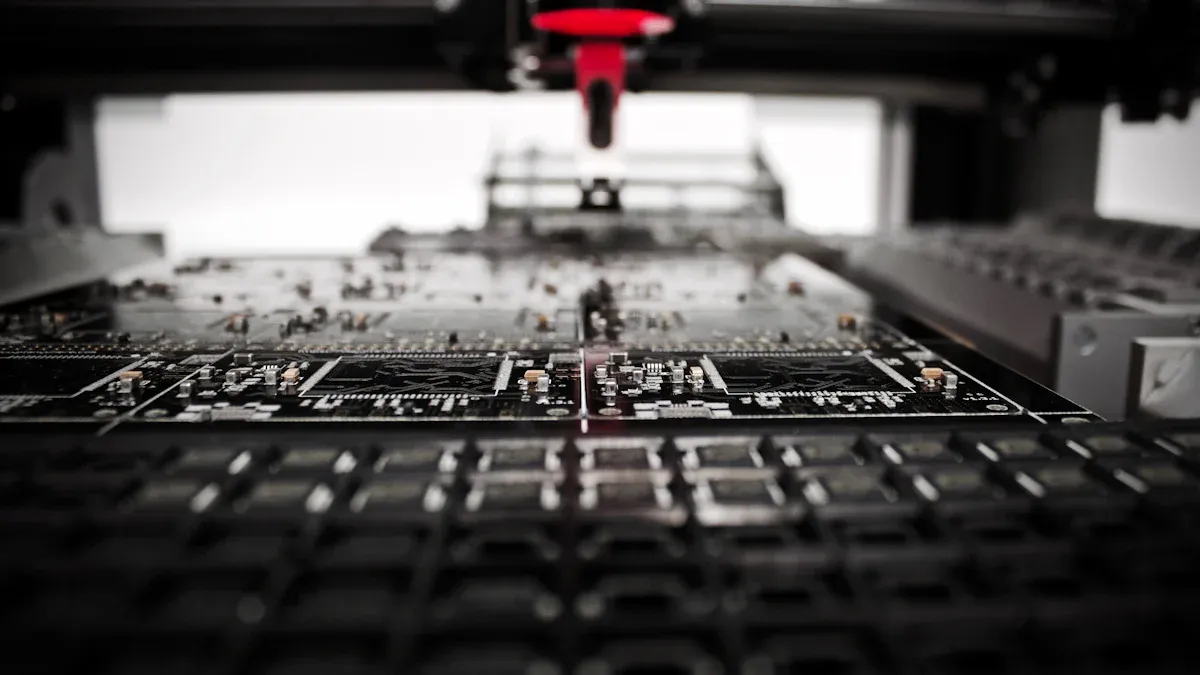
Choosing the best industrial sensor PCB assembly service is important. The market for industrial sensors is growing quickly. It is expected to increase from $19.28 billion in 2019 to $44.94 billion by 2032. The electronic manufacturing services industry is also expanding. By 2025, it may earn $614.57 billion, growing at a rate of 7.3% each year. These numbers show the need for good and dependable assembly services.
Many things affect your choice. For example, managing heat is very important. SMT parts can get damaged by too much heat. Reflow soldering helps protect these parts. Working together with engineers and using better materials make stronger designs. These steps help ensure your sensor PCB assembly is high-quality and reliable.
Key Takeaways
Picking the right PCB service is key for success. Look for companies with good quality checks and certifications.
Learn about pricing options to match your project size. Small projects may use pay-per-unit, while big ones need tiered plans.
Watch out for extra costs that could hurt your budget. Always ask for a full price list to avoid surprises.
Choose quality over cheap prices. Good services might cost more but save money on fixes later.
Clear communication with your provider gives updates and avoids project delays.
Cost Comparison
Pricing Models in 2025
In 2025, pricing for PCB assembly services offers more choices. You can pick pay-per-unit, subscription plans, or tiered packages. Each option fits different production needs. Pay-per-unit is great for small projects. Subscription plans work well for ongoing needs. Tiered packages give discounts for bulk orders, perfect for big productions.
