
Speeding up PCBA production while keeping quality high requires careful planning by PCBA manufacturers.
Focus on important aspects such as improved designs and streamlined workflows.
Collaborate effectively with suppliers to enhance processes and increase efficiency.
Effective planning can reduce waiting times by 20%, facilitating quicker deliveries.
To stay competitive, monitor metrics like production capacity and product quality.
These metrics align with global standards, enabling PCBA manufacturers to meet customer demands swiftly.
Intelligent strategies empower PCBA manufacturers to operate faster while maintaining strong quality.
Key Takeaways
Make PCB designs simpler to build faster and avoid errors. Using fewer parts and clear plans makes production quicker.
Use robots and smart machines for repeated tasks. This makes work faster and more accurate, keeping quality high.
Work closely with suppliers to get good parts on time. Good teamwork prevents delays and makes work smoother.
Follow lean manufacturing to reduce waste and improve steps. This saves time and materials while keeping quality good.
Check production numbers often to spot problems early. Watching quality and delivery helps meet goals and keep customers happy.
Make Designs Easier to Build (DFM)
Keep PCB layouts simple for faster assembly
Making PCB layouts simpler helps speed up assembly. Using fewer parts makes the design less complicated and easier to build. Placing parts in the right spots helps the process go smoothly. Spacing parts properly and adding clear labels also make production faster. For example, using standard designs means less custom tools are needed. This saves setup time and makes assembly quicker. Simple layouts also lead to fewer mistakes, which reduces waste and fixes.
Good layouts also make testing faster. Easier-to-test designs cut down the time spent checking for quality. This helps deliver circuit boards faster. By keeping designs simple, you can make assembly both quicker and more reliable.
Reduce design complexity to avoid mistakes and boost quality
Simpler designs not only speed up production but also improve quality. Complicated designs often cause mistakes during manufacturing, leading to delays and higher costs. Easier designs are quicker to build and test. For example, DFM-optimized designs set clear quality rules. This avoids redesigns and keeps the supply chain running smoothly. It also helps products reach the market faster.
Adding manufacturability checks during design helps save money and resources. Rafael, a company in Israel, used DFM to remove unneeded features. This cut costs by over 50% and brought in more supplier offers. This shows how simpler designs can save money and time.
Work with PCBA manufacturers early in the design process
Talking to PCBA manufacturers early can make designs easier to build. Their advice can spot problems before production starts, saving time and effort. Working together ensures designs match what manufacturers can do, reducing errors and delays.
DFM also allows quick checks in-house to speed up product development. Teaming up with manufacturers helps set clear quality goals and smooth out workflows. This teamwork speeds up production and ensures high-quality circuit boards.
Tip: Talking openly with PCBA manufacturers early can stop costly errors and make production more efficient.
