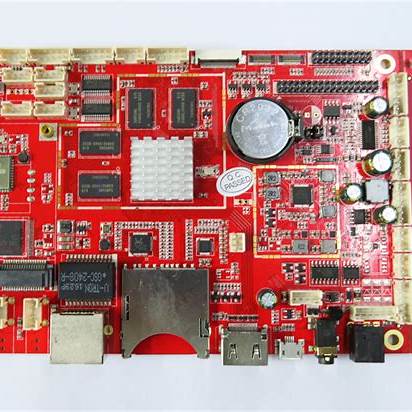
Optimizing important steps in custom PCBA manufacturing and testing is crucial. Each step, from design to delivery, affects your project’s success. By improving these steps, you can avoid delays and mistakes. This also helps ensure on-time delivery. For example, planning well in circuit board making prevents problems. Additionally, working closely with your PCB supplier enhances clear communication, ensuring the work is done correctly. These actions save time and make your final product more reliable.
Key Takeaways
Talking clearly with your PCB supplier prevents errors and saves time. Share all project info to keep things on track.
Good paperwork is important. Give full design files so your PCB company can work well and keep quality high.
Working closely with your PCB assembly company makes better designs and materials. Teamwork helps finish on time and improves products.
Checking quality often during production finds problems early. Use smart tools to make sure your PCBs are top-notch.
Strong packaging keeps your PCBs safe when shipped. Use bubble wrap and antistatic bags for safe delivery.
Order Placement and Initial Planning in Custom PCBA Manufacturing
Clear communication and defining requirements
Good communication is key to making custom PCBA successfully. When you explain your needs clearly, mistakes and delays are less likely. For example, during PCB prototyping, sharing exact details helps find design problems early. This makes sure the manufacturing matches what the final product needs. Poor communication can cause errors and take more time. To avoid this, talk openly with your PCB company and share all project details.
Talking clearly also makes the process better for customers. If you have special technical needs, discussing them with your PCB maker ensures they are done right. Working together improves timelines and builds trust with the best PCB supplier.
Proper documentation to avoid delays
Having good documents helps stop delays. When you give correct and full design files, it helps your PCB company work faster. Design for Manufacturability (DFM) shows how matching designs to production stops extra work. Also, simpler designs make production quicker and easier.
Good documents also cover things like production size, materials, and timeframes. These affect how long and how much the project costs. For instance, listing material choices clearly helps your PCB maker get parts on time. This saves time and keeps quality high, so there’s less need to fix mistakes.
Key Factor | How It Affects Time and Cost |
---|---|
Production Size | Impacts meeting deadlines and completing orders. |
Material Choices | Affects part availability and delivery times. |
Timeframes | Links directly to when the project finishes. |
Quality Checks | Ensures products meet needs, cutting down on fixes. |
Effective collaboration with the PCB assembly company
Working well with your PCB company makes manufacturing easier. Clear talks help everyone understand the project, and quality checks reduce mistakes. By teaming up with a trusted maker, you can pick better designs and materials. This lowers costs and makes production smoother.
Finishing on time depends on how well you work with your PCB maker. Sharing needed info quickly avoids delays. This teamwork also helps solve problems fast. For example, involving your PCB maker in design planning improves manufacturability. This makes products better and keeps customers happy.
Picking the best PCB supplier with experience helps teamwork even more. A good company brings new ideas and skills, ensuring your project succeeds. Their record of delivering quality on time builds trust and long-term partnerships.
Design Validation and Material Procurement for Quality Assurance
Checking design files to avoid mistakes
Checking your design files is very important in PCBA making. It makes sure your designs match what factories can do and meet quality rules. By looking at your designs early, you can find problems before making starts. This saves time and avoids expensive mistakes.
For example, test builds help find design and factory problems early. These tests let you make big fixes if needed. Also, making sure designs match needs ensures the product works right. Finding changes when moving from test to factory lowers risks. The table below shows why checking design files helps:
Proof Type | What It Does |
---|---|
Test Builds | Finds design and factory problems early, allowing big fixes. |
Matching Design to Needs | Ensures the product can be made and works as planned. |
Spotting Changes | Finds changes when moving from test to factory, lowering risks. |
By checking your designs, you make sure your PCB meets quality rules. This lowers the chance of problems and delays.