Think about your project size when choosing a pricing model. A small batch might not need a subscription plan. But, large-scale production can save money with tiered pricing. Knowing these options helps you pick the best one for your budget and goals.
Balancing Affordability and Value
Saving money is important, but quality matters too. Cutting costs too much can lead to bad products and higher expenses later. Instead, focus on balancing cost and value.
For example, a provider using advanced techniques may charge more. But their expertise can create better PCBs, reducing failures. Reliable services ensure your sensors work well, saving repair and replacement costs.
To find this balance, compare providers’ processes, tools, and history. Check reviews and case studies to see their value. By focusing on value over price, you make a smarter choice for your needs.
Identifying Hidden Costs
Hidden costs can hurt your budget if ignored. Some providers show low prices but add fees for extra services. These could include fast shipping, design changes, or testing. Always ask for a full cost breakdown before choosing a provider.
Delays in assembly can also add hidden costs. Missed deadlines might cause penalties or lost income. Picking a reliable provider with a good track record avoids these problems.
Poor-quality PCBs can also cost more in the long run. A cheaper provider might save money now but lead to failures later. This could mean repairs, replacements, or harm to your reputation. Spotting hidden costs early helps you avoid surprises and stick to your budget.
Quality and Reliability
Standards and Certifications for Industrial Sensors
When picking a provider for industrial sensor PCB assembly, choose one that follows important standards and certifications. These rules make sure the process is safe and high-quality.
Some key certifications include:
ISO 26262: This ensures electronic systems are safe and prevent failures.
AEC-Q100: This guarantees reliable parts, especially for car-related PCBs.
Other certifications like IPC-A-610 and IPC-A-600 are also important. They help ensure PCBAs are dependable. The table below shows key standards and their uses:
Standard | Description | Application Level |
---|---|---|
IPC-A-610 | Checks final product quality in PCB assembly. | Electronics |
IPC-A-600 | Ensures PCBAs are reliable for critical uses. | Aerospace, Automotive |
IPC Class 3A | Highest reliability standard for aerospace PCBAs. | Aerospace |
Picking a provider with these certifications ensures consistent and reliable results.
Reliability Metrics in PCB Assembly
Reliability metrics show how well PCBAs work and last. These are very important for industrial sensors, where failure is not an option.
Important tests include:
Automated Optical Inspection (AOI): Finds defects like bad solder or cracks.
Continuity Test: Checks for open or short circuits using DC current.
Hi-pot Test: Tests safety by checking isolation in high-voltage PCBs.
Thermal Shock Tests: Measures how PCBAs handle quick temperature changes.
The table below explains more reliability metrics:
Metric | Description | Measurement Type |
---|---|---|
In-circuit Testing | Finds shorts, opens, and checks voltage/current at points. | N/A |
Resistivity of Solvent Extract (ROSE) | Checks for leftover solder flux by measuring conductivity. | N/A |
Time Domain Reflectometry (TDR) | Measures impedance in single-ended and differential traces. | N/A |
Vibration Tests | Tests under military and aerospace standards. | N/A |
Fire Safety Tests | Meets fire safety rules like NEMA/NFPA/FAA standards. | N/A |
HALT/HASS Tests | Stress tests to find weak parts early. | N/A |
Environmental Exposure Tests | Checks performance in different environmental conditions. | N/A |
Electrical Stress Tests | Tests how PCBAs handle electrical stress. | N/A |
UL Safety Tests | Makes sure safety standards are followed. | N/A |
These tests help you understand how reliable a PCBA is, so you can make better choices.
Ensuring Quality Assurance
Quality assurance is key to making reliable PCBAs. Without good quality control, even advanced processes can fail.
Providers often use many tests to ensure quality. Burn-in testing, for example, stresses PCBAs with high heat and voltage. This finds weak parts before they are sold.
