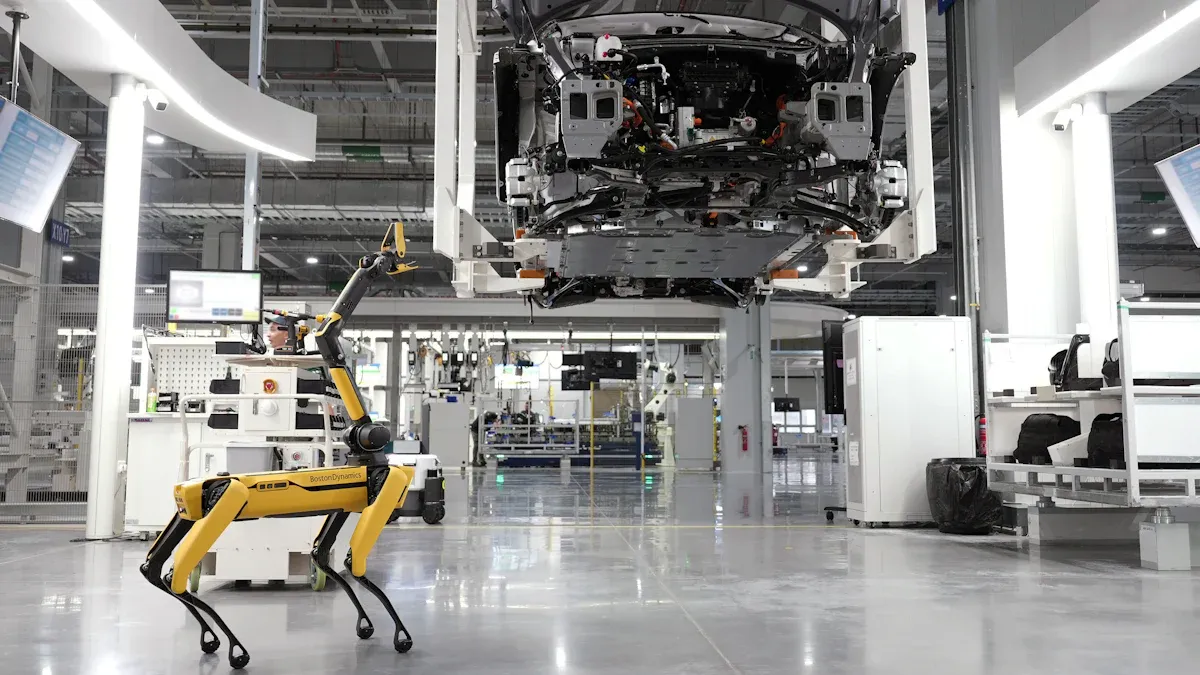
Printed Circuit Board Assembly (PCBA) is key to modern industrial automation controller PCBA. It helps factories work by linking and powering important parts. Without industrial automation controller PCBA, controllers wouldn’t work well for tough industrial jobs. This PCBA boosts efficiency, simplifies tasks, and supports new ideas. The automation controller PCBA connects sensors, actuators, and processors smoothly, making automation smarter and better.
Key Takeaways
PCBA works like the ‘brain’ of automation systems. It links important parts like sensors and processors to work smoothly.
Testing and checking quality are very important for PCBA. These steps make sure it works well in tough factory settings using tests like environmental and functional checks.
Picking the right materials for PCBA helps it last longer and work better. This is important for systems used in extreme conditions.
Future PCBA trends include making parts smaller, adding AI, and using eco-friendly methods. These changes will improve automation technology.
