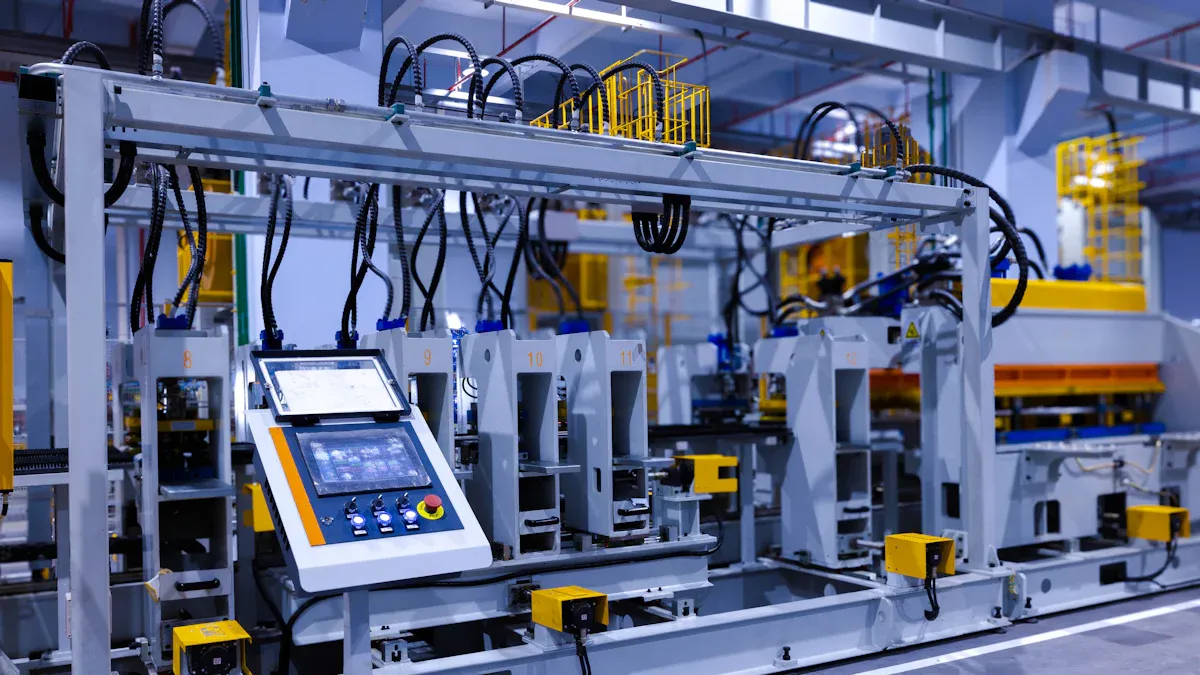
Hardware design plays a crucial role in enhancing the efficiency of edge computing for U.S. factories. With the integration of US-based IIoT manufacturing services, edge computing enables factories to operate faster, maintain higher reliability, and scale seamlessly to meet evolving demands. In 2023, hardware accounted for over 43% of the U.S. edge computing market, underscoring the significance of robust hardware in industrial operations. Combining advanced hardware with factory automation control systems amplifies these advantages, further driving the global CNC automation market’s growth from $61 billion in 2022 to $133 billion by 2030.
“Edge computing collects factory data, organizes it, and sends it to the cloud for better understanding.”
Key Takeaways
Edge computing helps factories work better by handling data near its source. This makes decisions faster and more reliable.
Strong hardware is important for edge computing. It helps devices survive tough factory conditions and work well.
Edge computing can predict machine problems early. This lowers downtime and repair costs by fixing issues before machines break.
Using AI and machine learning with edge computing gives quick results. It improves product quality and factory operations.
5G makes edge computing stronger. It sends data faster and connects more devices, making factories run smoother.
