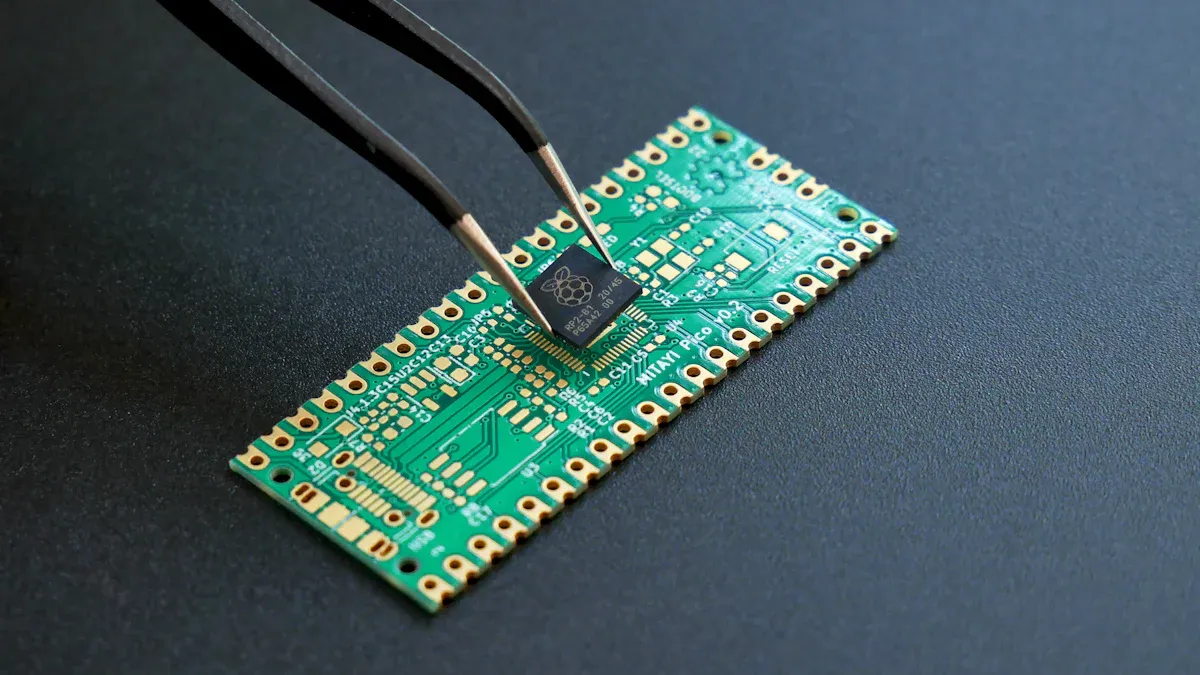
Mixed technology PCBA manufacturing uses two methods: SMT and THT. These methods work together to build one printed circuit board. This process helps make devices with small parts and strong connections.
Modern electronics depend heavily on this method. In 2023, the PCB and PCBA market was worth $68.4 billion. By 2032, it is expected to grow to $105.8 billion. This growth shows the need for smaller, better electronics in industries like cars and gadgets. Mixed technology PCBA helps create advanced designs and dependable devices.
Key Takeaways
Mixed technology PCBA uses SMT and THT to build strong circuit boards.
Combining SMT and THT helps create designs with small and big parts.
This method makes devices reliable for industries like cars, planes, and healthcare.
Mixed technology PCBA saves time and money while keeping devices high quality.
The need for better electronics shows why mixed technology is important today.
What is Mixed Technology PCBA Manufacturing?
Definition and Purpose
Mixed technology PCBA manufacturing combines SMT and THT on one circuit board. This method uses different parts like SMDs, through-hole components, and BGAs. By mixing these methods, it creates precise and strong connections. These are important for today’s electronics.
The goal of mixed technology is to fix the limits of using just one method. SMT is great for small, light parts placed with accuracy. THT is better for bigger, heavier parts needing strong support. Together, they make boards that are both detailed and sturdy. This makes mixed assembly perfect for reliable and flexible devices.
