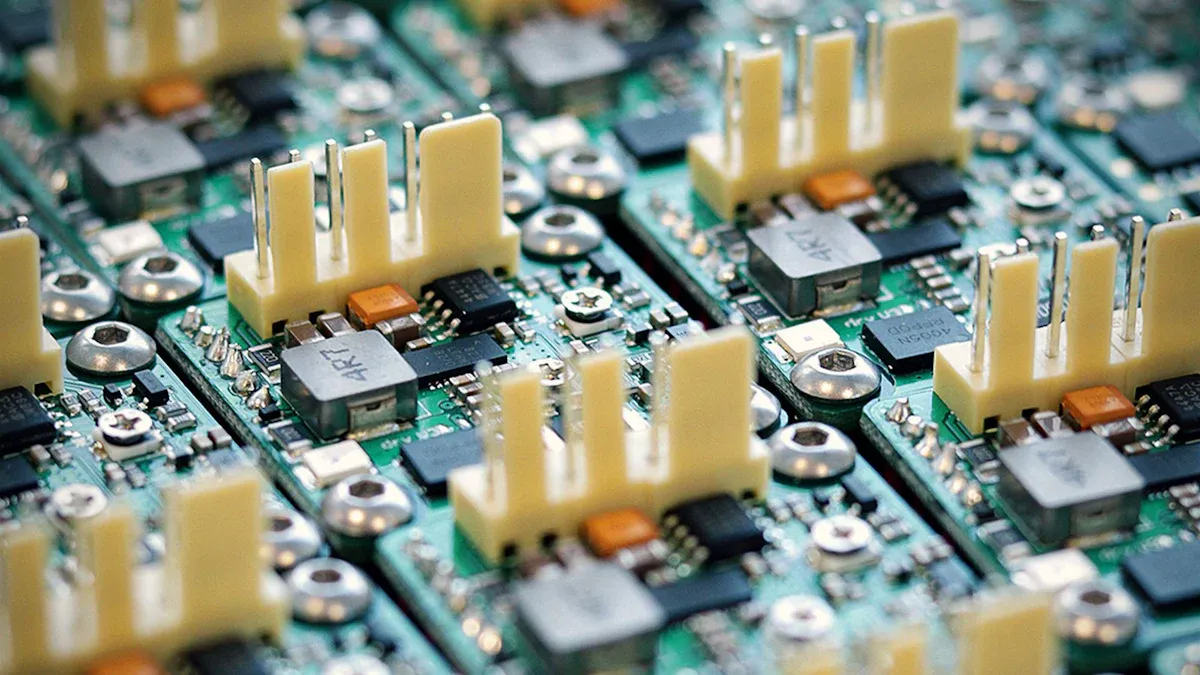
Ball Grid Array (BGA) and micro-BGA assembly services are essential for connecting chips to circuit boards. These techniques utilize small solder balls instead of pins, providing strong connections and compact designs. As a result, devices can operate more efficiently while saving valuable space.
By 2025, the demand for these assembly services is expected to increase significantly. Consider these statistics:
The BGA packaging market is projected to grow from $3.65 billion in 2024 to $7.08 billion by 2034, with an annual growth rate of 6.84%.
The outsourced chip assembly and testing market is anticipated to rise from $42.84 billion in 2024 to $46.87 billion in 2025, reflecting a growth rate of 9.4% each year.
These figures highlight the crucial role that BGA and micro-BGA assembly services play in driving innovation across various industries. They enhance the durability of devices against heat and movement, which is vital for the advancement of technology.
Key Takeaways
BGA and micro-BGA services help make small, efficient gadgets.
More people will use BGA technology as it becomes popular.
Micro-BGA works better with electricity and handles heat well.
Using BGA or micro-BGA improves how devices work and last.
Good tools are needed to build and check BGA assemblies.
Understanding BGA and Micro-BGA Assembly Services
Overview of BGA technology
Ball Grid Array (BGA) technology changed how chips connect to circuit boards. Instead of using pins, it uses tiny solder balls in a grid. These solder balls link the chip to the board both electrically and physically.
