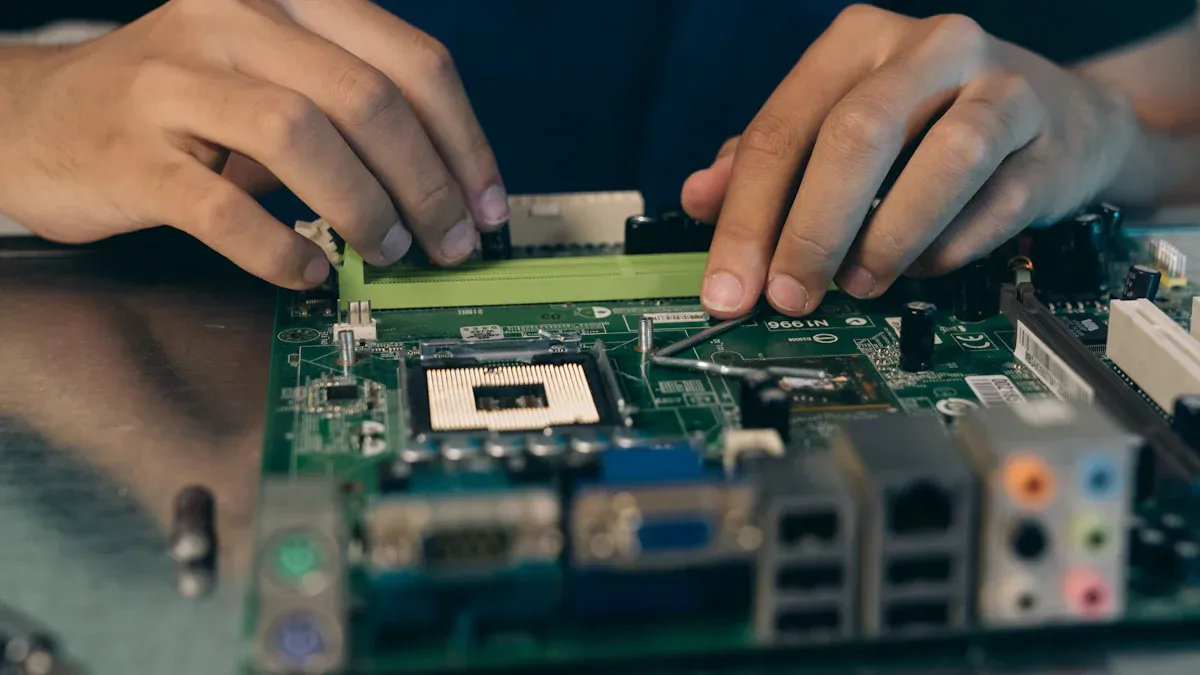
Printed circuit board assembly is very important in electronics today. Picking between through-hole PCB assembly techniques and surface mount methods depends on your project. Through-hole assembly puts parts into drilled holes, while surface mount places parts directly on the board.
In 2025, the market is changing fast. Surface mount is leading with over 57% of passive parts. Its speed and ease make it grow the fastest. Still, through-hole PCB assembly techniques are key for strong and reliable uses. Choosing the right method helps your designs work well and save money.
Key Takeaways
Through-hole technology creates strong connections. It works well in tough places like space and military projects.
Surface mount technology is quicker and cheaper. It helps make small designs and packed layouts, great for gadgets.
Mixed technology uses both methods. It makes boards strong and keeps them small.
Machines are changing PCB assembly. They make it faster and more exact, which helps modern factories.
Being eco-friendly in PCB assembly is important now. Green practices save money and help the planet.
Overview of Through-Hole Technology
What is Through-Hole PCB Assembly?
Through-hole PCB assembly, or THT, is an older way to attach parts to a circuit board. It uses drilled holes where component leads are placed. These leads are soldered to pads on the other side of the board. This creates strong electrical and physical connections.
This method started in the early 1900s and improved during World War II. Paul Eisler helped change the industry by inventing printed circuit boards. This replaced the slow process of hand-soldering wires. Through-hole assembly became important for reliable electronics like radios and military gear.