Automate Assembly Processes
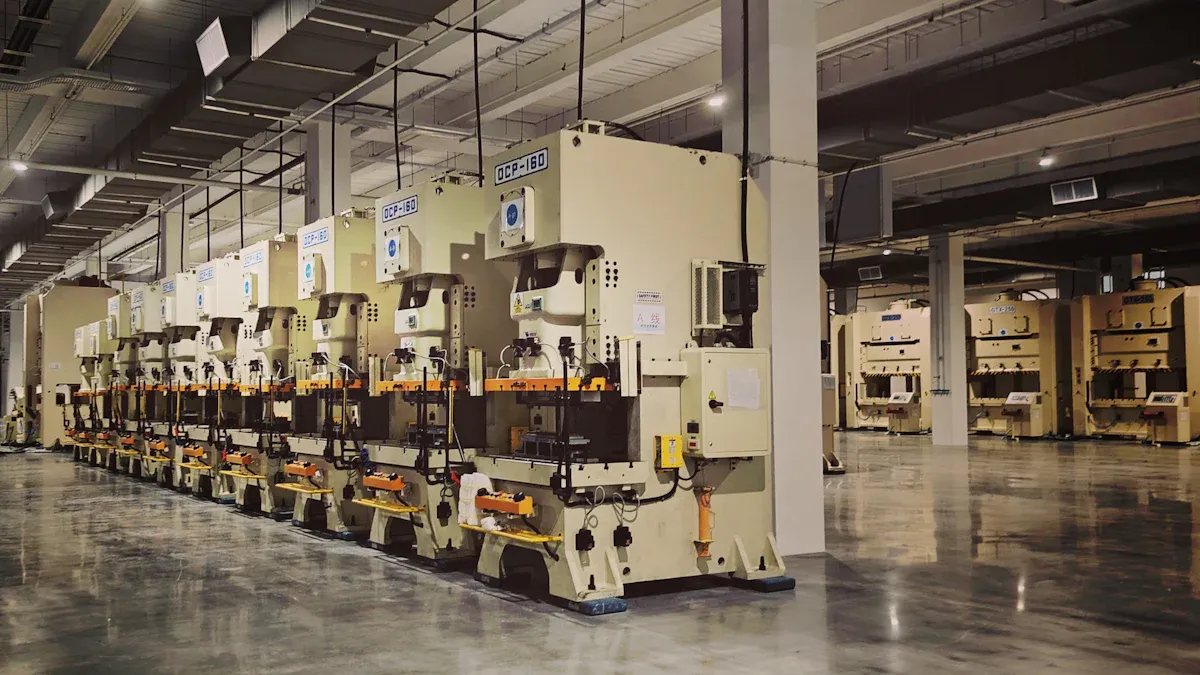
Use advanced pick-and-place machines for better accuracy
Modern pick-and-place machines make PCB assembly faster and more accurate. These machines can place thousands of parts every hour, saving time. They work with great precision, making products more reliable. For example, robotic arms pick parts from reels and place them on PCBs perfectly. This automation ensures accurate placement, no matter the project size.
Feature | What It Does |
---|---|
Speed | Places thousands of parts per hour, cutting assembly time. |
Accuracy | Ensures precise placement, improving product reliability. |
Automation | Handles complex or large-scale production with ease. |
These machines can handle different part sizes and types, showing their flexibility. By using them, you can improve both quality and efficiency in PCB assembly.
Add automated optical inspection (AOI) for better quality checks
Automated optical inspection (AOI) systems help keep PCB assembly quality high. They use cameras and special lights to take clear pictures of PCBs. Software compares these pictures to set standards to find tiny mistakes. This reduces the workload for workers and keeps quality consistent.
In tests, AOI systems inspected shiny materials like aluminum parts. They moved parts, adjusted cameras, and analyzed images quickly. This made inspections faster and more accurate. AOI systems also sort products into “good” or “bad” using sensors and software. Adding AOI to your process lowers defects and improves efficiency.
Use robots for repetitive tasks to save time
Robots make PCB assembly faster by doing repetitive tasks with accuracy. Robotic arms are great for placing parts and soldering. They reduce mistakes and can work nonstop. Robots also make workplaces safer by handling dangerous tasks, like working with toxic materials or high heat.
Benefit | What It Means |
---|---|
Consistency | Repeats tasks accurately, ensuring reliable products. |
Faster production | Speeds up assembly and reduces errors. |
Better material use | Uses resources wisely and cuts waste. |
Higher quality | Reduces mistakes and ensures excellent results. |
Robots can also assemble tiny devices, placing small parts precisely. Using robots helps mass production, shortens lead times, and keeps workspaces clean. This method boosts speed and ensures top-quality PCB assembly.
Implement Lean Manufacturing Principles
Find and fix production slowdowns
Slowdowns make PCB assembly take longer and cost more. Spotting these problems early helps production run smoothly. For example, manual checks often delay work and increase costs due to late error detection. Switching to AI tools like Vision Quality Inspection (VQI) speeds up checks and reduces mistakes, solving this issue.