BGA has many benefits. It improves how signals travel by reducing interference. Its small size also helps devices stay cool, making them more reliable. This is why BGA is popular in devices like smartphones, gaming systems, and powerful computers.
The global semiconductor market shows how important BGA is. In 2023, assembly services made up 64.44% of the market. This growth is due to the need for high-performance devices. Companies like Advanced Semiconductor Engineering Inc. and Amkor Technology Inc. lead this market by keeping up with new technology.
Introduction to Micro-BGA and its unique features
Micro-BGA (μBGA) builds on BGA’s benefits but is even smaller. It’s perfect for devices where space is limited. Micro BGA packages have a pitch of 0.4mm or less, making them tiny and easy to fit on boards. This design works well for wearables, IoT devices, and medical tools.
Micro BGA also boosts electrical performance. It reduces signal loss and speeds up data transfer. However, designing boards for micro BGA is tricky. The small pitch, sometimes just 0.25mm, needs precise tools and advanced methods.
Micro BGA isn’t just about size; it also handles heat better. The smaller solder balls and tight spacing help remove heat efficiently. This is important for devices that get very hot during use.
Key differences between BGA and Micro-BGA
BGA and micro BGA are similar but have key differences:
Feature | BGA | Micro-BGA (μBGA) |
---|---|---|
Pitch Size | Usually 0.8mm or larger | 0.4mm or smaller |
Package Size | Bigger, for general use | Smaller, for tight spaces |
Electrical Performance | Good | Better, with less signal loss |
Thermal Management | Works well | More efficient for heat control |
PCB Design Complexity | Moderate | High, needs advanced tools |
Micro BGA is best for small, high-performance devices but needs precision. BGA is easier to use and works for many applications. Knowing these differences helps you pick the right one. Both BGA and micro BGA meet the needs of today’s electronics.
Benefits of BGA and Micro-BGA Assembly
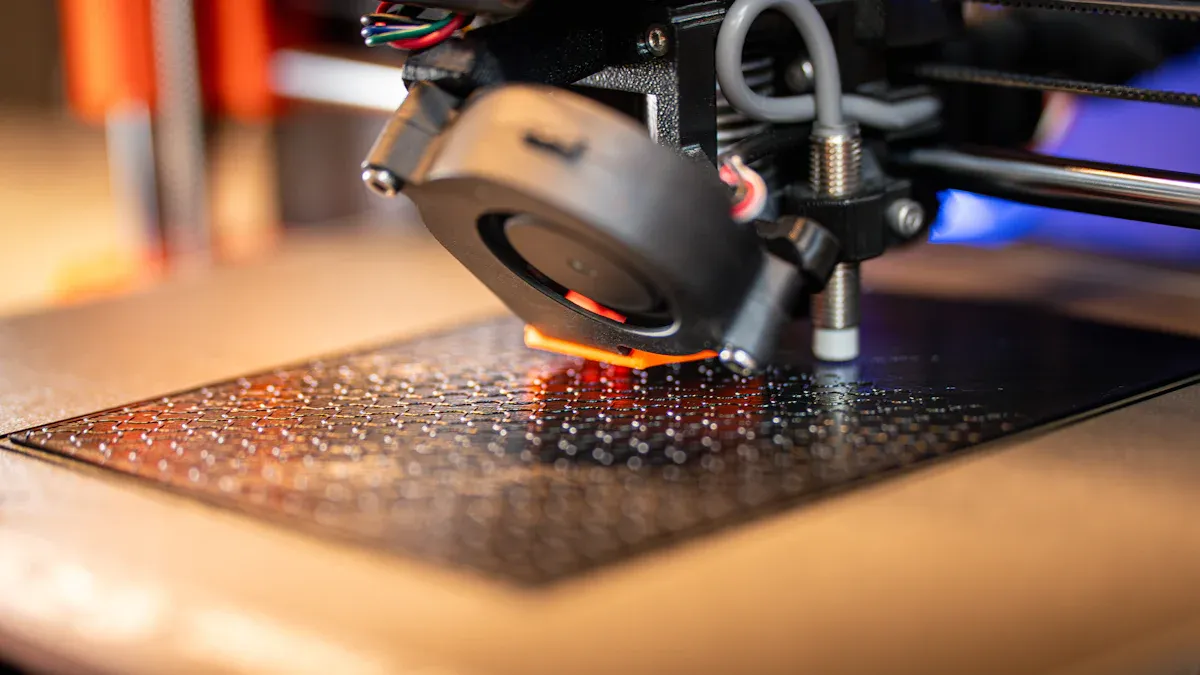
Better performance and faster data processing
BGA and micro-BGA help electronics work better and faster. These technologies cut down signal problems, making devices process data quickly and accurately. For example, routers and switches use BGA to handle 5G and cloud computing demands. They process data faster and use less energy, making them more efficient.