Look for providers using tools like AOI and in-circuit testing. These tools catch problems early, lowering the chance of future failures. Providers following IPC Class 3A standards offer the best reliability, especially for aerospace and critical uses.
By working with a provider focused on quality, you can trust your industrial sensor PCB assembly will meet top standards.
Turnaround Time
Delivery Times Across Providers
In 2025, delivery times for PCB assembly services differ a lot. Some companies use advanced technology to make things faster. For example:
Automation and AI help finish assembly much quicker.
Robots improve accuracy and speed to handle more orders.
Smart factories adjust fast to changes in demand.
These tools let some providers deliver quickly without losing quality. But not all companies use these technologies equally. When picking a provider, check if they have the tools to meet your deadlines.
Factors Influencing Turnaround Time
Many things affect how fast industrial sensor PCB assemblies are made. Knowing these helps you choose wisely.
Factor | What It Means |
---|---|
Complex Designs | Harder designs take more time to build. |
Material Shortages | Missing parts can delay the process. |
Factory Capacity | Busy times may slow down production. |
Strict Quality Checks | Extra testing ensures reliability but takes longer. |
Late Design Changes | Changing designs late can cause setbacks. |
Poor Communication | Misunderstandings between teams can create delays. |
Following Rules | Meeting legal standards adds extra steps. |
Shipping Problems | Delays in shipping or customs can slow delivery. |
Fixing these issues early helps avoid delays and keeps your project on schedule.
Speed vs. Quality in PCB Assembly
Getting things done fast is nice, but quality matters more. Rushing assembly can sometimes skip important checks.
Here’s an example of the trade-off:
Model | Input Size | Accuracy | Speed |
---|---|---|---|
Resnet50 | 800 x 800 | Higher | Slower |
Resnet50 | 640 x 640 | Lower | Faster |
Resnet101 | N/A | N/A | More Parameters |
This shows that better results often take more time. For important uses like industrial sensors, focus on quality. A good PCB assembly lasts longer and avoids problems later.
Technological Advancements in Industrial Sensor PCB Assembly
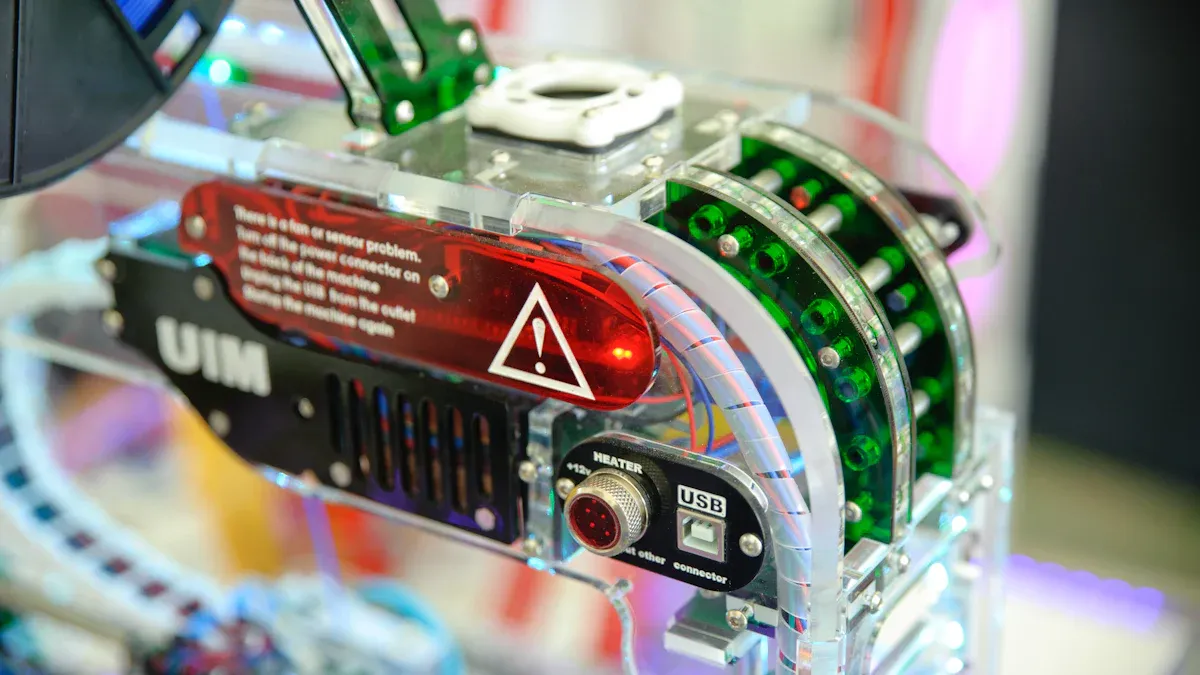
Role of AI and Automation
AI and automation are changing how PCBAs are made. These tools make the process faster and more accurate. Machines now do tasks like soldering and placing parts. This reduces mistakes and keeps the quality steady.
