better Precision and Quality Control in PCB Manufacturing
Automation improves accuracy and keeps quality consistent in PCB assembly. Tools like computer vision and lasers help find defects and place parts perfectly. These systems check every detail, reducing mistakes and improving how electronics are made.
Smart factories use tools like decision trees and object detection for precision. These tools can find defects with over 82% accuracy. Companies using computer vision report 99% success in spotting flaws. Object detection tools reach 98.5% accuracy, cutting false alarms and increasing profits.
Tip: Using automated tools improves quality and reduces waste, making better PCBs for your customers.
Faster Production and Higher Efficiency
Automation speeds up PCB assembly and increases production. Machines work faster than people, handling complex designs efficiently. This helps meet the demand for smart electronics while keeping quality high.
Automated systems reduce mistakes and make workflows smoother. Faster machines and fewer errors mean better products and quicker production. For example, automation allows tiny designs that manual work can’t handle.
Main Benefits of Automation in PCB Assembly:
Faster processes boost production speed.
Fewer mistakes improve accuracy and reliability.
Consistent quality ensures better electronics performance.
Lower costs make your business more competitive.
Using smart factory controllers helps you improve production without losing quality.
Saving Money by Reducing Waste and Using Resources Wisely
Automation saves money by using materials and energy efficiently. Smart factories monitor every step to avoid waste and cut costs. This makes production more profitable.
Automated tools also reduce downtime and repair costs. Predictive maintenance finds problems early, saving time and money. Automation also lowers material waste by placing and soldering parts precisely.
Note: Studies show predictive maintenance can cut downtime by 50%, proving the cost benefits of automation in PCB assembly.
By using automation, you can save money and still deliver high-quality PCBs to your customers.
Improved Flexibility and Scalability in Smart Factories
Smart factory controllers help factories adjust to changing needs fast. They let you make more PCBs or switch to custom designs easily. This keeps work smooth, even when customer demands change quickly.
How Smart Factory Controllers Enable Flexibility
Quick Changes to Production Lines
These controllers let you change production lines with little delay. For instance, switching from regular PCBs to custom ones is simple. Machines adjust settings automatically, saving time and effort.Handling Different PCB Designs
Advanced automation supports many PCB designs, from simple to complex. This ensures you meet customer needs without losing quality.Real-Time Updates
Smart controllers watch production live and make changes instantly. If a design changes during production, the system updates right away. This reduces waste and delivers what customers want.
Tip: Flexible systems help you stay ahead by adapting to market changes fast.
Scalability for Growing Demands
As your business grows, these controllers make scaling easy. You can increase production without major changes to your setup.
Adding New Machines Easily
New equipment fits in smoothly with existing systems. This helps your factory handle more work without trouble.Using Resources Wisely
These systems save materials, energy, and labor. Scaling up becomes cost-effective and efficient.Cloud Technology for Growth
Many controllers use cloud systems to manage data. This allows factories in different places to work together under one system.
Real-World Example: Keeping Up with Demand
Imagine a sudden rise in demand for a certain PCB. Old systems might struggle to keep up. But smart controllers adjust schedules and resources quickly. This ensures on-time delivery and happy customers.
Note: Studies show flexible factories meet deadlines 30% more often during busy times.
Using flexible and scalable systems prepares your factory for the future. These tools help you grow and succeed in a fast-changing industry.
Challenges in Using Smart Factory Controllers for PCB Assembly
High Costs at the Start
Using smart factory controllers needs a lot of money upfront. Buying advanced tools and upgrading systems can cost €150,000 to €500,000. These costs include new machines and setting up better technology. For smaller companies, this can be a big problem.
It often takes over three years to get your money back. This long wait can stop businesses from using automation. Also, technical issues and cybersecurity risks add to the cost. So, it’s important to check if the investment is worth it before starting.
Tip: Begin in small steps to spread out costs and avoid stress.
Problems with Old Machines
Adding new technology to old machines can be hard. Many older tools don’t work well with modern systems. Fixing this can take a lot of time and money. For example, making old machines fit new needs may need big changes.
