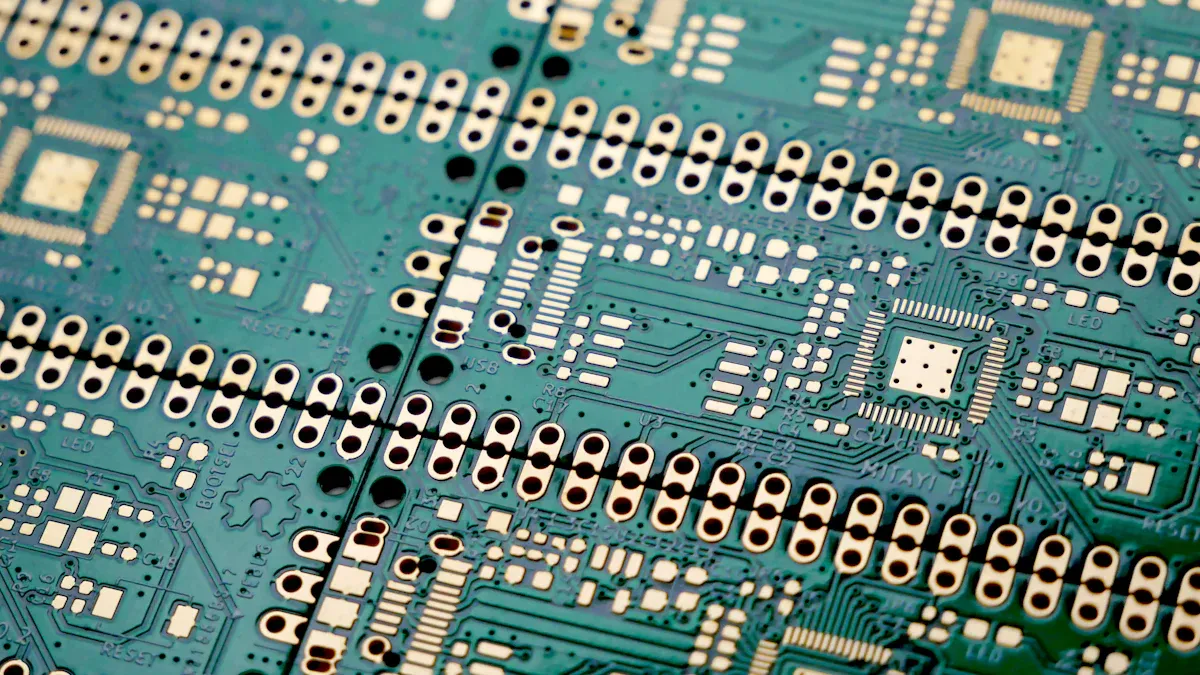
FDA rules play a crucial role in ensuring the safety and performance of medical devices. In the realm of Medical device IoT PCB manufacturing USA, reliability and traceability are essential, especially for devices like patient monitors and telemedicine tools, where precision directly impacts health outcomes. Effective monitoring systems require robust compliance with these regulations. As the adoption of medical IoT devices continues to grow rapidly, adhering to FDA standards is imperative for successful IoT PCB manufacturing for medical devices in the USA, ensuring both safety and optimal functionality.
Key Takeaways
FDA rules make sure medical devices are safe to use. Follow these rules to protect people and keep quality high.
Use a good quality system to track each production step. This helps follow rules and makes devices more reliable.
Add systems to track materials and processes. This helps find issues and keeps devices safe to use.
Test medical devices often in real-life situations. This finds problems and ensures devices work well for people.
Work closely with suppliers. Talking often and checking regularly helps keep quality and follow rules during manufacturing.
FDA Compliance in Medical Device IoT PCB Manufacturing USA
What is FDA Compliance for Medical Devices?
FDA compliance means following strict rules set by the U.S. Food and Drug Administration. These rules make sure medical devices are safe, work well, and are high quality. For medical device IoT PCB manufacturing USA, following these rules is required by law. It protects patients and ensures devices like monitors and telemedicine tools are reliable.
The FDA checks compliance through inspections, tracking devices after they are sold, and quality system rules. For example, 21 CFR Part 820 ensures devices are made to meet tough safety rules. Manufacturers must also have systems to handle complaints and report problems. These steps help make sure devices work properly and don’t harm patients.
Rules for Medical PCB Manufacturing
Making medical PCBs follows strict rules to keep quality and safety high. Important standards include:
ISO 13485: Focuses on managing quality and tracking materials.
IEC 60601: Sets safety rules for medical electrical devices like PCBs.
IPC Standards: Includes IPC-A-600, IPC-A-610, IPC-A-630, and IPC 6012 for PCB testing and quality.