The Role of PCBA in Industrial Automation Controllers
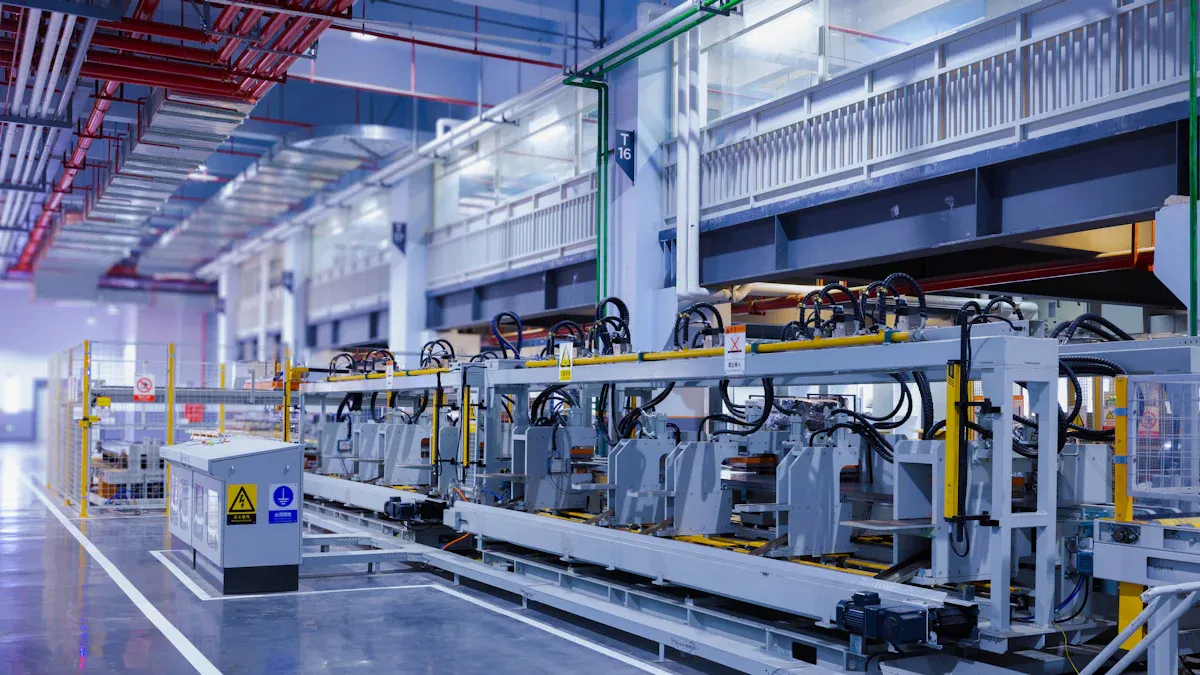
What is PCBA and its function in automation?
Printed Circuit Board Assembly (PCBA产品) is the base of modern automation. It brings together parts like resistors, capacitors, and microcontrollers on one board. This setup lets electricity move smoothly, helping systems do hard tasks. Think of PCBA产品 as the “brain” of automation. It handles signals, runs control tasks, and keeps parts working together.
“Printed circuit boards (PCBs) are key to making automation better. They hold electronic parts, let electricity flow, and act like the system’s nervous system. PCBs help control robots and manage complex factory tasks, showing their importance in automation controllers.”
In automation, PCBA产品 makes controllers work well and dependably. It helps run control tasks like checking sensors, managing actuators, and handling data. Without PCBA产品, automation systems wouldn’t be fast or accurate enough for today’s factories.
How PCBA supports industrial automation controllers
PCBA产品 improves automation controllers by adding reliability, accuracy, and flexibility. It connects microcontrollers, which make decisions, to sensors and actuators. This lets controllers check conditions, process data, and give commands quickly.
To stay reliable, PCBA产品 goes through strict testing steps. For example:
Front-Loaded Design Review finds problems early.
Precision Material Management uses trusted parts suppliers.
Full-Process Visualized Manufacturing Control checks every production step.
Dual Assurance Testing includes tough tests for durability.
These steps make sure the PCBA产品 works in tough factory settings without breaking. By avoiding breakdowns, PCBA产品 keeps automation systems running smoothly.
Examples of PCBA applications in automation systems
PCBA产品 is used in many automation tools like robotic arms and conveyor belts. It helps controllers read sensor data and adjust actions based on real-time needs. For instance, a robotic arm uses PCBA产品 to move precisely and assemble products correctly.
Testing shows how PCBA产品 supports automation systems:
Testing Method | Advantages | Disadvantages |
---|---|---|
Automated Optical Inspection | Very accurate, fast, finds tiny defects, less manual work | Needs high-quality cameras, glare can cause issues |
Burn-in Testing | Finds early failures, tests parts under tough conditions | Takes time, high heat may harm parts |
In-Circuit Testing | Checks assembly and function before use | N/A |
Environmental Testing | Mimics real-world conditions like heat and vibration | N/A |
EMC Testing | Makes sure no interference with other devices | N/A |
Functional Testing | Tests how it works in fake automation setups | N/A |
These tests ensure PCBA产品 works well in automation. By giving precise control and steady performance, PCBA产品 helps improve automation technology.
