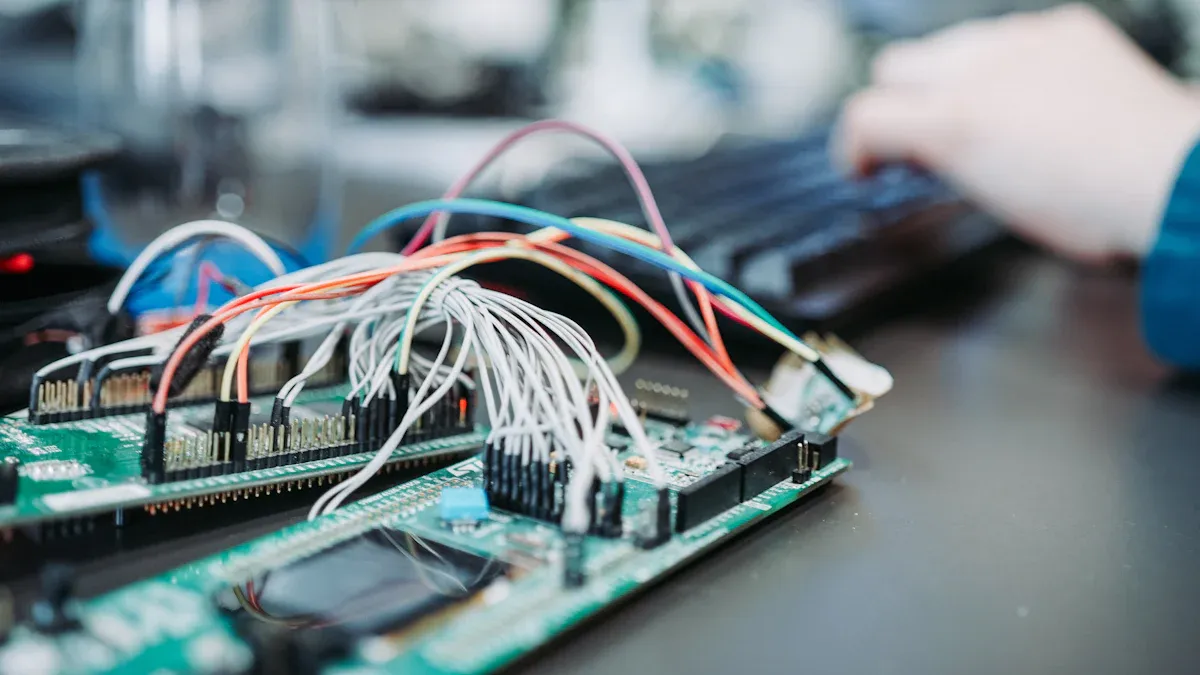
IIoT device manufacturing is revolutionizing the way you approach manufacturing. These IIoT devices provide real-time data, enabling you to monitor operations as they happen. This visibility helps you track materials, tools, and personnel, ensuring resources are allocated efficiently. Predictive maintenance, powered by IIoT device manufacturing, analyzes equipment performance to prevent unexpected failures. This approach reduces downtime and extends the lifespan of your machinery. For instance, companies have reported a 9% improvement in overall equipment effectiveness and saved $25 million by avoiding unnecessary production lines. These technologies not only improve productivity but also streamline operations for better results.
Key Takeaways
IIoT devices give live data to track work and decide fast.
Predictive maintenance stops sudden breakdowns, saving money and machines.
Live tracking finds problems, improves work speed, and cuts delays.
Using IIoT tools saves money by managing resources better.
IIoT makes workplaces safer, boosting teamwork and worker happiness.
Key Benefits of IIoT Device Manufacturing
Predictive Maintenance for Reduced Downtime
Predictive maintenance is one of the most transformative benefits of IIoT device manufacturing. By leveraging real-time data and predictive analytics, you can anticipate equipment failures before they occur. This proactive approach minimizes unplanned downtime and ensures your production lines operate smoothly. For example, manufacturers using predictive maintenance have reported a 30-50% reduction in machine downtime. Additionally, predictive maintenance strategies can increase uptime by 10-20% and reduce maintenance costs by 10-40%.
IIoT sensors embedded in machinery continuously monitor critical parameters like temperature, vibration, and pressure. These sensors detect anomalies and send alerts, allowing you to take corrective action promptly. This not only extends the lifespan of your equipment but also optimizes your manufacturing processes by reducing disruptions.
Tip: Implementing predictive maintenance can significantly enhance your operational efficiency and save costs in the long run.
Real-Time Monitoring for Operational Insights
Real-time monitoring is a game-changer for IIoT-enabled manufacturing environments. With IIoT devices, you gain instant visibility into your operations, enabling you to make informed decisions quickly. Continuous monitoring of equipment and production processes helps you detect anomalies and address them before they escalate into major issues.
