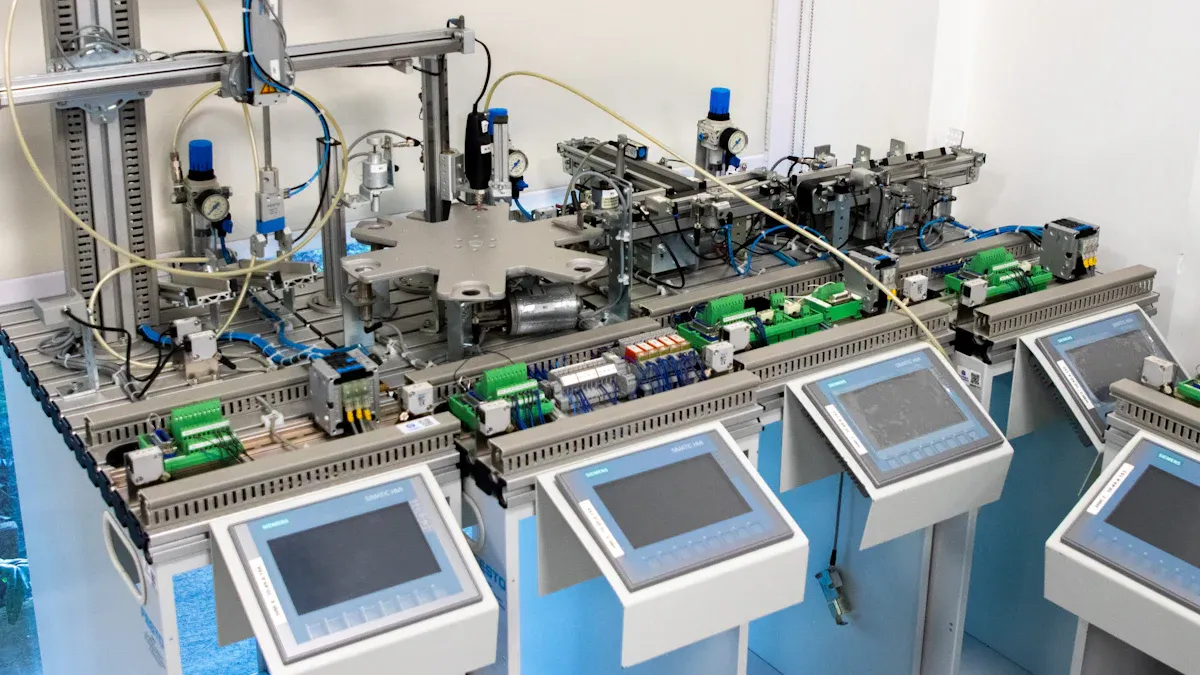
When choosing how to assemble a PCB, think about your project needs. Things like part size, strength, and price matter a lot. For example:
SMT parts are tiny, allowing smaller designs and quicker assembly.
THT is stronger, so it works well for heavy parts.
SMT lowers costs for big orders, but THT fits small ones.
SMT is common in portable gadgets and fast circuits. THT is still used for testing and tough jobs. A turnkey PCBA method makes the process easier and more accurate.
Key Takeaways
SMT works well for small and light designs. It is great for portable gadgets like phones and tablets.
THT creates strong connections, making it good for high-power uses and tough conditions.
Think about your budget and how many you need. SMT saves money for big orders, while THT fits small projects better.
Using both SMT and THT together can improve your design. You get the benefits of being small and strong.
Check the conditions your PCB will face. Pick THT for rough places and SMT for small devices.
