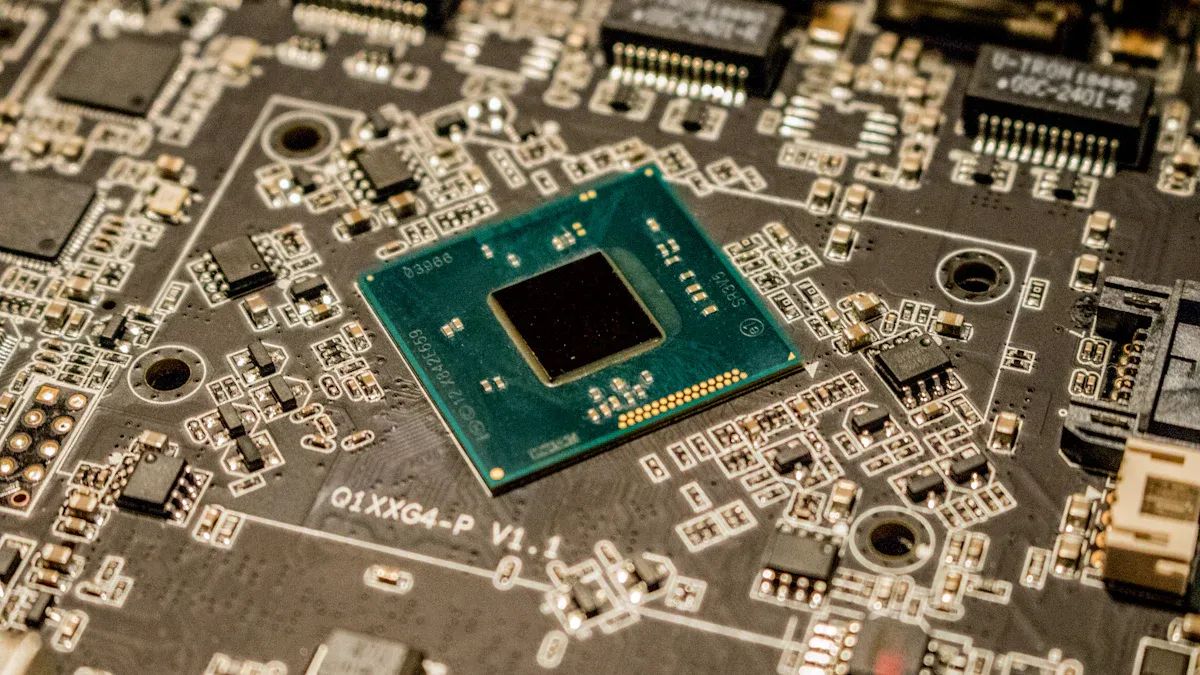
Sub PCBA means a smaller part of a bigger circuit board. It is very important for making modern electronics. It splits hard designs into smaller, easier parts. This helps make things faster and better.
It uses smart methods like robot soldering and surface mount tools. These methods make things more accurate and reliable. Careful testing checks that everything works well. Modular designs help companies change quickly for new needs. This makes production faster and saves money.
Key Takeaways
Sub PCBA makes circuit designs simpler and easier to handle.
It saves money and time by using modular designs and bulk production.
Sub PCBA improves how devices work and makes them more reliable.
In the future, Sub PCBA will help create smarter devices with IoT and AI.
Eco-friendly Sub PCBA methods lower harm to the environment and please consumers.
What is Sub PCBA?
Definition and Key Features
Sub PCBA means a smaller part of a bigger circuit board. It helps make modern electronics by breaking hard designs into smaller parts. This makes fixing and upgrading easier and faster.
Here are some important features of Sub PCBA:
Feature/Definition | Description |
---|---|
Bill of Materials (BOM) | A list of parts with details like voltage and current. |
Approved Vendor List (AVL) | A list of makers and part numbers for BOM items. |
Printed Circuit Board (PCB) | The base that holds and connects all the parts. |
PCA Document Package | A file with BOM, AVL, PCB data, CAD files, and test plans. |
These features help Sub PCBA meet high standards for electronics. By being modular, it makes building and fixing devices easier and more reliable.