SMT vs. THT in PCB Assembly
SMT and THT are the main ways to build circuit boards. Each has special features for different uses:
SMT (Surface Mount Technology):
Parts are placed on the board’s surface.
Best for tiny, light parts like resistors and chips.
Allows small designs and fast automated production.
Used in phones, IoT gadgets, and small electronics.
THT (Through-Hole Technology):
Parts have leads that go through board holes.
Strong bonds make it good for heavy or powerful parts.
Found in industrial tools, power systems, and cars.
Using both SMT and THT combines their strengths. SMT handles small, detailed parts, while THT adds strength for key components.
Advantages of Combining SMT and THT
Mixing SMT and THT gives many benefits for better PCBA results:
Versatility in Component Selection:
Mixed assembly uses all kinds of parts, from tiny to strong. This helps make complex and multi-use boards.Improved Performance:
SMT parts work well for fast and detailed tasks. THT parts add strength for heavy-duty jobs. Together, they make balanced boards.Enhanced Reliability:
Mixing SMT and THT makes boards tough against stress and harsh conditions. This is great for cars and planes.Cost and Time Efficiency:
Combining both methods saves time and money in production. It keeps quality high while speeding up the process.Support for Advanced Applications:
Modern devices like LED lights and IoT tools need mixed assembly. It helps make products faster and ready for scaling.
By using SMT and THT, mixed technology PCBA builds strong and flexible devices. It balances precision and strength, making it a top choice for many industries.
How Does Mixed Technology PCBA Manufacturing Work?
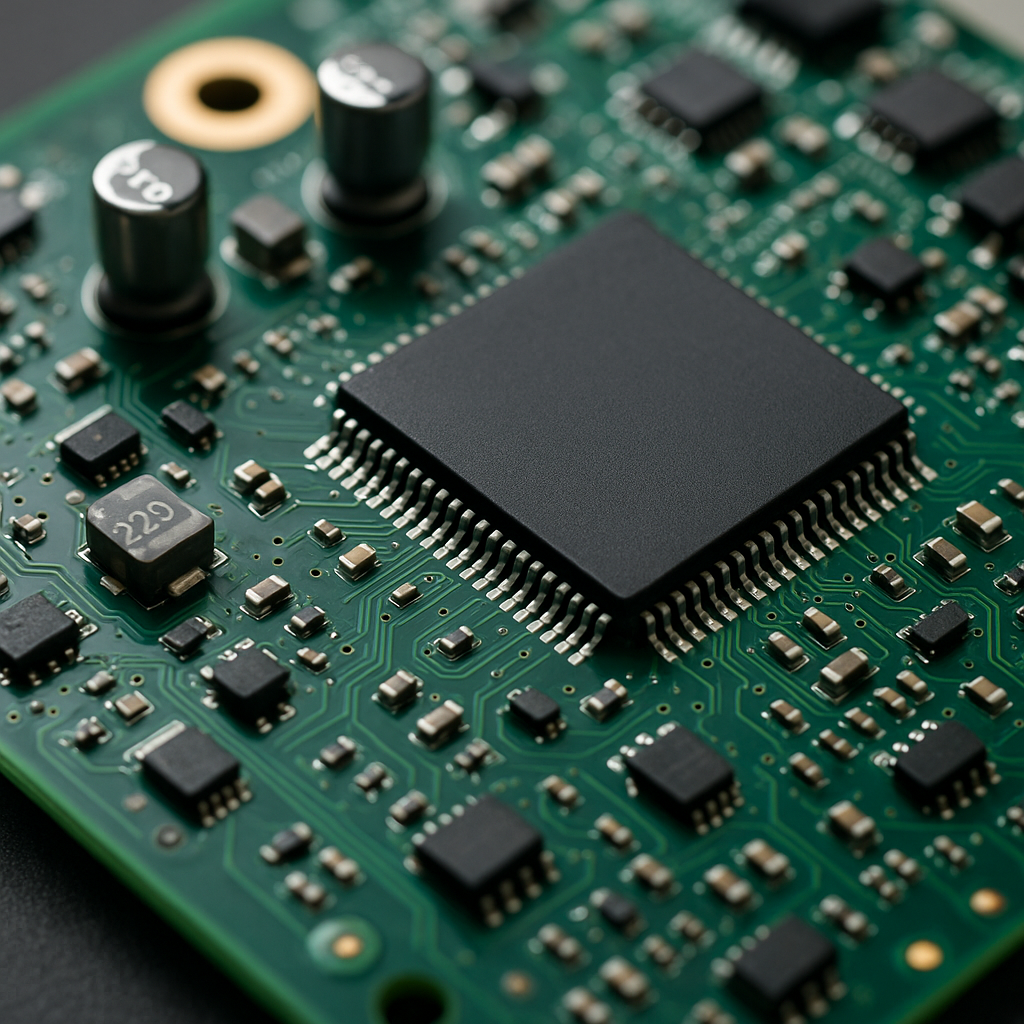
Combining SMT and THT Methods
Mixed technology PCBA uses SMT and THT together in one process. SMT places tiny parts on the board’s surface. THT adds parts with leads through holes in the board. These methods work together to make boards that are both precise and strong.
In most PCBA processes, SMT parts are added first because they are small and easy to place with machines. After soldering, THT parts are added by hand or with machines. This mix allows the assembly to handle both light and heavy parts. It is perfect for industries like cars and airplanes.
Parts Used in Mixed Technology Assembly
Mixed technology assembly uses many types of parts, each with a special job:
SMT Parts:
These include small items like resistors and chips. They are great for tight spaces in gadgets like phones.THT Parts:
Bigger parts like connectors and power modules fit here. They are strong and used in machines and medical tools.Hybrid Parts:
Some parts, like BGAs, mix SMT and THT features. These are used for advanced designs in mixed assemblies.
By using both SMT and THT, mixed technology PCBA can handle many parts. This makes it flexible and useful for different needs.
Problems in the Process
Mixed technology assembly has some challenges that need careful planning. Problems like slow work and delays can happen during the process. For example, Rockwell Automation found issues like too many parts being prepared and poor tracking of materials. Manual tracking also caused delays and slowed changes.
To fix these problems, Rockwell Automation used smart tools for real-time tracking. They replaced manual work with dashboards, improving labor efficiency by 25%. They also cut inventory and changeover times by 30%.
These examples show why advanced tools are important. By using automation and smart systems, you can solve problems and make the PCBA process better.
Steps in Mixed Technology PCBA Manufacturing
Solder Paste Application
The first step is applying solder paste to PCB pads. A stencil is used to place the paste in the right spots. This stencil is laser-cut to match the board’s design. The paste contains solder and flux, which help make strong connections.
Before use, every stencil is carefully checked for quality. The paste is printed only on areas where parts will go. This step is very important because uneven paste can cause problems later.
Tip: Keep solder paste in a cool place to keep it effective.
SMT Component Placement
Next, surface-mounted parts are placed on the board. Automated machines pick and place these parts onto the soldered pads. These machines follow designs made with special software for accuracy.
Parts are chosen from the Bill of Materials (BOM) and kept safe in dry cabinets. The machine picks each part and places it quickly and precisely. This step is great for small, detailed boards.
Note: Check the first board after placement to ensure everything is correct.
Reflow Soldering
Reflow soldering connects the parts to the board. The board goes through a reflow oven, which heats it carefully. The solder paste melts and sticks the parts to the board.
The oven has zones with different temperatures for smooth heating and cooling. This stops the board and parts from getting damaged. Good reflow soldering is key for strong connections.
Tip: Watch the oven’s heat settings to avoid mistakes in soldering.