In cars, BGA helps control units manage heat and work reliably. Electric vehicles depend on BGA to perform well in tough conditions. Servers for cloud computing also use BGA to save power and fit more computing power in less space. These features make BGA important for many industries needing high-performing devices.
Smaller designs for tight spaces
BGA and micro-BGA are great for saving space in electronics. Instead of pins, they use solder balls, which make parts smaller. This is helpful for wearables like smartwatches and fitness trackers. Micro-BGA lets these devices stay small but still powerful.
Other devices also benefit from compact BGA designs. Car systems like ADAS and infotainment units use BGA to fit more features in small spaces. Smartphones and tablets use BGA to pack more functions into thinner designs. This space-saving feature makes devices lighter and easier to carry without losing performance.
Better heat control and reliability
Managing heat is important for electronics, and BGA does this well. The solder balls in BGA packages help remove heat, stopping parts from overheating. This keeps devices working even during heavy use. Car control units use BGA to handle heat in hot environments.
Wearables like smartwatches use micro-BGA to control heat, making batteries last longer. Cloud servers with BGA handle big tasks without overheating, keeping them reliable. Choosing BGA assembly means your devices will stay cool and work consistently.
Applications of BGA and Micro-BGA in Electronics
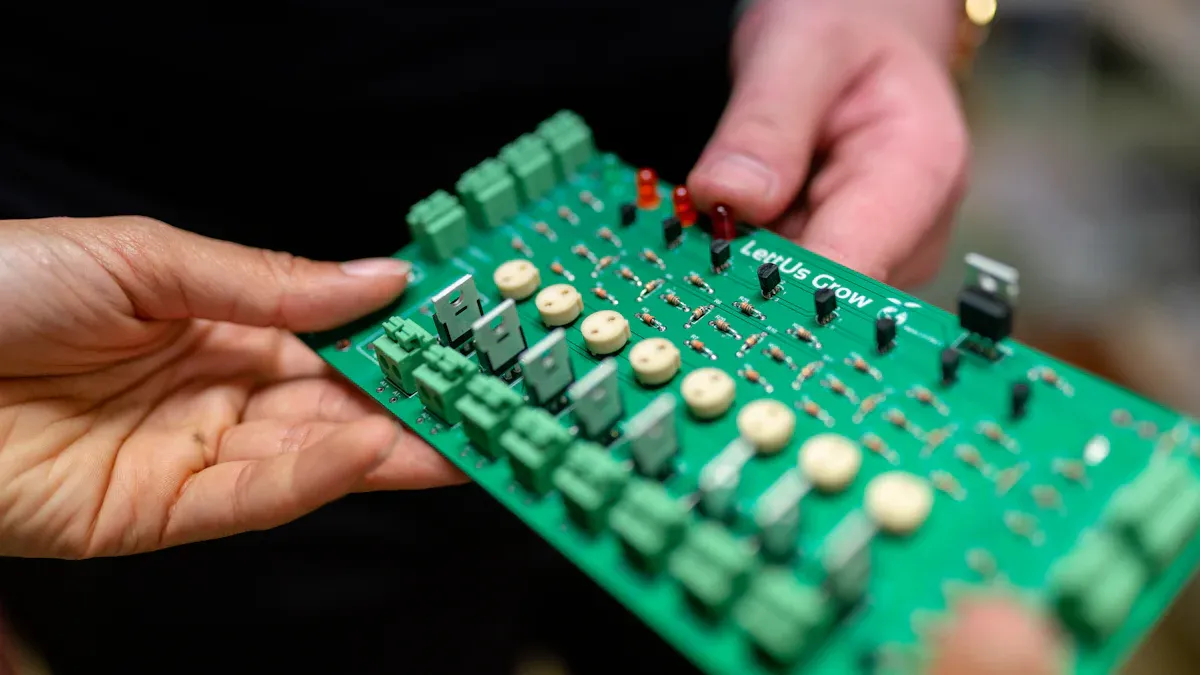
Consumer electronics: Smartphones, tablets, and wearables
BGA has changed how consumer electronics are made. It helps create smaller and stronger devices. Smartphones and tablets use BGA to fit powerful chips and memory in tight spaces. This makes them faster and their batteries last longer. Wearables like smartwatches use micro-BGA to stay small but still work well.