For instance, IIoT sensors collect critical data such as temperature, vibration, and energy consumption. AI-driven analytics then process this data to forecast maintenance needs and optimize performance. This approach minimizes unplanned outages and ensures your production lines remain operational longer. Real-time analytics also provide actionable insights that drive operational excellence, helping you identify inefficiencies and improve productivity.
Embedding sensors in machinery allows for continuous tracking of performance, which boosts productivity and reduces downtime. By leveraging real-time data, you can enhance your manufacturing processes and achieve better results.
Process Optimization to Maximize Efficiency
IIoT device manufacturing plays a crucial role in optimizing your manufacturing processes. By integrating IIoT technologies, you can streamline operations, reduce waste, and improve overall efficiency. Comprehensive process data generated through IIoT enables you to identify bottlenecks and implement solutions that enhance value creation.
The advancement of digitalization has enabled connected products and processes, further enhancing productivity and efficiency in industrial settings. For example, organizations that adopt IIoT technologies often experience up to a 50% reduction in unplanned downtime and a 20-40% increase in asset utilization. Additionally, process optimization through IIoT can lead to a 15-20% improvement in overall equipment effectiveness (OEE) and up to a 30% boost in productivity.
Practical applications, such as the use of RFID tags in inventory management, showcase the tangible benefits of IIoT adoption. These tags enhance traceability and improve downstream operations, ensuring your processes run smoothly. By embracing IIoT, you can stay competitive in an evolving market landscape and achieve measurable efficiency gains.
Note: Failing to adopt IIoT technologies may put your business at a disadvantage in today’s competitive manufacturing environment.
Cost Savings Through Resource Management
Efficient resource management is critical for reducing costs in manufacturing. IIoT devices empower you to monitor and optimize resource usage, ensuring minimal waste and maximum efficiency. By collecting real-time data, these devices help you identify areas where resources like energy, raw materials, and labor are underutilized. This insight allows you to make adjustments that save money and improve productivity.
For example, IIoT sensors can track energy consumption across your facility. By analyzing this data, you can pinpoint energy-intensive processes and implement strategies to reduce power usage. Some manufacturers have reported up to a 20% reduction in energy costs after adopting IIoT technologies. Additionally, IIoT-enabled inventory management systems ensure you maintain optimal stock levels, preventing overstocking or shortages that could disrupt production.
Tip: Use IIoT-powered analytics to forecast demand and align your resource allocation accordingly. This approach minimizes waste and maximizes profitability.
Another way IIoT helps you save costs is through predictive maintenance. By addressing equipment issues before they escalate, you avoid expensive repairs and production delays. This proactive strategy not only extends the lifespan of your machinery but also reduces the need for emergency maintenance, which often comes with higher costs.
Enhanced Safety and Workforce Collaboration
IIoT devices play a pivotal role in creating a safer and more collaborative work environment. Advanced equipment and wearable devices collect data to monitor workplace conditions and worker health, ensuring safety remains a top priority.
The National Safety Council estimates over 4.6 million workplace injuries occur annually in the U.S., costing over $161 billion.
In 2020, the private manufacturing industry reported 373,300 nonfatal injuries and illnesses.
By integrating IIoT technologies, you can significantly reduce these numbers. For instance, motion sensor-activated systems and interlocking dock controls prevent accidents by detecting unsafe conditions. Wearable devices like smartwatches monitor health parameters such as heart rate and body temperature. These devices alert workers and supervisors to potential hazards, enabling quick action to prevent injuries.
AI-driven predictive maintenance also enhances safety by preventing equipment failures that could endanger workers. Real-time monitoring of environmental conditions, such as air quality and temperature, ensures your team operates in a safe and healthy environment.
Note: A safer workplace not only protects your employees but also boosts morale and productivity. Workers are more likely to collaborate effectively when they feel secure and supported.
Collaboration improves further when IIoT devices facilitate seamless communication. For example, connected devices allow workers to share real-time data and insights, fostering teamwork and problem-solving. This level of connectivity ensures everyone stays informed and aligned, leading to smoother operations and better outcomes.
Emoji Insight: 🛠️ Leveraging IIoT for safety and collaboration creates a win-win scenario for both your workforce and your bottom line.