AI tools also help with smart decisions. For example, they study production data to find problems early. Fixing issues sooner saves time and money. AI also improves workflows by spotting delays quickly. This helps your industrial sensor PCBA projects finish on time.
Innovations in Manufacturing Techniques
New ways to make PCBAs are improving how they work. These methods focus on being faster and meeting modern needs. Some important changes include:
High-Density Interconnects (HDI): These allow smaller designs with more connections.
Flexible and Rigid-Flex PCBs: Perfect for devices that bend or move.
Eco-Friendly Materials: Using lead-free solder and recyclable parts helps the planet.
These methods make assembly better and support eco-friendly practices. Using them gives you great results while protecting the environment.
Trends in Miniaturization and Precision
Smaller and stronger devices are becoming more popular. This pushes the need for tiny and precise designs. HDI and microvia technology help make small boards without losing performance. The table below shows key trends shaping PCBA today:
Trend | Description |
---|---|
Advanced HDI Technology | Smaller spaces fit more parts with better designs. |
Microvia Integration | Tiny holes improve how signals move through the board. |
Improved Signal Integrity | Better materials help fast data transfer in small boards. |
Application Expansion | HDI is now used in cars, planes, and medical tools for better results. |
Ultra-Compact Design | Special techniques pack more parts into small spaces without signal problems. |
Advanced SMT Methods | Precise placement allows more parts and better heat control. |
Multi-Layer Flexibility | Flexible boards work well for wearables and smart devices. |
These improvements help meet the needs of modern industries. Using these trends lets you build strong and efficient industrial sensor PCBAs.
Customization and Scalability
Adapting to Custom Designs
Custom designs are key for special industrial sensor needs. In 2025, PCB assembly services are better at handling these demands. Providers now use modular designs that are easy to change. This helps you adjust quickly to new tools or upgrades.
For instance, companies like Sierra Circuits and Punch Through Design show how useful customization is. Circuit boards that used to take a week can now be made overnight. This fast service helps you meet deadlines and win more projects.
Custom software is also very important. It gives more options than ready-made solutions. By combining data from different places, these platforms help you make quick decisions. This makes your assembly process faster and more flexible.
Scaling for Large-Scale Production
Making more industrial sensor PCBAs needs strong systems to keep quality high. In 2025, providers use automation and AI to make production smoother. These tools ensure good results even with bigger orders.
Testing parts one by one is another helpful method. It lowers risks and speeds up production. Modular designs also let you grow without changing everything.
Picking a provider with scalable options helps you handle big orders. This way, your business can grow while staying flexible and competitive.
Flexibility in Prototyping and Small Batches
Prototyping and small batches are great for testing ideas. Small batches save money by avoiding extra stock and outdated parts. Quick production cycles let you test designs faster, giving you an edge.