Role in the PCBA Process
Sub PCBA is like a puzzle piece in making circuit boards. It breaks big circuits into smaller, working parts. This makes building faster and reduces mistakes.
In the process, Sub PCBA goes through steps like soldering, testing, and checking quality. These steps make sure each part works well before adding it to the final product. This way, the final device works better and is made more efficiently.
Differences Between Sub PCBA and PCBA
Sub PCBA and PCBA are similar but not the same. Sub PCBA focuses on small parts, while PCBA is the whole circuit board.
Here’s a simple comparison:
Aspect | Sub PCBA | PCBA产品 |
---|---|---|
Scope | Small parts of a circuit | Full circuit board |
Complexity | Makes hard designs simpler | Handles the whole circuit |
Application | Used in flexible, modular designs | Used in final products |
Knowing these differences shows how Sub PCBA helps make electronics work better and faster.
Applications of Sub PCBA in Consumer Electronics
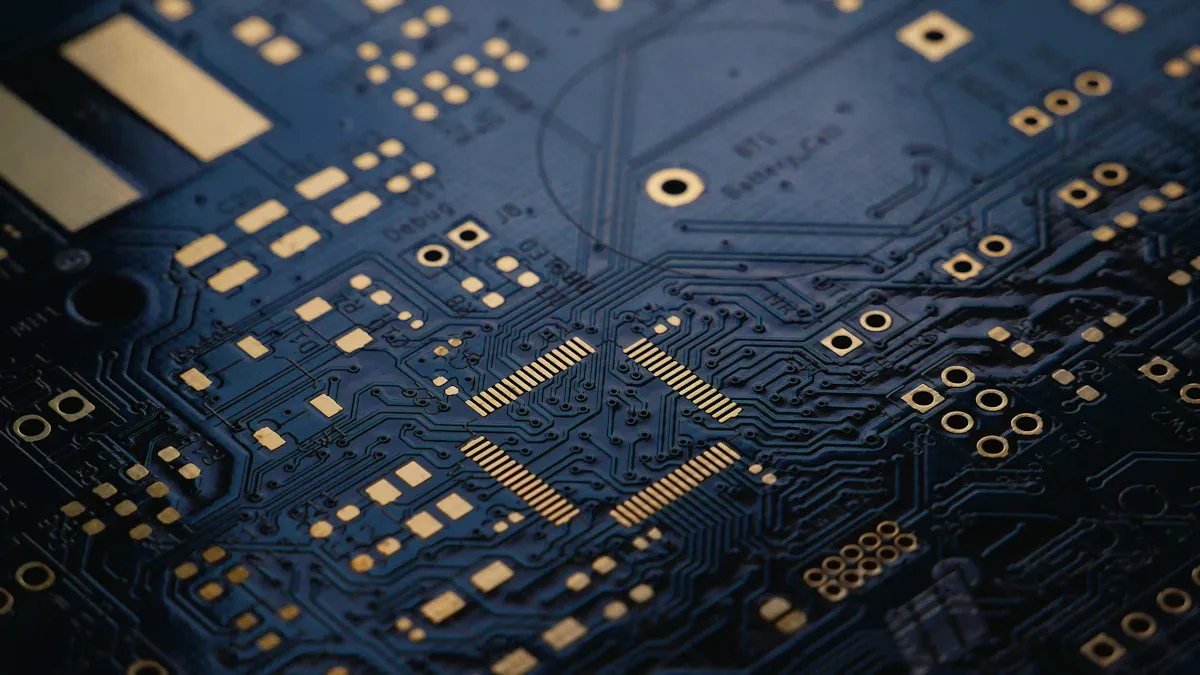
Sub PCBA is very important for making modern electronics. Its small and smart design helps create devices like phones, wearables, and smart home gadgets. Let’s see how Sub PCBA helps these cool technologies.