Understanding Surface Mount Technology (SMT)
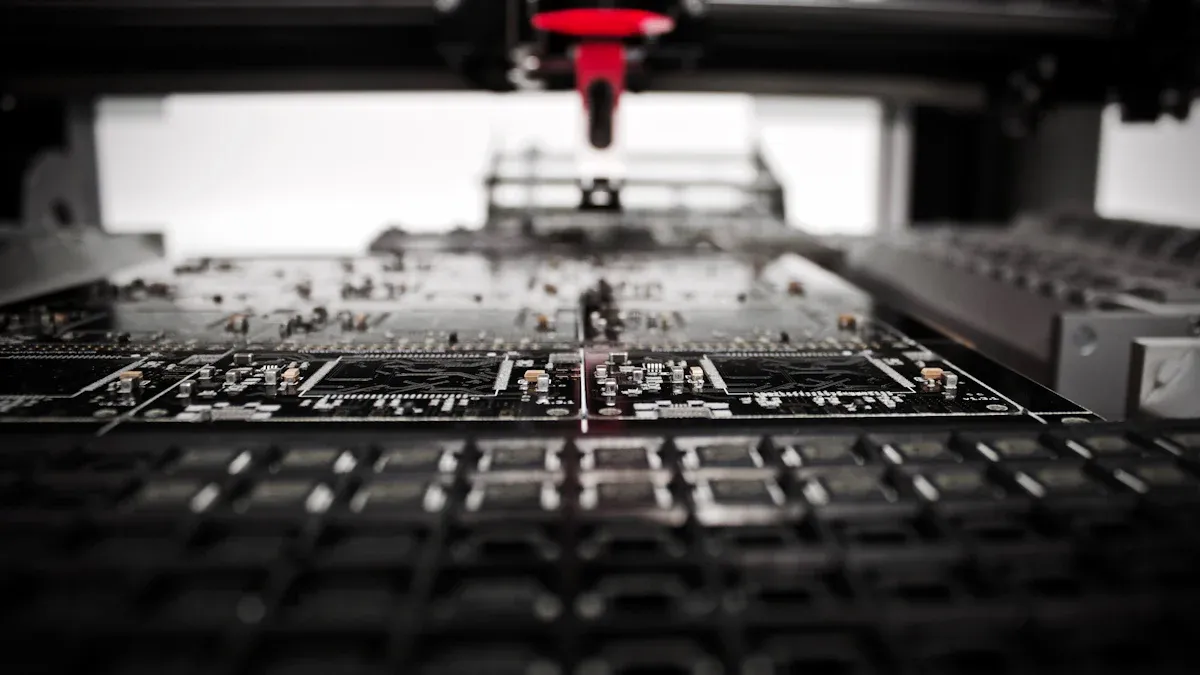
What is Surface Mount Technology?
Surface mount technology is a way to build PCBs. Components are placed directly on the board’s surface. Unlike older methods, SMT skips drilling holes. This makes designs smaller and more efficient. It allows more parts to fit on the board. This is great for modern electronics. Machines called pick-and-place help with SMT assembly. They place parts accurately and reduce mistakes. Automation makes production faster and more reliable, especially for big orders.
Benefits of SMT
Compact and lightweight design
SMT parts are much smaller than through-hole parts. This helps make circuits tiny, which is important for portable gadgets like phones and watches. Smaller parts also make products lighter. That’s why SMT is popular in consumer electronics.
High-speed assembly process
SMT uses machines to speed up production. These machines place parts quickly and precisely. This saves time during assembly. Faster production is helpful for making lots of products at once.
Cost-effectiveness for mass production
Automation in SMT lowers labor costs and reduces waste. For large orders, this saves a lot of money. Smaller parts also use less solder and coating, cutting costs further.
Benefit | Description |
---|---|
Small parts make circuits smaller and products lighter. | |
Lower Production Costs | Automation saves time and money for big orders. |
Optimized for High-Frequency Circuits | Tiny parts reduce interference and handle fast signals better. |
Reduced Requirement for Coatings | Less solder and coating are needed for smaller parts. |
Enhanced Vibration Resistance | Small, sturdy parts resist shaking and vibrations. |
Limitations of SMT
Less durable under mechanical stress
SMT has some downsides. It’s not as strong under physical stress. Parts are only attached to the surface, so they can break in shaky environments.
Unsuitable for high-power or high-voltage components
SMT isn’t good for high-power or high-voltage uses. The small size and surface connections can’t handle too much heat or electricity. This limits its use in heavy-duty machines.
Requires advanced equipment for assembly
SMT needs special tools like pick-and-place machines and ovens. These tools cost a lot, which can be hard for small projects or prototypes.
Exploring Through-Hole Technology (THT)
What is Through-Hole Technology?
