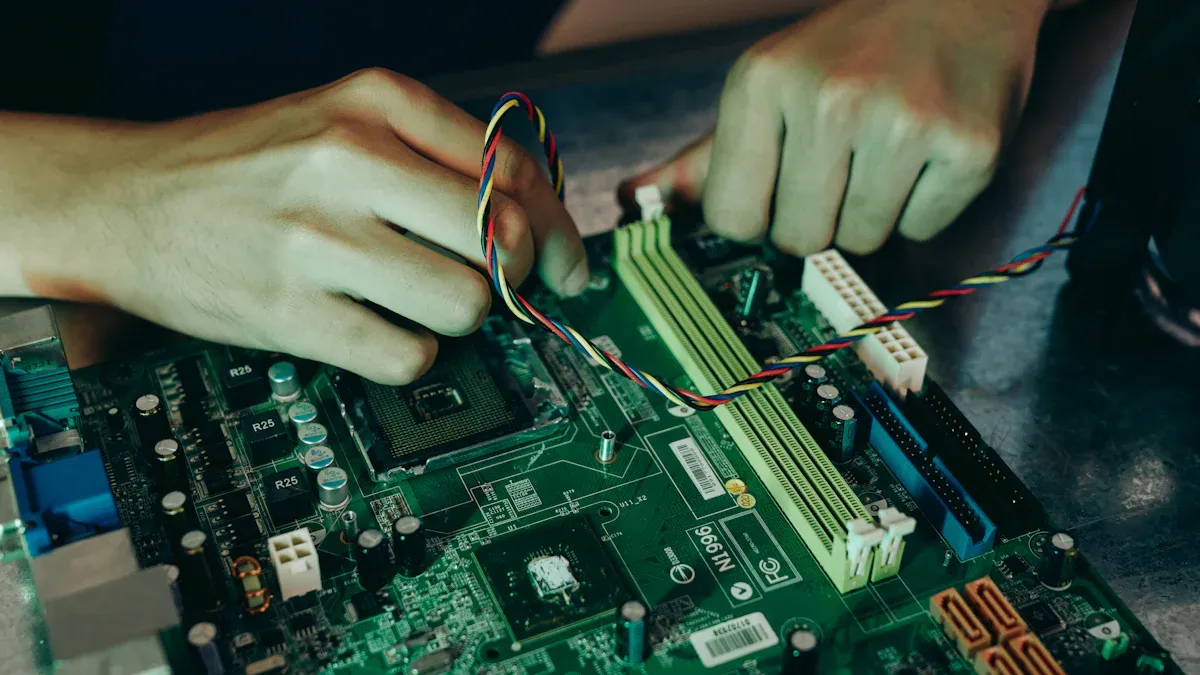
Delivering great products fast is crucial in the realm of circuit boards, especially when it comes to our prototype to production PCBA services. You need speed and accuracy to compete in today’s busy markets. Our company focuses on these needs by making PCBAs in just 24 hours. This quick process helps you design prototype boards faster and transition smoothly from testing to full production.
Industry standards highlight why speed and quality are essential. For example:
Fast delivery helps you meet tight schedules.
Good quality ensures reliable and strong PCBAs.
A customer happiness score of 85% or more indicates approval.
A promoter score over 50 means customers return.
By utilizing advanced methods and striving for excellence, we empower you to succeed in both testing and large-scale production with our prototype to production PCBA services.
Key Takeaways
Quick PCB assembly speeds up product creation. It cuts waiting time for tests, helping fix design mistakes faster.
Good-quality PCBAs are dependable. Careful checks during making stop problems and keep all units the same.
Talking clearly with your PCB maker is important. Clear updates and good support prevent errors and keep work moving.
Using smart machines and better plans makes work faster. These tools lower mistakes and make things run smoothly.
Customer opinions help improve work. Sharing thoughts helps makers do better and deliver on time.
Why speed and quality matter in prototype to production PCBA services
How fast turnaround helps product development and market entry
Quick PCB assembly speeds up product development. It cuts waiting time for testing circuits. This helps find design mistakes faster. Fixing issues quickly means moving from idea to prototype and then production faster.
Tip: Using quick-turn PCBs lets you test ideas early. You can try different parts or layouts without waiting.