The BGA market is growing fast because of the need for tiny parts. In 2023, the BGA solder spheres market was worth $1.2 billion. By 2032, it could grow to $2.5 billion. This shows how important small parts are for electronics. Companies like Unimicron and LG InnoTek are leading this growth. They make sure your devices stay modern and advanced.
Automotive systems: ADAS and infotainment
BGA is very important in cars. It helps systems like ADAS and infotainment work better. These systems need strong and fast electronics to do their jobs. BGA makes sure control units can handle tasks like processing data and staying cool.
Micro-BGA is great for small car designs. It lets car makers add more features in less space. For example, infotainment systems use BGA for better entertainment and connections. Electric cars also need BGA for managing heat and running smoothly. This makes BGA a key part of modern vehicles.
Telecommunications: 5G and IoT devices
5G and IoT devices depend on BGA and micro-BGA. These technologies help reduce signal problems and manage heat better. BGA is used in systems that make 5G networks work, like mm-wave subsystems.
IoT devices, like smart home tools and sensors, use micro-BGA to stay small and reliable. This means you get smarter devices that work well. As 5G and IoT grow worldwide, the need for BGA and micro-BGA will keep increasing.
Industrial and medical electronics: Robotics and diagnostics
Robots and medical tools depend on BGA and micro-BGA. These technologies help make small, efficient designs for modern needs.
In robots, BGA powers sensors and control systems. Robots need to move precisely and respond quickly. BGA helps by speeding up data and reducing signal issues. Micro-BGA is even smaller, fitting into tight spaces. This makes it perfect for compact robots like industrial machines or self-driving robots. These technologies ensure robots work reliably.
Medical devices also use BGA and micro-BGA. Portable tools like ultrasound machines and health monitors need to be small and light. Micro-BGA helps make these devices easy to carry while staying accurate. It also manages heat, keeping devices cool during long use.
Other medical tools, like MRI machines, also use BGA. They handle tough tasks like complex calculations and heat control. This keeps them working well during important procedures. With BGA and micro-BGA, you can build strong and powerful devices.
Tip: When designing medical or industrial tools, balance size and performance. BGA and micro-BGA help you achieve this, making them vital for today’s technology.
Challenges in BGA and Micro-BGA Assembly
Inspection and quality control complexities
Checking the quality of BGA and micro-BGA is tricky. Problems like “head-in-pillow” defects can pass early checks but fail later. These happen when solder balls touch but don’t bond well. Issues like warped packages, solder paste mix, and PCB settings cause these defects.
Defect Type | Description | Impact on Assembly Process |
---|---|---|
Weak Connections | Problems like ‘head-in-pillow’ pass checks but lack strength | High chance of breaking under heat or pressure, even after delivery |
Causes of Defects | Warped packages, PCB settings, and solder paste issues | These problems raise defect rates and make quality checks harder |
Cost of Missed Defects | Fixing bad parts costs a lot | Skilled workers are needed for repairs, slowing production |
To fix these problems, use better tools and methods for inspections. This ensures micro-BGA assemblies are strong and reliable.