Applications of IIoT in Smart Factories
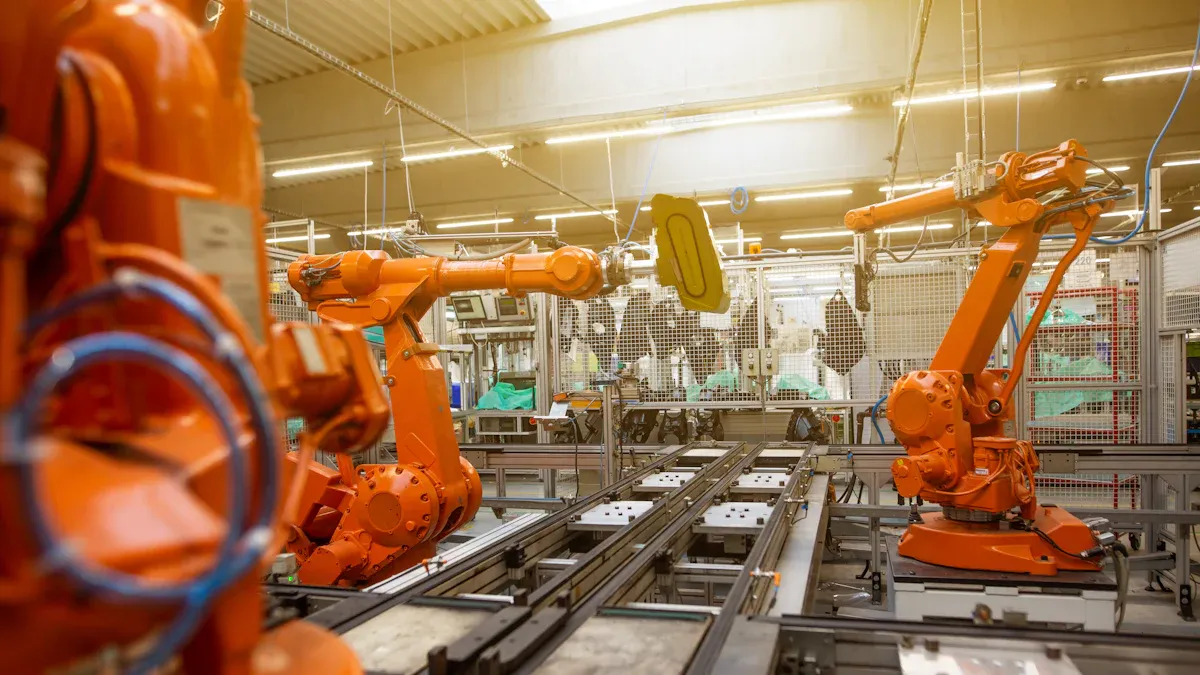
Asset Tracking and Operational Management
IIoT devices revolutionize asset tracking and operational management in smart factories. By using technologies like GPS and RFID, you can monitor the location and condition of assets in real time. This visibility ensures that tools, equipment, and materials are always where they need to be, reducing delays and improving efficiency. For example, real-time location systems allow you to quickly locate assets, streamlining operations and minimizing downtime.
IIoT sensors also track the condition of materials throughout the supply chain. Automated alerts notify you of inventory disruptions, enabling you to address issues before they impact production. A paper and pulp company, Artesis, used IoT sensors for predictive maintenance, achieving a 20% reduction in maintenance costs and a 10% increase in production efficiency. These results highlight the critical role of IIoT in optimizing asset management.
Tip: Implement IIoT-powered asset tracking to reduce waste and improve operational efficiency in your factory.
Quality Control and Defect Prevention
IIoT devices enhance quality control by providing real-time data on production conditions. Sensors embedded in machinery collect information such as temperature, pressure, and humidity, ensuring that products meet quality standards. This data allows you to detect defects early, reducing waste and improving customer satisfaction.
For instance, IIoT implementations in quality control have achieved impressive results:
Metric | Value |
---|---|
Processing Time per Casting | 2.3 seconds |
Throughput | 26 castings/minute |
Casts per Hour | 1560 casts/hour |
Casts per Day | 37,440 casts/day |
Mean Absolute Error (MAE) | 0.05 mm |
Root Mean Square Error (RMSE) | 0.07 mm |
These metrics demonstrate how IIoT can improve precision and efficiency in manufacturing processes. Companies like Siemens and Bosch have successfully implemented IIoT for quality control. Siemens improved production efficiency and reduced waste, while Bosch enhanced operational data sharing, leading to better troubleshooting and lower warranty costs.
Note: Real-time quality monitoring not only reduces defects but also boosts your factory’s reputation for delivering high-quality products.
Supply Chain Automation and Optimization
IIoT devices play a vital role in automating and optimizing supply chains. By collecting and analyzing vast amounts of data, these devices provide insights that help you streamline operations and reduce inefficiencies. Analysts predict global data consumption will double from 74 zettabytes in 2021 to 149 zettabytes by 2024, reflecting the growing importance of data in supply chain management.
Poor coordination among supply chain partners costs industries billions annually. For example, inefficiencies in the U.S. food industry alone result in $30 billion in losses each year. IIoT devices address these challenges by improving operational visibility and enabling better communication between stakeholders. Connected sensors monitor stock levels, ensuring you maintain optimal inventory and avoid disruptions.