Types of PCBA in Industrial Automation
Single-layer PCBs
Single-layer PCBs are the easiest type of circuit boards. They have one conductive layer for all parts and connections. These boards work well for simple tasks that don’t need complex circuits. You can find them in basic tools like sensors or LED lights. They are cheap to make and easy to produce.
Tip: Single-layer PCBs are great for making many low-cost items.
Even though they are simple, single-layer PCBs are important in automation. They work well for tasks that don’t need advanced features. Their basic design makes them strong and easy to fix, which is helpful for many industries.
Multi-layer PCBs
Multi-layer PCBs are more advanced than single-layer ones. They have several conductive layers separated by insulating materials. This design allows for more complex circuits and better performance. These PCBs are used in advanced tools like robotic controllers and PLCs.
PCB Type | Market Share Growth | Reasons for Growth |
---|---|---|
Standard Multilayer | Higher CAGR of 6.21% | Useful for high-density tasks and saving space in small devices. |
Double-sided PCBs | Significant growth | Better for control units and growing demand in electric cars and smart systems. |
Multi-layer PCBs are great for saving space while doing complex jobs. They are essential for modern automation because they handle tough tasks with ease.
Flexible PCBs
Flexible PCBs can bend and twist without breaking. This makes them perfect for tight spaces or moving parts. In automation, flexible PCBs are used in robotic arms or wearable devices for workers.
PCB Type | Features | Market Role |
---|---|---|
Flexible Circuits | Lightweight and useful for many different tasks. | N/A |
HDI | High-density designs for small and compact devices. | N/A |
Flexible PCBs have many benefits. They are light, strong, and can handle tough conditions. As industries move toward smaller and smarter designs, flexible PCBs are becoming more popular.
Rigid-flex PCBs
Rigid-flex PCBs mix features of rigid and flexible boards. They have stiff layers joined by bendable ones. This design gives strength and flexibility together. These PCBs work well in devices needing both toughness and adaptability.
A big advantage of rigid-flex PCBs is saving space. They combine layers, cutting down on cables and connectors. This makes them perfect for small automation systems. For example, they are used in robotic arms or tiny controllers.
Another benefit is their toughness. Flexible layers handle vibrations, while rigid ones add support. This keeps the PCB working in harsh conditions. Rigid-flex PCBs are dependable for hard automation tasks.
These PCBs also make assembly easier. Fewer parts mean fewer mistakes during production. This lowers costs for automation systems. They also improve signals by keeping parts close together. This helps send data faster and more accurately.
Benefits of PCBA in Automation Systems
Reliability in harsh industrial environments
PCBs must work well in tough factory conditions. These include high heat, moisture, and corrosive surroundings. PCBA产品 stays reliable through strict testing. Tests copy real-world conditions to find weak spots.
Environmental Testing: Uses methods like HAST, temperature cycling, and salt spray tests.
HAST: Checks how PCBs handle heat and moisture. It finds problems like peeling or rust.
Temperature Cycling Testing: Tests how PCBs react to quick temperature changes. It spots weak solder joints.
Salt Spray Testing: Measures PCB resistance to corrosion. This is vital for marine and factory use.
These tests make sure PCBs stay strong in hard environments. Reliable PCBs reduce downtime and keep systems running smoothly.
Note: Strong PCBs are key for automation. They ensure steady performance in tough conditions.
Space-saving designs for compact controllers
Modern systems need small controllers that work well in tight spaces. PCBs help by using smart designs to save space.
Rigid-flex PCBs mix stiff and bendable layers. This design absorbs vibrations and fits better.
Magnetic current sensors shrink PCB size by combining functions. They simplify layouts and reduce wiring.
New materials like composites and 3D-printed electronics save space and cut weight.
For example, a robot company had trouble with big shunt resistors. Switching to Allegro’s ACS71240 sensors made their controllers smaller, cheaper, and better. These ideas make PCBs great for compact automation tools.
