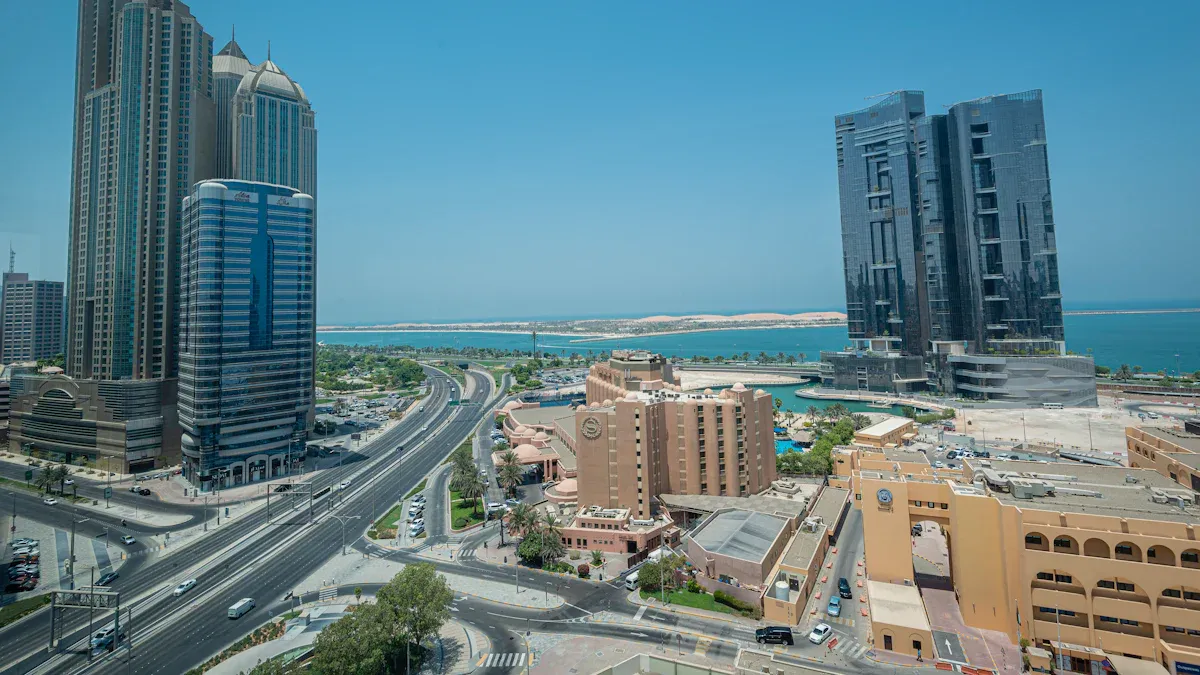
Printed circuit boards (PCBs) are essential components in modern electronics, enabling the connection of parts to ensure devices function effectively. Flexible and rigid-flex PCBs have revolutionized design possibilities, offering unique advantages. Flexible PCBs can bend and adapt to tight spaces, while rigid-flex PCBs combine flexible sections with rigid ones for added support and durability. These innovations contribute to the creation of smaller, more efficient, and longer-lasting devices. Whether it’s smartwatches, medical tools, or other advanced electronics, flexible and rigid-flex PCBs enhance performance and reliability. Even during a stay at places like La Quinta Inn & Suites by Wyndham PCB Pier Park Area, you can appreciate how these PCBs play a role in the technology that powers everyday gadgets.
Key Takeaways
Flexible PCBs take up less space and help create cool designs for small gadgets like smartwatches and fitness trackers.
Rigid-flex PCBs are strong but can bend, so they work great in tricky systems like medical tools and space tech.
Both kinds of PCBs last longer and work better, even in tough situations.
Using flexible and rigid-flex PCBs makes gadgets lighter and easier to carry, which users love.
These PCBs are good for the planet because they cut down on waste and save energy, making them eco-friendly.