Standard | What It Does |
---|---|
ISO 13485 | Ensures quality systems for medical devices, including tracking. |
IEC 60601 | Sets safety and performance rules for medical electrical devices. |
IPC-A-600 | Lists rules for circuit board quality. |
IPC-A-610 | Explains quality rules for electronic parts. |
IPC-A-630 | Covers making, testing, and inspecting PCBs. |
IPC 6012 | Details performance and testing needs for PCBs. |
FDA Regulations | Controls how medical devices are made under 21 CFR Part 820. |
Following these rules shows manufacturers care about safety and quality. It also helps meet the needs of doctors and patients.
Why Compliance Matters in Medical PCB Manufacturing
Compliance is very important for medical PCB manufacturing. First, it keeps devices safe and working well. Devices that don’t meet rules can harm patients or stop working. For example, the FDA tracks how often devices cause serious problems and how well they work.
Statistic | What It Measures |
---|---|
Rate of serious adverse events | How often devices cause serious problems. |
Probability of device effectiveness | How likely the device works as it should. |
Patient’s survival probability | The chance a patient survives using the device. |
Sensitivity and specificity | How accurate a diagnostic device is. |
Second, compliance helps avoid big problems like recalls or fines. Breaking rules can delay selling products and hurt a company’s reputation. By following rules, companies can compete better and earn trust from customers.
Finally, compliance helps companies improve. FDA inspections are not just checks; they help companies fix problems and get better. Treating inspections as a way to improve ensures devices stay safe and reliable.
Tip: Focus on fixing and preventing problems during inspections. This helps keep your devices safe and high quality.
High Reliability in Medical Device PCBA Manufacturing
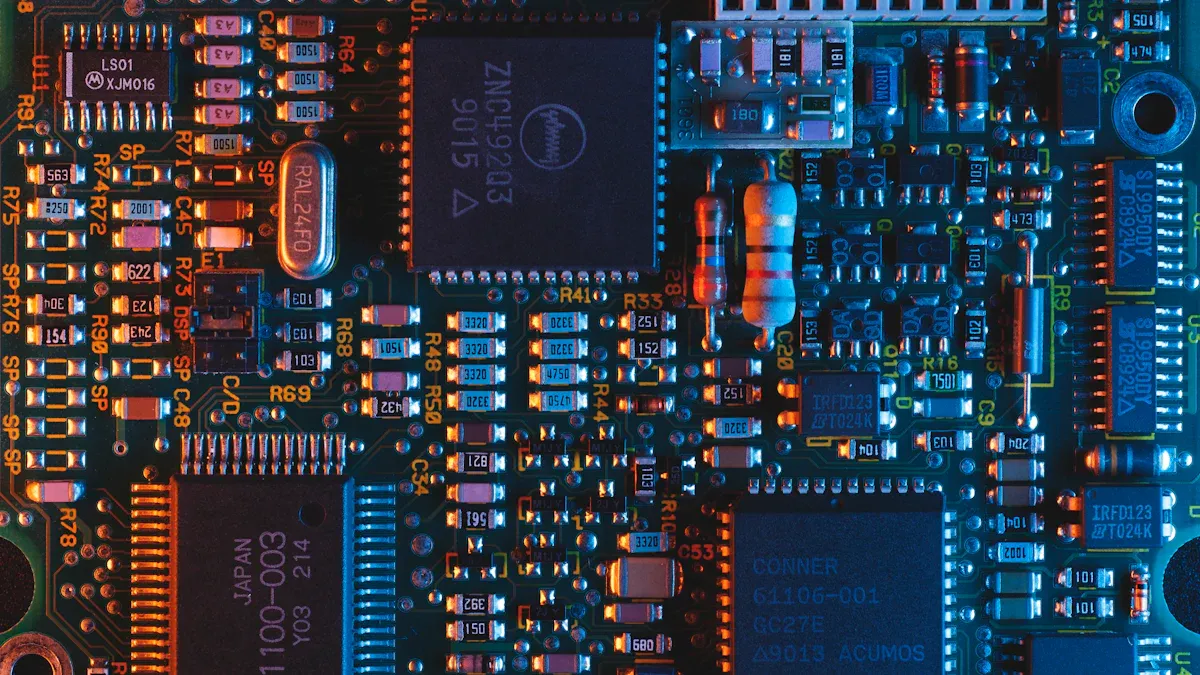
Role of Design Controls in Reliability
Design controls are key to making reliable medical devices. Using clear steps helps find and fix risks early. Statistical Process Control (SPC) tracks quality by watching important numbers. Tools like control charts show changes quickly. This keeps production steady and high-quality.
