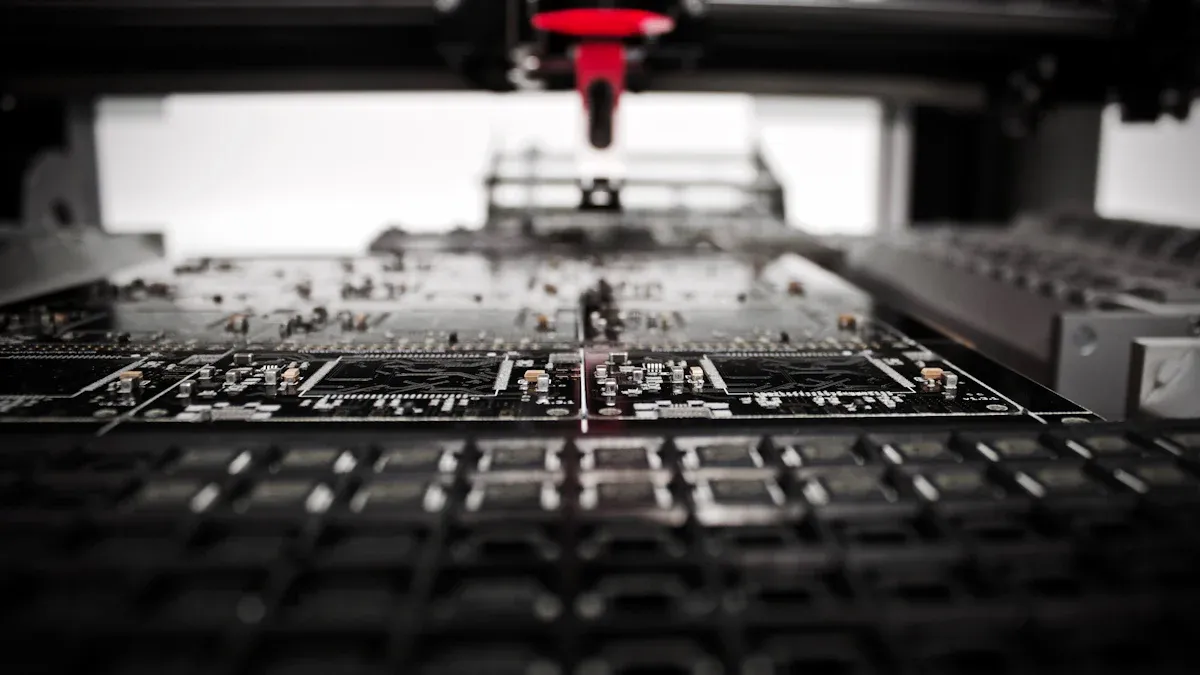
In 2025, a PCB factory with integrated PCBA capabilities will play a crucial role in the electronics industry. These facilities enable businesses to produce products more efficiently and cost-effectively by manufacturing circuit boards and assembling components on them. The increasing demand for electronics makes such capabilities even more essential.
The integrated circuits market is projected to grow from $401.81 billion in 2024 to $446.8 billion in 2025, reflecting an 11.2% annual growth rate.
The global semiconductor market is expected to reach $687 billion in 2025, with a growth rate of 12.5%.
This rapid growth highlights the importance of a PCB factory with integrated PCBA capabilities in providing innovative and affordable solutions for industries like electronics and telecommunications.
Key Takeaways
Factories that combine PCB and PCBA save time and money.
Pick factories with ISO and IPC certifications for safe, quality products.
Choose factories offering flexible options like prototypes and large orders.
Check reviews and examples to see if a factory is reliable.
Pick a factory that can grow with your business needs.
Understanding PCB and PCBA Capabilities
What is PCB Manufacturing?
Printed circuit board (PCB) manufacturing makes the base for electronic circuits. A PCB holds and connects parts like resistors, capacitors, and microchips. The process has many steps to ensure the board works well and lasts long.