Basics of edge computing in manufacturing
What is edge computing and why it matters in factories
Edge computing handles data near where it’s created, like sensors or machines. It doesn’t rely only on faraway cloud servers. This helps factories make quick decisions, which is very important. By cutting delays, edge computing reacts faster to changes, improving work speed and dependability. It also checks machine health locally to stop breakdowns, saving money. Plus, edge computing works well with factory automation systems, sharing data smoothly and keeping processes running.
Note: Today’s edge platforms are built tough for factory conditions. They keep working even in harsh environments, making them key for smart factories.
Why edge computing matters for U.S. IIoT manufacturing
In U.S. IIoT manufacturing, edge computing helps factories stay ahead. It connects factory tools with IT systems, boosting performance and handling data instantly. For example, using cameras with IIoT can spot product flaws right away, ensuring quality. Edge computing also filters machine data to avoid overloading servers and lets managers check equipment from afar. These features meet the need for smarter maintenance and energy-saving solutions in U.S. factories.
Example Use | What It Does |
---|---|
Predictive Maintenance | Finds machine problems early using local data, saving time and money. |
Condition-based Monitoring | Sorts machine data nearby, helping remote checks and lowering server strain. |
Manufacturing-as-a-Service | Makes temporary setups easier and speeds up customer responses. |
How edge computing compares to cloud computing
Edge computing and cloud computing do different jobs in factories. Edge computing is great for tasks needing quick reactions, like monitoring machines closely. It processes data nearby to avoid delays. Cloud computing, however, is better for storing and analyzing lots of data over time. While cloud computing helps with big-picture insights, edge computing focuses on fast actions, which smart factories need. Together, they balance speed and large-scale data handling.
Hardware design considerations for edge computing
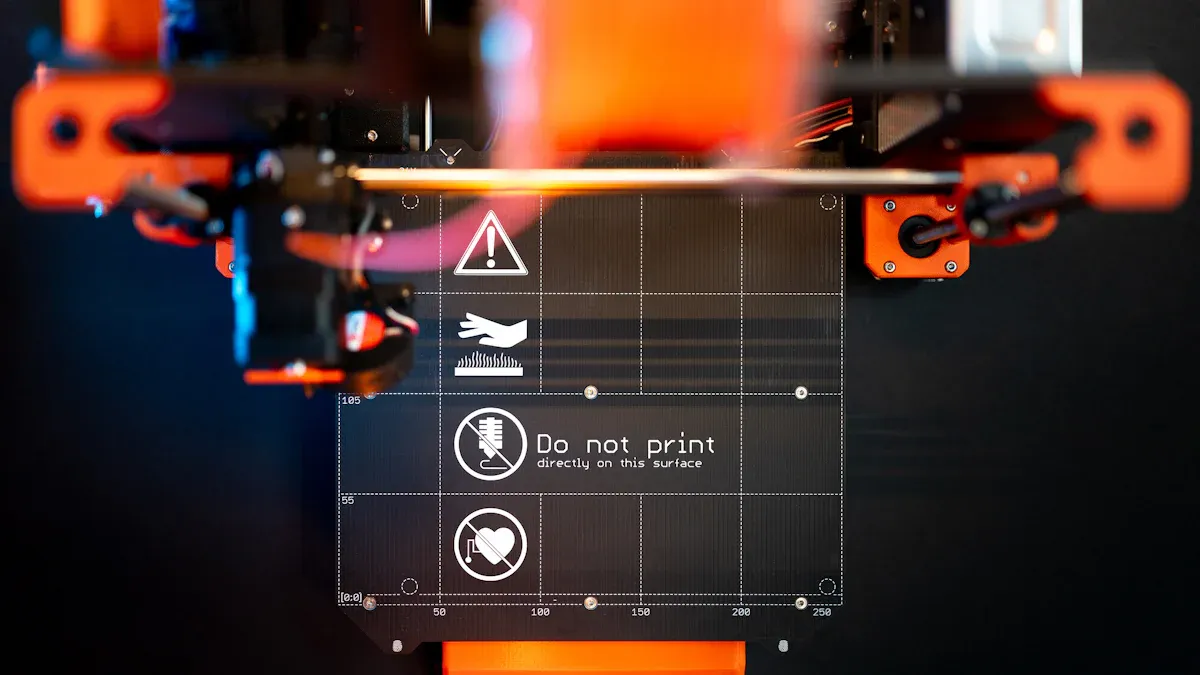
Processing power and performance optimization
Processing power is key for edge computing in factories. Edge devices must quickly handle tasks like analyzing data and making AI decisions. They need to work fast and stay accurate. To do this, factories use energy-saving processors and accelerators. These parts save power while keeping performance high. Techniques like pruning and quantization make devices work better in low-power setups.