Cost-efficiency in production and operation
PCBA产品 helps save money in many ways. It lowers production costs, boosts efficiency, and cuts operating expenses. Here’s how:
Lean production model: Reduces waste and improves supply chains. Materials arrive only when needed.
Automation technology: Speeds up production and ensures consistency. Machines lower labor costs and improve efficiency.
Quality control: Finds defects early to avoid waste. This saves resources and reduces rework.
Energy management: Cuts energy use with smart monitoring systems. Equipment runs more efficiently.
Supply chain management: Builds strong supplier relationships. Just-in-Time buying lowers storage costs.
These methods make PCBA产品 a smart choice for automation. Using PCBs in systems saves money while keeping performance high.
Enhanced functionality and performance
In industrial automation, better features and performance are very important. PCBs help controllers do hard jobs quickly and accurately. Today’s PCBs are made to handle advanced tasks, making automation systems smarter and stronger.
1. Advanced Signal Processing
PCBs manage data between sensors, actuators, and controllers. They process signals fast for quick actions. For example, a robotic arm’s PCB产品 reads sensor data and moves right away. This improves work speed and reduces mistakes.
2. Combining Many Functions
Modern PCBs combine different tasks into one board. This removes extra parts and makes systems simpler. For example, a PCB产品 in a PLC can collect data, process it, and send messages all at once. This saves space and boosts efficiency.
Tip: Choose PCBs with built-in features to make automation easier and better.
3. Fast Communication
Automation needs quick and steady communication between parts. PCBs allow fast data transfer using special designs and materials. Whether it’s a conveyor belt or robot, the PCB产品 keeps everything working smoothly.
4. Custom Designs for Special Jobs
PCBs can be made to fit specific automation needs. You can add features like temperature sensors or wireless tools. This lets you design controllers for exact tasks, improving how they work.
5. Support for New Technologies
As automation grows, PCBs change to support new ideas like AI and IoT. For example, an IoT PCB产品 can send data to the cloud for analysis. This helps with things like predicting problems and remote checks.
Note: Using PCBs that work with new technologies can prepare your systems for the future.
6. Better Energy Use
PCBs also help save energy. They spread power efficiently and reduce waste. This lowers costs and supports eco-friendly goals.
Feature | Benefit |
---|---|
Advanced Signal Processing | Quick actions and better accuracy |
Function Integration | Simple design and improved efficiency |
High-Speed Communication | Fast and steady data sharing |
Customization | Special designs for unique automation needs |
Emerging Technology Support | Ready for future tools and smarter systems |
Energy Efficiency | Lower costs and helps the environment |
PCBs are key to making automation systems work better. Picking the right PCB产品 can improve speed, accuracy, and flexibility in your controllers.
Design and Assembly Tips for Industrial Automation Controller PCBA
Keeping PCBs Cool for Better Performance
Managing heat is key to keeping PCBs stable and working well. High heat can damage parts and cause expensive delays. To stop this, control the heat of electronic parts and let it escape easily. Using thicker copper and wider traces can help reduce heat problems. Also, plan the PCB产品 layout carefully to avoid hot spots.
To remove heat faster, use tools like fans or heat sinks. These move heat away from important areas, keeping the PCB产品 at safe temperatures. For powerful systems, place parts wisely and follow heat management rules. This ensures the PCB产品 stays strong and works reliably.
Tip: Test how well your PCB产品 handles heat in real-world conditions to catch problems early.
Blocking EMI for Clear Signals
Electromagnetic interference (EMI) can mess up PCBs, especially where many devices are used. To keep signals clear, add EMI shields during assembly. Materials like copper or aluminum block unwanted signals and protect sensitive parts.
Good grounding and short signal paths also help reduce EMI. Keep high-frequency parts apart to avoid interference. Testing for EMI ensures your controllers meet standards and work well in busy environments.
Note: EMI shielding not only improves performance but also makes PCBs last longer.
Picking Strong and Efficient Materials
Choosing the right materials is important for tough and efficient PCBs. Materials must handle heat, vibrations, and chemicals in factories. Tests like peel and pull checks ensure layers stick well for long-term use.
Efficient materials also improve how PCBs work. High-quality copper and substrates boost performance and save energy. By balancing strength and efficiency, you can make PCBs that work well in tough systems.