Emoji Insight: 📦 Automating your supply chain with IIoT can save costs, reduce delays, and improve overall efficiency.
By adopting IIoT technologies, you can transform your supply chain into a well-oiled machine, capable of meeting the demands of modern manufacturing.
Energy Efficiency and Sustainability
Energy efficiency and sustainability have become critical priorities in modern manufacturing. By adopting IIoT technologies, you can significantly reduce energy consumption while promoting environmentally friendly practices. IIoT devices enable real-time monitoring of energy usage, allowing you to identify inefficiencies and optimize processes. For example, sensors embedded in machinery track energy consumption patterns, helping you pinpoint areas where energy is wasted. This data empowers you to make adjustments that lower costs and reduce your factory’s carbon footprint.
Predictive maintenance, another key feature of IIoT, also contributes to energy efficiency. By addressing potential equipment failures before they occur, you can avoid sudden breakdowns that often lead to energy waste. Modern systems integrate energy efficiency metrics with equipment reliability data, ensuring that your operations remain both cost-effective and sustainable. Additionally, IIoT solutions allow you to complete the same tasks with less energy, enhancing overall efficiency.
The collective adoption of IIoT across industries has a profound impact on sustainability. Smart systems not only reduce energy consumption but also contribute to broader environmental goals. For instance:
Real-time monitoring optimizes energy usage, minimizing waste.
Predictive maintenance prevents sudden failures, reducing unnecessary energy expenditure.
Advanced systems identify inefficiencies, enabling timely interventions to save energy.
By leveraging IIoT, you can align your manufacturing processes with sustainability goals while maintaining high levels of productivity. This approach not only benefits the environment but also enhances your company’s reputation as a responsible industry leader.
Tip: Use IIoT-powered energy analytics to track and improve your factory’s energy efficiency. Small changes can lead to significant savings over time.
Advanced Factory Automation
IIoT technologies are at the heart of advanced factory automation, transforming how you manage production processes. By interconnecting machines and automating data acquisition, you can achieve unprecedented levels of precision and efficiency. For example, companies like Tastitalia have used IIoT to gain precise control over production costs and quality, enhancing their competitiveness in the market.
Real-time data collection and analysis play a pivotal role in automation. IIoT devices continuously monitor equipment performance, providing insights that help you optimize operations. This level of automation reduces manual intervention, minimizes errors, and accelerates production timelines. For instance, the Cornaglia Group improved production efficiency by integrating IIoT solutions, enabling better cost control and faster decision-making.
Predictive maintenance also enhances automation by ensuring that your machinery operates at peak performance. Companies like Ansaldo Energia have digitized their production sites, using IIoT to optimize maintenance schedules and streamline production processes. Similarly, Volkswagen’s Industrial Cloud integrates data across factory sites, potentially increasing productivity and reducing costs on a large scale.
The benefits of advanced factory automation extend beyond efficiency. By automating repetitive tasks, you can free up your workforce to focus on more strategic activities. This not only boosts morale but also fosters innovation within your team. Additionally, automated systems improve product quality by maintaining consistent production standards.
Emoji Insight: 🤖 Embracing IIoT-driven automation allows you to stay ahead in a competitive market while delivering high-quality products efficiently.
By adopting IIoT technologies, you can transform your factory into a smart, automated facility that meets the demands of modern manufacturing. The integration of advanced systems ensures that your operations remain agile, efficient, and future-ready.
Core Components of an IIoT System
Sensors and Actuators for Data Collection
Sensors and actuators form the backbone of any IIoT system. Sensors gather critical data from your manufacturing equipment, such as temperature, pressure, and vibration levels. This data helps you monitor the health of your machinery and ensures smooth operations. Predictive maintenance solutions rely heavily on these sensors to detect anomalies and prevent equipment failures. Actuators, on the other hand, respond to the data collected by sensors and execute actions like adjusting machine settings or stopping operations during emergencies.
To measure their effectiveness, you can track key performance indicators (KPIs) such as defect rates, first-pass yield, and on-time delivery performance. Here’s a quick overview:
KPI | Description |
---|---|
Defect rates and types | Measures the number and types of defects in products. |
First-pass yield | Indicates the percentage of products manufactured correctly without rework. |
Scrap and rework rates | Tracks the amount of material wasted and the need for reprocessing. |
Customer complaint rates | Assesses the frequency of customer complaints regarding product quality. |
On-time delivery performance | Evaluates the ability to deliver products as scheduled. |
Modern tools like automated inspection systems, vision systems, and real-time monitoring devices enhance the accuracy of data collection. These technologies ensure your manufacturing processes remain efficient and reliable.