Another helpful feature is Dynamic Voltage and Frequency Scaling (DVFS). It changes power use based on the task, balancing speed and energy use. High-end GPUs, which can do over 1,300 TOPS, are used for jobs like spotting problems or recognizing images. Low latency is also important. It helps edge devices process data fast, which is needed for smart factory tasks.
Tip: Picking the right processor, like ARM or AMD, can improve edge device performance. GPUs are great for tough jobs like creating images.
Durability and resilience for industrial environments
Factories can be tough places for edge computing hardware. Extreme heat, moisture, and shaking mean devices must be strong. Manufacturers test hardware to make sure it lasts. Tests like HTOL and HAST check if parts can survive harsh conditions. Burn-in testing finds weak parts early, so only reliable devices are used.
Standards like MIL-STD-810G are important for factory hardware. These tests check for things like heat, vibration, and dust resistance. For example, Test Method 501 checks how devices handle heat, and Test Method 510 looks at dust protection. These tests make sure edge devices work well in rough factory settings.
Note: Rugged edge devices are needed to keep factories running smoothly, even in tough conditions.
Scalability for future growth in smart factory automation
Scalability helps edge computing grow with smart factories. As factories use more IoT and AI, they need hardware that can handle more data and new tools. Modular designs let factories add parts when needed, making upgrades easy.
The smart factory market is growing fast. In 2023, it was worth $292.83 billion and could reach $1,203.38 billion by 2033. This growth is driven by a 15.18% yearly increase. Over 90% of factory leaders say digital tools are key to success. Edge computing helps by processing data quickly and using AI to improve production and supply chains.
Tip: Working with expert service providers can help factories add scalable edge solutions that fit current and future needs.
Seamless integration with factory automation control systems.
Edge computing helps factories improve automation by connecting devices and control systems. This connection allows quick data processing, less delay, and better system compatibility. Factories can gather, study, and use data locally, which fits well with automation needs.
Good integration systems are flexible, scalable, and link edge devices to the cloud. These systems let factories upgrade from simple SCADA setups to advanced Industry 4.0 tools without losing performance. Edge devices with flexible designs can handle data from IIoT devices while working in real-time. This helps factories grow their automation without slowdowns.
Feature | Description |
---|---|
Scalability | Works for basic SCADA and advanced Industry 4.0 systems. |
Edge-to-Cloud Deployment | Fits many edge devices, improving factory system compatibility. |
Edge Computing Capabilities | Collects and processes data quickly, cutting delays. |
Scalable Architecture | Grows with needs, connects IIoT devices, and manages data. |
Versatility for Industry 4.0 | Handles many industrial tasks, great for modern automation. |
Edge computing works well with factory systems, ensuring smooth data movement and better operations. Using flexible systems, factories can upgrade processes while staying fast and reliable.
Tip: Working with skilled automation experts can make integration easier and boost edge computing benefits.
Energy efficiency and sustainable power management.
Saving energy is important for edge computing in factories. It lowers costs and supports eco-friendly goals. New edge devices use smart power-saving methods to work well without wasting energy. These devices have special parts designed for low energy use, meeting factory needs efficiently.