Problem Type | What Happens |
---|---|
Slow Inspections | Manual checks take time and raise costs. |
Worker Shortages | Fewer skilled workers slow down production. |
Using AI Tools | AI systems make inspections faster and more accurate. |
Tools like Value Stream Mapping help find tasks that waste time. This method improves workflows and speeds up production. Fixing slowdowns makes PCB assembly faster and less expensive.
Cut material waste but keep quality high
Cutting waste saves money and time in PCB assembly. Overproduction, defects, and delays are common waste sources. For example, making too many products uses extra resources and space. Using Just-in-Time (JIT) production ensures you only make what’s needed, reducing waste.
Waste Type | Efficiency Loss | What It Means |
---|---|---|
Defects | 10%-20% | Broken parts or rework waste time and money. |
Overproduction | 10%-20% | Making too much ties up resources. |
Planned Downtime | 40%-50% | Scheduled stops waste time during production. |
Unplanned Delays | 40%-50% | Unexpected stops slow down work and raise costs. |
The 5S method—Sort, Set in Order, Shine, Standardize, and Sustain—organizes workspaces better. This system cuts waste while keeping quality high.
Simplify workflows for faster PCB assembly
Simpler workflows make PCB production faster without losing quality. AI tools check past data to predict when machines need fixing, avoiding delays. Predictive maintenance schedules repairs early to stop sudden breakdowns. These methods improve speed and ensure on-time delivery.
Other ideas, like adjusting settings during assembly, improve performance. Managing materials ensures parts are ready when needed. Automating tasks speeds up work and reduces mistakes.
Main Workflow Tips:
Use AI tools to plan maintenance early.
Schedule production to save time.
Manage materials to avoid delays.
By simplifying workflows, you can save money and time. This method ensures fast production and great results.
Collaborate with Reliable Suppliers
Get high-quality parts with steady delivery times
Using high-quality parts makes your circuit boards work well. Certifications like UL Recognized Component Mark and UL D Mark show they meet global rules. These certifications help your products stand out and gain trust in the market. Long waits or missing materials can hurt product quality. To stop this, choose suppliers who deliver on time. Reliable suppliers help you finish projects faster and keep quality high.
Changes in politics or factory locations can slow deliveries. Working with a trusted PCB assembler reduces these problems. For example, turnkey providers handle the supply chain to ensure parts arrive on time. This method avoids delays and keeps your fast-turn PCB projects on track.
Build good partnerships with dependable suppliers
Good supplier partnerships save money and improve PCB assembly. Talking often builds trust and leads to better deals. For example, half of surveyed Chief Procurement Officers (CPOs) said strong supplier ties lowered costs. Close teamwork with suppliers can uncover savings and secure better terms.
Reliable PCB assemblers value long-term partnerships. They work well even with urgent orders. For instance, NWLPS uses a supplier management system to check performance and reduce risks. This system improves efficiency and speeds up critical projects.
Tip: Check supplier performance regularly to find ways to improve and strengthen relationships.
Track supplier metrics to ensure steady deliveries
Watching supplier metrics keeps your supply chain reliable. Important metrics include quality, delivery, cost, service, and OTIF (on-time and in-full) rates. Good quality parts avoid recalls, and on-time deliveries prevent delays. Tracking these metrics helps you pick dependable suppliers and keep production smooth.
Metric Type | What It Shows |
---|---|
Quality | Checks if parts meet standards; bad quality causes recalls and hurts your brand. |
Delivery | Measures if parts arrive on time; delays slow production. |
Cost | Compares prices to market rates; finds hidden costs without lowering quality. |
Service | Rates supplier help and problem-solving; shows ability to avoid disruptions. |
OTIF Performance | Tracks orders delivered on time and complete; poor scores lead to shortages. |
Regular checks improve teamwork and efficiency. This helps your PCB assembly service stay reliable during busy times. Using these metrics ensures fast PCB projects without losing quality.