Failure Mode and Effects Analysis (FMEA) finds and ranks possible problems by risk level. Fixing big risks first keeps devices working well. Tools like Kaplan-Meier estimators predict how long parts will last. They also show how often parts might fail in real use.
Design Control Measure | Purpose | Methods and Metrics |
---|---|---|
Statistical Process Control (SPC) | Track and control quality using key data. | Control Charts, Process Capability (Cp, Cpk). |
Failure Mode and Effects Analysis (FMEA) | Find and rank risks by importance. | Risk Priority Number (RPN). |
Reliability and Survival Analysis | Predict part lifespan and failure rates. | Kaplan-Meier Estimator, Cox Model. |
Material Selection for Medical-Grade PCBAs
Picking the right materials makes medical PCBs last longer. Use biocompatible materials that handle cleaning without breaking down. Finishes like gold or ENIG stop rust and keep parts connected well.
Materials must handle heat, pressure, and chemicals during use. Fire-resistant and UL-approved materials add safety. For implants, use safe, non-toxic materials to avoid bad reactions. Strong materials keep devices working and patients safe.
Testing Protocols for Medical Devices
Testing ensures medical PCBs work well and stay reliable. Tests copy real-life stress to check device performance. Heat and pressure tests check microvias for strength under tough conditions.
Test methods must be accurate and precise. Models like linear regression and Monte Carlo simulations help find weak spots. These tests improve device reliability. Following strict testing rules ensures devices meet FDA standards and work well for patients.
Medical PCB Traceability and Why It Matters
Traceability helps keep medical devices safe and high-quality. It tracks every part and step in making medical PCBs. This ensures devices follow rules and work well in healthcare.
How Traceability Systems Work
Traceability systems make production faster and meet rules. They track each step, from materials to finished products. Problems can be found and fixed quickly, lowering risks and improving quality.
Benefits of traceability systems include:
Cuts data entry time by 75%.
Lowers unfinished work by 32%.
Boosts quality by 18%.
Saves nearly 10% on costs with lean methods.
Recall costs grow ten times at each product stage.
These systems also improve how PCBs are made. They give real-time updates, control production, and cut waste. Each PCB meets quality checks. The table below shows more benefits:
Benefit | What It Does |
---|---|
Better Production Control | Helps manage and monitor production levels. |
Less Waste | Finds problems to reduce waste during manufacturing. |
Makes sure items pass quality checks. | |
Real-time Supply Chain Info | Gives instant updates for better decisions. |
Secure Records | Uses blockchain to keep records safe and unchangeable. |
Fewer Human Errors | Automation lowers mistakes during production. |
Problem Solving | Quickly finds and fixes issues when they happen. |
Using these systems ensures medical devices are safe and reliable.
Keeping Records for PCB Traceability
Good records are key for PCB traceability. They show where parts come from, where they’re made, and how they’re used. This helps find defects, check quality, and follow rules.
To improve traceability, focus on:
Writing down where each part comes from.
Keeping detailed records to spot defects.
Showing you follow safety and quality rules.
Clear records make work easier and customers happier. Accurate records help fix problems fast and prove your focus on safety.
Managing Data for Rules and Audits
Managing data is important for following rules and passing audits. Organized systems store, find, and study data easily. This supports traceability and ensures FDA compliance.
Companies with strong data systems meet rules 70% more often. They spend 45% less on rule-following tasks and succeed more. Good data systems save money, improve work, and make PCBs more reliable.
To manage data better, focus on:
Using systems that show real-time production and supply info.
Automating tasks to avoid mistakes and keep data correct.
Updating records often to match new rules.
These steps make audits easier and show your commitment to quality medical devices.
Best Practices for FDA-Compliant PCBA Manufacturing
Setting Up Quality Management Systems
A good quality management system (QMS) is very important. It helps make sure medical PCBs are made safely and correctly. Create a system to check every step of production. This keeps everything consistent and follows the rules. Start by making clear steps for design, building, and testing. Use tools like charts to track progress and spot problems early. Check your QMS often to stay on track and improve.
Keeping records is a big part of your QMS. Write down every step, where materials come from, and test results. These records help with tracking and make audits easier. A strong QMS ensures medical devices are safe and work well for patients.
Managing Risks in Medical PCB Manufacturing
Managing risks is key to making safe medical PCBs. Look for risks at every step, from picking materials to testing. Tools like FMEA help you find and rank risks by importance. Fixing the biggest risks first keeps devices safe and working.
The environment can also cause problems. Materials must handle heat, pressure, and cleaning without breaking. Stress tests show how devices work in real life. By managing risks early, you make devices safer and follow the rules better.