Advanced hardware like AI accelerators and low-power SoCs handle tough tasks while saving energy. AI accelerators use tensor cores for deep learning with less power. Low-power SoCs combine machine learning, security, and radio functions in one chip, cutting energy waste. Tiny microcontrollers with small batteries manage simple sensor tasks, saving even more energy.
Hardware Type | Description |
---|---|
AI Accelerators | Tensor cores for deep learning, using little power. |
Low-Power Systems-on-Chip | Chips with ML, security, and radio in one. |
Micro-controllers | Small controllers for sensors, powered by tiny batteries. |
Energy Harvesting Innovations | Solar panels, kinetic harvesters, and thermal generators for powering devices. |
Using renewable energy, like solar panels or kinetic harvesters, makes edge devices greener. Chips designed for AI tasks use less energy, and smaller designs reduce waste. These features make edge computing more sustainable.
Note: Factories using energy-smart edge devices save money and help the environment.
Applications of edge computing in U.S. manufacturing
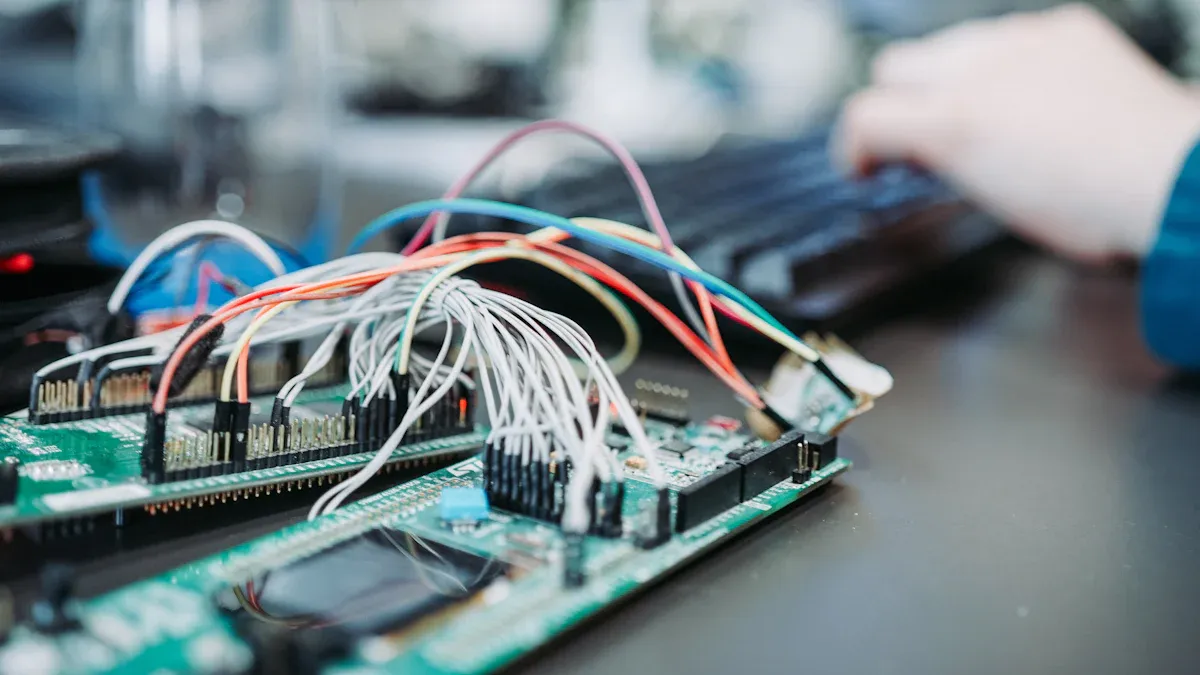
Predictive maintenance to cut downtime and save money
Predictive maintenance changes how factories care for machines. Using edge computing, factories watch equipment closely and predict problems early. This stops surprise breakdowns and lowers repair costs. For example, one car company saved 25% on repairs and improved production by 20% with predictive maintenance.