Here’s how fast turnaround helps your projects:
Benefit | Description |
---|---|
Faster product timeline | Shorter testing waits mean quicker fixes and progress. |
Lower project risks | Early tests catch design mistakes, saving money and time. |
Better decisions | Real samples allow true performance tests, not just simulations. |
Competitive advantage | Getting to market faster boosts sales and customer trust. |
Quick-turn PCB services also help you adjust to market changes. Cutting production time from weeks to days gives you an edge. Your products reach customers faster.
Why quality is key for prototypes and production
Good quality is vital for reliable PCB assembly. For prototypes, it ensures designs work during testing. For production, it keeps all units consistent and dependable.
Factories use strict quality checks to reduce defects. These include solder tests, circuit checks, and stress tests. Working with manufacturers early helps spot problems. This makes moving from prototype to production smoother.
Evidence | Explanation |
---|---|
Strong testing | Tests mimic real-world use to find flaws. |
Consistent quality | Reliable prototypes meet high standards every time. |
Industry compliance | Following rules ensures quality and reliability. |
Focusing on quality avoids costly mistakes. It ensures your PCB services meet both functional needs and industry rules.
The challenge of balancing speed and quality in PCBA
Keeping both speed and quality in PCB assembly is tough. Rushing can hurt quality. To fix this, factories use advanced tools, better workflows, and strong supply chains.
Prototypes check basic functions cheaply. Production needs strict quality checks for reliability. This balance keeps both speed and quality high.
Note: Watching and testing during production finds problems early. Fixing them quickly ensures good results without delays.
By solving these challenges, you can move smoothly from prototype to production. Tight deadlines can still be met with great results.
Processes and technologies driving fast PCB assembly services
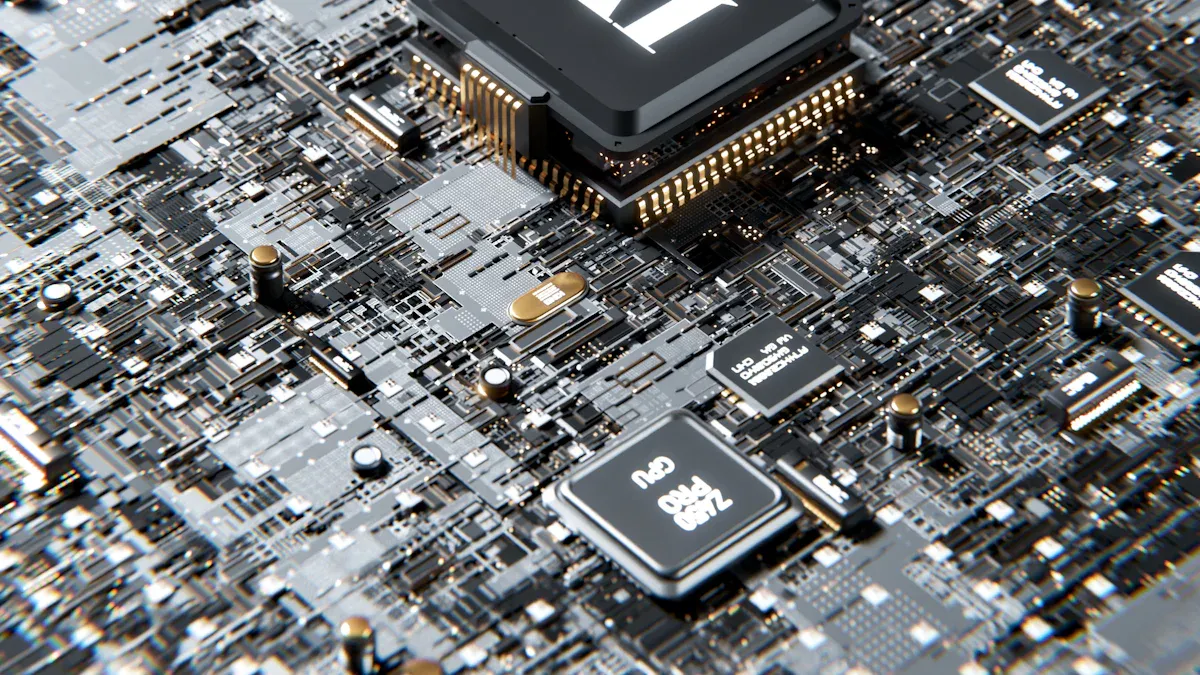
Modern machines and automation for faster production
Today’s PCB assembly uses smart machines and automation for speed. These systems handle tasks like applying solder paste, placing parts, and checking for errors. They reduce mistakes and make sure results are consistent, even for tricky designs.