Tip: Regularly calibrate your sensors to maintain data accuracy and improve operational outcomes.
Gateways for Seamless Data Transmission
Gateways act as the communication bridge between your sensors and the cloud. They collect data from various devices and transmit it securely to centralized systems for analysis. Without gateways, your IIoT system would struggle to handle the vast amounts of data generated by sensors.
These devices also ensure seamless communication by converting different protocols into a unified format. For example, they can translate data from legacy systems into formats compatible with modern cloud platforms. This capability allows you to integrate new technologies without overhauling your existing infrastructure.
Gateways also play a crucial role in enhancing security. They encrypt data during transmission, protecting it from potential cyber threats. By using gateways, you can ensure that your data remains safe while enabling real-time decision-making.
Emoji Insight: 🌉 Think of gateways as the bridges that connect your factory floor to advanced analytics tools, ensuring smooth and secure data flow.
Cloud Platforms for Data Analysis
Cloud platforms are where the magic of IIoT data analysis happens. These platforms store and process the data collected by your sensors, providing actionable insights to improve your operations. For instance, predictive analytics tools on cloud platforms can forecast equipment failures, helping you schedule maintenance before issues arise.
Several manufacturers have already seen remarkable improvements by adopting cloud platforms. HarbisonWalker International improved forecast accuracy and achieved over 90% on-time delivery by consolidating data onto a single cloud system. Western Digital reduced data reporting time from 24-48 hours to just 20 minutes, enabling faster decision-making.
Manufacturer | Improvement in Accuracy and Speed |
---|---|
HarbisonWalker International | Improved forecast accuracy and on-time delivery to over 90% by consolidating data onto a single cloud ERP system. |
Western Digital | Reduced data reporting time from 24-48 hours to about 20 minutes, enabling quicker access to business intelligence. |
Bitron | Eliminated data silos, allowing managers to create reports easily and make empirical decisions using accurate data. |
Bonnell Aluminum | Enhanced visibility into supply chains, leading to better purchasing and inventory decisions through connected data. |
Cloud platforms also improve data accuracy by automating processes and reducing human errors. Faster time-to-insight ensures you can respond to challenges quickly, keeping your production lines running efficiently.
Note: Choose a cloud platform that aligns with your specific manufacturing needs to maximize its benefits.
Machine Learning and Analytics Tools
Machine learning (ML) and analytics tools are transforming how you manage manufacturing processes. These technologies analyze vast amounts of data collected by IIoT devices, providing actionable insights that improve efficiency and reduce downtime. By leveraging ML algorithms, you can predict equipment failures, optimize production schedules, and enhance overall operational performance.
Here’s how ML and analytics tools are making an impact across industries:
In the manufacturing industry, ML algorithms analyze sensor data from production equipment to predict maintenance needs, reducing downtime and optimizing efficiency.
In the energy sector, AI and ML monitor parameters like temperature and pressure to predict equipment failures, ensuring consistent power generation and minimizing costly shutdowns.
In transportation and logistics, ML models predict maintenance needs for vehicles by analyzing engine performance and wear-and-tear data, allowing for planned maintenance during scheduled downtimes.
In healthcare facilities, AI-driven predictive maintenance ensures the availability of critical medical devices by monitoring performance and preventing equipment failures.
These tools also enhance analytics by identifying patterns and trends in your data. For example, predictive analytics can forecast demand, helping you adjust production levels to avoid overstocking or shortages. This level of precision ensures you allocate resources effectively, saving time and money.
Tip: Use ML-powered analytics to uncover hidden inefficiencies in your processes and make data-driven decisions that boost productivity.
User Interfaces for Real-Time Decision-Making
User interfaces (UIs) designed for real-time decision-making empower you to monitor and control manufacturing operations with ease. These interfaces present complex data in a clear and intuitive format, enabling you to act quickly and effectively.
Real-time data analytics allows you to continuously monitor production processes. This capability helps you identify bottlenecks and inefficiencies before they escalate, enhancing operational efficiency. For instance, unplanned downtime costs industrial manufacturers an estimated $50 billion annually. Predictive maintenance, supported by real-time UIs, can reduce machine downtime by 30-50% and increase machine life by 20-40%.
Key benefits of real-time UIs include:
Improved productivity: 75% of manufacturing quality issues can be prevented with proper real-time monitoring and analytics.
Cost savings: IIoT implementations in manufacturing are expected to generate economic value between $1.2 and $3.7 trillion globally by 2025.
Enhanced decision-making: A recent study found that 86% of manufacturing executives consider real-time analytics crucial to their operational strategy.
These interfaces also foster collaboration by providing a centralized platform where teams can access and share data. This transparency ensures everyone stays aligned, leading to smoother operations and better outcomes.