Experts must work together to make the process smooth. But this teamwork can be tricky and cause delays. Connecting old systems to new networks also increases hacking risks. Strong security plans, like IEC 62443 or NIST rules, are needed to stay safe.
Problem Type | Details |
---|---|
Technical Issues | Old machines don’t easily match with new systems, making it expensive. |
Teamwork Challenges | Experts need to work together, which can be tough to manage. |
Cost Problems | High prices of new tools make it hard for some companies. |
Training Workers and Fixing Skill Gaps
Smart factory controllers need skilled workers to run them. Employees must learn how to use and fix these advanced systems. Many workers may not have the right skills, which creates a problem.
Teaching workers takes time and money. Training should cover both technical skills and safety from cyber threats. Without good training, workers may find it hard to adjust. This can slow down work and cause problems.
Note: Ongoing training programs help workers stay ready for new tools and methods.
Cybersecurity Risks in Connected Manufacturing Systems
Connected systems make PCB assembly faster and smarter. But they also bring cybersecurity risks. Adding IoT devices, AI tools, and cloud systems can expose your factory to cyberattacks. Knowing these risks helps you stay safe and keep customer trust.
Common Cybersecurity Threats in Smart Factories
Data Breaches: Hackers might steal important data like PCB designs or customer info. This can hurt your business and damage your reputation.
Ransomware Attacks: Cybercriminals could lock your systems and ask for money to unlock them. This stops production and costs you money.
Unauthorized Access: Weak passwords or old security systems let attackers control your machines. This can cause bad products or stop work.
Supply Chain Attacks: Problems in third-party tools or software can lead to threats. These attacks are often unnoticed until major damage happens.
Did You Know?
A 2023 report says ransomware attacks on factories rose by 87% in two years.
How to Reduce Cybersecurity Risks
Use Strong Passwords: Add multi-factor authentication (MFA) for better security.
Update Software Often: Fix weak spots by keeping devices and apps updated.
Watch Your Network: Use tools to spot strange activity and act fast.
Teach Your Team: Train workers to avoid scams and use safe online habits.
Cybersecurity Step | Why It Helps |
---|---|
Multi-Factor Authentication | Blocks unauthorized access |
Software Updates | Repairs security problems |
Network Monitoring | Finds threats quickly |
Employee Training | Lowers mistakes from human errors |
By fixing these risks, you protect your factory and keep production running smoothly. Cybersecurity is not just a tech issue—it’s key to running a smart factory well.
Real-World Uses of Smart Factory Controllers in PCB Assembly
Siemens’ Example of Smart Factory Technology in PCB Making
Siemens shows how smart factory tools improve PCB production. At their Amberg plant in Germany, they use automation and IoT for 75% automated PCB assembly. This setup reduces mistakes and waste while keeping quality high.
Real-time data helps track machines and improve workflows. If a machine starts wearing out, predictive tools warn workers early. Fixing issues before they cause delays saves time and boosts efficiency. Siemens proves smart factory tools make PCB production smoother and more reliable.
Success in Large-Scale PCB Production
Smart factory controllers speed up large-scale PCB assembly. Companies like Foxconn use robots and AI to make millions of PCBs each year. These tools ensure high quality even with big orders.
Automated optical inspection (AOI) checks every PCB for flaws. This ensures only good products are sent out. Real-time data finds slow spots and improves schedules. With these tools, factories meet high demand without losing speed or quality.
Custom and Prototype PCB Assembly Benefits
Smart factory controllers also help with custom and prototype PCBs. Highleap Electronic uses fast prototyping to improve designs quickly. This helps companies keep up with market changes and new tech.
Tools like AOI and X-ray checks find problems early, ensuring top performance. Automation makes work precise and repeatable. Real-time data improves production lines for better results.
Evidence Type | What It Shows |
---|---|
Automation | Automated PCB making improves accuracy, speed, and output. |
Automated Optical Inspection (AOI) | Checks PCBs carefully for flaws, ensuring reliable products. |
Real-time Data Analytics | Tracks production live, fixing issues and improving efficiency. |
Using these tools, factories can make custom PCBs quickly and with great quality, meeting customer needs effectively.
