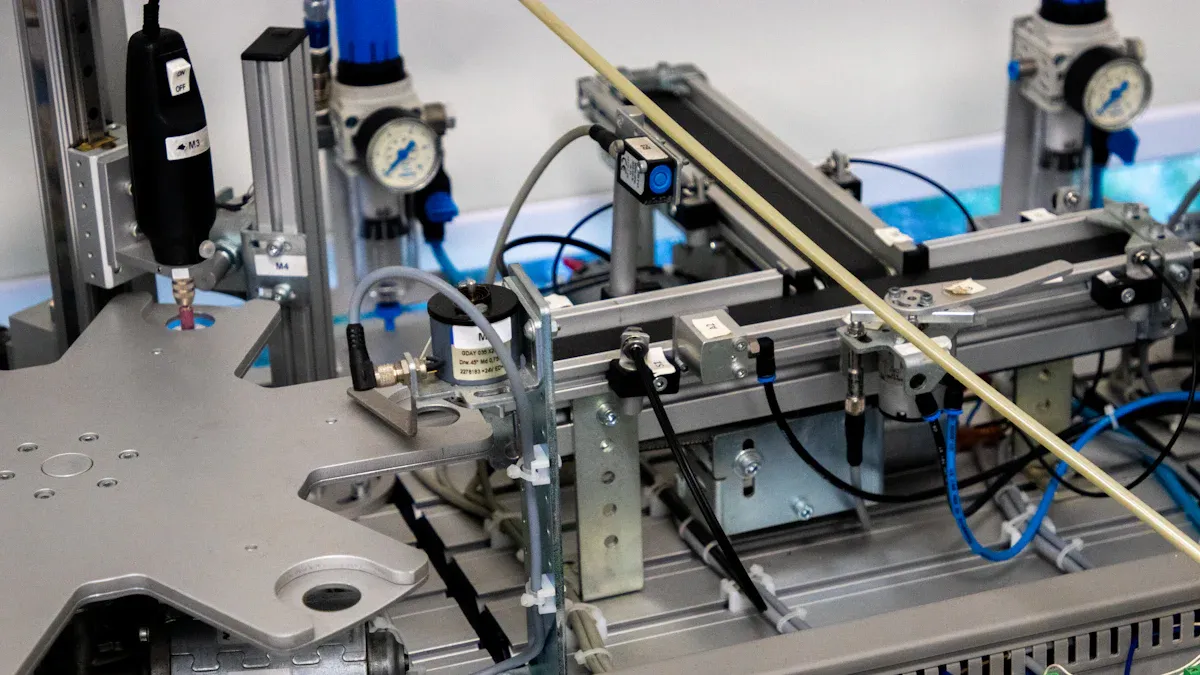
When making PCBAs, quality is very important, especially for a USA-based PCBA manufacturer. Good products are needed to satisfy customers, and this starts with strong quality checks. PCBA makers in the USA focus on controlling every step to avoid mistakes.
Why is this important? Tools like Shewhart Control Charts show that 99.73% of data stays within +/- 3-sigma limits. This proves how important accuracy is. These tools help keep the process smooth and trustworthy. From choosing materials to final checks, each step helps a USA-based PCBA manufacturer create great products.
Key Takeaways
Quality control is very important in making PCBAs. It makes sure products work well and satisfy customers.
Good raw materials stop problems like short circuits or system breakdowns. Always pick reliable suppliers.
Smart testing tools like AOI and X-ray find mistakes early. This saves both time and money during production.
Following IPC rules helps gain customer trust and keeps PCBAs high-quality.
Testing and customer feedback help improve processes and make better products over time.