Metric/Definition | Description |
---|---|
Through-Hole Technology (THT) | Drilling holes in PCBs for leads, ensuring strong connections. |
Solder Joint Quality | How good solder joints are, affecting performance and lifespan. |
Types of Holes | Includes Plated Through Hole (PTH) and Non-Plated Through Hole (NPTH). |
Component Types | Active and passive parts with axial or radial leads. |
Assembly Time | Time needed to attach parts, affecting production speed. |
Advantages of THT | Strong connections, heat resistance, and easy repairs for many uses. |
Advantages of Through-Hole Assembly
Through-hole assembly has many benefits for certain projects.
Components attached with THT are less likely to break during use.
The process makes strong bonds between parts and the board, working well in tough conditions.
It handles high heat, making it great for aerospace and military devices.
Repairs are simpler because parts are easier to reach than surface-mounted ones.
These features make through-hole assembly a good choice for durable and heat-resistant designs.
Disadvantages of Through-Hole Technology
Through-hole technology has some problems despite its strengths. Bigger parts take up more space on the board. Drilling holes for each lead uses valuable area, leaving less room for other parts. This can also make routing signal paths harder, which may affect how circuits work.
The process takes more time and effort than surface mount technology. Drilling, placing leads, and soldering are slower, raising production costs. For large-scale manufacturing, this lowers efficiency.
As devices get smaller, through-hole mounting struggles to keep up. It doesn’t work well for tiny designs, making it less useful for modern gadgets.
Applications of Through-Hole PCB Assembly Techniques
Through-hole PCB assembly is used in many areas needing strength and reliability. This method is great for projects that need strong parts and can handle tough conditions.
Prototyping and Hobby Projects: THT works well for small projects and prototypes. You can test circuits by hand, skipping costly testing tools. This makes it a budget-friendly option for hobbyists and engineers trying new ideas.
Aerospace and Military Equipment: Harsh environments like aerospace and military use through-hole mounting. Strong soldering keeps parts secure during vibration, heat, or pressure.
Industrial Machinery: Big machines often use THT for their circuit boards. The strong connections handle stress and high currents in industrial work.
Repairable Electronics: Through-hole technology makes fixing things easier. You can replace or re-solder parts, which is helpful for products needing repairs.
Educational Kits: Many learning kits use through-hole assembly. Bigger parts and visible leads help beginners learn soldering and circuits.
Through-hole mounting is also good for small-batch productions. It uses cheap tin-lead solder and helps check for problems like board bending. This makes timelines easier to manage, especially for hand-made boards.
If you need strength, easy repairs, or simple testing, through-hole technology is a solid choice. It’s still popular where durability and simplicity matter more than making things tiny.
Overview of Surface Mount Technology
What is Surface Mount Technology?
Surface mount technology (SMT) changed how PCBs are made. It lets parts stick directly to the board’s surface. Unlike through-hole methods, SMT skips drilling holes. This makes it faster and easier. Surface mount devices (SMDs) are small parts without leads. They attach to the board using solder paste. The process has three steps: add solder paste, place parts, and heat the board in a reflow oven to secure them.
SMT started in the 1960s as “planar mounting.” It became popular in the 1970s for saving space and time. By the 1980s, pick-and-place machines made SMT the top choice for PCB assembly. Today, it’s used in industries like cars, phones, and electronics. These fields need small, high-density designs.
Advantages of Surface Mount Assembly
Surface mount assembly has many benefits for modern electronics.
Compact Designs: SMT uses smaller parts and fits more on the board. This improves speed and performance.
Cost-Effectiveness: No drilling means lower costs. Automated tools help make large amounts quickly.
Improved Electrical Performance: Shorter paths improve signals and reduce interference.
Faster Production: Machines speed up the process, saving time.
These features make SMT perfect for industries needing small and fast designs.
Feature | Surface Mount Technology (SMT) | Through Hole Technology (THT) |
---|---|---|
Component Density | High, uses both sides of the board | Lower, uses one side only |
Size of Components | Smaller, great for tiny designs | Bigger, takes more space |
Automation | Mostly automated process | Needs more manual work |
Cost-Effectiveness | Cheaper for large production | Costly for small production |
Disadvantages of Surface Mount Technology
SMT has some downsides too.
Difficult Repairs: Small parts are hard to fix. Sometimes, the whole board needs replacing.