Emoji Insight: 📊 Real-time UIs simplify complex data, helping you make faster, smarter decisions that drive success.
Challenges in IIoT Device Manufacturing
Addressing Security and Data Privacy Concerns
Security and data privacy remain critical challenges in IIoT device manufacturing. As you integrate IIoT systems, vulnerabilities in legacy equipment can expose your operations to cyber threats. Many older systems cannot receive updates without disrupting production, leaving them open to attacks. Flat network configurations further increase risks by allowing malware to spread across your entire system once it gains access.
To protect your operations, you need robust cybersecurity measures. Without them, malware infections or data breaches could halt production, leading to significant revenue losses. For example:
Legacy systems often lack modern security features, making them easy targets for hackers.
Malware can move laterally through flat networks, compromising multiple devices.
Operational stoppages caused by cyberattacks can result in costly downtime.
Investing in advanced security protocols, such as network segmentation and real-time threat detection, can safeguard your systems. These measures ensure your data remains secure while minimizing disruptions.
Ensuring Interoperability with Legacy Systems
Interoperability between IIoT devices and legacy systems is essential for smooth operations. However, outdated equipment often struggles to communicate with modern technologies. This challenge forces you to allocate a significant portion of your IT budget to maintaining older systems, leaving less room for innovation.
Companies spend 70% to 80% of their IT budgets on legacy system maintenance.
Organizations using outdated systems experience a 20% lower productivity rate compared to those with modern setups.
While upgrading systems requires an initial investment, the long-term benefits outweigh the costs. AI integration, for instance, reduces maintenance expenses and improves efficiency. By modernizing your infrastructure, you can enhance productivity and allocate resources toward innovation.
Scaling IIoT Systems for Future Growth
Scaling IIoT systems to meet future demands presents another challenge. Many manufacturers struggle to move beyond pilot projects, limiting the potential of their IIoT investments.
Source | Year | Key Finding |
---|---|---|
Bain & Company | 2022 | Four-fifths of companies are scaling fewer than 60% of IIoT proofs of concept. |
McKinsey | N/A | 70% of manufacturers surveyed could not scale IoT beyond pilot projects. |
To overcome this, you need a clear strategy for scaling your IIoT systems. Focus on building scalable architectures and investing in employee training. These steps will help you unlock the full potential of IIoT, ensuring your operations remain competitive in a rapidly evolving market.
Managing High Initial Costs and ROI Expectations
Adopting IIoT systems often involves significant upfront costs. These expenses include purchasing sensors, gateways, cloud platforms, and analytics tools. Additionally, integrating these technologies with existing systems may require infrastructure upgrades. While these costs can seem overwhelming, understanding the long-term benefits helps you justify the investment.
IIoT systems deliver measurable returns by improving efficiency, reducing downtime, and optimizing resource usage. For example, predictive maintenance reduces repair costs by up to 40%, while real-time monitoring minimizes production delays. These savings quickly offset the initial expenses, making IIoT a cost-effective solution in the long run.
To manage costs effectively, prioritize scalable solutions. Start with pilot projects to test the technology’s impact before expanding. This approach allows you to measure ROI and make adjustments as needed. Additionally, explore government grants or tax incentives for adopting smart manufacturing technologies.
Tip: Focus on high-impact areas like predictive maintenance or energy efficiency to maximize your ROI early in the adoption process.
By carefully planning your IIoT implementation, you can balance initial costs with long-term gains. This strategy ensures your investment drives sustainable growth and keeps your operations competitive.
Training Workforce for IIoT Integration
Your workforce plays a critical role in the success of IIoT adoption. Without proper training, employees may struggle to operate and maintain these advanced systems. Equipping your team with the right skills ensures smooth integration and maximizes the benefits of IIoT technologies.
Training programs should focus on key areas:
Real-time data monitoring to detect issues early and reduce downtime.
Predictive maintenance to extend equipment lifespan and improve reliability.
Process optimization to enhance efficiency and product quality.
Energy efficiency strategies to lower costs and support sustainability goals.
IIoT system proficiency for troubleshooting and system management.
Cybersecurity awareness to protect critical data from threats.
Data analysis skills to extract actionable insights from IIoT data.
Adaptability to keep up with evolving IIoT technologies.
Note: Studies show that well-trained employees improve system efficiency by up to 30%, highlighting the importance of workforce readiness.
Investing in training not only boosts employee confidence but also fosters a culture of innovation. As your team becomes proficient in IIoT systems, they can identify new opportunities for improvement, driving continuous growth.
Emoji Insight: 📚 Empowering your workforce with IIoT knowledge ensures your factory stays ahead in the competitive manufacturing landscape.