Raw Material Selection and Inspection by USA-Based PCBA Manufacturers
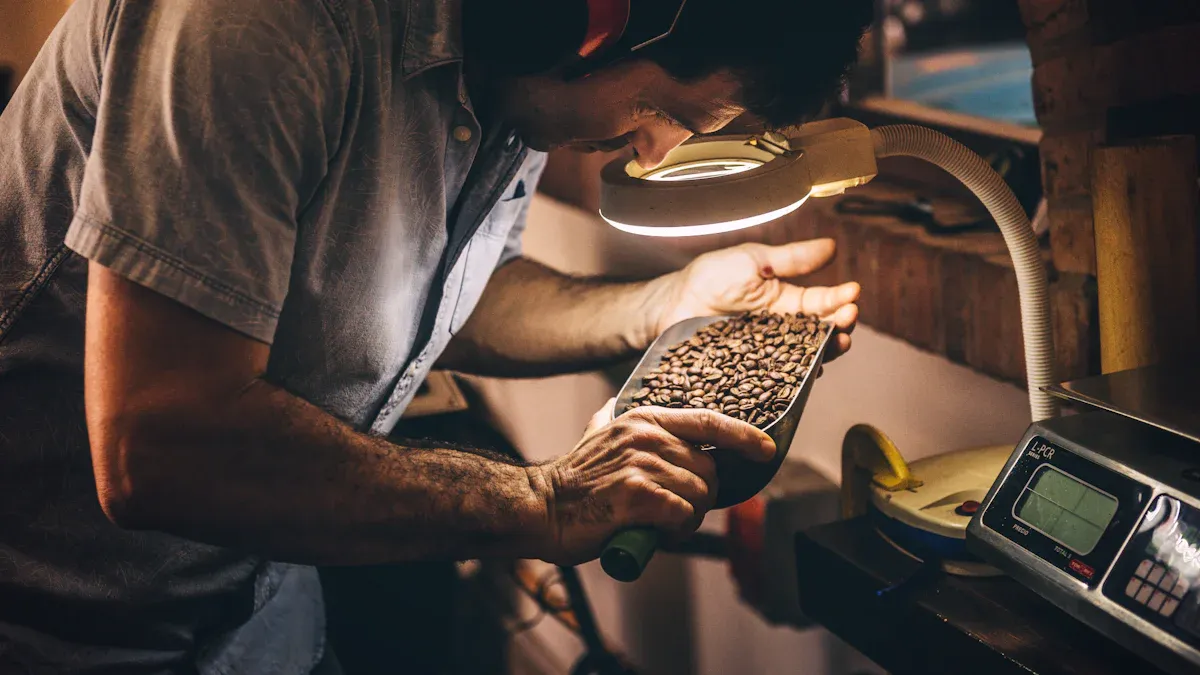
Why high-quality raw materials matter
In PCBA production, good materials are the starting point. They help make products that work well and last long. USA-based PCBA makers choose parts from trusted suppliers to keep quality steady. This reduces problems and makes the PCB stronger.
Why is this important? Bad materials can cause short circuits or system failures. Using top-quality parts means going beyond basic standards. This focus on quality helps USA-based PCBA makers succeed in a tough market.
Checking and testing materials before use
Before making PCBAs, all parts are carefully checked. Only the best materials are used for assembly. Special tools find defects, check sizes, and confirm details. Early checks save time and money later.
Here’s how USA-based PCBA makers do it:
They set clear rules for checking quality in every batch.
Advanced tools, like X-rays, find hidden problems.
Workers get regular training to improve these checks.
This careful process lowers costs, speeds up delivery, and keeps quality high. Few bad parts make it into production, showing how well these checks work.
Making sure parts are real and reliable
Using real and reliable parts is key in PCBA making. Fake or bad parts can harm how products work and their safety. USA-based PCBA makers take extra care to check every part’s source and quality.
Here’s how they do it:
Aspect | Description |
---|---|
Real Parts | Makes sure parts meet standards, lowering the chance of failures. |
Tracking | Follows parts from supplier to product, keeping the supply chain honest. |
Quality Checks | Finds and fixes problems to make better products. |
Trusted Suppliers | Works with good suppliers to get real and reliable parts. |
Advanced Testing | Uses tools like X-rays to spot fake parts. |
Tracking parts is very important. It meets rules and makes products safer and better. By using trusted suppliers and smart testing, USA-based PCBA makers keep their products top-notch.
Common problems with bad materials and their effects on PCBAs
Using bad materials in PCBA making can cause many problems. These issues don’t just lower product quality—they also waste time, money, and hurt trust. Let’s look at common problems caused by poor materials and how they affect PCB assemblies.
1. Poor Performance and Reliability
Bad materials often don’t meet needed standards. This can cause weak electrical performance, loose connections, or even total failure. For example, a cheap capacitor might break under high voltage. This isn’t just annoying—it’s a big problem for customers.
2. More Failures
Low-quality parts fail more under stress. Heat, shaking, or long use can break them. For instance, a weak solder joint might crack, causing bad connections. These failures are hard to find and fix, creating more trouble.