High Equipment Costs: SMT needs special machines that are pricey to buy and maintain.
Temperature Sensitivity: Parts can get damaged by heat, so soldering must be careful.
Inspection Challenges: Tiny parts make checking quality harder and more expensive.
Disadvantage | Description |
---|---|
Hard to Repair | Small parts make fixing tough, often needing board replacement. |
Expensive Equipment | Special machines cost a lot to buy and maintain. |
Heat Sensitivity | Parts need careful soldering to avoid damage. |
Static Sensitivity | Anti-static tools are needed to protect parts. |
Hard to Inspect | Tiny parts make quality checks tricky and costly. |
SMT is great for saving space and time. But its challenges mean you need good planning and tools.
Applications of Surface Mount Assembly
Surface mount assembly is very important in making modern electronics. It is used in industries needing small designs, fast production, and low costs.
Consumer Electronics
Surface mount assembly is widely used in consumer electronics. In 2022, it made up 32.5% of the market. It helps make phones, smartwatches, and gaming consoles. These devices need small parts and quick production. SMT helps companies meet the demand for light and portable gadgets.
Industrial Automation
In factories, SMT is used for medical tools, power devices, and automation machines. It handles complex parts, improving how things work. This sector is growing fast, with a 7.7% yearly growth rate. SMT’s accuracy and speed make it great for tough and high-performing systems.
Automotive Sector
The car industry depends on SMT for large-scale production. It lowers costs while keeping quality high. SMT is used in sensors, control units, and car entertainment systems. As cars get smarter, SMT helps fit more parts without losing strength.
Tip: For projects needing large production, SMT is the best option. Its automated process and ability to scale make it ideal for big manufacturing jobs.
Sector | Benefits |
---|---|
Industrial | Fastest growth at 7.7%, used in medical tools, automation, and power devices. |
Consumer Electronics | 32.5% market share, helps make smaller and faster products. |
Automotive | Grows with mass production, saving costs with high quality. |
Surface mount assembly keeps improving PCB designs. It works well for everything from gadgets to factory machines. Using SMT’s benefits, you can build reliable and efficient products.
Key Differences Between Through-Hole and Surface Mount Technologies
Assembly Process Comparison
The way through-hole and surface mount technologies are assembled is very different. Through-hole PCB assembly needs parts to go into drilled holes. These parts are soldered to pads on the other side of the board. This process often takes more time and uses manual or partly automated work.
Surface mount technology (SMT) skips drilling holes. Parts are placed directly on the board using solder paste. Machines do most of the work, like placing parts and heating them in a reflow oven. This makes production faster and reduces mistakes.
Parameter/Aspect | Through-Hole Technology | Surface Mount Technology (SMT) |
---|---|---|
Component Size | Bigger parts with leads or pins | Smaller parts without leads |
Component Density | Lower density, larger boards | Higher density, smaller boards |
Assembly Time | Slower due to manual work | Faster with machines |
Assembly Process | Manual or partly automated | Fully automated |
Rework and Repair | Easier because leads are accessible | Needs special tools |
Note: SMT is great for making many products quickly. Through-hole works better for small or special projects.
Cost Considerations
Cost is an important factor when picking between these two methods. Through-hole assembly costs more. It uses bigger parts and takes more time because of manual work. Drilling holes and soldering parts by hand also need extra resources.
SMT is cheaper. Automation lowers labor costs, and smaller parts allow for more production. This makes SMT the best choice for industries making large amounts of products.
Technology Type | Cost Factors |
---|---|
Through-Hole | Costs more due to manual work and bigger parts. |
Surface Mount | Costs less because of automation and higher production rates. |
To save money, think about your project’s size and needs. Through-hole is worth it for small or repairable designs. For large-scale production, SMT is a smarter choice.
Reliability and Durability
Reliability is another big difference between these two methods. Through-hole parts make strong bonds with the board. This makes them tough and able to handle vibration, heat, and stress. For tough jobs like aerospace or factory machines, through-hole is often better.
SMT is fast but less durable. Its small parts and lack of strong leads make it easier to damage from vibration or shocks. Still, SMT is great for projects where saving space and speed matter more than strength.
Through-Hole Technology: Strong and durable, good for tough jobs.
Surface Mount Technology: Fast and space-saving, great for high-density designs.