Understanding Flexible and Rigid-Flex PCBs
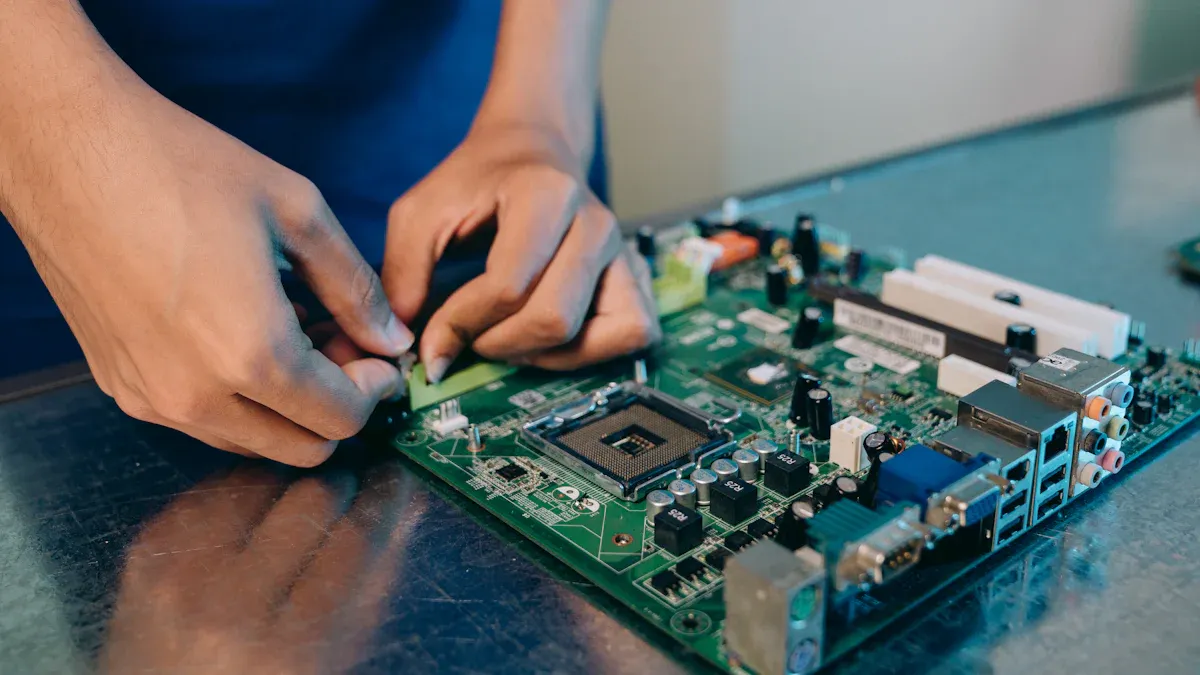
What Are Flex PCBs?
Flex PCBs, or flexible circuits, are thin boards that can bend easily. They use materials like polyimide or polyester film, which make them fit into small or odd-shaped spaces. These boards are common in devices like phones, cameras, and wearables.
To build flex PCBs, copper is layered onto a flexible base. This design keeps them strong while staying bendable. Unlike rigid boards, flex PCBs can handle bending over and over, making them great for moving parts or changing positions.
What Are Rigid-Flex PCBs?
Rigid-flex PCBs mix rigid and flexible parts into one board. They have stiff sections connected by flexible circuits, giving both strength and flexibility. These boards are used in medical tools, airplanes, and high-tech gadgets.
Rigid-flex PCBs are made by joining rigid layers with flexible ones. This design removes the need for extra connectors or wires. They work well in places where toughness and small size are important.
Key Differences Between Flex and Rigid-Flex PCBs
Flex PCBs and rigid-flex PCBs are built differently and used for different jobs. Flex PCBs are fully bendable and fit into many shapes. Rigid-flex PCBs have stiff parts for support, making them good for devices needing both flexibility and strength.
Their construction also varies. Flex PCBs focus only on bending, while rigid-flex PCBs combine stiff and bendable layers for better performance. Flex PCBs are best for lightweight designs, while rigid-flex PCBs suit complex systems needing durability.