Making material buying easier
Getting materials quickly and correctly is key to good PCBA work. When buying parts, make sure they work well and have no flaws. Good parts make the final product more reliable. Clear PCB design info also makes buying parts simpler.
To make buying easier, follow these tips:
Parts must work well to ensure the product works.
PCB design info should be clear and easy to use.
Good parts are needed for a reliable product.
A safe supply chain stops fake parts.
Enough parts prevent delays in making products.
Working with a top PCB maker gives you a safe and steady supply chain. Good makers are known for delivering quality on time. They also use new tools and ideas to make buying faster. By focusing on these tips, you keep quality high and save money.
Stopping supply chain slowdowns
Supply chain problems can mess up schedules and cause delays. To stop this, you need a strong supply chain that keeps parts coming. Managing suppliers well and using many sources lowers the risk of running out of parts. Building trust with good suppliers also helps avoid problems.
Using real-time inventory tools can stop slowdowns. These tools help you avoid having too many or too few parts. Just-in-time inventory saves money and keeps parts ready. New tech, like buying software, makes things faster and clearer, cutting down slowdowns.
By fixing supply chain issues early, you protect your business and meet deadlines. Working with a top PCB maker strengthens your supply chain. This ensures your PCBA projects go smoothly and on time.
Optimizing the Manufacturing Process in PCBA
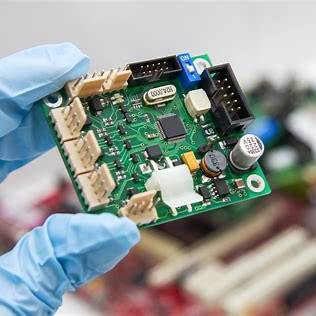
Important steps in making PCBA (like SMT and through-hole)
Making PCBA needs several key steps for good results. Surface Mount Technology (SMT) is a fast and accurate method. It uses machines to place parts on the PCB, lowering mistakes. This process keeps the quality high and consistent. Through-hole assembly works with SMT to secure parts using leads in drilled holes. This method is best for parts needing strong connections.
The through-hole process has four main steps:
Drill: Holes are drilled for the component leads.
Insert: Parts are added by hand or machines.
Solder: Hot solder attaches leads to the board.
Inspect: Checks ensure soldering meets quality standards.
When these steps are improved, production becomes faster and cheaper. Using these methods helps make quick PCBs without losing quality.
Planning production for better results
Good production plans help meet deadlines and keep quality high. A clear plan ensures each step in making PCBs runs smoothly. For example, matching SMT and through-hole schedules avoids delays. Tools that track progress in real-time can adjust plans quickly.
Metrics like cycle time and throughput show how plans help. Cycle time is the total time to make a PCB. Throughput is the number of PCBs made in a set time. Reducing cycle time and boosting throughput gets PCBs to customers faster. This saves time and makes customers happier.
Metric | What It Shows |
---|---|
Cycle Time | Time to make one PCB, showing efficiency. |
Throughput | Number of PCBs made in a certain time, showing production speed. |
Yield Rate | Percentage of PCBs passing checks first try, showing process success. |
Defect Rate | Percentage of bad PCBs, showing areas to fix. |
Equipment Utilization | How well machines are used during production. |
Checking quality during production
Quality checks are important to reduce mistakes in PCBA making. Using advanced tools, like AI systems, finds defects faster. These tools save time and improve production speed. For example, automated checks during SMT and through-hole steps ensure high-quality PCBs.
First Pass Yield (FPY) is a key way to measure quality. It shows the percentage of PCBs passing all checks the first time. A higher FPY means better quality control. Watching defect rates also helps find problems to fix. By focusing on these numbers, you can keep quality steady while improving production.
Spending on quality checks ensures your PCBs meet customer needs. This reduces the need for fixes and builds trust in delivering great PCBs on time.
Testing Services and Quality Assurance
Why thorough testing is important
Testing carefully helps make sure your circuit board works well. It finds problems early, saving money and time. Testing checks quality at every step, ensuring the board is safe and works right. Without good testing, small problems can cause big failures later.