Edge computing processes data right where it’s made. This keeps predictive maintenance working even if the network is weak. It removes delays and gives quick updates, helping factories fix issues fast. Predictive maintenance also boosts Overall Equipment Effectiveness (OEE) by cutting machine problems and improving work flow.
Note: Factories using predictive maintenance with edge computing have fewer problems, better output, and lower costs.
Evidence Description | Impact on Manufacturing Downtime |
---|---|
Predictive maintenance improves OEE by minimizing unplanned downtime. | Increases production efficiency and cost savings. |
Edge computing reduces reliance on centralized cloud infrastructure. | Ensures predictive maintenance remains operational. |
Real-time data processing eliminates latency, enabling rapid decision-making. | Enhances responsiveness to potential equipment failures. |
Watching and analyzing in real-time for better choices
Real-time monitoring helps factories make smarter decisions. Edge computing allows constant checking of machines and production lines. By handling data locally, factories can find problems, track progress, and fix issues fast.
Important metrics like OEE, cycle time, and defect rates help improve factory work. Real-time analysis shows useful insights about these numbers. This helps factories run better and avoid delays. For instance, AI tools can spot patterns that slow production, letting factories act quickly to stay efficient.
KPI | Description |
---|---|
Overall Equipment Effectiveness (OEE) | Measures machine performance, availability, and output quality. |
Production Cycle Time | Tracks how long it takes to complete a unit from start to finish. |
Defect Rates | Monitors product quality and highlights recurring issues. |
Downtime Tracking | Identifies why and when production stops, helping prevent future slowdowns. |
Supply Chain Efficiency | Ensures materials arrive on time to prevent bottlenecks. |
Tip: Real-time analytics with edge computing help factories improve production and make faster decisions.
Better quality checks with edge-based AI
Edge-based AI has changed how factories check for defects. Machine learning, like CNNs, finds patterns and spots problems in products. These tools improve defect detection by over 60%, making products better and reducing waste.
In chip-making, machine learning raised productivity by 30% and saved 300 work hours monthly. Edge computing analyzes data instantly, helping factories find and fix defects right away. This is very important for industries needing perfect results.
Note: Factories using edge-based AI for quality checks get better at finding defects and improving production.
Enhancing worker safety with edge-enabled IoT devices.
Edge-enabled IoT devices are improving safety in U.S. factories. These devices watch for dangers and act fast to prevent harm. They collect and study data right where it happens, helping factories stay safe and efficient.
Sensors with edge tools can spot risks like air changes or pressure drops. For example, pumps with pressure issues may fail soon. Finding these problems early helps fix them before accidents happen. In aviation, edge systems check engine data to avoid failures and keep flights safe.
Factories using IoT devices see better safety and health for workers. These systems check air, temperature, and machines, warning about unsafe conditions. Fixing risks quickly keeps workers safe and factories running smoothly. They also help meet safety rules, showing care for employees.
Edge computing makes these devices work better by handling data nearby. This cuts delays and allows quick action during threats. Wearable IoT devices can track heart rate or body heat. If something seems wrong, alerts go out fast, letting supervisors act quickly. This keeps workers safe and avoids factory slowdowns.
Using edge-enabled IoT devices has made factories safer. Fewer accidents happen, and work stays productive. Real-time checks and automation keep safety rules in place without slowing work. By combining edge computing with IoT, factories create safer places to work.
Tip: Work with IoT experts to set up safety systems that fit your factory.
Challenges in hardware design for edge computing
Balancing cost with performance and durability
Making hardware for edge computing needs careful planning. Factories want devices that work fast and survive tough conditions. But creating advanced chips for edge devices is hard. Tiny parts and complex designs make production expensive and affect strength.
Factories must manage limits like power and size while keeping performance high. Checking long-term costs, like repairs and downtime, helps save money. Using energy-efficient designs lowers expenses even more. Hardware also needs to grow with factory needs without constant upgrades.
Tip: Modular hardware designs can grow easily and save money over time.