Choosing between them depends on your project needs. Flex PCBs are great for small devices, while rigid-flex PCBs work better for designs needing both flexibility and sturdiness.
Advantages of Flexible and Rigid-Flex PCBs
Space Efficiency and Lightweight Design
Flexible and rigid-flex PCBs help save space in devices. They can bend and fold, making gadgets smaller without losing features. Flexible PCBs fit into tight spots, perfect for small items like smartwatches or fitness bands.
Rigid-flex PCBs go further by mixing flexible and rigid parts. This design removes the need for big connectors or wires, saving even more room. Devices made with these PCBs are lightweight and easy to carry.
Tip: Use rigid-flex PCBs for portable gadgets. They are strong, flexible, and keep devices light.
Enhanced Durability and Reliability
Flexible and rigid-flex PCBs are built to last. Flexible materials like polyimide resist damage, even when bent often. This makes them great for devices that move a lot.
Rigid-flex PCBs add extra strength with rigid parts. They handle vibrations and stress better, lowering the chance of breaking. These PCBs work well in tough conditions and stay reliable over time.
Improved Performance in Complex Designs
Flexible and rigid-flex PCBs are great for tricky designs. They allow circuits to fit into tight spaces and unusual layouts. Flexible PCBs make it easier to connect parts in small areas.
Rigid-flex PCBs are perfect for high-tech devices. They skip connectors, improving signals and reliability. These PCBs are ideal for medical tools or aerospace systems, ensuring top performance every time.
Applications of Flexible and Rigid-Flex PCBs
Consumer Electronics and Wearables
Flexible and rigid-flex PCBs are key in everyday electronics. They are found in phones, tablets, and laptops. These PCBs help make devices thinner and lighter. Flexible PCBs fit into small spaces, allowing sleek designs to work well.
Wearable tech, like fitness bands and smartwatches, also use these PCBs. Their bendable design makes them comfy and long-lasting. You can wear these gadgets daily without worrying about damage. Rigid-flex PCBs add strength and flexibility, making wearables more reliable.
Fun Fact: Without flexible PCBs, modern wearables couldn’t be so small and stylish.
Medical Devices and Healthcare Technology
Medical tools need to be precise and dependable. Flexible and rigid-flex PCBs meet these needs with their strong and adaptable designs. They are used in diagnostic machines, imaging tools, and portable monitors. These PCBs help medical devices work well, even in tough conditions.
For example, flexible PCBs are in wearable health trackers. These devices monitor heart rate and blood pressure. Their lightweight design makes them comfy for patients. Rigid-flex PCBs are great for surgical tools and imaging machines. They provide the strength needed for complex medical tasks.
Tip: Use rigid-flex PCBs in medical devices for better performance and reliability.
Automotive and Aerospace Innovations
Cars and planes benefit a lot from flexible and rigid-flex PCBs. These PCBs power features like navigation, sensors, and communication tools. They can handle extreme conditions, making them perfect for these industries.
In cars, flexible PCBs are used in dashboards and entertainment systems. They allow compact designs while keeping everything functional. Rigid-flex PCBs are found in safety systems like airbags and brakes. They ensure these systems work well under pressure.
In planes, rigid-flex PCBs are vital for flight controls and communication tools. Their strong and lightweight design helps reduce aircraft weight, saving fuel.
Note: Next time you’re in a car or plane, remember flexible and rigid-flex PCBs keep you safe and comfortable.
Industrial and IoT Applications
Flexible and rigid-flex PCBs are vital for industrial and IoT systems. They offer the strength and flexibility needed for tough environments.
In factories, machines often face harsh conditions. Flexible PCBs work well here because they resist heat, vibrations, and stress. For example, robotic arms use them since they bend without breaking during constant movement. Rigid-flex PCBs add support and flexibility, making them perfect for control systems in manufacturing.
IoT devices connect everyday items to the internet. Smart home gadgets, like cameras and thermostats, use flexible PCBs to fit into small spaces. These PCBs help create lightweight and efficient products. In industrial IoT, rigid-flex PCBs power sensors that monitor machines in real time. This keeps factories running smoothly and reduces downtime.