Step | What Happens |
---|---|
Material Selection | Picking materials like copper and substrates based on cost and flexibility. |
Pattern Creation | Making circuit designs using light-sensitive film and UV light. |
Copper Removal | Taking away extra copper with chemicals or lasers. |
Hole Drilling | Making holes for parts using lasers or drills. |
Metal Coating | Adding metal to holes and surfaces using plating methods. |
Protective Layer | Applying a coating to stop solder from connecting wrong areas. |
The PCB market is growing fast. It will rise from $65.82 billion in 2024 to $68.75 billion in 2025. This growth comes from more demand in areas like electric cars and healthcare.
What is PCBA and Why is Integration Important?
Printed circuit board assembly (PCBA) means putting electronic parts onto a PCB to make it work. This step turns a plain PCB into a useful device. Having PCB and PCBA in one place gives big advantages.
For example, smart systems using AI make production faster and better. These systems help manage supplies, cut waste, and improve efficiency. Combining PCB and PCBA steps saves time and ensures better quality. This makes factories with both PCB and PCBA abilities very helpful for projects.
Benefits of Integrated PCB and PCBA Solutions
Combining PCB and PCBA processes offers many benefits:
Benefit | What It Means |
---|---|
Saving Money | Finding problems early avoids costly fixes and bad products. |
Affordable Quality Checks | AOI is cheaper than other methods like X-ray checks for common issues. |
Quick Problem Fixes | Inline AOI catches mistakes fast, stopping bigger problems. |
The PCB and PCBA recycling market will grow from $7.36 billion in 2024 to $21.42 billion by 2033. This shows how important eco-friendly practices are becoming. Choosing combined solutions lowers costs and helps the planet.
Criteria for Evaluating Top PCB Factories
Certifications and Compliance Standards (e.g., ISO, IPC, RoHS)
Certifications show a factory meets important rules and standards. These rules ensure quality, safety, and eco-friendly practices. For example, IPC standards like IPC-A-600 and IPC-6012 check how good circuit boards look and work. They focus on things like surface flaws, plating thickness, and electrical features.
Standard | What It Covers |
---|---|
IPC-A-600 | Rules for checking PCB looks and deciding what’s acceptable. |
IPC-6012 | Guidelines for rigid PCBs, including plating and electrical tests. |
IPC-2221 | General design rules for PCBs, covering materials and layout. |
ISO 9001 | Global standard for quality systems, requiring regular checks. |
RoHS Compliance | Limits harmful materials in electronics to protect the environment. |
Factories with these certifications make reliable and eco-friendly products. This improves product life and reduces breakdowns.
Range of Services Offered (e.g., prototyping, mass production, testing)
Good factories provide many services for different project needs. These include prototyping, mass production, and testing. Prototyping helps test designs before making many products. Mass production makes sure items are ready for the market quickly. Testing ensures products work properly and last long.
Service Type | What It Does |
---|---|
Mass Production | Handles all steps to make products ready for sale. |
Prototyping | Helps turn ideas into real designs for production. |
Testing | Uses methods like RF and X-Ray to check product quality. |
Testing tools like AOI and X-Ray find problems early. Factories offering full services, like prototyping and inspections, make production easier.
Cost-Effectiveness and Pricing Models
Saving money is important when picking a factory. New printing tools and automation can cut costs by 30%. Faster production improves quality and reduces waiting times. Many factories now offer flexible pricing, like discounts or custom rates for small orders.
Year | Market Value (in billions) | Growth (%) |
---|---|---|
2023 | 67.9 | N/A |
2024 | 70.9 | 5.4 |
2029 | 92.4 | N/A |
Choosing a factory with smart pricing helps save money. It also keeps your project high-quality and competitive.
Lead Time and Delivery Reliability
When picking a PCB factory with PCBA abilities, timing matters. You need a factory that meets deadlines and keeps quality high. New production methods have made big improvements.
Lead times are now 4-5 weeks, 30-35% faster.
On-time deliveries improved from 85% to an amazing 97%.
Customer satisfaction grew by 25%, showing better service.
Production costs dropped by 15%, saving more money.
These changes help keep your projects on track. Fewer delays mean you can meet market needs. Reliable delivery builds trust and strengthens your factory partnership.
Scalability and Production Volume Capabilities
Scalability is key when choosing a PCBA factory. Whether you need a few items or many, the factory should handle it well. Modern factories use smart machines and flexible systems to do this.
High-volume lines make thousands to millions of items weekly. Some factories can make 100,000 PCBs in one week.
Automated tools speed up production and lower costs.