Test Type | What It Checks |
---|---|
Mechanical Loading | Handles weight, shaking, and shocks. |
Thermal Loading | Works in extreme heat and cold. |
Electrical Loading | Prevents electrical problems. |
Chemical Loading | Resists rust and chemical damage. |
Aging Tests | Predicts how long it will last. |
Tip: Use tested materials to avoid sudden failures in tough factory settings.
Scalability and manufacturability in design
Making PCBs scalable and easy to produce is very important. Scalability means your PCB产品 can grow or add features later without starting over. Manufacturability ensures PCBs can be made quickly, cheaply, and in large amounts.
Key Ideas for Scalability
Modular Design: Divide your PCB产品 into smaller parts you can reuse. This makes upgrades simple and saves redesign time. For example, a modular PCB产品 in a robot can easily add new sensors.
Future-Proofing: Pick parts that can handle more power or features. For instance, using microcontrollers with extra power helps with future updates.
Flexible Layouts: Leave space on your PCB产品 for future changes. Adding extra connectors or pins makes upgrades easier.
Tip: Plan ahead. A scalable PCB产品 saves time and money when systems grow.
Key Ideas for Manufacturability
Standardized Components: Use common parts to avoid supply problems. This also lowers costs and keeps quality steady.
Simplified Assembly: Use fewer layers and parts in your PCB产品. A simple design is faster to make and reduces mistakes.
Testing Accessibility: Add test points to your PCB产品. These help find problems during production.
Factor | Scalability Advantage | Manufacturability Advantage |
---|---|---|
Modular Design | Easy to upgrade | Makes assembly simpler |
Standardized Parts | Works with future needs | Cuts production costs |
Flexible Layouts | Allows system growth | Eases testing and fixing |
By focusing on scalability and manufacturability, your PCBs stay flexible and affordable. These ideas improve automation systems and make them easier to build and maintain.
Testing and Quality Assurance in PCBA
Functional testing for operational accuracy
Functional testing checks if PCBs work as they should. It acts like a real-world test to see if the controller works properly. This testing looks at how the PCB产品 handles signals, processes data, and connects with other parts. For example, in factories, functional testing might copy a robotic arm’s movements to check its control and response.
Different methods improve functional testing. ICT tests check circuits, voltage, current, and noise. FCT tests run the whole PCB产品 to find hardware or software problems. Fatigue tests check if the PCB产品 stays reliable under heavy use. These tests make sure controllers work well in tough conditions.
Tip: Test your PCBs often to find problems early and save time.
Environmental testing for industrial conditions
Environmental testing checks if PCBs can handle harsh factory conditions. Controllers face heat, moisture, and shaking, so testing ensures they stay strong. For example, temperature cycling tests expose PCBs to quick temperature changes to find weak spots. Salt spray tests check if PCBs resist rust, which is important for marine or chemical factories.
Quality assurance sets rules for these tests. A manual explains management policies, while a plan lists steps for each project. Internal checks happen regularly, while external checks use outside experts to review processes.
Quality Assurance Component | Description |
---|---|
Quality Assurance Manual | A guide with rules for making quality products. |
Quality Assurance Plan | Steps for ensuring quality in specific projects. |
Quality Control (Internal) | Regular checks to keep data accurate. |
Quality Control (External) | Outside reviews to check measurement processes. |
Note: Environmental testing keeps PCBs working in the hardest conditions.
Inspection methods for defect detection
Inspection finds problems during PCB产品 production. Automated optical inspection (AOI) is better than manual checks because it’s faster and more accurate. AOI uses smart algorithms to spot defects quickly. Studies show AOI works much better than older methods, which are slower and less reliable.
Advanced tools like SRN_Net are great at finding tiny PCB产品 defects. These tools have high accuracy and recall rates, proving how useful they are. Other methods, like micro-sectioning and time-domain reflectometry, also help find defects.
Tip: Use automated tools with smart algorithms to reduce errors and improve quality.
Following Industry Standards and Certifications
Following industry standards and certifications makes sure PCBs are safe and high-quality. These rules help you design and build PCBs that work well in automation systems. They also prevent costly mistakes and ensure you follow legal rules.
One important standard is IPC-A-610. It sets rules for how electronic assemblies should look and work. This ensures your PCB产品 meets strict quality levels. Another key certification is ISO 9001, which focuses on managing quality. Using this helps improve processes and deliver reliable results.