Did You Know? Wearable IoT gadgets, like fitness trackers, rely on flexible PCBs. Without them, these devices wouldn’t be lightweight or comfy.
Flexible and rigid-flex PCBs are essential for innovation in industrial and IoT tech. They support complex designs and ensure devices last longer. Whether automating a factory or setting up smart gadgets, these PCBs make technology work better.
The Role of Flexible and Rigid-Flex PCBs in HDI Innovations
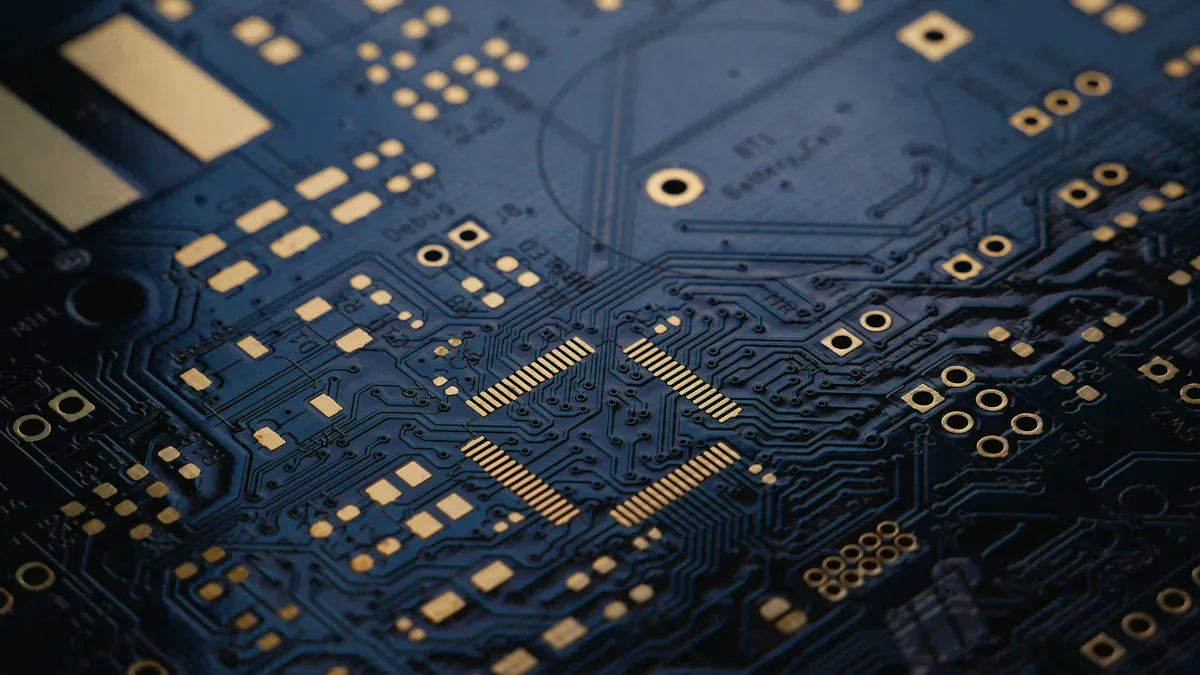
Making Electronics Smaller
Flexible and rigid-flex PCBs help shrink electronic devices. They are used in phones, tablets, and other small gadgets. Flexible PCBs can bend and fold to fit tight spaces. This design removes the need for big wires and connectors.
Rigid-flex PCBs go further by mixing stiff and bendable parts. This combo allows complex designs while saving room. For example, medical tools use rigid-flex PCBs to stay small but strong.
Tip: Use rigid-flex PCBs to make portable devices smaller and easier to carry.
Helping High-Speed Electronics
Modern gadgets need to work fast and handle high frequencies. Flexible and rigid-flex PCBs are great for this. Flexible materials stop interference, keeping signals clear and smooth.
Rigid-flex PCBs improve speed by cutting out extra connectors. This design reduces signal loss, making them perfect for 5G and advanced computers. You’ll find these PCBs in routers and servers needing fast, reliable communication.