Tip: Use through-hole for projects needing strength and reliability. Pick SMT for compact and fast designs.
Application Suitability
When picking between through-hole and surface mount methods, think about your project’s needs. Each method has its own strengths and weaknesses, so knowing these will help you decide.
Through-hole technology is great for projects needing strength and reliability. Its parts make strong connections, which work well in tough conditions. For example, aerospace and military devices use through-hole because it handles vibration, heat, and stress. It’s also good for prototypes and repairable designs. You can easily replace or fix parts, making testing and repairs simple.
Surface mount technology is best for modern, compact designs. It fits more parts on smaller boards, making it ideal for gadgets like phones, laptops, and smartwatches. SMT is also great for large-scale production. Its automated process speeds up manufacturing and lowers costs. This is why industries like automotive and factory automation prefer SMT. However, SMT doesn’t do as well in harsh conditions, and its tiny parts are harder to fix.
Here’s a quick comparison to help you decide:
Technology Type | Advantages | Disadvantages |
---|---|---|
Through-Hole (THT) | Strong and reliable, works in tough conditions, easy to repair | Bigger parts, slower manual assembly |
Surface Mount (SMT) | Compact designs, fast production, great for electronics | Less durable in harsh conditions, harder to repair and test |
Tip: Choose through-hole for strong and repairable designs. Pick surface mount for small, high-volume projects.
By knowing the differences, you can pick the right method for your project. Whether it’s a tough industrial board or a sleek gadget, the right choice ensures good performance and saves money.
Emerging Trends and Considerations for 2025
Advancements in Automation
Automation is changing how PCBs are made in 2025. Tools like pick-and-place machines, robotic arms, and AI systems make work faster and better. Pick-and-place machines put parts on boards with great accuracy. Robotic arms handle soldering tasks perfectly, improving quality and reliability.
AI helps find problems during production. Machine learning predicts defects, ensuring good results. Automated optical inspection systems check boards for mistakes, reducing human errors. These tools are important for industries needing fast and high-quality production.
Technology | Description | Impact on PCB Assembly |
---|---|---|
Pick-and-place machines | Machines that place parts on PCBs accurately. | Speeds up and improves assembly. |
Robotic arms | Robots that solder parts with precision. | Boosts quality and reliability. |
AI-driven quality control | AI systems that predict production defects. | Ensures consistent and error-free results. |
Automated optical inspection | Systems that automatically check PCBs for flaws. | Reduces mistakes and improves quality. |
Tip: Want faster and better production? Automation tools are a smart investment.
Miniaturization and High-Density Designs
Smaller devices need smaller PCBs. High-density designs, like those in phones and wearables, use tiny parts and tight layouts. Microvia technology helps make boards with more features in less space.
High-frequency materials also help miniaturization. These materials improve signals and work well in small designs. The demand for HDI (High-Density Interconnect) PCBs is growing as devices get smaller and more advanced.
Evidence Type | Description |
---|---|
Demand for Compact Devices | Smaller gadgets need smaller PCBs with more features. |
Advancements in Microvia Technology | Microvia tech allows tighter layouts and higher density. |
Integration of High-Frequency Materials | Special materials improve signals in compact designs. |
Market Dynamics | HDI PCBs are in demand for complex, small devices. |
Note: Miniaturization helps create advanced designs for modern gadgets and machines.
Mixed Technology Assemblies
Mixed technology uses both through-hole and surface mount methods. This combines the strengths of both. Through-hole parts are strong and reliable. Surface mount parts are small and fast to assemble.
Industries like cars and aerospace benefit from this mix. In cars, it cuts cleaning time and improves production success. In aerospace, it boosts coating quality and long-term reliability. Mixed technology also reduces defects and speeds up assembly in electronics.
Case Study | Industry | Key Improvements |
---|---|---|
Case Study 1 | Consumer Electronics | 30% faster assembly, 50% fewer cleaning defects, 20% better reliability |
Case Study 2 | Automotive Electronics | 40% less flux used, 25% shorter cleaning time, 15% better first-pass yield |
Case Study 3 | Aerospace Electronics | 60% less contamination, 35% better coating, 50% fewer long-term failures |
Tip: Mixed technology is great for projects needing both strength and compact designs.