Factories can switch between small and big orders without losing quality.
This flexibility helps both new and big companies. Startups can order small amounts affordably. Big businesses can rely on large-scale production for market needs. Advanced tools also allow quick changes to meet your demands.
Customer Support and After-Sales Services
Good customer support and after-sales help are very important. A great factory listens to your needs and helps you succeed.
Factories with good support answer questions and fix problems fast.
Skilled staff guide you during design and assembly steps.
After-sales help includes testing and using PCBs to ensure they work well.
A TechInsights survey showed how important these services are. Over 1,800 people rated suppliers on service and performance. Reviews and feedback from others can help you find factories with excellent support.
Comparison of Top PCB Factories with Integrated PCBA Capabilities in 2025
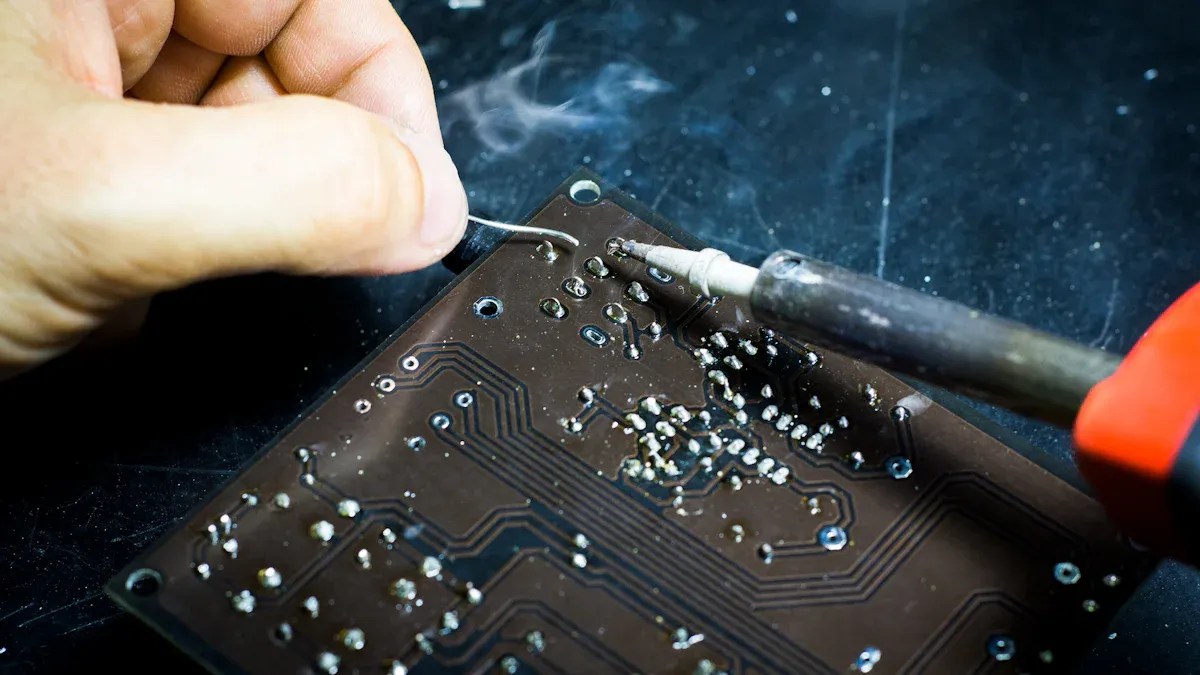
FS Tech – A Top Choice for PCB and PCBA Services
FS Tech is a leader in making and assembling circuit boards. They work on both small and big projects with advanced tools. Their combined PCB and PCBA services make production faster and better.
FS Tech uses tools like AOI and X-ray to find mistakes early. These tools help save materials and improve production speed. They offer services like prototyping, testing, and mass production. This makes FS Tech a great choice for electronics manufacturing.
Customer satisfaction is very important to FS Tech. They provide help during and after production to ensure high-quality products. If you need a dependable factory for PCB and PCBA, FS Tech is an excellent option.
Sierra Circuits – Reliable PCB and PCBA Solutions
Sierra Circuits is known for making high-quality circuit boards and assemblies. They are trusted for their accuracy and dependable products. Sierra Circuits follows strict industry rules to ensure top-notch results.