3. Design Problems
Bad materials might not fit your design. They could be the wrong size, have mismatched tolerances, or act differently. This can cause assembly mistakes or expensive fixes. Sometimes, it means throwing away a whole batch of PCBs.
4. Safety Risks
Fake or low-grade parts can be dangerous. For example, a fake resistor might overheat and catch fire. This can harm users and damage your company’s name. Checking every part is key to staying safe.
Tip: Always buy from trusted suppliers and test materials carefully. Spending more on quality now saves money later.
5. Higher Costs
Cheap materials may seem like a good deal but cost more later. Broken parts can delay work, increase waste, and need extra testing or repairs. These hidden costs make bad materials a bad choice for serious makers.
6. Environmental Harm
Bad materials don’t last long, creating more electronic trash. This hurts the planet and goes against eco-friendly practices. Choosing good materials helps the environment and makes longer-lasting products.
In summary, bad materials cause many problems, like poor performance, higher costs, and safety risks. By focusing on quality, you can avoid these issues and make reliable, high-quality PCB assemblies.
Process Control in PCBA Manufacturing
Watching soldering steps for accuracy and dependability
Soldering in PCBA making needs to be precise. Every connection must be strong and dependable. To do this, manufacturers track key numbers:
Metric | Description |
---|---|
Defects per Million Opportunities (DPMO) | Counts defects per million chances, showing quality levels. |
First Pass Yield (FPY) | Shows the percentage of PCBs passing checks on the first try. |
Rework Rate | Tracks how many PCBs need fixing after assembly. |
Scrap Rate | Measures the percentage of unusable PCBs due to mistakes. |
These numbers show how well soldering is going. Watching them helps catch problems early. Fixing issues quickly makes PCBs stronger and longer-lasting.
Making sure parts are placed correctly
Putting parts in the right spot is very important. A misplaced part can ruin a PCB. Manufacturers use smart tools to check for accuracy:
Testing Method | Description |
---|---|
Automated Optical Inspection | Uses cameras to find missing or wrong parts by comparing images. |
In-Circuit Testing | Uses a special tool to test PCB functions by touching test points. |
Functional Validation Testing | Loads software onto the board to check if it works as planned. |
These tools help find mistakes before they grow into big problems. Using them ensures every part is in the right place.
Checking quality during production
Real-time checks act like a safety guard during production. They catch mistakes as they happen, so fixes are quick. Here’s what gets checked:
Component Verification: Makes sure parts are present, correct, and in good shape.
Assembly Sequence Validation: Confirms parts are installed in the right order.
Precision Alignment Monitoring: Checks if parts are aligned properly.
Connection Verification: Tests electrical and mechanical connections for strength.
Real-Time Process Control: Stops production immediately if defects are found.
Documentation and Traceability: Keeps records of parts, assembly steps, and quality checks.
By monitoring these areas, manufacturers keep quality high and reduce errors. This careful process ensures PCBs meet top standards.
Advanced testing methods: AOI, X-ray, and ICT
Testing is key to making sure PCBs are high quality. Advanced methods like Automated Optical Inspection (AOI), X-ray inspection, and In-Circuit Testing (ICT) help ensure every board is top-notch. Here’s how these methods work and why they matter.
Automated Optical Inspection (AOI)
AOI uses cameras to check PCBs for problems. It compares the board to a design to find missing parts, solder mistakes, or misaligned pieces. This method is quick and accurate, catching surface issues early.
Why it matters: AOI saves time and money by fixing errors early. It ensures boards are made correctly from the start.
X-ray Inspection
X-ray inspection looks inside the PCB for hidden problems. It finds issues like gaps in solder or misaligned layers. This is great for complex boards with tiny or layered parts.
Pro Tip: Use X-ray inspection for dense boards where other methods might miss problems.
In-Circuit Testing (ICT)
ICT checks if the PCB works properly. It uses probes to test parts and connections, making sure everything functions as it should. This method is very reliable for checking performance.
Key takeaway: ICT not only finds problems but also proves the board works in real-life conditions.
By using these advanced tests, manufacturers can make reliable, high-quality PCBs that meet customer needs.
Implementation of IPC standards (e.g., IPC-A-610)
Standards like IPC-A-610 set rules for making quality PCBs. They give clear steps for things like soldering and placing parts. Following these rules ensures boards are consistent and dependable.
What is IPC-A-610?
IPC-A-610 is the top standard for PCB assembly. It explains what a “good” board should look like, including solder quality, part alignment, and cleanliness. Following these rules helps meet industry standards.