Automation brings clear benefits:
Automated systems cut energy use by 40% and PCB waste by 60%.
Apple saved 35% on energy and boosted product output by 20% with automated testing.
Siemens reduced material waste by 50% and improved efficiency by 30% using robotic tools.
Using these technologies helps make quick PCBs with great quality. It also cuts waste and saves energy. This keeps your PCB-making process smooth and dependable.
Better workflows for faster and smoother production
Improved workflows are key to speeding up PCB production. By making each step better, manufacturers avoid delays and work faster. For instance, automated checks catch mistakes early, so less fixing is needed later.
Here’s how better workflows help PCB assembly:
Benefit Description | Quantified Impact |
---|---|
Fewer errors found by manual checks | Over 90% fewer errors |
Coplanarity issues | Fully removed |
Time saved in manual inspections | Hours saved per job |
Money saved per production run | $200–250 saved in costs |
These changes save time and money. They also let you focus on improving your PCB designs. Better workflows ensure quick services deliver reliable results, even with tight deadlines.
Smart supply chains for meeting tight schedules
A good supply chain is key for fast PCB assembly. Smart supply chain plans keep parts flowing, so production stays on track. Making lots of units at once lowers costs and boosts efficiency.
Important strategies include:
Building strong ties with suppliers for steady part supplies.
Improving processes to shorten wait times for big orders.
Speeding up prototyping to move from design to testing faster.
Using fast-turn flex PCB methods to support quick changes and updates.
These plans help you adjust to new needs and deliver great PCBs on time. By focusing on supply chains, you can handle tough projects and meet deadlines with ease.
Quality assurance in 24-hour PCBA production
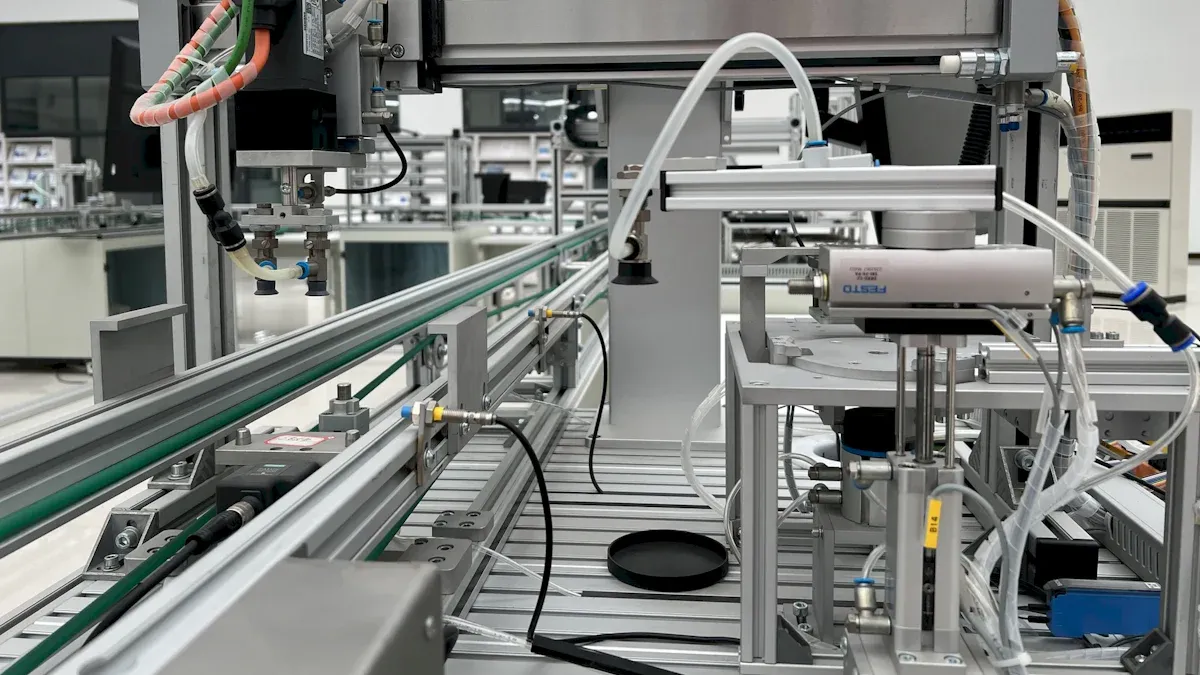
Making high-quality PCBAs in 24 hours needs strong quality checks. By using strict tests, following industry rules, and watching production closely, you can make sure the results are reliable and efficient.