Ensuring cybersecurity in edge computing systems
Edge computing faces special security problems because devices are spread out. Each device could be attacked, making systems less safe. Many IoT devices lack strong security, making them easy targets for hackers. Problems like stolen data or DDoS attacks can happen.
To stay safe, factories need strong security plans. Regular updates and checks fix weak spots. Separating networks keeps edge devices away from important systems. Encrypting data protects it during use and storage. Multifactor authentication adds extra safety to devices.
Note: Security rules and regular checks are key to keeping edge computing safe in factories.
Managing interoperability with legacy systems
Connecting edge computing hardware to old factory systems is tough. Many factories use older machines that don’t work well with new devices. This causes problems with sharing data and slows down processes. Without good connections, factories may waste time and create data gaps.
Modern tools help fix these issues by using platforms made for specific factory needs. These tools let old systems and edge devices share data smoothly. Flexible solutions help factories update systems while keeping things running well.
Tip: Working with skilled integration experts makes switching to edge computing easier and improves system connections.
Tackling delays and limited data capacity.
Delays and limited data capacity are big challenges for edge computing hardware. These problems can slow down factory systems, especially when quick decisions are needed. Factories using edge computing must solve these issues to keep things running smoothly.
Delays, called latency, happen when there’s a gap between making and processing data. Too much delay can make edge systems less effective, like in predictive maintenance or live monitoring. Limited data capacity, or bandwidth, means only a small amount of data can move through networks. Crowded networks make this worse, lowering system performance.
Problem Type | What It Means |
---|---|
Limited Bandwidth | Small data capacity slows down edge computing performance. |
High Latency | Delays in data processing hurt system efficiency. |
Network Overload | Crowded networks make edge computing slower and less reliable. |
Edge computing solves these problems by placing servers and storage near where data is made. This setup reduces delays, allowing faster data handling and decisions. Devices close to data sources use available bandwidth better, cutting network crowding and improving operations.
Placing servers near data sources reduces delays.
Devices close to data use bandwidth better, avoiding network issues.
Factories can improve even more by using hardware designed for their needs. Fast processors and low-delay communication tools make systems quicker. Modular designs let factories grow their systems without losing efficiency.
Tip: Work with hardware experts to pick parts that balance speed, data capacity, and growth for edge computing.
Fixing delays and data limits is key to keeping edge computing reliable in factories. By using nearby data processing and strong hardware, factories can solve these problems and get the most out of edge computing.
Solutions and future trends in edge computing hardware
Advances in ruggedized hardware for industrial automation
Ruggedized hardware is crucial for keeping factories running in tough conditions. New designs focus on modular systems that make operations stronger. Industry 4.0 pushes for connected and reliable tools, highlighting the need for strong industrial networks. Innovations like conveyor systems and sensors help factories work better by improving communication and secure IoT connections.
Robots and smart software link different parts into one smooth system. These setups use standards like OPC UA and MQTT to share data easily. Connected devices help with predictive maintenance and advanced data analysis. Ruggedized hardware is now a must-have for modern factories.
Tip: Using ruggedized hardware improves factory reliability and supports Industry 4.0 goals.
Modular and customizable edge devices for smart factory automation
Modular edge devices give factories flexibility to grow and adapt. These devices adjust to changes, letting factories expand without big hardware changes. Examples include systems for tracking errors and testing compressors. These tools collect data instantly, helping factories make better choices and work more efficiently.
Case Study Title | Description | Link |
---|---|---|
Remote Misjudgment Monitoring Solution | Tracks and shows errors by production line and model. | Download Case Study |
Compressor Test Facility | Uses real-time tools for testing pumps. | Download Case Study |
Energy Monitoring System | Manages energy use on time and within budget. | Download Case Study |
These modular tools make it easy to add edge computing to factories. They allow real-time tracking and analysis, improving workflows and cutting downtime.
Note: Modular designs are perfect for factories moving to Industry 4.0 systems.