Using tools like the Chi-Square Test shows where issues happen. This improves testing and lowers mistakes. Fixing specific problems makes things better over time. The table below explains how these methods help:
Evidence Type | What It Does |
---|---|
Chi-Square Test | Finds problem areas and improves production steps. |
Targeted Interventions | Fixes certain issues to lower defect numbers. |
Continuous Improvement | Tracks progress and shows how defects are reduced. |
By using these ideas, your circuit board will meet safety rules and stay high quality.
Adding testing to the production process
Adding testing to production catches problems early and saves resources. A custom plan for your circuit board makes testing easier. Tools like Automated Optical Inspection (AOI) and In-Circuit Testing (ICT) can check quality without slowing production.
You can measure how well testing works with key tools. For example, AOI finds assembly mistakes, and continuity tests check electrical paths. The table below shows common testing tools and their uses:
Testing Method | What It Does | Why It’s Important |
---|---|---|
Automated Optical Inspection (AOI) | Finds assembly mistakes automatically | Ensures good quality during production. |
Continuity Test | Checks for broken or short circuits | Confirms the board works electrically. |
Hi-pot Test | Tests safety for high-voltage parts | Makes sure the board is safe to use. |
In-Circuit Testing | Measures electrical values | Checks if components work properly. |
ROSE Test | Looks for leftover solder flux | Keeps the board clean and reliable. |
TDR Test | Measures signal paths | Ensures good signal quality. |
Vibration Tests | Tests strength under shaking | Checks if the board is strong enough. |
Thermal Shock Tests | Tests under hot and cold conditions | Ensures the board works in all climates. |
Using these tools keeps testing on track with production, ensuring quality and timely delivery.
Picking the right testing methods
Choosing the best testing methods keeps your circuit board high quality. Each method has good and bad points, so pick what fits your needs. For example, manual testing is simple but not great for tiny parts. X-ray testing finds hidden issues but needs special tools.
The table below compares testing methods to help you decide:
Testing Method | Good Points | Bad Points | Best For |
---|---|---|---|
Manual Testing | Easy for checking part placement visually. | Hard for tiny parts; doesn’t collect data. | Simple boards with fewer parts. |
X-ray Inspection | Finds hidden solder problems. | Needs special tools and training. | Complex boards with hidden connections. |
In-Circuit Testing | Accurate and easy for workers to use. | Costs more to set up. | Modern electronics with many components. |
Functional Testing | Tests how the board works in real situations. | Takes time and needs special setups. | Complex boards needing full testing. |
FAI Testing | Saves time with automated checks. | Hard to set up at first. | First-time checks for new designs. |
By knowing the pros and cons, you can create a testing plan that works best. This ensures your board is reliable and builds trust with your PCB maker.
Packaging, Delivery, and Client Communication