Through-hole technology means putting parts through drilled holes. These parts are soldered to the other side of the PCB. This method makes strong connections, perfect for tough conditions. THT is often used in planes and power systems. The table below shows its main points:
Aspect | Description |
---|---|
Definition | |
Mechanical Durability | THT lasts three times longer than SMT under stress. |
Operational Methodology | Used in tough places like airplanes and power systems. |
Applications | Needed for hardware in hot or shaky environments. |
Benefits of THT
Strong mechanical bond for components
THT keeps parts firmly attached, even in harsh conditions. This makes it great for industries like cars and airplanes.
Ideal for high-power and high-voltage applications
THT works well in systems needing high power and safety. For example:
MRI machines use THT for strong circuits.
Boeing uses THT in flight boards for storm safety.
Satellites rely on THT for lasting performance in space.
Easier to prototype and repair
THT is simple to test and fix. You can swap parts easily without fancy tools. This makes it good for small projects and testing.
Limitations of THT
Larger and heavier components
THT parts are big and heavy, so they don’t fit small gadgets. This limits their use in modern electronics where space is tight.
Slower and more labor-intensive assembly process
Drilling holes takes time and slows production. Hand soldering also makes THT slower for making lots of products.
Higher cost for mass production
THT costs more because it needs extra materials and work. The table below compares THT problems with SMT benefits:
Aspect | THT Limitations | SMT Advantages |
---|---|---|
Component Size | Big parts take up more space | Small parts fit more in less space |
Assembly Speed | Slower due to drilling and manual work | Faster with machines |
Even with these issues, THT is still trusted for important jobs. Using a turnkey PCBA method can make the process faster and more accurate.
SMT vs. THT: A Comparative Analysis
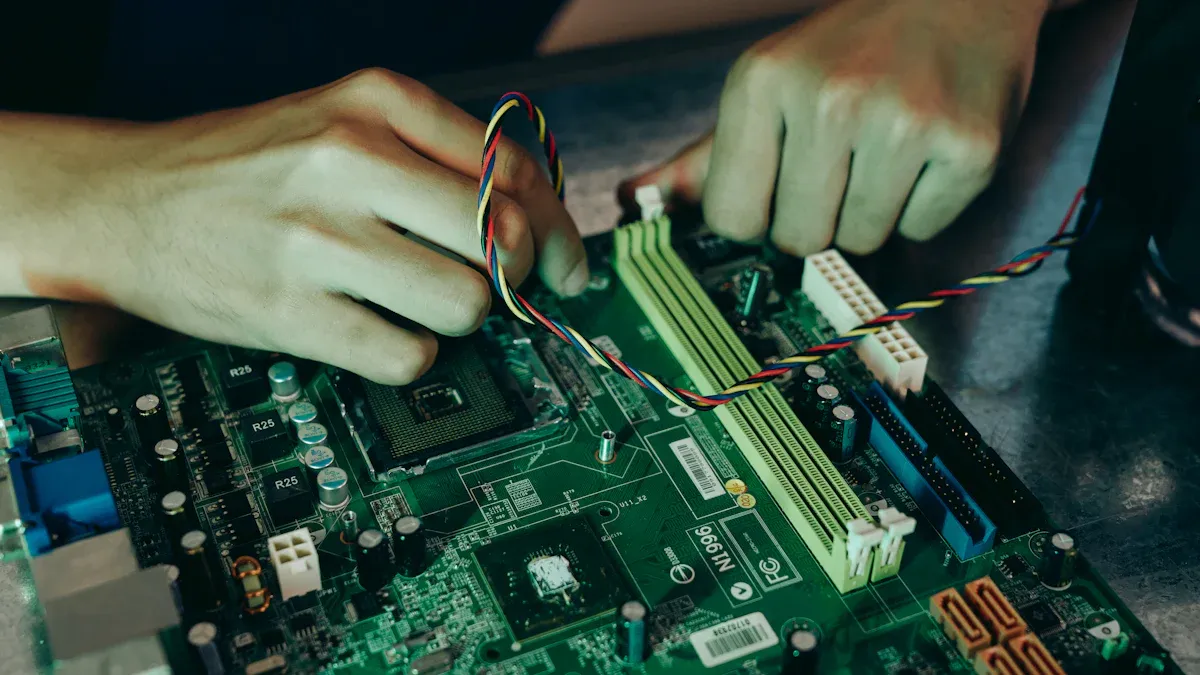
Key Differences Between SMT and THT
Assembly process and equipment
SMT uses machines like pick-and-place systems for assembly. These machines work fast and reduce mistakes. THT, however, needs people to drill holes and solder parts. This makes THT slower and harder to do. SMT requires expensive tools, but THT can use simpler, cheaper equipment. This makes THT better for small projects.