Integration of AI and machine learning at the edge
Adding AI and machine learning to edge devices makes factories smarter and faster. Edge AI handles data nearby, cutting delays and speeding up responses. Devices with tensor cores and low-power chips do tasks like finding defects and predicting problems.
Edge AI tools analyze data instantly, spotting patterns and issues in production. For example, 5G networks provide fast, low-delay communication, letting devices send important messages quickly. Mesh networks add extra reliability, keeping systems running smoothly.
Aspect | Description |
---|---|
Data Transmission | Sends important control messages for quick decisions. |
Latency Reduction | Offers fast, low-delay connections for edge tasks. |
Network Resilience | Mesh networks ensure reliable operations in different settings. |
Edge AI helps factories use advanced tools and automation, boosting efficiency and growth. Combining AI with edge computing brings big improvements to factory operations.
Tip: Factories using AI at the edge save money and work more efficiently.
The role of 5G in enabling faster and more reliable edge computing.
5G technology helps edge computing work faster and more reliably. It sends data quickly and reduces delays, making edge devices share information almost instantly. This is very important for factories where quick decisions and fast actions are needed.
With 5G, delays in edge computing systems are much lower. Data from sensors and machines is processed nearby without interruptions. For example, predictive maintenance uses instant data checks to stop equipment problems. 5G makes these systems work better, cutting downtime and boosting productivity.
5G also connects many devices at once. Smart factories use thousands of tools like sensors and cameras. 5G networks handle these connections easily, keeping devices working smoothly. This helps factories grow without losing performance.
Another benefit of 5G is better mobility for edge devices. Portable tools, like wearable IoT gadgets, stay connected with 5G’s fast and stable network. These devices can check worker safety or track machines in real time, even in hard-to-reach places.
Feature | Benefit |
---|---|
Ultra-Low Latency | Allows quick data processing and decisions. |
High-Speed Connectivity | Speeds up data sharing for edge computing tasks. |
Massive Device Support | Manages many IoT devices in smart factories. |
Enhanced Mobility | Improves portable device performance in tough environments. |
Using 5G with edge computing makes factories more efficient and reliable. This combination supports smarter and more connected industrial systems.
Tip: Work with 5G providers to connect edge computing systems smoothly.
Strong hardware design is very important for edge computing in U.S. factories. It helps process data quickly and connects well with factory systems. This improves how factories work and keeps them reliable. One big use of edge computing is predictive maintenance. It finds problems early, stops surprise breakdowns, and saves money on repairs. It also helps machines last longer, making factory work better.
The U.S. leads in making smart factory tools and edge computing hardware. New ideas like modular designs and adding AI will change factories even more. Using these new tools will help factories grow, make smarter choices, and work in eco-friendly ways.
FAQ
What is edge computing, and how is it different from cloud computing?
Edge computing works near where data is made, acting quickly. Cloud computing stores and studies data far away for big-picture insights. Edge computing is for fast actions, while cloud computing helps with long-term planning.
Why is hardware design important for edge computing in factories?
Good hardware design helps edge devices work well in factories. It improves speed, strength, and energy use. Well-designed hardware connects easily with factory systems and grows with future needs.
How does edge computing make predictive maintenance better?
Edge computing checks machine data nearby to find problems early. It cuts downtime by acting fast and avoids delays from faraway systems. Predictive maintenance keeps machines running longer and costs less to fix.
What does 5G do for edge computing in factories?
5G makes data move faster and cuts delays. It connects many devices and helps portable tools work better. Factories can decide quicker and keep systems running smoothly with 5G.
Can edge computing help factories be more eco-friendly?
Edge computing saves energy with smart hardware and green power. It reduces waste by spotting problems quickly. Factories use less energy and work in a more earth-friendly way.
See Also
Essential Technologies Shaping PCBA Production in Today’s Electronics
Exploring Industrial Edge Computing Devices and Their Automation Impact
Leading IIoT Hardware Innovations for Industry Applications in 2025