Testing protocols to ensure high-quality PCBAs
Testing is key to keeping quality during PCB产品 assembly. It makes sure every board meets standards and customer needs. Finding problems early reduces waste and saves time and money. Testing also ensures the final product works well in real-life use.
Evidence Description | Impact on PCBAs |
---|---|
PCB testing ensures compliance with industry standards and client preferences. | This leads to the production of safe, reliable, and high-performing PCBAs. |
Early identification of issues during manufacturing minimizes rework and scrap. | This optimizes production efficiency and reduces costs associated with defective components. |
Testing guarantees product quality that meets or exceeds customer requirements. | Enhances customer satisfaction by providing fail-proof electronic products tailored to diverse needs. |
Popular testing methods include in-circuit testing (ICT) and automated optical inspection (AOI). These tests find problems like bad soldering, misplaced parts, or electrical errors. Using these methods checks quality at every step and ensures good results.
Tip: Testing often during production helps catch and fix issues early. This ensures high-quality PCBAs without delays.
Certifications and compliance with industry standards
Certifications prove your PCB产品 process meets global quality rules. They show you are committed to making safe and reliable products. Important certifications include:
Certification | Description |
---|---|
AS9100 | Aerospace standard based on ISO 9001, ensuring compliance with DOD, NASA, and FAA quality requirements. |
ISO 9001 | Ensures organizations provide high-quality products and services, with certification demonstrating adherence to quality management principles. |
JOSCAR | A collaborative tool for the aerospace, defense, and security industry to verify supplier compliance and pre-qualification. |
UL Certification | Indicates that PCBs meet safety and performance standards, ensuring reliability and safety in electronic products. |
These certifications not only prove your processes are good but also build customer trust. They ensure your products follow rules and work well in different conditions.
Note: Keeping certifications like ISO 9001 and AS9100 helps you check quality and meet top industry standards.
Continuous monitoring and quality control measures
Watching production all the time is important for quality. By tracking steps and data, you can fix problems early. Good quality control includes:
Etching: Checking temperature and speed for the best results.
Lamination: Managing pressure and heat to avoid mistakes.
Drilling: Measuring during drilling to prevent errors.
Plating: Watching thickness and stickiness to catch issues.
Solder Mask: Controlling coating thickness to stop defects.
Soldering: Checking heat levels for strong solder joints.
Smart tools like Statistical Process Control (SPC) help track data live. This finds patterns and reduces mistakes, making production better. Numbers like First Pass Yield (FPY) and defect rates show quality. Low defects and high FPY mean stable and good production.
Callout: Using methods like Lean Manufacturing and Six Sigma improves quality and innovation. These help you make great PCBAs every time.
By combining strict tests, certifications, and constant checks, you can ensure top quality in 24-hour PCBA产品 production. These steps make sure your products meet customer needs and industry rules every time.
Expertise and experience: The foundation of the best PCB manufacturer
Skilled engineers and technicians optimizing production
The best PCB产品 makers depend on skilled workers. Engineers and technicians with years of experience make production faster and better. Engineers with over 10 years of work and technicians with 5 years of practice bring valuable skills. They often update rules to improve PCB产品 safety and quality.
Important quality checks include:
FAI (First Article Inspection): Confirms accuracy before making many boards.
ICT (In-Circuit Test): Checks if the PCB产品 works after soldering.
AOI (Automated Optical Inspection): Finds visual problems automatically.
SPI (Solder Paste Inspection): Ensures solder paste is applied correctly.
Drop Test: Tests how strong the PCB产品 is when dropped.
These checks, along with expert workers, ensure every PCB产品 is reliable and high-quality.
Leveraging years of experience for reliability and consistency
Experience helps the best PCB产品 makers stand out. Years of learning improve processes and ensure great results. Buying in bulk and working well with suppliers make material sourcing easy. Clear instructions prevent mistakes, and early testing finds problems fast.