Component size and weight
SMT parts are tiny and light, perfect for small gadgets. THT parts are bigger and heavier, so they take up more space. This makes THT less useful for devices where size and weight matter.
Durability and mechanical strength
THT is stronger because its parts go through the board. These parts can handle shaking and stress better. SMT parts only stick to the surface, so they break more easily. For tough jobs, THT is the better choice.
Aspect | SMT | THT |
---|---|---|
Compact Design | ✔️ | ❌ |
Lower Production Costs | ✔️ | ❌ |
Optimized for High-Frequency Circuits | ✔️ | ❌ |
Superior Mechanical Durability | ❌ | ✔️ |
Ease of Prototyping | ❌ | ✔️ |
Higher Material Consumption | ❌ | ✔️ |
Reduced Component Density | ❌ | ✔️ |
When to Choose SMT
Consumer electronics and compact devices
SMT is best for gadgets like phones, tablets, and smartwatches. It helps make small, lightweight designs. SMT also allows more parts to fit on a board. This is important for modern electronics.
High-volume production with cost constraints
For making lots of products, SMT saves money and time. Machines do most of the work, cutting labor costs. This makes SMT great for industries needing fast, large-scale production.
When to Choose THT
Industrial and military applications
THT is needed for tough jobs in factories and the military. Companies like Boeing use THT for airplane controls because it’s reliable. Lockheed Martin uses THT in satellites to handle space radiation and stress.
Company | Application | Evidence |
---|---|---|
Boeing | Flight control boards | THT components ensure reliability in high-stress environments, preventing failures during critical operations. |
Lockheed Martin | Satellite boards | THT uses custom solder alloys to endure space radiation, showcasing adaptability and longevity. |
Prototyping and repairable designs
THT is great for testing and fixing designs. Its parts are easy to remove and replace. This makes THT useful for small projects and experiments.
Practical Advice for Choosing the Right PCB Assembly Method
Factors to Consider
Project budget and production volume
Your budget and how many units you need matter. SMT is great for making lots of products quickly. Machines do most of the work, saving time and money. For example, SMT can cost four times less than THT for big orders. But for small projects or prototypes, THT is cheaper. It uses simple tools and manual assembly. Plan your costs carefully to pick the best method for your budget.
Environmental and mechanical stress requirements
Think about where your PCB will be used. If it faces shaking or stress, THT is stronger. It works well in tough places like factories or airplanes. But for small, light devices, SMT is better. Its parts are tiny and handle vibrations well. This makes SMT perfect for portable gadgets like phones.
Component type and availability
The parts you need also affect your choice. SMT is good for small, fast circuits. THT works better for big, powerful parts like transformers. The table below shows which method fits different uses:
Application | SMT | THT |
---|---|---|
Portable devices (smartphones, IoT) | ✔️ | ❌ |
Industrial equipment (PLC controllers) | ✔️ | ✔️ |
High-frequency circuits (RF) | ✔️ | ❌ |
Power connectors/high-current connectors | ❌ | ✔️ |
Mass production (>1000 units/series) | ✔️ | ❌ |
Prototyping/small series (<10 units) | ❌ | ✔️ |
Systems requiring miniaturization | ✔️ | ❌ |
High-power components (transformers) | ❌ | ✔️ |
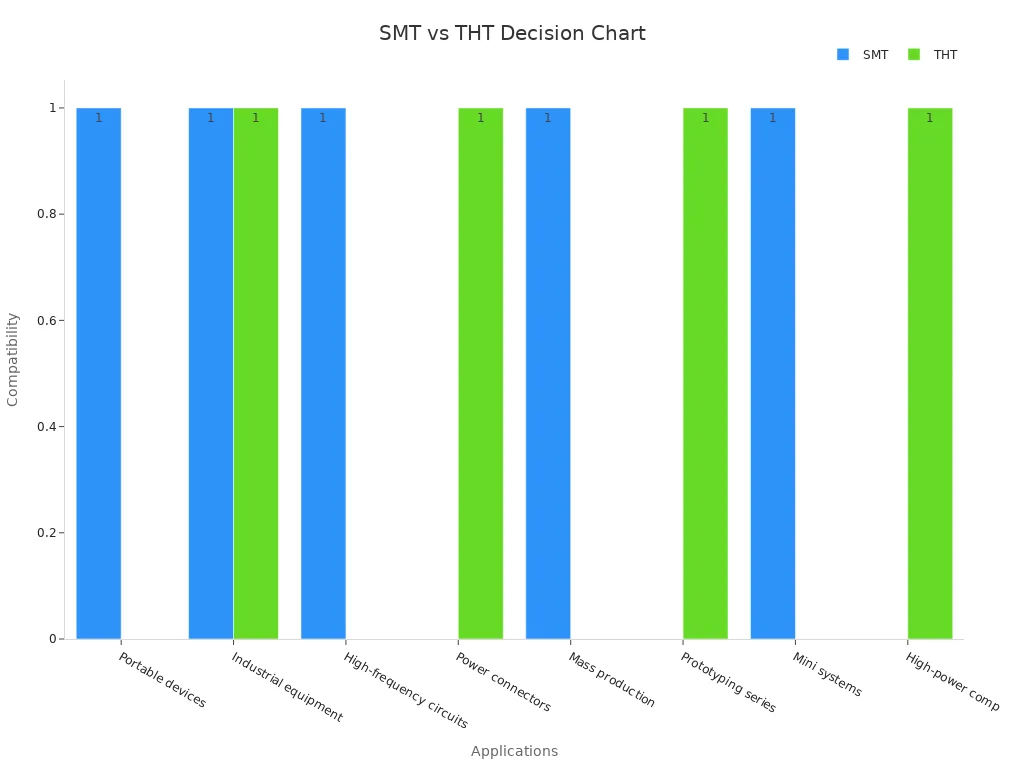
The Hybrid Approach: Combining SMT and THT
Benefits of a hybrid PCB design
Using both SMT and THT together can be smart. This mix lets you use SMT for small, fast parts and THT for strong, heavy ones. It gives you more design options and meets different needs. A hybrid design can also save money. You get the speed of SMT and the strength of THT for important parts.
Examples of mixed technology PCB assembly
Many industries use hybrid designs for balance. For example:
Automotive electronics: SMT handles sensors, while THT secures connectors.
Medical devices: SMT makes small circuits, and THT powers strong parts.
Consumer electronics: SMT keeps gadgets light, and THT strengthens ports.
By combining both methods, you get the best of both worlds. Turnkey PCBA services often support hybrid designs, making the process easier and faster.
SMT and THT each have their own strengths and weaknesses. SMT is great for small designs and making lots of products cheaply. THT is better for strong connections and easy repairs. The table below shows how they differ:
Aspect | SMT | THT |
---|---|---|
Compact Design | ✔️ | ❌ |
Lower Production Costs for High Volumes | ✔️ | ❌ |
Superior Mechanical Durability | ❌ | ✔️ |
Ease of Prototyping | ❌ | ✔️ |
Higher Material Consumption | ❌ | ✔️ |
Reduced Component Density | ❌ | ✔️ |
Pick the method that fits your project’s needs for size, strength, and cost. If you need both small size and durability, using both SMT and THT together can work well.
FAQ
What is the main difference between SMT and THT?
SMT puts parts on the PCB surface. THT places parts through drilled holes. SMT works well for small designs and fast production. THT is stronger, so it’s better for tough conditions.
Can I use both SMT and THT in one PCB design?
Yes, you can mix SMT and THT. SMT is good for small, light parts. THT is great for strong, high-power parts. Using both gives more options and better performance.
Which method is better for prototyping?
THT is best for testing designs. Its parts are simple to move and replace. This makes it good for small projects or designs that change often.
Is SMT always cheaper than THT?
No, not always. SMT saves money for big orders because of machines. But THT costs less for small projects since it uses simple tools and manual work.
How do I decide which method to use?
Think about your project needs. SMT is great for small gadgets and big orders. THT works for strong parts, testing, or high-power uses. Mixing both methods can help if you need strength and small size.
Tip: Check your budget, stress levels, and parts before choosing.