Smartphones and Tablets
Phones and tablets use Sub PCBA to work better in small spaces. Every time you use your phone, Sub PCBA helps it run smoothly. It handles tricky circuits and adds more features in tiny areas. This allows phones to have sharp screens, fast processors, and strong batteries.
The need for phones and tablets keeps growing. Here are some facts:
Aspect | Details |
---|---|
Market Size (2023) | About $68.4 billion |
Projected Market Size (2032) | Could grow to $105.8 billion |
CAGR | 4.9% growth during this time |
Key Growth Driver | More people want advanced electronics like phones and tablets. |
Technological Influence | 5G and IoT make better PCBs needed for new devices. |
These numbers show why Sub PCBA is key for making better devices. As 5G and IoT improve, Sub PCBA will help create faster and smarter gadgets.
Wearable Technology
Wearables like smartwatches and fitness bands are part of daily life. Sub PCBA makes them small and light but still powerful. For example, your smartwatch can check your heart rate, count steps, and even make calls because of Sub PCBA.
Tiny PCBs are super important for wearables. Sub PCBA saves space while keeping all the features. This makes wearables comfy to wear and full of useful tools. Whether it’s a fitness band or health tracker, Sub PCBA helps make these devices easy to use and dependable.
Smart Home Devices
Smart home gadgets like speakers, thermostats, and cameras need Sub PCBA to work well. These devices use sensors and wireless tools, which need small and accurate PCBs. Sub PCBA makes sure everything works together smoothly.
For example, a smart thermostat uses Sub PCBA to read temperature and connect to your phone. A smart speaker uses it for voice commands and clear sound. By improving PCB design, Sub PCBA makes smart home gadgets work better, making your home easier to manage and more connected.
Applications of PCBAs Beyond Consumer Electronics
Automotive Electronics
PCBAs are very important in today’s cars. They help advanced systems like lane warnings and cruise control work. These systems use PCBAs to process data fast and safely.
With more electric and hybrid cars, PCBAs are even more needed. Car parts like engines use PCBAs to work better and save energy. Other parts, like lights and air systems, need small and strong PCBAs to work well.
The car industry is the fastest-growing market for PCBAs. It is growing by 5% each year from 2023 to 2028. This is because more people want electric cars and smarter driving systems.
Medical Devices and Equipment
PCBAs are changing how medical tools work. They are used in health monitors, scanners, and devices like pacemakers. These tools need very accurate PCBAs to work properly.
For example, health monitors use PCBAs to check heartbeats and blood pressure. Big machines like MRI scanners use PCBAs to handle data and give correct results. The healthcare field uses PCBAs to make devices better and more reliable.
Industrial Automation Systems
PCBAs are making factories smarter. They help sensors and controls share data quickly. This is important for running machines and checking processes.
In tough factory settings, PCBAs stay strong and work well. They are used in robots, assembly lines, and monitoring tools. With advanced PCBAs, factories can work faster and more accurately.
Benefits of Sub PCBA in Electronics Manufacturing
Saving Money and Making More
Sub PCBA helps lower costs and make more products. It splits hard designs into smaller, easier parts. This makes building faster and cheaper.
Making parts in bulk saves time and money. If more products are needed, factories can quickly make extra parts. They don’t need to change the whole process. This keeps production cheap and flexible as needs grow.
Smaller and Smarter Designs
People want smaller, portable gadgets. Sub PCBA helps make tiny, smart designs.
Small designs are key for phones and wireless gadgets. Designers must fit more features into less space.
HDI PCBs add more connections in tiny areas. They are great for slim devices like laptops and phones.
Companies like Molex create smart solutions to shrink product size while adding features.
Sub PCBA saves space and keeps devices powerful. It helps make gadgets that are small, handy, and efficient.