THT Component Insertion
THT insertion means putting parts into drilled holes on the PCB产品. This can be done by hand or with machines. Each part must fit perfectly into its assigned hole. Common parts include connectors, capacitors, and others needing strong support.
In mixed assembly, THT comes after the SMT process. This order ensures small parts are secure before adding bigger ones. THT is often used for parts handling high power or stress. This step is key to making a strong and lasting PCBA产品.
Tip: Check the direction of polarized parts like diodes and capacitors. Wrong placement can cause problems in the final board.
Wave or Manual Soldering
After THT parts are placed, soldering is the next step. Wave soldering is common for this. The PCB产品 moves over molten solder, which sticks to leads and pads. This method is fast and works well for large batches.
For smaller jobs or tricky designs, manual soldering is better. A soldering iron is used to connect each lead to its pad. Mixed assembly often uses both methods, depending on the board’s design.
Note: Use the right soldering temperature for the materials. Too much heat can harm the PCB产品 or parts.
Inspection and Testing
Inspection and testing are the last steps in mixed assembly. These steps check if the PCBA产品 works and meets quality standards. Automated Optical Inspection (AOI) finds soldering mistakes or misaligned parts. AOI uses cameras and software to spot issues quickly.
Functional testing is also important. This tests if the board works as it should. For mixed assembly, special tools may be needed to test both SMT and THT parts. Careful inspection and testing ensure reliable, high-quality products.
Tip: Keep records of test results to find and fix repeated problems.
Benefits of Mixed Technology PCBA Manufacturing
Versatility in Design
Mixed technology assembly allows for flexible electronic designs. It uses both SMT and THT methods together. SMT parts make small and light designs possible. THT parts add strength for high-power needs. This mix works well for many products, like IoT gadgets and machines.
The layout of mixed PCBs helps save space on the board. It also reduces the need for many product versions. This is useful for complex devices like CPUs and communication tools. These designs need both space-saving and reliable performance.
Cost-Effectiveness
Mixed technology assembly helps lower costs in making PCBs. Using SMT and THT together reduces the number of parts needed. Automated SMT placement cuts labor costs. THT adds strength, so repairs or replacements are less frequent.
This method also improves production speed. Combining machines and manual work fits different production sizes. It keeps quality high while saving money. This makes mixed PCB assembly a smart choice for small and large projects.
Enhanced Reliability
Mixed PCB assembly makes strong and dependable electronic boards. SMT parts are precise and efficient. THT parts are tough and handle stress well. Together, they create boards that work in tough conditions, like cars and planes.
Using machines for SMT and hands for THT ensures accuracy. This mix secures every part and lowers failure risks. Reports show more demand for reliable electronics, boosting mixed technology use. This proves its value in today’s manufacturing.
Note: Mixed PCB assembly is key to making strong, efficient devices. It meets the needs of modern technology.
Support for complex assemblies
Mixed technology PCBA is great for handling complex assemblies. It combines SMT and THT methods to manage different parts easily. This method works well for hybrid assemblies needing both precision and strength.
Hybrid assemblies use small SMT parts and strong THT parts. For instance, SMT chips are good for fast processing. THT connectors are better for steady power. Mixing these methods ensures each part works perfectly in its role.
Complex designs also benefit from mixed technology’s flexibility. You can add advanced parts like BGAs or hybrid components. These are important for high-performance devices like communication tools or factory machines.
Tip: Plan your PCB layout carefully for hybrid assemblies. This saves space and helps fit SMT and THT parts smoothly.
Mixed technology also makes production easier for tricky designs. Machines place SMT parts quickly, while THT parts are added by hand for accuracy. This mix lowers mistakes and makes the final product more reliable.
With mixed technology, you can handle complex assemblies confidently. It offers the tools to build modern, advanced electronics that meet today’s needs.
Applications of Mixed Technology PCBA
Consumer Electronics
Mixed technology PCBA is important for making consumer electronics. It helps create small and efficient devices by using both surface-mounted and through-hole parts. This technology is found in smartphones, tablets, and wearables. These gadgets need tiny, light parts for easy carrying and strong parts for lasting use.