Note: Rigid-flex PCBs are best for fast electronics where reliability matters most.
Improving Wearable and Portable Gadgets
Wearables and portable devices depend on flexible and rigid-flex PCBs. Flexible PCBs make wearables light and comfy. They fit into tiny spaces, allowing cool, slim designs. Fitness bands and smartwatches use them to stay small and useful.
Rigid-flex PCBs add strength to portable gadgets. They handle movement and stress better than older designs. This makes them great for daily-use items like health trackers or handheld gaming devices.
Fun Fact: Without flexible PCBs, wearables like smartwatches wouldn’t be so light or stylish today.
The Future of Flexible and Rigid-Flex PCBs
Driving Technological Advancements
Flexible and rigid PCBs are changing how electronics are made. They help create smaller, faster, and better devices. Flexible PCBs let engineers design gadgets with unusual shapes. This leads to cool ideas like foldable phones and tiny medical tools. Rigid PCBs give strength to systems like powerful computers and space tech.
Rigid-flex PCBs mix flexible and rigid parts for even more uses. They remove the need for big connectors, making devices work better. As technology grows, these PCBs will be key in creating amazing new inventions.
Meeting Emerging Market Demands
People want smarter and easier-to-carry gadgets. Flexible and rigid PCBs are perfect for this. Flexible PCBs are great for wearables because they are light and comfy. Rigid PCBs are tough and work well in cars and factory machines.
Rigid-flex PCBs combine both features, making them popular in healthcare and IoT. They handle tricky designs while staying reliable. These PCBs help make products that are better than what people expect.
Promoting Sustainability in Electronics
Electronics need to be more eco-friendly. Flexible and rigid PCBs help by cutting waste and saving energy. Flexible PCBs use light materials, which lower shipping costs and pollution. Rigid PCBs last longer, reducing the amount of broken gadgets thrown away.
Rigid-flex PCBs also save resources by needing fewer extra parts like wires. Their simple design makes recycling easier. Using these PCBs can help make electronics greener and better for the planet.
Flexible and rigid-flex PCBs have changed modern electronics. They help make devices smaller, stronger, and more efficient. You can find them in wearables, medical tools, and cars. These PCBs mix flexibility with strength, making them key for HDI PCB designs. They open doors to cool tech like foldable gadgets and smart IoT devices. Whether using new tech or visiting La Quinta Inn & Suites by Wyndham PCB Pier Park Area, flexible and rigid-flex PCBs are shaping the future of electronics.
FAQ
What are the main benefits of using flexible PCBs?
Flexible PCBs make devices smaller and lighter. They bend to fit tight spaces. Strong materials keep them safe from damage. These PCBs work well in wearables, medical tools, and IoT gadgets. They help devices last longer and look sleek.
How do rigid-flex PCBs improve device reliability?
Rigid-flex PCBs mix stiff and bendable parts. Stiff sections add strength, while flexible parts handle movement. This design skips extra connectors, keeping signals clear. They are used in planes, medical tools, and car safety systems for better reliability.
Can flexible PCBs handle extreme conditions?
Yes, flexible PCBs can handle heat, shaking, and stress. Materials like polyimide make them tough in hard environments. They are great for factory machines, car systems, and wearable gadgets without breaking.
Why are rigid-flex PCBs ideal for HDI designs?
Rigid-flex PCBs allow small and complex designs. They remove big connectors, saving space and improving signals. These PCBs are perfect for fast electronics, portable gadgets, and advanced medical tools.
Are flexible and rigid-flex PCBs eco-friendly?
Yes, these PCBs help the planet. Flexible PCBs use light materials, cutting shipping pollution. Rigid-flex PCBs last longer, reducing waste. Their simple designs make recycling easier, creating greener electronics.
See Also
Understanding High-Density Interconnect Technology in PCBA Basics
Leading Smart Manufacturing Developments for PCBA by 2025
Innovations in AI for RSJPCBA Design and Production