Sustainability and Environmental Impact
Sustainability is very important in PCB assembly today. In 2025, industries focus more on eco-friendly methods. These changes aim to cut waste, lower pollution, and make greener products. Using sustainable ways helps the planet and meets industry rules.
Green Initiatives in PCB Manufacturing
PCB makers are using green methods to protect the environment. These steps reduce harmful chemicals, recycle materials, and save energy.
Recycling metals like copper and aluminum reduces waste and reuses materials.
Safer coatings and green chemicals replace harmful ones, protecting nature.
Making PCBs locally cuts transport pollution and lowers carbon footprints.
These actions help the planet and follow global rules like RoHS (Restriction of Hazardous Substances).
Environmental Impact Assessments
Environmental studies show how PCB making affects the planet. They check things like global warming and pollution levels. These studies help find ways to improve.
Using lead-free materials is safer for people and nature.
Recyclable boards save resources by needing fewer raw materials.
Energy-saving methods cut greenhouse gas emissions.
These checks guide companies to use better, greener methods and follow eco-rules.
Benefits of Sustainable PCB Assembly
Using eco-friendly methods has many benefits for your projects.
Saves Money: Recycling and less waste lower costs over time.
Follows Rules: Meeting eco-standards avoids fines and builds a good reputation.
Better Efficiency: Energy-saving tools make production faster and easier.
By choosing green methods, you can make great products and help the planet.
Tip: Use recyclable parts and energy-saving tools in your designs. Small changes can greatly reduce your environmental impact.
Sustainability in PCB assembly is now a must. It helps businesses stay competitive and eco-friendly. By going green, you support the planet and reach your goals.
Picking between through-hole and surface mount methods depends on your project. Through-hole is stronger and works for reliable designs. Surface mount is better for small, fast-made products.
Technology Type | Advantages | Disadvantages |
---|---|---|
Through-Hole Mounting | – Stronger bonds, great for reliable projects. | – Needs drilled holes, which take time and cost more. |
– Handles parts under mechanical stress well. | – Reduces space for routing on multi-layer boards. | |
– Good for testing and trying out ideas. | – Slower part placement compared to surface mount. | |
– Needs soldering on both sides of the board. | ||
– Smaller parts fit more on the board. | – Not as strong for parts under mechanical stress. | |
– Faster to make since no drilling is needed. | ||
– Quicker placement, saving time and money. |
New trends like automation and smaller designs are changing PCB assembly. To choose the best method, think about costs, vendors, and design needs.
Aspect | Description |
---|---|
Lifecycle Analysis | Knowing how long parts last helps avoid future problems. |
Vendor Assessment | Picking good vendors ensures steady quality and part supply. |
Prototyping | Testing designs helps improve size, function, and fixes issues. |
Cost-Efficiency | Researching parts and planning well saves money. |
Time Optimization | Managing time for testing and design changes improves results. |
By matching your project’s needs with these tips, you can make strong and efficient PCBs in 2025.
FAQ
1. What makes through-hole and surface mount technologies different?
Through-hole uses drilled holes to hold parts securely. Surface mount places parts directly on the board. Through-hole is stronger, while surface mount is faster and smaller.
2. Which method is best for testing new designs?
Through-hole is great for prototyping. Its bigger parts and easy-to-reach leads make testing and fixing simple. You can swap parts during development easily.
3. Can both methods be used in one project?
Yes, you can mix both methods. Through-hole adds strength, and surface mount saves space and time. This mix works well for complex designs like cars or planes.
4. How does automation help PCB assembly in 2025?
Automation makes production quicker and more accurate. Machines like pick-and-place tools and AI systems reduce mistakes. They also help create high-quality boards faster.
5. Is surface mount good for tough conditions?
Surface mount is not as strong in harsh environments. Its small parts can’t handle heat or vibration well. Through-hole is better for tough jobs.
Tip: Pick the right method based on your project’s needs for strength, size, and speed.
See Also
Choosing The Best PCB Assembly Method: SMT Or Through-Hole
Key Applications Of Through-Hole Technology In 2025 Electronics
Advanced Soldering Techniques For Precision PCB Assembly Today
Comparing Turnkey PCBA And Consignment Manufacturing In 2025