They handle every step of production, from design to testing. Their tools include laser drills and automated soldering machines. These tools make products strong and efficient.
Sierra Circuits also cares about the environment. They follow RoHS rules to reduce harmful materials. This makes them a good choice for eco-friendly companies. If you want reliable electronic manufacturing, Sierra Circuits is a complete solution.
Sanmina Corporation – Expert in Large-Scale Manufacturing
Sanmina Corporation is one of the best electronic manufacturers worldwide. They offer many services, including PCB and PCBA for industries like healthcare and cars.
Sanmina uses advanced machines to handle large orders quickly. Their focus on quality ensures products meet market needs.
Metric | Value |
---|---|
Revenue Growth (last quarter) | 8.1% |
Gross Margin (5 years average) | 8.2% |
Operating Margin (5 years average) | 4.6% |
EPS Growth (5 years CAGR) | 14.8% |
Sanmina’s steady growth shows their dedication to quality.
Sanmina also offers great customer support. Their team helps with tough projects and ensures smooth production. If you need a trusted partner for PCB assembly, Sanmina is a smart choice.
AT&S – Leading in PCB and PCBA Innovation
AT&S is a leader in PCB and PCBA technology. They focus on new ideas and eco-friendly methods in their work. AT&S makes advanced products like HDI PCBs and embedded component packaging. These improve how well electronic devices work and last.
Their factories use modern machines to make top-quality PCBs and assemblies. Automated tools help them work precisely, lowering mistakes and boosting speed. AT&S spends a lot on research to stay ahead in the fast-changing electronics world.
They care about the environment by using green methods. AT&S reduces waste and uses materials that can be recycled. This makes them a great choice for businesses that value sustainability.
AT&S works with industries like cars, healthcare, and telecom. Their products are used in things like electric cars and medical tools. If you need smart and dependable PCBA solutions, AT&S has the skills and tools to help.
Tip: Pick a factory that values innovation and the environment. AT&S excels in both, offering great products and green practices.
TTM Technologies – Reliable and Flexible PCB Maker
TTM Technologies is known for making reliable and flexible PCBs. They offer many products for different uses. These include HDI, flexible, and RF boards for industries like cars, aerospace, and healthcare.
Buying Viasystems made TTM better at making multilayer and flexible PCBs. This helped them become a top company in high-performance PCB production. They can handle both small and large orders quickly and well.
Feature | Details |
---|---|
Product Variety | Makes HDI, flexible, and RF boards for many uses. |
Industry Focus | Works with industries like cars, aerospace, and healthcare. |
Acquisition Benefits | Gained advanced multilayer and flexible PCB skills from Viasystems. |
Market Strength | Known as a leader in high-quality PCB manufacturing. |
TTM is reliable, delivering on time and meeting high standards. Their advanced tools make production faster and products stronger. Customers trust TTM for their PCBA needs.
They also focus on new technology. Their factories use advanced machines to make complex PCBs and assemblies. These are used in demanding fields like aerospace and healthcare.
If you want a factory that is flexible, reliable, and advanced, TTM is a great pick. They ensure your project meets industry rules and performs well.
Note: TTM’s ability to handle both small and big orders makes them perfect for startups and large companies. Their systems adjust to your needs, saving money and time.
Key Things to Think About When Picking a Factory
Matching Factory Skills to Your Project
To pick the right factory, know your project needs. Factories have different skills, so check if they match yours. For example, if you need complex designs like multilayer boards, the factory must handle advanced methods. If eco-friendly options matter, choose one that follows RoHS rules.
Factories with flexible systems can make both small and big orders. This is helpful for new and big companies. A Cleveland company improved by working with a factory that fit its needs. The factory hired more workers and managed them well, raising staff levels to 91%. This cut down on people leaving and kept workers longer.
Project Style | Best Fit Factors |
---|---|
Agile | Complex projects, customer involvement |
Waterfall | Big projects, low risk |
Lean | Saving resources, less waste |
Balancing Cost, Time, and Quality
Keeping costs, time, and quality balanced is key. PCB costs can go up if materials are wasted or mistakes happen. To avoid this, pick a factory with good testing systems. These systems catch problems early, saving money and materials.