The Future of Smart Factory Controllers in PCB Manufacturing
New Trends in Automation and Smart Factories
Smart factories are changing fast with new technology. Tools like AI, robots, and IoT make manufacturing easier and faster. These tools also help make PCBs more accurate and reliable.
Studies show important trends in PCB automation. For example, 64% of manufacturing tasks can now use machines. AI can increase productivity by up to 50%. Also, the robot market using PCBs may grow 40% yearly by 2027.
Trend Description | Statistic |
---|---|
Automatable Manufacturing | 64% of global manufacturing is automatable |
Productivity Improvement | AI algorithms can improve productivity by up to 50% |
Growth of Robot Market | Projected CAGR of 40% by 2027 for robots powered by PCBs |
These trends prove automation is improving electronics production. Using these tools helps factories work faster and stay competitive.
How 5G and Edge Computing Help PCB Assembly
5G and edge computing are making factories smarter. 5G offers speeds up to 20 Gbps, much faster than 4G’s 1 Gbps. This speed helps PCB assembly move quicker and devices connect better.
Better connections also improve reliability and allow new uses in PCB design. For example, 5G’s low delay helps sensors share data instantly. This keeps every step of production smooth.
5G is 20 times faster than 4G, boosting factory speed.
Stronger connections support advanced PCB designs and tools.
Low delay ensures devices and sensors work together perfectly.
Adding 5G and edge computing improves factory performance. It helps meet the needs of modern electronics production.
Future Growth of Smart Factory Controllers
More factories are using smart controllers because of their benefits. Over 63% of manufacturers are investing in automation tools. CNC laser controllers are popular, holding 61% of the market. They are fast and handle complex tasks well.
AI-powered controllers improve precision by 51%. Cloud-based systems are also growing, with 44% of metal companies using them. These tools make factories more efficient and easier to expand.
Touchscreen and remote controllers grew 46% from 2022 to 2024.
AI-driven laser systems improved efficiency by 56%.
Cloud controllers help factories adjust to market changes.
As these tools grow, automation in PCB assembly will improve. Using them now prepares factories for future success.
Smart factory controllers are changing how PCBs are made. They make work faster by using machines to do tasks. These systems cut waste and improve how products turn out. They also show live data to spot problems and fix them quickly. This helps save money, avoid delays, and make better PCBs faster.
Starting with these tools can cost a lot and needs training. But the benefits over time are worth it. Using smart factory controllers helps your business grow and stay flexible. As new tech develops, these systems will become even more important for better and smarter manufacturing.
FAQ
What is a smart factory controller?
A smart factory controller is a tool that automates factory work. It uses IoT, AI, and robots to make tasks faster and easier. These systems help reduce mistakes and improve how products are made. You can watch and control processes live for better results.
How does IoT improve PCB assembly?
IoT links machines, sensors, and systems to share information easily. It helps check assembly lines, find problems early, and do tasks automatically. This saves time, reduces downtime, and makes better PCBs.
Are smart factory controllers expensive to implement?
Yes, they cost a lot at first, between $150,000 and $500,000. But they save money later by cutting waste, speeding up work, and making more products. Starting small can help keep costs manageable.
Can smart factory controllers work with older machines?
Connecting smart controllers to old machines can be hard. Older tools may not work well with new technology. You might need upgrades or changes to make them fit. Experts can help solve these problems.
How do smart factory controllers handle cybersecurity risks?
Smart controllers use strong passwords, updates, and tools to stop cyberattacks. Training workers and improving security plans also help keep systems safe. Regular updates make factories less likely to face threats.
See Also
Enhancing Industrial Automation Efficiency Through PCBA Solutions
Leading Trends Shaping PCBA in Smart Manufacturing by 2025
Exploring AI Advantages in PCB Assembly Operations
Boosting PCBA Production Speed While Maintaining High Quality