Why it’s important
Using IPC standards isn’t just about following rules. It builds trust with customers. It shows that quality and reliability are priorities in the manufacturing process.
How manufacturers implement IPC standards
Training: Workers are trained regularly on IPC rules.
Audits: Checks are done often to ensure rules are followed.
Documentation: Records are kept to track compliance and fix problems.
Fun Fact: IPC-A-610 has levels for different uses. Class 1 is for basic electronics, while Class 3 is for critical items like medical or aerospace devices.
By using IPC standards, manufacturers improve their processes and satisfy customers. Everyone benefits from better quality.
Post-Production Quality Assurance by USA-Based PCBA Manufacturers
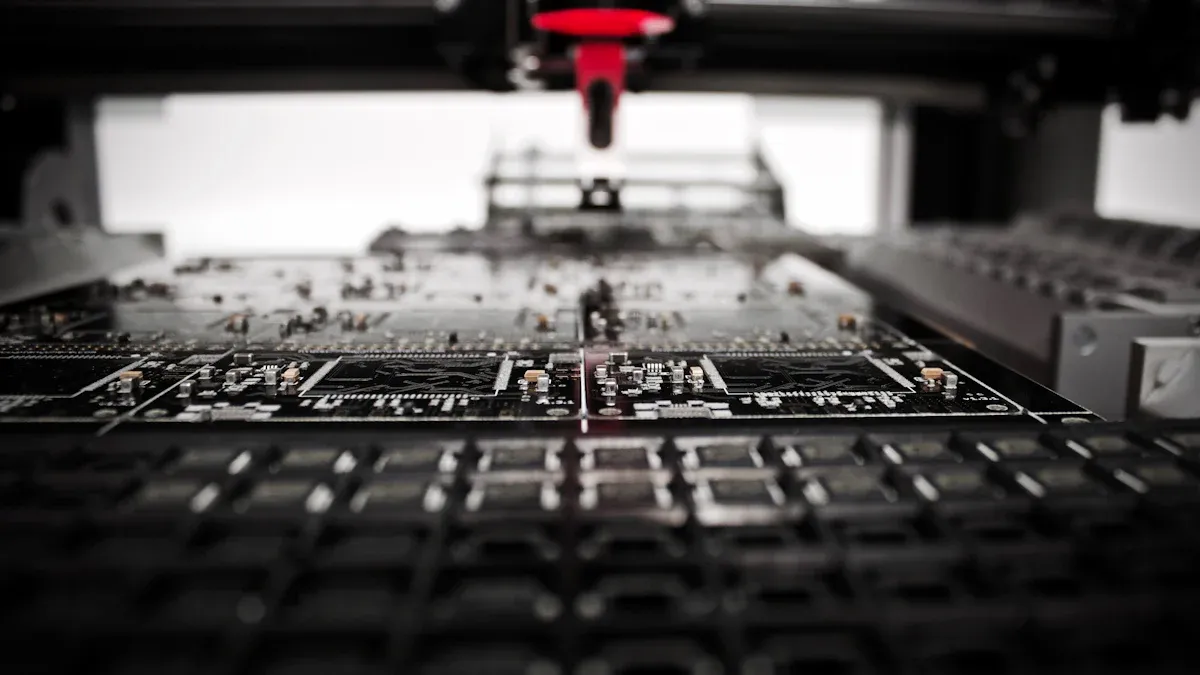
Final checks to confirm product works
After making PCBAs, they are checked to ensure they work. This step finds hidden problems before products are sent out. USA-based PCBA makers use advanced tests like functional validation. This test adds software to the board to see if it works in real-life situations.
Final checks also include looking for physical problems. These could be soldering mistakes or parts in the wrong place. By using these methods, manufacturers make sure the boards are high quality. Careful checks improve reliability and lower the need for fixes or replacements.
Testing for strength and tough conditions
To make sure PCBAs last, manufacturers test them under hard conditions. These tests show weak spots by copying extreme situations. Here are some common tests:
Test Type | What It Does | Why It’s Done |
---|---|---|
HALT – Highly Accelerated Lifetime Testing | Pushes boards to extreme limits to find design flaws. | Finds early problems by testing beyond normal conditions. |
HASS – Highly Accelerated Stress Screening | Uses heat and shaking to cause early failures. | Removes bad boards before they are shipped. |
Shock and Drop Testing | Drops and hits boards to test their strength. | Checks if boards can handle impacts in portable devices. |
Burn-In Testing | Runs boards in tough conditions to find weak ones. | Ensures only strong boards are sent out. |
These tests make sure PCBAs are strong and reliable, even in hard environments. By doing this, USA-based PCBA makers create products that last and balance quality with cost.