Better Performance and Dependability
Sub PCBA makes devices work better and last longer. Careful testing ensures every part works right:
Testing Type | What It Checks |
---|---|
Stress Testing | Tests how parts handle heat, cold, and wet conditions. |
Power Testing | Checks how parts work under high power and heavy use. |
Problem Analysis | Finds and fixes issues by studying broken parts. |
These tests prove sub PCBA parts are strong and reliable. Devices with sub PCBA work well in real life. This focus on quality makes sub PCBA key in making modern electronics.
Challenges and Solutions in Sub PCBA Manufacturing
Common Manufacturing Issues
Making Sub PCBA can be tricky and affect quality. Problems often happen during making and putting parts together. Here are some common issues:
Defect Type | Description |
---|---|
Warpage | The board bends during production. |
Component Placement | Parts are not placed correctly on the board. |
Board Stackup | PCB layers are not arranged properly. |
Thermal Considerations | Heat causes problems during assembly. |
To fix these problems, follow good PCB assembly steps:
Design the PCB to lower costs and avoid mistakes.
Spot and fix design problems early.
Arrange parts well for easy building and assembly.
Planning well helps reduce mistakes and saves money. It also ensures your electronics are high-quality and work well.
Technological Innovations and Solutions
New technology helps solve manufacturing problems. Robots and precise tools place parts more accurately. HDI technology makes small designs possible without losing features.
Heat problems can be fixed with heat sinks and special materials. Using these new ideas makes your PCBA stronger and work better.
Quality Control and Testing Processes
Testing is very important to make sure electronics work right. Good PCB assembly includes testing at every step. Common tests are:
Burn-in Testing: Finds early problems by using extreme conditions.
In-circuit Testing: Quickly checks if parts work.
Functional Circuit Testing: Tests if the whole board works.
Boundary Scan Testing: Helps test multi-layer boards with hard-to-reach parts.
Testing during and after making catches problems early. Final tests make sure the product is ready to use. These steps ensure your PCBA is reliable and high-quality.
Future Trends in Sub PCBA Technology
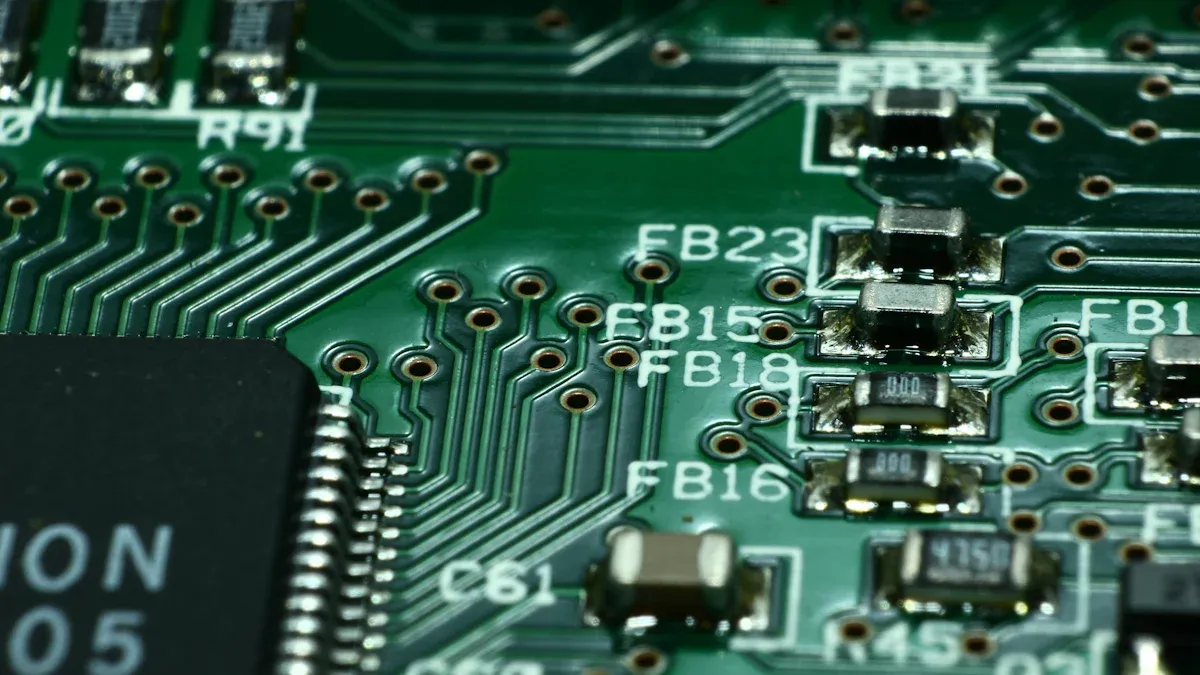
Smaller and More Powerful Devices
People want smaller gadgets that still work really well. Sub PCBA helps make tiny designs without losing features. This is seen in phones, wearables, and car electronics.