Meeting deadlines is also important. Factories that plan well and work with suppliers avoid delays. Some factories now deliver PCBs 30% faster, helping you stay on schedule.
Quality is just as important. Design for Testability (DFT) makes testing easier and lowers mistakes. Factories using DFT make better boards that meet industry rules.
Why Certifications Matter for Certain Industries
Certifications are important for quality and safety. Industries like healthcare and aerospace need strict standards. Look for factories with certifications like ISO 9001, AS9100, or IPC-6012. These show the factory follows global rules.
Factor | What to Check |
---|---|
Quality | Factories with good reviews and proven success. |
Pricing | Costs that fit your budget. |
Delivery Time | Can they meet your deadlines? |
Customer Help | Are they quick to answer and solve issues? |
Technical Skills | Can they handle your design needs like layers and materials? |
Certifications | Do they have ISO or other needed approvals? |
Production Size | Can they make the amount you need? |
Location | Is the factory close enough for fast shipping? |
Certifications build trust and ensure good results. Factories with these approvals are more likely to give you reliable PCBA solutions.
Checking Customer Reviews and Case Studies
Customer reviews and case studies help you learn about a factory. They show how well a factory works and solves problems. These tools guide you in picking the right factory for your PCBA needs.
Why Reviews Are Important
Reviews share what other customers experienced. They tell if a factory keeps promises like good quality, fast delivery, and helpful support. Positive reviews mean the factory does well. Negative ones show areas to watch out for. Look for reviews that talk about testing, delivery, or other PCBA services.
Tip: Read reviews from people with projects like yours. Their feedback will be more useful.
What Case Studies Show
Case studies give real examples of a factory’s work. They explain how the factory solved problems or handled special requests. For example, a case study might show how a factory made many PCBAs quickly or used green methods for a project. These stories prove the factory’s skills and flexibility.
How to Use Reviews and Case Studies
Follow steps to compare reviews and case studies. Make a list of things to check, like quality and cost. Look for common points in reviews, such as happy customers or good support. In case studies, find results like faster delivery or better product quality.
Factor | What to Check |
---|---|
Quality | Positive comments about how products work. |
Delivery Reliability | Notes on fast and on-time deliveries. |
Customer Support | Proof of quick and helpful responses. |
Innovation | Examples of smart ideas or advanced PCBA tools. |
By studying reviews and case studies, you can see a factory’s good and bad sides. This helps you pick a factory that fits your project needs.
PCB factories with combined PCBA abilities offer great benefits. They make and assemble circuit boards in one place. This setup speeds up production and delivery times. It also improves quality, lowers costs, and makes products more reliable. Factories like FS Tech, Sierra Circuits, and AT&S are known for flexible and smart PCBA solutions for many industries.
When picking a factory, check if their PCBA services fit your needs. Think about things like price, delivery time, and how much they can produce. Choosing a factory that meets your needs helps make better products faster. The right factory partner can help you succeed in a tough market.
FAQ
What is the difference between PCB and PCBA?
A PCB is an empty board for electronic parts. PCBA is when parts are added to the PCB, making it work. Think of PCB as the base and PCBA as the finished product.
Why are integrated PCB and PCBA factories better?
These factories do both PCB making and assembly together. This saves time, improves quality, and cuts costs. You get faster results and fewer mistakes than using separate places.
How do certifications like ISO or IPC help you?
Certifications show the factory follows strict rules for quality and safety. For example, ISO 9001 ensures good quality, and IPC standards check PCB reliability. Certified factories give you trusted and safe products.
Can small businesses benefit from scalable factories?
Yes, scalable factories can handle small and big orders. They offer flexible options, which are great for startups. You can start small and grow production as your business grows.
How do I pick the right PCB factory for my project?
Think about what your project needs. Check the factory’s certifications, services, and reviews. Make sure they fit your budget, quality, and delivery needs. Look for examples of similar projects to see their skills.
See Also
Emerging Trends in Smart Manufacturing for PCBA by 2025
Navigating ITAR Regulations for PCBA Production in 2025
Essential Technologies Shaping PCBA Production for Today’s Electronics
Comparing Leading PCBA Providers in the Industry 4.0 Era
Choosing the Ideal PCBA Manufacturer to Suit Your Requirements