Thermal management and heat dissipation issues
Managing heat is very important for BGA and micro-BGA. If adhesives don’t fully cover parts, heat builds up, causing overheating. Studies show defective joints lose 21% of their strength at room temperature. Also, creep performance drops by 150% when adhesives have flaws.
Aspect | Findings |
---|---|
Heat Management | Good heat control is key for chips to work well. |
Adhesive Problems | Poor adhesive coverage lowers heat transfer slightly. |
Strength Loss | Defective joints lose 21% of their strength at normal temperatures. |
Creep Performance | Defective joints fail 150% faster at room temperature. |
Temperature Sensitivity | Defects affect performance more at lower temperatures. |
Strong heat solutions are needed to stop overheating and keep devices working well for a long time.
Soldering and rework challenges
Soldering BGA and micro-BGA parts needs great care. Micro-BGA’s tiny size makes soldering harder. Fixing bad parts is also tough because nearby connections can get damaged. Skilled workers are needed for repairs, which raises costs.
To solve these issues, invest in better soldering tools and training. This helps make assembly more accurate and reduces expensive repairs.
Cost effects of high-density designs
High-density designs like BGA and micro-BGA improve electronics. But they also cost more to make. Why are they pricier? It’s because making them is harder and needs special tools. These designs need careful assembly, which raises production costs.
The materials used also add to the price. For instance, flip-chip BGA (FC BGA) uses shorter paths for electricity. This makes it work better but needs advanced materials. FC BGA has the biggest market share and grows at 7.37% yearly. Flip-chip chip-scale packages (FC CSP) are also growing fast. They are popular in smartphones and wearables, which need small and efficient designs.
Type | Growth Rate | Market Impact |
---|---|---|
FC BGA | 7.37% | Biggest market share due to better conductivity and shorter paths. |
FC CSP | N/A | Growing fast because smartphones and wearables need small, efficient designs. |
Fixing high-density designs can be expensive too. Micro-BGA packages are tiny, making repairs tricky. Skilled workers and special tools are needed, which increases costs. Inspection tools for quality checks are also pricey but important for reliability.
Even with higher costs, high-density designs are key for modern devices. They help make gadgets smaller, faster, and more efficient. Investing in these designs keeps you ahead in the tech world.
BGA and Micro-BGA give amazing advantages. They improve performance and allow smaller designs. These technologies are used in many fields. Examples include electronics, cars, communication tools, and medical devices. This shows how useful and important they are.
Note: These technologies do more than innovate. They solve real problems in today’s electronics.
When using these solutions, remember that skill in assembly is crucial. Fixing issues like quality checks and heat control keeps devices strong and efficient. By using these improvements, you can lead in the fast-changing tech world of 2025.
FAQ
What makes BGA better than older packaging methods?
BGA helps devices work faster by cutting signal problems. It also handles heat well and allows smaller designs. This makes it great for modern gadgets like phones and gaming consoles.
Why is micro-BGA used in wearables and IoT gadgets?
Micro-BGA is tiny, so it fits in small devices. It improves how electricity flows and keeps devices cool. This helps wearables and IoT tools stay reliable and work better.
How do you check BGA and micro-BGA for problems?
Special tools like X-rays find hidden issues in assemblies. Machines like AOI systems spot problems like misplaced solder balls or weak links.
Tip: Checking often keeps assemblies strong and avoids costly fixes.
Are BGA and micro-BGA assemblies costly to make?
Yes, they need special tools and skilled workers, which costs more. But their benefits, like better performance and smaller sizes, make them worth it for many uses.
Can BGA and micro-BGA handle high heat?
Yes, both manage heat very well. BGA uses solder balls to remove heat, and micro-BGA’s small size helps cool devices. This makes them great for hot environments like cars and servers.
Note: Good heat control keeps devices working longer.
See Also
Evaluating Top All-in-One PCBA Manufacturing Solutions for 2025
Contrasting Turnkey and Consignment PCBA Manufacturing Approaches in 2025
Innovations in RSJPCBA Design and Assembly Through AI Technology
Strategies to Speed Up PCBA Production While Maintaining Quality
Perfecting PCBA Production Methods for Superior Quality Outcomes