Working with Suppliers for Compliance
Working closely with suppliers helps meet rules and improve quality. Use online tools to share updates and talk easily. Regular updates help fix problems before they grow. Audits make sure suppliers follow FDA rules and meet your quality needs.
Good supplier relationships also make devices more reliable. When suppliers know your rules, they give you better materials. This teamwork lowers risks and ensures devices work well for patients.
Overcoming Challenges in Medical Device PCBA Manufacturing
Fixing Common Compliance Problems
Making medical PCBAs can be tricky. You need to follow strict rules, keep records accurate, and check processes carefully. Rules like ISO 13485 and FDA’s 21 CFR Part 820 require strong quality systems and detailed paperwork. Without these, devices might fail tests or harm patients.
To solve these problems, use better manufacturing methods. For example, adding underfill adhesive and using a laser stencil process makes solder joints stronger for 0.4mm pitch BGAs. This can make devices last up to 100,000 hours. Another method is using stepped coverlay and thicker copper for flex boards. This lowers defect rates from 8% to 0.3%, saving lots of money. These methods help meet rules and make devices work better.
Problem | Fix | Result |
---|---|---|
Weak solder joints for 0.4mm BGAs | Underfill adhesive + laser stencil process | Lasts up to 100,000 hours |
Flex board defects | Stepped coverlay + thicker copper | Defects drop from 8% to 0.3% |
Soldering issues with heat mismatch | Gradient heat + copper pillar connections | Lasts up to 50,000 hours |
Solving Traceability and Record-Keeping Issues
Tracking materials and steps is key for safe devices. You must know where parts come from and what they’re made of. Good records help pass audits and follow changing rules.
Using traceability systems makes tracking easier. These systems show every step in making PCBAs. They help improve designs and cut costs. Keeping records of materials and processes also helps with long-lasting products. This ensures you meet rules and can prove it when needed.
Handling Supply Chain and Material Problems
Problems in the supply chain can slow down production. Issues like worker shortages, sterilization rules, and cyberattacks are common. For example, COVID-19 caused material shortages and higher costs. These problems show why managing the supply chain is so important.
To avoid these issues, work with different suppliers and build strong partnerships. Check suppliers often and watch the supply chain in real time. Protecting patient data with cybersecurity is also important to meet health rules.
Problem | What It Means |
---|---|
Worker Shortages | Fewer skilled workers due to aging and fewer new hires. |
Sterilization Rules | Changing methods to meet health standards and lower risks. |
Cybersecurity Risks | Protecting patient data with strong security systems. |
Supply Chain Delays | COVID-19 caused material shortages and higher costs. |
Surgery Declines | Sales dropped 82% during the pandemic, showing financial risks. |
By solving these problems, you can make your manufacturing process stronger and safer.
Following FDA rules, ensuring reliability, and keeping good records are key. These steps protect patients, improve devices, and meet strict rules.
Evidence Type | What It Means |
---|---|
Strict Rules | Medical devices must follow tough rules like FDA’s QSR and the EU’s MDR. These rules track every step of a product’s life. |
Keeping Patients Safe | Good records link all parts and documents to protect patients. |
Watching After Sales | Records help find problems after sales, like during recalls. |
To meet these goals, use strong quality systems and test devices carefully. Follow FDA 21 CFR 820.30 to make sure devices are safe and work well. Doing this builds trust and helps your business grow in the medical IoT field.
FAQ
What does FDA compliance mean for PCBA manufacturing?
FDA compliance means following strict rules for safety and quality. It includes keeping detailed records and using quality systems. These steps protect patients and make devices reliable.
Why is traceability important in medical PCBA manufacturing?
Traceability tracks every part and step in making PCBAs. It helps find and fix problems fast. This improves quality, meets rules, and keeps patients safe.
How can you improve reliability in medical IoT devices?
To improve reliability, use strong designs and good materials. Test devices carefully with stress tests. Tools like FMEA find risks early to keep devices working well.
What role do suppliers play in FDA compliance?
Suppliers provide parts that meet safety rules. Working with them ensures they know your quality needs. Regular checks and good communication keep devices reliable.
How do you handle supply chain challenges in PCBA manufacturing?
Use many suppliers and watch your supply chain closely. Build strong partnerships and protect data with cybersecurity. These steps prevent delays and keep production steady.
See Also
New Developments in FDA-Approved PCBA Services for Healthcare Devices
The Importance of PCBA Manufacturing for IoT Devices Today
Navigating ITAR Regulations for PCBA Production in 2025
Is Outsourcing Medical Device PCBA Production Worth It? Pros and Cons