Finding problems early is another plus. Testing during prototyping leads to better final products. This boosts your reputation and success. Providers who focus on small batches are also quick to adapt. They help you change products based on customer needs.
This flexibility ensures your prototypes and small batches are top-quality. It also keeps costs low and timelines short. Using these services helps you create better products faster.
Customer Support and Service
Communication and Responsiveness
Good communication is key for smooth PCB assembly work. Providers with quick customer support keep you updated at every step. This openness helps you see progress and fix problems early.
In 2025, top providers focus on fast replies. They make sure to communicate clearly so your projects stay on schedule. For example:
Teams answer questions quickly to avoid delays.
Regular updates show how production is going.
Clear steps prevent mistakes during the assembly process.
Picking a provider with great communication saves time and effort. It ensures your needs are handled well.
Post-Sale Support and Problem Resolution
Help after the sale is as important as the assembly itself. Good providers offer full support to fix any issues after delivery. This includes repairs, troubleshooting, and design changes if needed.
Strong post-sale support makes sure your PCB works well. Providers with top-quality checks often have no product rejections. They also follow IPC-A-610 rules to meet industry standards.
When choosing a provider, find one offering complete services. This includes making, sourcing parts, and testing. These providers can solve problems faster and better.
Examples of Exceptional Customer Service
Great customer service makes the best providers stand out. Some companies deliver 100% on time for months in a row. This shows they care about meeting deadlines.
Providers using advanced testing methods improve their service even more. These tests ensure your PCB meets high standards and avoids defects. Full support, from design to testing, shows they value customer satisfaction.
By picking a provider with a strong history, you get smooth service. This ensures high-quality PCBs for your industrial sensors.
Picking the best industrial sensor PCB assembly service in 2025 needs careful thought. You should look at cost, quality, speed, technology, custom options, and customer help. These factors are key to making sure your project is done well and on time.
The industrial sensor PCB assembly market is growing fast. By 2025, it could reach USD 40.80 billion, with a yearly growth rate of 3.44% until 2034. This growth comes from more demand for electronics, better automation, and more complex circuits. The table below shows important industry facts:
Metric | Value |
---|---|
Market Size (2025) | USD 40.80 Billion |
Compound Annual Growth Rate | 3.44% (2025-2034) |
Key Drivers | More demand for electronics, better automation, complex circuits, use in cars, eco-friendly rules |
To find the right service, balance cost and quality. Don’t pick providers with cheap prices but poor quality. Choose those with good reviews, modern tools, and helpful support. Think about what you need most, like quick delivery, large orders, or special designs. Matching these with your goals will help you get a reliable and affordable service.
FAQ
What matters most when picking a PCB assembly service?
Focus on quality and reliability. Choose providers with certifications like IPC-A-610 and ISO 26262. These certifications ensure safe and high-quality results. Reliable services help avoid failures and save money later.
How can I keep my PCB assembly project on time?
Pick a provider with advanced tools and clear communication. Regular updates and quick replies prevent delays. Fix design issues early to avoid setbacks.
Are eco-friendly materials used in PCB assembly?
Yes, many providers now use lead-free solder and recyclable parts. These materials follow environmental rules and lower your carbon footprint. Ask your provider about their green practices.
How does AI help in PCB assembly?
AI makes production faster and more accurate. It spots problems early and improves workflows. This keeps quality steady and speeds up delivery times.
Can I grow from prototypes to big production with one provider?
Yes, many providers offer scalable solutions. Modular designs and automation make it easy to switch from small batches to large orders. This flexibility helps your business expand.
💡 Tip: Check a provider’s scalability options before starting long-term projects.
See Also
Key Developments Influencing Industrial IoT PCB Assembly By 2025
Evaluating Premier One-stop PCBA Manufacturing Solutions For 2025
Understanding Automotive PCBA Assembly And Its Importance In 2025
New Developments In FDA-Compliant PCBA Services For Healthcare Devices
Grasping ITAR Regulations Impacting PCBA Manufacturing In 2025