Future Trends in IIoT and Smart Factories
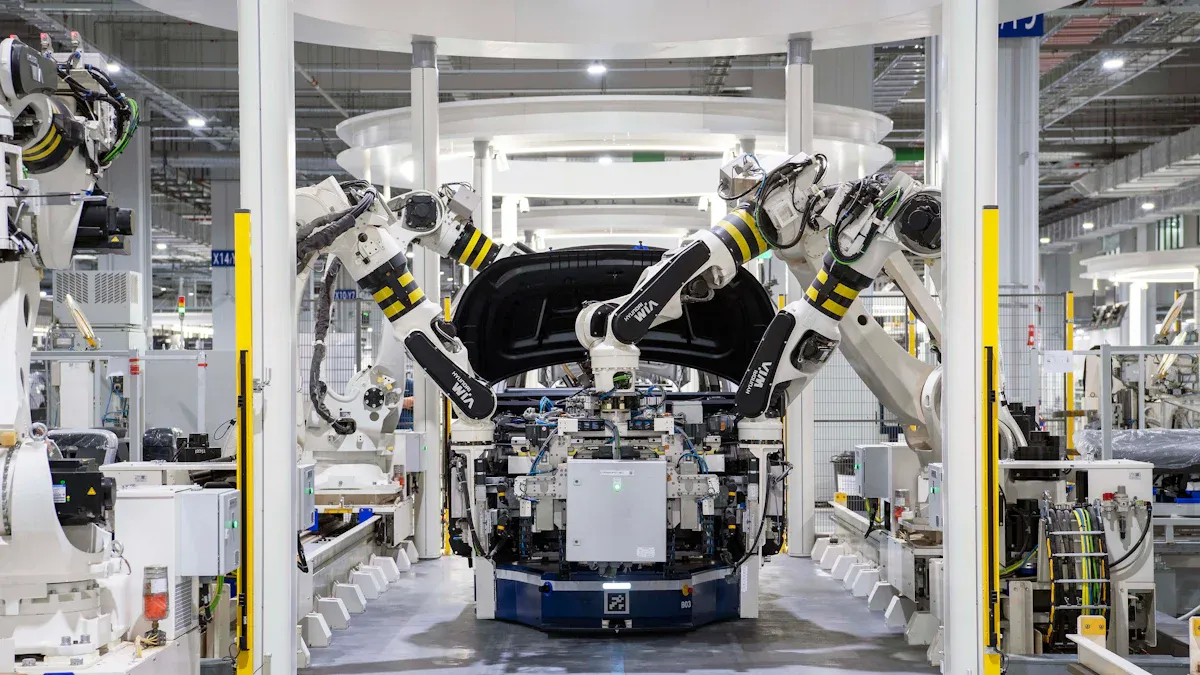
AI and Machine Learning Integration
AI and machine learning are transforming how you approach manufacturing. These technologies analyze vast amounts of data to predict trends, optimize processes, and improve decision-making. For example, AI systems in supply chains enhance inventory control by anticipating market demands. In healthcare, intelligent platforms streamline documentation, boosting accuracy and efficiency.
AI models also analyze millions of images and social media posts daily. This capability helps you predict product trends with a 93% reliability rate. By integrating AI into your operations, you can manage inventory effectively and tailor your strategies to meet market needs.
Tip: Use AI-powered analytics to uncover hidden inefficiencies and stay ahead of industry trends.
Edge Computing for Faster Data Processing
Edge computing brings data processing closer to your factory floor, reducing latency and improving decision-making speed. Unlike traditional cloud systems, edge computing processes data locally, enabling faster responses. For instance, it reduces latency by 30-50 milliseconds and detects defects 200% faster. This improvement increases production throughput by 15-25% and lowers scrap rates by up to 35% in semiconductor manufacturing.
By adopting edge computing, you can enhance operational efficiency and respond to challenges in real time. This technology ensures your factory remains agile and competitive in a fast-paced market.
Emoji Insight: ⚡ Edge computing accelerates data processing, helping you make quicker, smarter decisions.
5G Connectivity for Enhanced Communication
5G connectivity revolutionizes communication in IIoT systems. With ultra-low latency and high throughput, it supports advanced applications like semi-autonomous machinery. For example, 5G enables control of vessels with a latency of less than 20 milliseconds and a throughput of 300 Mbps. On the shop floor, it provides stable performance and excellent coverage, ensuring seamless operations.
This connectivity allows you to integrate more devices into your IIoT ecosystem, enhancing collaboration and efficiency. By leveraging 5G, you can unlock new possibilities for automation and innovation in your factory.
Note: 5G connectivity ensures your IIoT systems operate smoothly, even in complex environments.
Digital Twins for Process Simulation
Digital twins revolutionize how you simulate and optimize manufacturing processes. These virtual replicas of physical systems allow you to monitor equipment performance in real time. By using digital twins, you can detect anomalies immediately, reducing downtime and improving productivity. For example, they continuously track machine conditions, ensuring you address issues before they escalate.