Aspect | Description |
---|---|
BOM Review | Uses bulk buying and supplier ties for smooth sourcing. |
Documentation | Keeps instructions clear to avoid mistakes during production. |
Testing | Uses early testing to catch and fix problems quickly. |
This mix of experience and smart methods builds trust. It ensures the manufacturer delivers reliable PCB产品 services for your projects.
How expertise ensures seamless prototype to production transitions
Expertise makes moving from prototype to production easy. Focusing on simple debugging during prototypes ensures smooth production later. Experts find problems early, saving time and money. Efficient processes reduce delays between prototype and production stages.
Benefit | Description |
---|---|
Streamlined Path from Concept to Volume Production | Speeds up the process from design to delivery using popular tools. |
Expert Design Optimization Services | Spots design issues early to avoid delays in manufacturing. |
Guaranteed Speed and Consistent Quality | Improves production steps and checks quality to meet deadlines. |
With expert help, the best PCB产品 makers ensure smooth transitions. They deliver top-quality results on time for every project.
Customer support and communication in a top PCB assembly company
Easy and quick communication with clients
Good communication is key to working well with a PCB company. Clear and fast updates help you understand your project better. They also reduce mistakes, improve designs, and make products more reliable.
Here’s why clear communication helps:
Sets clear goals for the project.
Improves details to avoid costly errors.
Solves problems faster through teamwork.
Helps you make smart design choices.
Prepares you for challenges to lower risks.
At JHYPCB, we focus on being helpful and easy to reach. Our team answers questions within 24 hours. Each client gets a dedicated manager for smooth communication.
Good communication isn’t just about being nice—it helps your project succeed. Clear updates stop errors, quick replies meet deadlines, and support helps handle problems better.
Live updates and tracking progress
Live updates are important when working with a PCB company. They let you see progress and fix problems quickly. Dynamic Process Control (DPC) systems make this possible.
DPC finds issues early and fixes them fast.
It cuts waste and improves quality checks.
The system gives accurate data to track progress.
With live updates, projects run smoother and finish on time. This openness keeps your project on track and meets your needs.
Using feedback to improve and meet deadlines
Customer feedback helps make services better. When you share your thoughts, it improves processes and quality. Feedback shows what needs fixing so the company can meet your needs.
By sharing your experience, you help improve workflows and speed up delivery. Your input helps find delays and fix them. This teamwork ensures you get great PCBAs on time, every time.
Making high-quality PCBAs in 24 hours needs key steps. These include getting parts quickly, smooth assembly, and smart designs. The table below shows the main points that make this happen:
Factor | Description |
---|---|
Total Components | More parts can make assembly take longer. |
Component Types | Some parts, like through-hole, are harder to assemble than SMT. |
Assembly-Friendly Design | Easy-to-assemble designs lower mistakes and speed up work. |
Part Availability | Ordering parts while making PCBs saves time. |
Focusing on these steps helps make PCBAs faster and still high-quality. We aim for speed, accuracy, and happy customers to help you succeed.
FAQ
What is the quickest way to get a PCBA prototype?
Use a 24-hour fast-turnaround service for quick prototypes. This service delivers your prototype fast without losing quality. Manufacturers use better workflows and smart machines to meet tight deadlines.
Tip: Send your design files early to speed things up.
How is quality ensured in such a short time?
Manufacturers use automated tests and strict quality checks. They also monitor production in real-time to fix problems fast. Certifications like ISO 9001 and AS9100 ensure they follow industry rules.
Can I check my PCBA order progress?
Yes, many manufacturers offer live updates. Systems like Dynamic Process Control (DPC) let you track production steps. This keeps you informed and helps solve issues quickly.
What affects the 24-hour turnaround time?
Things like design complexity, parts availability, and order size matter. Simple designs and having parts ready can help meet deadlines.
Note: Share clear requirements to avoid any delays.
Are 24-hour PCBAs good for large production?
Yes, but they work best for prototypes or small orders. Large-scale production may need more time to keep quality consistent.
See Also
Achieving Superior Quality Through Advanced PCBA Manufacturing Techniques
Understanding Key Differences Between Prototype and Production PCBs
Comparing Turnkey and Consignment PCBA Manufacturing Approaches
How to Choose the Ideal PCBA Manufacturer for You
Essential Soldering Techniques for Precision PCB Assembly Today