The need for better PCB solutions is growing fast. In 2024, the PCB Design and Layout Service Market was worth USD 2.2 billion. By 2033, it is expected to grow to USD 4.5 billion, with an 8.5% yearly growth from 2026 to 2033. This shows how hybrid assembly is needed to meet the changing demands of consumer electronics.
Tip: Mixed technology PCBA keeps devices reliable and supports creative designs.
Automotive Systems
Cars depend on mixed technology PCBA for advanced features. It is used in systems like ADAS, infotainment, and engine control units (ECUs). These systems combine small processors with powerful parts for reliability and performance.
Mixed assembly also helps with monitors, controls, and navigation tools. For example, radar monitors help avoid blind spots, and GPS gives accurate directions. Hybrid assembly makes these systems precise and tough, perfect for the challenges of cars.
Note: Hybrid assembly makes vehicles safer and improves driving experiences.
Aerospace and Defense
Aerospace and defense need reliable systems for tough conditions. Mixed technology PCBA combines strong through-hole parts with precise surface-mounted ones. It is used in communication tools, radar systems, and navigation devices for planes and military use.
Studies show its reliability. Silicone-based fillers work well in high heat, keeping performance steady. Careful cleaning stops tin whiskers, which can harm PCBAs. These steps make hybrid assemblies great for aerospace and defense, where reliability is key.
Tip: Mixed technology PCBA ensures systems work well in extreme conditions.
Industrial Machinery
Mixed technology PCBA is key for industrial machines. It is used in tools needing both accuracy and strength. Manufacturing, robotics, and automation systems depend on hybrid assembly to work well. These machines need small parts for control and tough parts for power.
For instance, robots use surface-mounted sensors to track movements. They also use through-hole connectors to manage high power. Hybrid assembly helps these machines work reliably in hard conditions. It supports features like live monitoring and automatic changes, boosting efficiency.
Heavy-duty tools like CNC machines and conveyor belts also use this technology. These tools need strong PCBs to handle heat, shaking, and long use. Hybrid assembly designs boards to meet these needs. It mixes SMT and THT for a balance of accuracy and durability.
Tip: Focus on heat control when designing PCBs for machines. This keeps them working well in hot conditions.
Medical Devices
Medical devices need to be very reliable and accurate. Mixed technology PCBA helps by using SMT and THT together. Devices like pacemakers, pumps, and testing tools use hybrid assembly to meet strict rules.
In testing tools, SMT parts process data fast. THT parts give steady power connections. Hybrid assembly makes sure these devices work well and last long. Portable devices like glucose monitors also use this method. It helps make small designs that are still strong.
Hybrid PCBs are also used in surgery tools and imaging systems. These tools must work perfectly to keep patients safe. Hybrid assembly helps design boards that meet these important needs.
Note: Always check quality carefully when making PCBs for medical tools. This ensures they meet industry rules.
Design and Assembly Considerations
PCB Layout Optimization
A good PCB layout helps with smooth assembly and performance. Following simple rules can stop problems like overheating or signal issues.
Keep enough space between parts to avoid electrical problems.
Make trace width and spacing fit the current for better signals.
Place vias smartly to improve heat flow and signal quality.
Group similar parts together to make routing easier.
Add clear labels and markings for easy assembly and fixing.
Mark areas to avoid placing parts where interference may happen.
These steps help design boards for both surface-mounted and through-hole parts. This is very helpful for hybrid assembly, where accuracy and strength matter.
Tip: Follow manufacturing rules to match your design with production needs.