The Substrate-Like PCB (SLP) market is growing fast. Key points include:
Expected growth of 12% yearly from 2025 to 2033.
Growth driven by complex devices, electric cars, and IoT.
Electronics and car industries leading this growth.
These changes show how smaller designs are shaping the future. Devices are becoming smarter, smaller, and more efficient.
IoT and AI Working Together
Sub PCBA is important for adding IoT and AI to devices. It connects sensors, processors, and communication tools easily. This makes devices work better and adjust to new needs.
Here’s how Sub PCBA helps IoT and AI:
Feature | What It Does |
---|---|
Custom Solutions | Special designs for different IoT devices. |
Easy Integration | Combines sensors and communication tools smoothly. |
Growth Potential | Built to expand with bigger IoT networks. |
Industry Progress | Helps create smart cameras, retail tools, and industrial devices. |
Speed and Quality | Ensures fast, reliable, and high-quality performance. |
With these features, Sub PCBA powers smart homes, connected cars, and advanced factories.
Eco-Friendly Manufacturing
Making Sub PCBA is becoming greener to protect the planet. Companies are using better methods to reduce harm. These include:
Using lead-free solder and water-based materials.
Recycling to cut down on waste.
Saving energy and using renewable power.
Choosing materials that can be recycled.
Following rules like RoHS and REACH.
These steps help the environment and meet consumer demands for green products. Sub PCBA is leading the way to a cleaner, greener future.
Sub PCBA is key to making modern electronics better. It is used in phones, wearables, cars, and medical tools. Its design makes building easier and devices more reliable. Sub PCBA helps create smaller, smarter, and efficient gadgets, pushing innovation ahead.
The future of Sub PCBA looks bright with new ideas. IoT, AI, and green manufacturing will help it grow more. As technology changes, Sub PCBA will stay important in making advanced electronics.
FAQ
What does Sub PCBA mainly do?
Sub PCBA breaks big circuits into smaller, easier parts. This makes building faster, reduces mistakes, and improves how devices work.
How does Sub PCBA help electronics?
Sub PCBA makes gadgets smaller, smarter, and more efficient. It helps build things like phones, wearables, and smart home devices that work well and last long.
Can Sub PCBA be used outside electronics?
Yes, Sub PCBA is used in cars, medical tools, and factories. It helps with electric cars, health devices, and smart machines.
What problems happen in Sub PCBA making?
Problems include bending boards, wrong part placement, and heat issues. Good planning, better tools, and testing fix these problems.
Is Sub PCBA good for the environment?
Yes, makers use green ways like lead-free solder and recycling. These steps save energy and meet eco-friendly goals.
See Also
Innovative Technologies Shaping PCBA Production In Consumer Electronics
Discover The Role Of AI In Advancing PCBA Today
New Developments In FDA-Approved PCBA Solutions For Healthcare
Comparing Turnkey And Consignment PCBA Manufacturing Approaches
Understanding Automotive PCBA Assembly And Its Importance In 2025