Predictive analytics is another powerful feature of digital twins. It helps you foresee equipment failures and schedule maintenance proactively. This approach minimizes unplanned downtime and extends the lifespan of your machinery. Additionally, digital twins enable you to simulate different operational scenarios. This capability allows you to identify optimal parameters, leading to energy savings and better product quality.
Here are some key benefits of digital twins in manufacturing:
Continuous monitoring of equipment performance reduces downtime and boosts productivity.
Predictive analytics helps you anticipate failures and extend equipment life.
Simulation of operational scenarios improves energy efficiency and product quality.
By adopting digital twins, you can enhance your manufacturing processes and achieve higher efficiency. These tools provide valuable insights that help you make informed decisions and stay competitive in the industry.
Sustainability and Green Manufacturing Innovations
Sustainability is becoming a cornerstone of modern manufacturing. By adopting green innovations, you can reduce your environmental impact while improving efficiency. Many companies are leading the way in sustainable practices. For instance, Sierra Nevada Brewing Co. uses solar power and water recycling to minimize waste. Patagonia incorporates recycled materials into 94% of its products, showcasing its commitment to eco-friendly manufacturing. Siemens AG focuses on renewable energy solutions to reduce reliance on non-renewable sources.
Green manufacturing also emphasizes energy efficiency and resource optimization. Technologies that save energy and reduce waste play a crucial role in achieving sustainability goals. Pollution prevention is another key aspect, as it lowers emissions and effluents at the source. For example:
Energy-efficient systems reduce power consumption and operating costs.
Resource optimization ensures minimal waste while maximizing material use.
Pollution prevention strategies help you meet environmental regulations and improve air quality.
By integrating these innovations, you can align your operations with sustainability goals. This approach not only benefits the environment but also enhances your brand’s reputation as a responsible manufacturer. Sustainable practices position your business for long-term success in an increasingly eco-conscious market.
IIoT devices are reshaping manufacturing by improving efficiency, safety, and productivity. Real-time monitoring reduces costs and enhances decision-making, while automation streamlines operations. For example:
Benefit | Description |
---|---|
Improved Efficiency | Real-time visibility into the supply chain allows manufacturers to reduce costs and adapt quickly to changes. |
Enhanced Safety | IIoT-enabled quality control systems monitor production processes in real-time, reducing defects and errors. |
Increased Productivity | Automation of functions and better data integration streamline operations and enhance equipment performance. |
Smart Factories | Advanced sensors and robotics collect and analyze data for better decision-making across the enterprise. |
Proactive Repairs | Real-time asset tracking and predictive analytics help in managing repairs before failures occur. |
Better Supply Chain Management | Analytics improve the agility of manufacturing companies, allowing them to respond to customer demand swiftly. |
Despite challenges like security and scalability, IIoT offers unmatched benefits. Emerging technologies such as AI and edge computing will further enhance factory efficiency. The integration of IIoT and AI enables predictive maintenance, reducing downtime and boosting ROI.
As industries embrace these innovations, they position themselves for sustained growth and competitive advantage. By adopting IIoT, you can transform your factory into a smarter, more efficient operation.
FAQ
What is IIoT?
IIoT stands for the Industrial Internet of Things. It involves using connected devices and sensors in industrial settings to collect and analyze data. This technology helps you improve efficiency, reduce downtime, and make informed decisions in manufacturing processes.
How does IIoT improve manufacturing efficiency?
IIoT enhances efficiency by providing real-time data on equipment performance. You can monitor operations, predict maintenance needs, and optimize processes. This proactive approach reduces downtime and increases productivity, ensuring your manufacturing lines run smoothly.
What are the security concerns with IIoT?
Security concerns include potential cyberattacks on connected devices. You must implement robust cybersecurity measures to protect your data and systems. Regular updates, network segmentation, and real-time threat detection can help safeguard your IIoT infrastructure.
How can IIoT reduce costs?
IIoT reduces costs by optimizing resource usage and minimizing waste. Real-time monitoring helps you identify inefficiencies, while predictive maintenance prevents costly equipment failures. These strategies lead to significant savings in energy, materials, and labor.
What role does AI play in IIoT?
AI analyzes data collected by IIoT devices to provide actionable insights. It helps you predict equipment failures, optimize production schedules, and improve decision-making. By integrating AI, you can enhance the overall performance and efficiency of your manufacturing operations.
See Also
The Importance of PCBA Manufacturing in IoT Devices Today
Enhancing Industrial Automation Efficiency Through Effective PCBA
Essential Technologies Shaping PCBA Production for Today’s Electronics
Streamlining PCBA Manufacturing: Key Time Optimization Strategies