Component Placement Strategies
Placing parts well is key for hybrid assembly. It reduces wiring problems and boosts performance. Real-world examples show how to do this:
Case Study | Key Results | Main Strategies |
---|---|---|
Medical Device Maker | 30% faster market time, 25% lower inventory costs, 15% better product quality | Modular lines, advanced inspections, flexible teams |
Aerospace Electronics Company | 40% less setup time, 20% better equipment use, 35% more on-time deliveries | Lean methods, smart scheduling, quick-change tools |
You can use these ideas by grouping parts by their job and placing them evenly. Put important parts near power or signal paths to avoid problems. For hybrid designs, place surface-mounted parts for machine use and through-hole parts for hand placement.
Note: Using modular lines and advanced tools can improve your assembly process.
Thermal Management
Controlling heat is important for a working PCB. Heat-making parts need careful placement to stop overheating.
Keep hot parts away from sensitive ones to avoid damage.
Use thermal vias to spread heat across the board.
Add heat sinks or cooling systems for high-power parts.
Design the layout to allow airflow around key parts.
Hybrid assembly needs smart heat control. Surface-mounted parts usually make less heat, but through-hole parts may need extra cooling. Balancing these needs ensures the board lasts longer.
Tip: Test your PCB in real conditions to find and fix heat problems early.
Quality control protocols
Quality control makes sure hybrid assemblies meet high standards. It checks each step to find mistakes early. Following strict rules helps create reliable and efficient PCBs.
Automated Optical Inspection (AOI):
AOI uses cameras and software to look for defects. It finds missing parts, solder problems, and alignment issues. This method is quick and accurate, perfect for hybrid assemblies.X-ray Inspection:
X-rays check hidden solder joints in complex designs. They work well for hybrid boards with BGAs or advanced parts.Functional Testing:
Functional tests check if the PCB产品 works correctly. Simulating real-world conditions shows how it performs. This step is key for medical devices or aerospace systems.Environmental Stress Testing:
Stress tests expose the PCB产品 to extreme conditions. These include heat changes, shaking, and moisture tests. They ensure the hybrid assembly can handle tough environments.
Tip: Keep records of test results. This helps fix problems and improve designs.
Using these steps ensures quality and reduces failures. Hybrid assemblies need extra care because they mix different methods. Careful testing makes sure the product meets industry rules and customer needs.
Mixed technology PCBA is important for today’s electronics. It mixes accuracy and strength to make reliable products. This method helps new ideas by using advanced tools like AI and IoT.
Smart tools help companies work faster and save money.
Using these methods keeps businesses strong in a changing market.
By using mixed technology, you can handle tricky designs. It helps meet the need for better, stronger devices. This way, your products stay useful, tough, and future-ready.
FAQ
What is the main purpose of mixed technology PCBA manufacturing?
Mixed technology PCBA uses SMT and THT together. This makes boards that are both flexible and strong. It lets you use tiny, precise parts and tough, durable ones on one board. This method helps create advanced designs and ensures great performance.
How do SMT and THT differ in their applications?
SMT is best for small, light parts like chips and resistors. THT works well for bigger, heavier parts like connectors and power modules. Together, they meet many electronic needs.
What industries benefit the most from mixed technology PCBA?
Industries like cars, planes, gadgets, and medical tools use mixed technology PCBA. It helps with complex designs, makes devices last longer, and meets high-performance needs.
Tip: For tough environments, mixed technology adds extra reliability.
What challenges might you face in mixed technology PCBA?
You might face problems like slow work, tracking issues, or alignment mistakes. Using smart tools and real-time tracking can fix these and make work faster.
Can mixed technology PCBA reduce production costs?
Yes, it can save money. SMT machines lower labor costs, and THT makes boards stronger, cutting repair needs. Mixing these methods speeds up work and reduces waste, saving money over time.
Note: Plan your design well to save the most money.
See Also
Achieving Superior Quality Through Effective PCBA Manufacturing Strategies
Comparing Turnkey And Consignment PCBA Manufacturing Approaches 2025
Speeding Up PCBA Production While Maintaining High Standards
Ensuring Smooth Transition From Prototype To PCBA Production
Comprehensive Quality Control Throughout The Entire PCBA Manufacturing Process