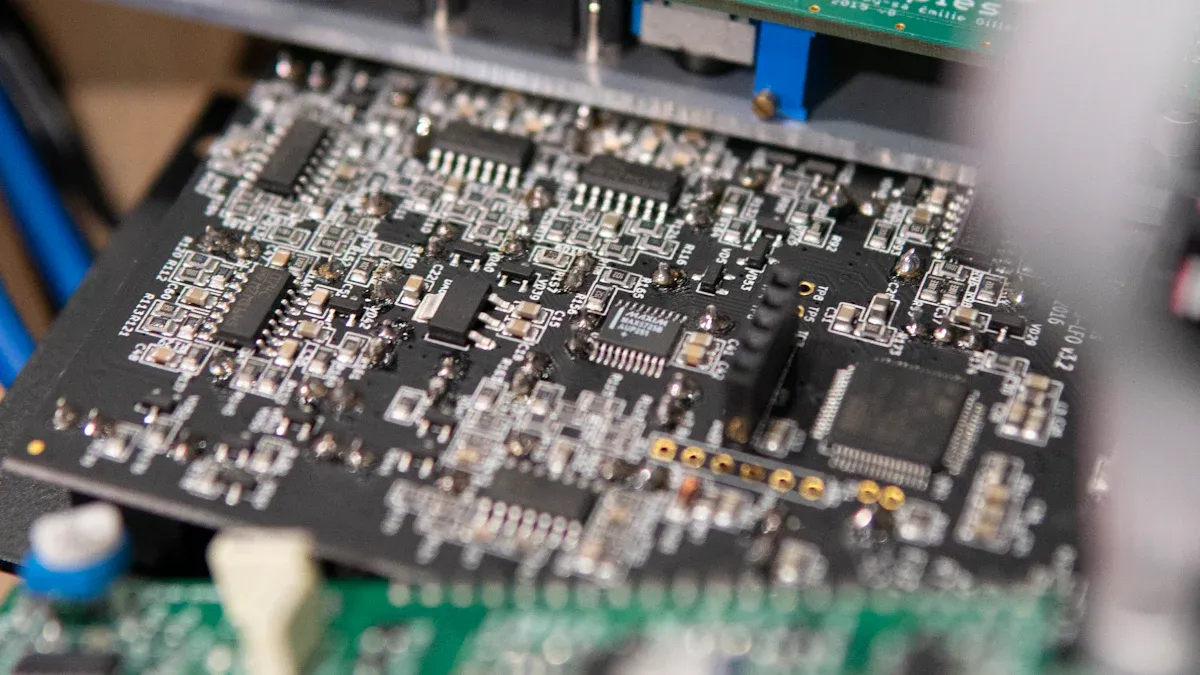
Keeping the pcb safe with good packaging
Good packaging keeps your pcb safe during shipping. It protects against things like moisture and static electricity. Using antistatic bags and bubble wrap helps the pcb arrive in perfect shape, ready to use.
Here are key materials for better protection:
Cushioning Materials: Bubble wrap and foam stop shocks and bumps.
Immobilization Materials: Cardboard dividers and foam keep parts from moving.
Static Protection Materials: Antistatic bags and foam protect against static damage.
Strong packaging lowers repair costs and keeps the pcb working well. This ensures it works properly in devices and makes customers happy with a reliable product.
Delivering on time
On-time delivery is very important in pcb making. A good shipping plan helps boards arrive when needed. Choosing a trusted shipping company reduces delays. Tracking tools let you check where your shipment is.
To stay on schedule, work closely with your pcb supplier. Share your timeline early so they can plan production. This teamwork avoids delays and keeps your project moving forward.
Talking with clients about delivery
Clear updates build trust and improve service. Let clients know where their shipment is and when it will arrive. Sharing tracking info and delivery times helps manage their expectations.
If there’s a delay, tell clients quickly and offer solutions. This shows you care about good service. Being open and honest builds strong relationships. It also ensures clients have a positive experience with your company.
Improving each step in custom PCBA making helps things run better. From checking designs to packing, every part is important. Focusing on these steps can stop delays and make results better.
Working with a trusted PCB company makes the process stronger. Their skills help avoid mistakes and finish work on time. This teamwork ensures your PCB projects are done right.
Always aim for quality and speed in your projects. Doing this not only makes your PCB work well but also earns your clients’ trust.
FAQ
How long does it take to make a PCB?
The time depends on your design and order size. Simple projects take 5-10 business days. Faster services can shorten this time.
How is PCB quality checked during production?
Quality is checked using tests like AOI and ICT. These tests find problems early to ensure the PCB works well and is safe.
Can urgent PCB orders be completed quickly?
Yes, some companies offer fast services for urgent orders. They speed up steps and focus on your project to deliver quickly.
What materials are used to make PCBs?
PCBs use FR4 for the base, copper for circuits, and solder masks for protection. These materials make PCBs strong and reliable.
How do I pick the best PCB maker?
Choose a company with good experience, modern tools, and great service. Make sure they handle everything from design checks to delivery for your needs.
See Also
Comparing Turnkey PCBA And Consignment Manufacturing Approaches
Achieving Superior Results Through Effective PCBA Manufacturing Techniques
Guidelines For Assembling PCBA And Avoiding Typical Mistakes
Choosing The Ideal PCBA Manufacturer To Meet Your Requirements
Understanding The Key Differences Between Prototype And Production PCBs