Focus on Quality Checks and Testing
Test during production to keep quality high
Testing during production helps find problems early. This avoids expensive fixes later. Checking quality at every step ensures good results. For example, in-circuit testing (ICT) finds electrical issues and checks parts are placed correctly. This works well for making many boards. Automated optical inspection (AOI) uses cameras to spot tiny defects accurately.
Benefits of testing during production:
Finding problems early saves money and keeps quality high.
Watching key details reduces errors and speeds up work.
Stopping problems before they happen costs less than fixing them.
By preventing mistakes instead of just finding them, you can keep quality high and work faster.
Check if products work as they should
Functional testing makes sure your boards work properly. It checks if the final product does what it’s supposed to do. This testing sees if hardware and software work well together. For example, it ensures programs run smoothly with the board.
Benefit | What It Means |
---|---|
Software works correctly. | Testing ensures the product meets its purpose. |
Saves money. | Fixing problems early avoids big costs later. |
Happy customers. | Reliable products make users trust your brand. |
Adding functional testing helps you deliver great products that meet customer needs and avoid costly mistakes.
Use a strong quality system for better results
A strong quality system keeps production consistent and reliable. It sets clear rules, keeps good records, and spots risks early. For example, regular checks can find problems and fix them before inspections.
Key Part | What It Does |
---|---|
Processes stay consistent. | Clear steps avoid mistakes and keep quality steady. |
Records are complete. | Good documentation helps track and check everything. |
Risks are managed. | Spotting risks early prevents bigger issues later. |
Improvement is ongoing. | Feedback helps make things better over time. |
Regular checks. | Internal reviews prepare for outside inspections. |
Using a quality system ensures steady production, fewer risks, and constant improvement in making PCBs.
Speeding up PCB production while keeping quality high needs smart planning. Use better designs, automation, lean methods, trusted suppliers, and strong quality checks. These steps help PCBA makers deliver great products quickly.
Important industry points show why speed and quality must work together:
Affordable methods should still keep products strong and reliable.
Custom designs need careful planning to balance speed and quality.
Good quality avoids waste and fixes, helping long-term success.
Key Point | What It Means |
---|---|
Quality Checks | Early inspections and AOI find problems fast, improving results. |
Efficient Production | Spotting issues early cuts rework, saving time and money. |
Ongoing Monitoring | Regular checks keep quality steady without slowing production. |
Using these ideas, you can make PCB assembly faster and meet market needs. Keeping both speed and quality is key for lasting success in the PCBA world.
FAQ
How can PCBA production be made faster?
Focus on DFM, use automation, and simplify workflows. Work with trusted suppliers and apply lean methods. These steps cut delays and boost efficiency without lowering quality.
How do you keep quality high while speeding up production?
Use automated tests like AOI and in-line checks. Perform functional tests to ensure everything works well. A strong QMS helps find and fix problems early.
Why is working with suppliers important for PCBA production?
Good suppliers provide quality parts and deliver on time. Strong relationships lower risks, improve speed, and meet tight schedules. Checking supplier performance ensures they stay dependable.
How does automation help in PCB assembly?
Automation makes repetitive tasks faster and more accurate. Machines like pick-and-place tools, AOI systems, and robots improve speed and keep quality steady in big projects.
How do lean methods improve PCBA production?
Lean methods cut waste, fix slowdowns, and make workflows better. Ideas like JIT production and the 5S system save time and keep quality high.
Tip: Mixing lean methods with automation makes production quicker and more reliable.
See Also
Achieving Superior Quality Through PCBA Manufacturing Mastery
Rapid Production: Our Secrets to 24-Hour PCBA Turnaround
Streamlining PCBA Production: Key Time Optimization Strategies
Selecting The Ideal PCBA Manufacturer To Suit Your Requirements
Comparing Turnkey And Consignment PCBA Manufacturing Approaches