For automation controllers, CE and UL certifications are very important. CE certification shows your controller meets European safety and environmental rules. UL certification proves it is safe to use in North America. These certifications build customer trust and show your focus on quality.
Testing is crucial to meet these standards. You need to inspect PCBs and controllers carefully to ensure they meet the rules. For example, environmental testing checks if PCBs can handle tough conditions. Functional testing makes sure controllers work as they should.
By following these rules, you make your automation systems more reliable. Customers will trust your products because they meet global standards. This improves your reputation and helps you sell in international markets.
Tip: Keep up with new standards and certifications. Staying updated helps you stay competitive in automation.
Future Trends in Industrial Automation Controller PCBA
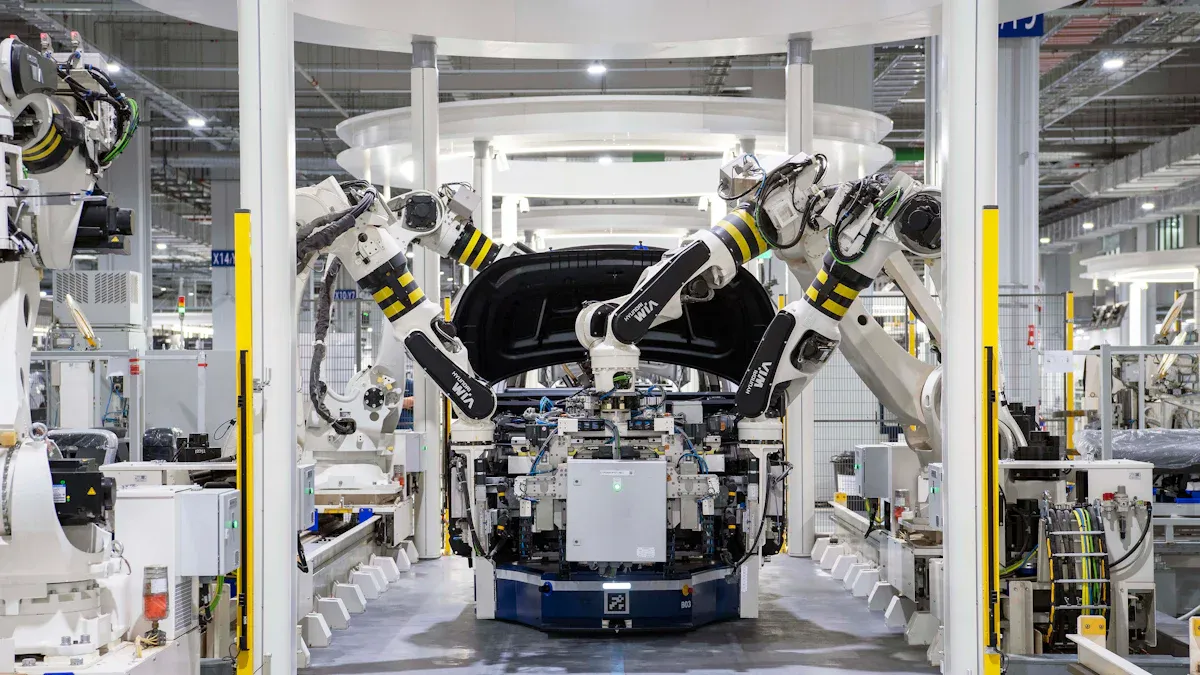
Miniaturization and high-density interconnects
Smaller and smarter devices are shaping the future of PCBs. High-density interconnect (HDI) technology helps make this possible. It allows tighter wiring and more circuits in small spaces. This makes controllers lighter and saves room while adding advanced features.
Source | Summary |
---|---|
High Density Interconnect PCB Market | Growing need for tiny, smart designs supported by HDI technology. |
Ideas and Innovation Blog | Explains how HDI boosts compact designs with dense wiring. |
HDI PCB Market Size Report 2032 | Shows demand for smaller, complex devices driving HDI growth. |
Using HDI, controllers can be compact yet powerful. This meets the need for space-saving and efficient automation tools.
Integration of AI and IoT technologies
AI and IoT are changing how PCBs work in automation. AI improves designs by predicting better wiring paths and fixing signal issues. IoT lets controllers share data and connect with other devices for remote monitoring.