Following rules and earning certifications
Certifications prove that PCBAs meet industry rules. USA-based PCBA makers follow standards like IPC-A-600, ISO 9001, and RoHS. These rules ensure boards are safe, reliable, and eco-friendly. For example:
IPC-A-600 checks the quality of circuit boards.
ISO 9001 ensures good processes and steady quality.
RoHS stops harmful materials, helping the environment.
UL Certification checks fire safety and electrical performance.
Manufacturers also use Statistical Process Control (SPC) to track production. This method finds and fixes problems early. By following these rules, manufacturers meet your needs and build trust with great customer service.
Feedback loops for continuous improvement
Improving quality is key in making PCBAs. Feedback loops help make processes better and products top-quality. How does it work? Information is collected from testing, customer feedback, and production results. This data is then used to fix issues and improve.
Here’s how feedback loops help PCBA quality:
Feedback Source | How It Helps Quality |
---|---|
Testing Results | Finds repeated problems and fixes them to avoid future issues. |
Customer Inputs | Matches production to real needs, making products meet expectations. |
Production Outcomes | Spots slowdowns, making manufacturing faster and more reliable. |
Using this information reduces mistakes and improves efficiency. For example, custom QA plans let manufacturers check for specific customer needs. Clear reports keep everyone informed, building trust and delivering what customers want.
Pro Tip: Teams should always share feedback. Open communication speeds up fixes and keeps quality steady.
Case studies: Solving tough quality problems
PCBA makers sometimes face hard problems. But with smart tools and ideas, they can solve even the hardest challenges. Let’s see how new technologies are changing quality control.
One study shows how framing problems well and using tech tools can help. This method doesn’t just fix issues—it stops them before they happen.
“This research offers two key benefits: framing the problem and using technical tools to solve it. The first helps industry workers, while the second is useful for researchers. Framing the problem is new and hasn’t been explored much in past studies, which mostly focus on finding and fixing issues.”
AI tools are also changing the game. Here’s how they improve quality control:
Machine Learning and Deep Learning find defects and spot unusual issues.
AI studies big data to find patterns missed by older methods.
These tools improve accuracy, cut errors, and save time.
By using these advanced tools, manufacturers can solve problems quickly and make sure PCBAs are always high-quality.
Quality control in PCBA making is very important. It ensures products are reliable and work well. By checking every step, from materials to testing, each board meets high standards. USA-based makers use smart tools, strict rules, and skilled workers to get great results.
Good quality control does more than improve products. Here’s why it matters:
Benefit | What It Means |
---|---|
Fewer Defects | Smart tools like AI find problems early, improving quality. |
Better Production | Predictive tools make production faster and more efficient. |
Lower Costs | Fewer mistakes save money and make processes smoother. |
Strong quality control prevents issues like bad soldering or missing parts. This saves money and builds customer trust. In the end, everyone benefits from better quality and lower costs.
FAQ
What does quality control do in PCBA manufacturing?
Quality control makes sure every PCBA is high quality. It finds problems early, makes products more reliable, and saves money. This means better products that last longer.
How do USA-based PCBA makers check if parts are real?
They buy parts from trusted suppliers and use tools like X-rays. This ensures the parts are real, safe, and work well without being fake.
Why are tests like AOI and ICT important?
These tests find problems during production. AOI looks for surface mistakes, and ICT checks if the board works right. Together, they make products more accurate and reduce errors.
How do manufacturers use customer feedback?
They study feedback to make products and processes better. Reviews, test results, and data help them find and fix problems. This keeps customers happy and improves quality.
What certifications should a PCBA maker have?
Look for IPC-A-610, ISO 9001, and RoHS certifications. These show the maker follows rules for safety, quality, and helping the environment.
See Also
Achieving Superior Quality Through Effective PCBA Manufacturing Strategies
Ensuring PCB and PCBA Quality: The RSJPCBA Approach
Guidelines for PCBA Assembly and Avoiding Frequent Mistakes
Selecting the Ideal PCBA Manufacturer to Meet Your Requirements
Comparing Turnkey and Consignment PCBA Manufacturing Approaches in 2025