Routing Optimization: AI finds better wiring paths to avoid mistakes.
Signal Integrity Enhancement: Models improve signal quality for smoother operations.
Defect Detection: AI spots flaws to ensure reliable PCBs.
Counterfeit Component Detection: Machine learning helps find fake parts faster.
These tools make PCBs smarter and more dependable for modern automation systems.
Green manufacturing and sustainability
Eco-friendly practices are becoming important in making PCBs. Factories now use safer materials, renewable energy, and recycling methods to protect the environment.
Technology | Description |
---|---|
Lead-free soldering | Uses safer metals like tin and copper to reduce waste. |
Renewable energy | Uses solar or wind power to cut emissions. |
Zero-waste manufacturing | Recycles leftovers to save raw materials. |
Biodegradable materials | Makes PCBs from plant-based materials for less pollution. |
Choosing green methods helps the planet while keeping automation systems high-quality.
Advanced materials for next-generation PCBs
The materials used in PCBs have changed to meet new technology needs. These advanced materials make PCBs work better, last longer, and use energy more efficiently. They can handle higher heat, resist damage, and transfer data faster.
One common material is high-frequency laminate. It helps PCBs work in devices needing quick communication, like 5G systems. Ceramic-based substrates are another option. They let PCBs handle very high heat, perfect for factory machines. Flexible polymers are also widely used. They let PCBs bend to fit small spaces without breaking.
Did you know? Scientists are studying graphene for future PCBs. Graphene is super light, very strong, and conducts electricity better than older materials.
Here’s a simple table of advanced materials and their uses:
Material | Key Benefit | Common Use Case |
---|---|---|
High-frequency laminate | Helps with fast communication | 5G networks, IoT devices |
Ceramic substrates | Works well in extreme heat | Industrial automation, aerospace |
Flexible polymers | Adds flexibility and strength | Wearable devices, robotics |
Graphene | Improves conductivity and lowers weight | New technologies |
These materials make PCBs stronger and more useful. They also save energy, helping the environment. When picking materials for your PCB产品, think about what your system needs. Using advanced materials can boost performance and make devices last longer.
PCBA is crucial for industrial automation controllers, serving as the core of modern systems. It improves how industries work by boosting efficiency, dependability, and creativity.
During COVID-19, PCBA proved its value by making devices more efficient.
Medical tools like ventilators showed how PCBA helps create life-saving innovations.
Companies like Elvia and Calumet Electronics increased PCB production to meet urgent needs.
Application/Use | What It Does |
---|---|
Industrial Robots | Help robots move precisely for tasks like welding. |
Machine Vision Systems | Assist in checking quality and recognizing objects. |
Smart Sensors | Track machine health and environmental changes. |
The future of PCBA includes smaller designs, AI features, and eco-friendly production. These changes will make automation smarter and better for the planet.
FAQ
1. What is the difference between PCB and PCBA?
A PCB产品 is just the plain circuit board with no parts. PCBA产品 is the PCB产品 after parts like resistors and microcontrollers are added. PCBA产品 is the working board used in automation systems.
2. Why is PCBA important for industrial automation?
PCBA产品 links sensors, actuators, and processors in controllers. It ensures smooth communication, accurate control, and efficient work in factories. Without PCBA产品, automation systems wouldn’t be fast or precise enough for modern needs.
3. How does PCBA handle harsh industrial conditions?
PCBA产品 is made with strong materials and tested for toughness. Tests like heat cycling and rust resistance ensure it works well in heat, moisture, and shaking. This makes it perfect for tough factory environments.
4. Can PCBA be customized for specific automation needs?
Yes, PCBA产品 can be designed with special features like wireless tools or temperature sensors. Custom designs make PCBA产品 better for unique tasks, improving how automation systems work.
5. What trends are shaping the future of PCBA?
Smaller designs, AI, and eco-friendly methods are key trends. Tiny, smart boards save space, while AI boosts performance. Green practices like lead-free soldering and recyclable materials make PCBA产品 better for the planet.
Tip: Follow these trends to keep your automation systems ready for the future.
See Also
Exploring PCBA’s Importance in Industrial Automation Processes
The Impact of PCBA on Efficiency in Automation Systems
Essential Technologies Shaping PCBA Production for Today’s Electronics